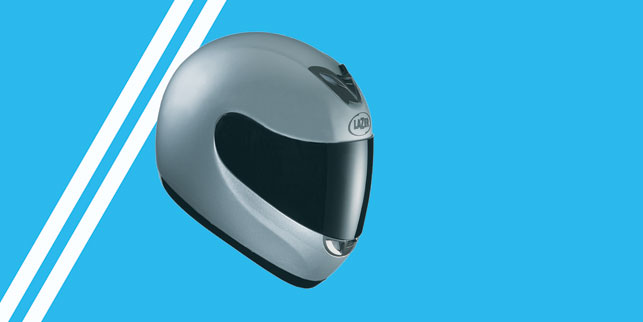
The SuperSkin technology has so far been incorporated into two Lazer helmets
Although conventional motorcycle helmets shield the head against a severe blow, they don’t protect from the biggest cause of motorcycle fatality – rotational head injury.
Whenever the head is struck it rotates to a greater or lesser extent and these rotational stresses can cause tearing of blood vessels and nerves in the brain.
However, a new innovative helmet design is said to be able to reduce this intercerebral shearing by 67.5 per cent and the mechanical effects of rotational acceleration by more than 50 per cent. In other words, on impact the outer skin-like lubricated helmet membrane can stretch and slide over the outer hard shell to prevent the dangerous rotational forces being transmitted to the head and brain.
This may sound very sophisticated but the Lazer SuperSkin helmet is in fact just mimicking what naturally occurs in our bodies – although the thick bone of the skull provides much of the direct protection against a severe blow, the skin on our scalps acts as protection against rotation whenever the head receives an impact by sliding over the surface of the skull to absorb rotational injury.
So, with nature having given him the inspiration, Dr Ken Phillips wanted to demonstrate that the same effect could be designed into a helmet.
He set up his own company in 1999 in order to research his invention – Phillips Head Protection System (PHPS) – and filed for a patent. However, moving it from an idea into a marketable and fully tested product design would require a great deal of research and development.
First principles
Eight years ago Dr Phillips turned to Berkshire-based Industrial Design Consultancy (IDC). “Dr Phillips approached us after he carried out some very initial tests at the Transport Research Laboratory (TRL) with some very crude prototypes, which were enough to prove that the basic principle showed an advantage. Drop tests demonstrated that the rotation was a lot lower than a standard helmet,” recalls Stephen Knowles, of his first project at the company and now IDC’s managing director.
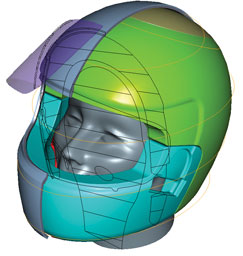
Pro/Engineer was used to design the helmet due to its ability to create complex surface geometry
Having examined this fairly complex mechanical problem IDC realised that it would have to create a design that consisted of three elements – a stretchy outer membrane, a layer of lubricant underneath and then a hard shell.
“When the helmet impacts the surface at an oblique angle the outside tends to grip the surface causing the outside of the helmet to rapidly decelerate whilst the centre of the head continues and this causes rotation. What we were looking to achieve was to prevent the outside of the helmet shell being slowed down by the impact,” explains Knowles.
“Putting the stretchy outer skin layer over the shell with a lubricant between the surfaces, allows the main helmet structure to slide relative to the outer skin and relative to the impact surface. This prevents the outside of the helmet from decelerating too sharply and reduces the rotational shock to the helmet and head.”
Material science
As this revolutionary product design would require a careful combination of materials, IDC started out by writing a programme liaising with TRL in order to systematically identify materials that could meet each element of the design. Initially materials were tested for resistance and strength based around flat sheets. Brian Gough, IDC’s project leader for the development explains, “We knew at the very early stage that we wanted to get an understanding of the materials. We could then quickly rule out some of the less likely ones enabling us to create a short list.”
The team at IDC also looked at many different kinds of lubricants, elastomers and adhesives, which would be the method of securing the membrane around the outside to the hard helmet shell. “Ultimately this membrane has to be secure all the way round the periphery – it shouldn’t rip or damage in everyday wear but then in an impact situation it must be able to move and slide,” adds Gough.
