Vertical Aerospace, a UK aviation startup, is set to launch the world’s first certified winged electric vertical takeoff and landing (eVTOL) with its VA-1X.
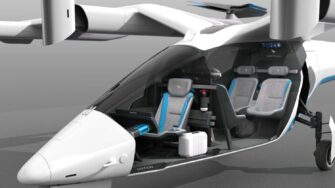
The backers of such transport praise its ability to be quiet, efficient and carbon-emission free, and are building them up as the next urban mobility solution.
Innovators like Vertical Aerospace plan to move more freely and access local heliports and airports where noise regulations currently restrict the number of flights per day.
The race in the aerospace sector to bring an eVTOL aircraft to market is really heating up, and with its VA-1X winged design producing higher speeds and lift that reduces necessary electrical load when in flight, Vertical Aerospace is one of the frontrunners.
“The VA-1X aircraft has been designed to carry five people – a pilot and four passengers,” says Vertical Aerospace head of engineering Eric Samson. “We are targeting inter- and intra-city travel with a range of up to 100 miles at cruise speeds of 150mph.”
Vertical Aerospace is currently building a demonstrator, which it plans to fly in the third quarter of 2021 before certifying and bringing the final aircraft to market in 2024.
“We’re in the process of writing a new chapter in the aviation industry,” says Samson.
“We’re working with emerging technologies, including intuitive and safe flight control technologies from Honeywell. At the same time, we’re defining a new certification basis and collaborating with leading companies around the globe.”
The team are using the Dassault Systèmes 3DExperience platform to develop the aircraft, to share files and information, and to ensure the VA-1X meets the right certifications with authorities.
“It’s a one-stop shop and single source of truth for Vertical Aerospace and our business partners that allows us to work concurrently wherever we are in the world,” suggests Samson.
All of Vertical Aerospace’s product development is being defined and managed through the 3DExperience platform on Cloud, with assistance from Dassault Systèmes’ business partner Desktop Engineering (DTE) to maximise how it can take advantage of all the features and tools.
“The amount of functionality the platform delivers is hugely exciting,” says James McMillan, senior design engineer at Vertical Aerospace. “We’ve started by focusing on our core business needs and making sure we get these processes up and working, such as building a product structure and implementing a part numbering system, which is future proof and will support configuration control.
“When we have fleets of operational aircraft, we need complete traceability of all the parts.”
A program is in place to get part numbering system in place straight away, but through collaborating with DTE and Dassault Systèmes, the product structure can be future proofed.
“The cloud ensures business resilience and allows us to continue working from any location at any time,” Samson adds. “Having all our data reside on the cloud ensures a single source of truth while saving us any upfront capital investment. All of our apps are always up-to-date and we can add and remove functionality according to our changing requirements.”
Actions can be sent out to the required teams in decision meetings; session can be recorded, and key people can sign-off documentation – particularly important as the company advances to the next stages of its product development.
McMillan explains that the end-to-end process is really important as the company looks to the future.
“We will be able to map change management with configuration control, allowing us to set effectivity ranges on design solutions to make sure that they’re applicable to certain groups of aircraft.
