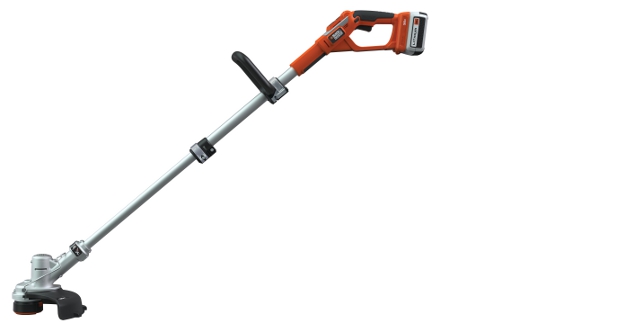
Black & Decker’s lithium-ion cordless grass trimmer fitted with a long-lasting 36 volt battery
Take charge
Cordless tools and gardening equipment have been available for a while, but they still present a challenge to designers wishing to increase the compact performance of their products.
Black & Decker are maestros when it comes to developing innovative products for tackling chores, and its UK design office in County Durham set itself the task of creating a battery that would add to the experience of using its products.
The 36v lithium ion battery is powerful enough to run its electric grass-strimmers and hedge-trimmers, while being compact and light enough to mount into the design.
The lithium ion power source also maintains its level of charge for longer periods; for a product not in everyday use this means it can be dug out of the garden shed a few weeks after its last charge and still work.
Black & Decker took the standard abilities of the battery even further, shaping it to fit the lines of the products it powers. Most interesting is the addition of a ‘state of charge’ gauge which gives the user an idea of how much power the battery has left; useful to know before getting halfway around the garden and finding your strimmer has fizzled out of power.
The gauge is fitted into the latch that secures the battery, a design that saves on space and, because of its cunning design, is intellectual property of Black & Decker.
Even for a humble battery, lots of sketching is performed before concepts are rounded down into a design that works with a number of different garden products.
A 3D model is created in Catia, allowing prototypes to be made on the team’s Objet 350v to test for size and fit, and the CAD model can then be developed for all the manufacturing and moulding purposes.
The models are also taken into Keyshot, which provides accurate renders to share with Black & Decker’s other offices and marketing team.
The final product is a compact, robust unit that (sadly) gives us fewer excuses not to go out and tidy the back yard.
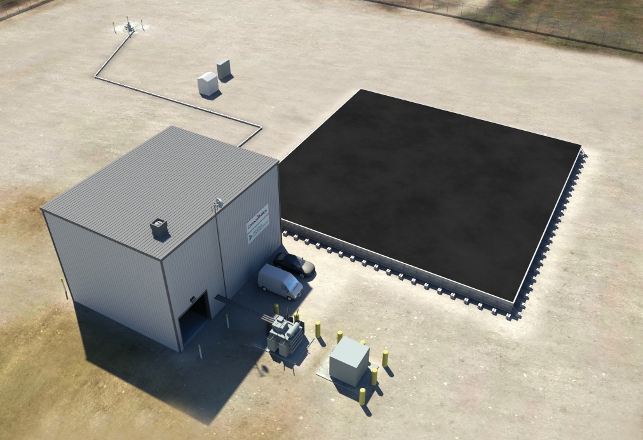
The General Compression Advanced Energy Storage system takes intermittent electricity from conventional wind turbines and stores that energy in the form of high-pressure air in underground geologic formations
Blackout buster
Generators can only provide energy until their fuel runs out – for a hospital, emergency stations or sites responsible for network servers, this isn’t long enough – so investing in an energy storage system is key.
Storing the captured power of the wind for later use is the challenge addressed by General Compression, based in Newton, Massachusetts.
The result is the General Compression Advanced Energy Storage (GCAESTM) system is an enormous air compressor and expander capable of absorbing, storing, and efficiently releasing the energy generated by wind turbines. Without burning any fuel, the GCAES returns as much as 75 per cent of the stored energy to the process, a significant return when compared to other energy storage solutions.
Simon Helmore, a project engineer at General Compression, brought several years of experience using Autodesk Inventor software to the company having previoulsy designed handheld medical devices: “One of my biggest concerns at the start was the difference in scale from what I was used to.”
The team also uses AutoCAD P&ID, Autodesk Plant 3D and most importantly, Autodesk Maya for presentations and visualisations that have helped it raise over $38 million so far, including grants from the U.S. Department of Energy.
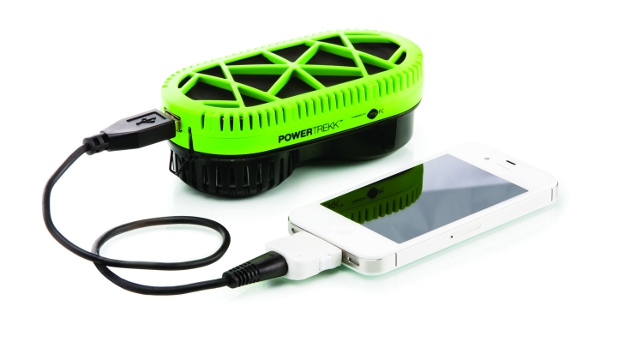
Power packed
As we become more inseparable from our mobile devices, the more the need grows to power them in remote locations, far from a solitary plug socket, which is where the PowerTrekk fits in.
Designed by Stockholm-based outfit Propeller, this brightly attired, pocket sized power generator is powered by nothing more than water and its fuel cell is the size of an ice hockey puck.
As a project for its client MyFC, using its innovative fuel cell technology, Propeller were involved early on in the process.
To operate, hydrogen must be supplied to the fuel cell, and the fuel cell must be exposed to the open air. The fuel cell inside silently converts hydrogen into electricity via the Proton Exchange Membrane in the fuel cell.
As a result, the distinctive grill on top is not only aesthetic, but allows air in to aid the process and cool the unit as the chemical reaction to provide the electricity heats up the unit slightly.
By making the top section bright, it not only makes it easy to find in the bottom of a rucksack, but also easy to spot should you lose it when about to leave a music festival. It also draws in the eye away from the larger base, making the product as a whole seem smaller.
The team at Propeller sketched out three iterations of the PowerTrekk as a concept, before choosing the key elements to create the final design.
The design was built in 3D using Rhino, and later SolidWorks, before the 3D dimensions were used to mill out foam models for shape referencing, and rapid prototypes made for a conclusive appraisal.
The unit provides 4-watt hours of power before the fuel cell need changing, making it a great device for the great outdoors.
We take look at devices that pack some power
Default