In these tests they also measured the coefficient of friction, which is the ratio between the force that is pushing two surfaces together and the force that it then takes to slide that sideways. On impact in a standard helmet, the direct forces between the shell and the outside are very high and so too is the sideways force that wants to rotate the head. The aim with this design was to bring this rotation element down. “If you can reduce the friction or ‘grippiness’ between the road surface and the outer part of the helmet then it will skid off it rather than gripping and spinning,” explains Gough.
As well as the materials testing, IDC also carried out user research into competing helmet products. “Motorcycle helmets come in a range of sizes and different manufacturers and models have varying geometry. IDC’s designers got feedback from users to find which helmets were generally considered more comfortable, and also analysed a range of helmets for liner thickness and impact performance,” says Gough.
Design development
Armed with this knowledge IDC moved into CAD. Rhino was used initially to create a few early concepts for general testing and development of the technology. The team then moved into Pro/Engineer and due to the balance between appearance, fit, comfort and impact absorption it meant a lot of time was spent on fine adjustment to the geometry. “Pro/E was used for its ability to create complex surface geometry that can then be analysed, manipulated and built upon to deliver the required result,” explains Gough.
A full assembly model was built including the basic data of the wearer’s head, the comfort lining, the impact absorbing liner, the main helmet shell and outer membrane skin. The benefit of Pro/E, according to Gough, was that it allowed the geometry of all these parts to be created and linked from the original model. Once the geometry was checked and approved, Delcam PowerMill was then used to machine a master pattern of the outer shape of the helmet shell. “This machined pattern was then used to check and approve the geometry and used as the master form for making the moulds for the shell and membrane,” adds Gough.
In-house prototyping
Central to the research and development process was rapid prototyping and IDC has the advantage of having IDCModels, an extensive rapid prototyping and model making facility in-house. It includes two CNC machining centres, a 3D Systems Viper stereolithography machine, two large chamber vacuum casting machines, a vacuum forming machine, a full woodworking shop, a water extracted spray booth, conventional lathes and a milling machine. This diverse range of equipment is manned by a team of five highly skilled model makers, pattern makers and tool makers.
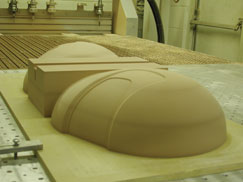
Delcam PowerMill was used to machine a master pattern of the outer shape of the helmet shell
Three elements of the helmet were prototyped and apart from the helmet shell, which is made from a composite of Kevlar and carbon fibre and manufactured at an aerospace factory, the rest of the prototypes were produced in-house.
Although the impact absorbing liners would eventually be moulded from expanded polystyrene (EPS), in the early prototype stages, due to all the tests that would be carried out (and to cut down on the expense of making a mould) IDC chose to machine these from Styrofoam. This is essentially an EPS building foam with the same impact absorbing properties as moulded expanded polystyrene. Once the Styrofoam had been proved to be suitable, precision CNC machining was used to sculpt the multiple impact absorbing liners from a polystyrene block.
According to Vincent O’Horo, head of IDCModels and rapid prototyping specialist, machining expanded polystyrene foam is not very common and having a three-axis machining centre in-house certainly had its advantages. “The large format bed (1.2m x 2.4m) meant up to 12 liners could be machined in a single overnight run,” he comments. “Delcam was also useful in arranging this multiple machining and optimised the cutters and speeds to facilitate rapid production without compromising accuracy.” Delcam was additionally used to make a forming tool for a prototype visor.
Vacuum casting was used to make the stretchy outer membrane. A mould for the membrane was CNC-machined in resin from the Pro/E CAD data ensuring that the inside surface of the membrane skin was an exact match for the outer surface of the helmet shell.
Two part polyurethane elastomer materials were then poured into the mould cavity under a vacuum and oven cured in the mould. Every prototype made meant that IDC was making new versions of the membrane on different materials. “Various stiffness and hardness resins were trialled to find the optimum combination to give the best safety performance,” explains O’Horo.
The test process
With a full helmet now prototyped IDC embarked on the many various rounds of testing. In order to find the right combination of materials, Gough estimates that well over 100 different prototypes were made all based around the same basic geometry.