“Today, we go to a single user, single log in and you’re able to see the entire process cradle to grave. It’s phenomenal. When we start producing aircraft and services, we are hopeful that we can achieve a fully 3D process with our suppliers, exchanging digital data all the way from production planning down to customer service, maintenance and repairs.”
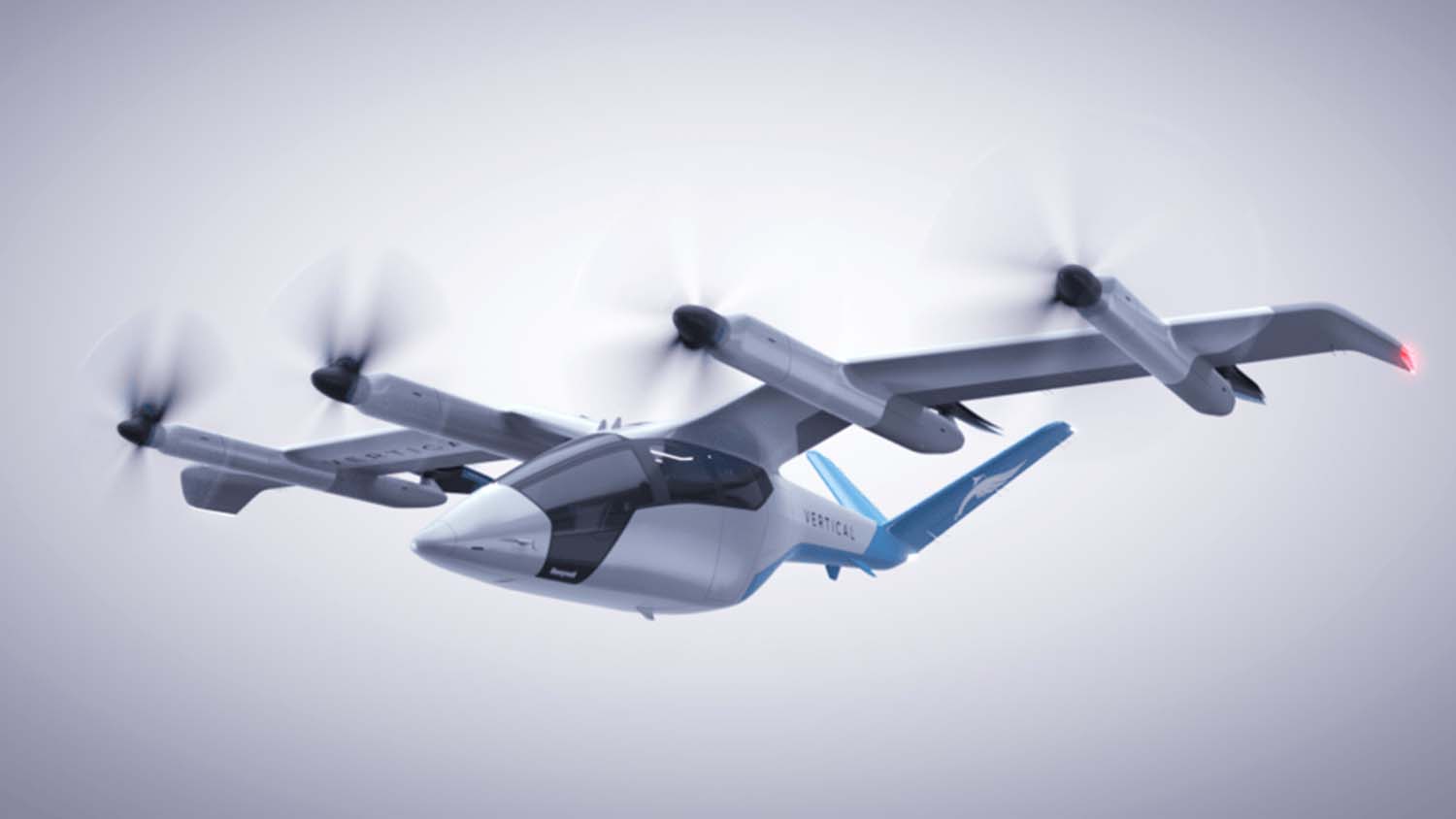
Vertical Aerospace’s engineers use CATIA as its CAD for the aircraft structure, having needed a package that has the power to cope with a whole aircraft and its various systems.
“This is a composite aircraft primarily,” says John Russell, senior design engineer at Vertical Aerospace. “When you design in other CAD packages, you tend to simplify composite structure. But the analysis work that goes into composites and understanding plies, orientations and layers of composites is complicated.
“With this platform, very early on we could build a composite part using a composite workbench to build up the layers and plies. It takes a bit more time to set it up, but when there is more analysis being done, we can look at the best way to manufacture the part from start to finish; it is a far quicker process.”
Russell says that in the future it will be able to give this digital data to manufacturers and go straight to manufacturing.
Importantly, the 3DExperience platform enables Vertical Aerospace to build a virtual twin of the aircraft and incorporate all aspects, from aerodynamics to electronics.
“We’re mapping out the 2D electrical functional work and linking it directly to the 3D model,” McMillan says. “Soon, we will have the ability to link the 2D and 3D into the whole system architecture so that we can map it from the top-level aircraft definitions with requirements all the way down to the 2D and 3D.
“Everything will be in one place; we’re not looking around for different datasets and transferring data across. It’s a single source solution. So, if you move or change some of the functional work, it gives you an alarm that your 3D model.”
Vertical Aerospace is able to carry out concurrent engineering and allow all users in the company to access the information they need to keep projects on track by using the 3DExperience platform.
“The platform brings all teams together,” says Russell, explaining that the design process initially starts with the aerodynamics team shaping the aircraft and analysing the aerodynamic flow. Once a master geometry surface has been built and CAD data is linked to it, then they can change the aerodynamic shape, and because of the Dassault Systèmes platform the CAD models are quickly updated too.
“People who don’t have CAD access can see all this in the web-based app,” Russell continues. “They can see the aerodynamic shape, the structure and interrogate the bill of materials. For everyone to see the parts and models and define a project plan – that’s a really big deal!”
The company is growing its supplier network to bring its aircraft to market faster, and will use its 3D model to hand over specific information down the supply chain. Russell says that this will include details such as the analysis work from the stress and aerodynamics teams, as well as all the manufacturing, assembly and installation instructions integrated into the model.
All this is geared to make the handover to manufacturing far easier, faster and much more effective.
As Vertical Aerospace brings its aircraft to market, it is working closely with the safety regulator CAA (Civil Aviation Authority) to help shape the regulations and define new levels of safety in the industry.
Having the full digital traceability will help the team to achieve a DOA certification from CAA, and reach market ahead of the competition.
“You’re only limited by your imagination,” says McMillan. “We’re excited about the potential of what we can achieve with the platform – and that is a completely digital representation of the aircraft. Everywhere I’ve looked for a solution, I’ve found it on the platform. It’s so exciting!”