Many of these tests were carried out at TRL and another advantage of having their own in-house prototyping facility was that the technical staff at IDCModels together with IDC’s engineers could communicate with TRL on testing the helmets and this resulted in the exact dimensional and impact requirements being met. “Also the limited availability of test slots often meant new liners were needed at very short notice. Having the facility in-house allowed us to react to the demand,” adds Gough.
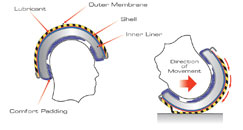
The Phillips head protection system – click to see it in testing
At TRL much of the testing focussed on measuring the rotational acceleration impacted on the head by an oblique impact against a road surface. “To simulate this, the helmets tested were fitted onto a test head form and dropped onto an incline 15 degrees from the vertical and having an abrasive surface to replicate the road. The test head form was instrumented with accelerometers to measure linear and rotational accelerations (effectively the level of shock) transmitted to the head. In addition, many of the tests were recorded with high speed video in order to observe the behaviour,” says Gough.
The other tests that the prototype needed to go through in order to make it a commercially viable product included age testing. Here it was discovered that over time some of the materials used for the membrane tended to absorb the lubricant. This meant that the lubricant would disappear into the material and so change its material properties. “It also meant that the lubricant was no longer there when you needed it to make the friction between the two surfaces,” explains Knowles.
In the painting tests it was discovered that either the paint wouldn’t adhere to the membrane material properly or it would change its chemical properties. As standard paints couldn’t be used IDC found a paint manufacturer that had a very robust elastic type of paint. “Obviously at every stage when you are moving things forward and trying new materials you need to redo the tests and ensure that
by introducing this new element you haven’t taken away the benefit of the system that was originally identified,” says Gough.
Having carried out tests at TRL, prototypes were also submitted to a government study on helmet safety as well as other European test houses to ensure that it conformed to the EC standards. “We also submitted it for further testing, which goes beyond these standard helmet tests as these don’t test very rigorously for the rotational shocks as the awareness of the danger of rotational shocks has only come about more recently,” explains Gough.
“So, we did some other testing with a recognised test house to measure the rotational acceleration and basically it verified that there was dramatic improvement in rotational acceleration.”
On track to production
Despite the project’s many technical challenges, setbacks and breaks in the development process as Dr Phillips sought potential licensees, there was a strong motivation by all involved to see this life-saving invention realised in a real product.
For Knowles, Thomas Edison’s famous quote rings true: ‘Invention is 1% inspiration and 99% perspiration’.
“Everyone involved at IDC could see how the thing could work but it meant actually proving it and solving all the practical and commercial issues such as making it cost effective, making it so that it wouldn’t be an addition to the helmet, making it unattractive to consumers or making it not too heavy and unwieldy to carry. So, fine tuning all of these extra considerations against this very demanding technical requirement to withstand these very high loads, to break at just the right amount, and have these low frictions – that was the challenge and that needed a lot of time and focus,” explains Knowles.
The model was now ready for prototype manufacturer however, according to Knowles, before it was approved cross sections of the geometry were measured and compared to reference data in Pro/E. “Ultimately we got to the stage where we had a complete blueprint for how you make a helmet according to this invention. We had all the test results to prove that it works, all the manufacturing data and material specifications – basically everything you need to take it forward,” says Knowles.
In the meantime Dr Phillips had found a Belgian manufacturer Lazer to licence his technology to and who would have exclusive use of it on its motorcycle helmets. It then took a further two years for Lazer to get the Superskin helmets to market and in their production research IDC and Dr Phillips assisted in helping them understand the technology and adapt it to their in-house processes and helmet designs.
Lazer also carried out further tests at an independent laboratory based at the Louis Pasteur University of Strasbourg in association with the CNRS, the French National Scientific Research Centre.
Launched at the end of last year, the SuperSkin technology has so far been incorporated into two Lazer helmets – open face Rider and full-face Solano variants.
The helmets will hit UK shelves this summer with prices ranging from £150 to £200. However, the project doesn’t end there as IDC is currently working with Dr Phillips on developing other applications for the technology and water sports, American football and equestrian versions are currently under investigation.
“We have been doing some initial studies on applying the technology to different types of head protection,” says Knowles. “There is quite a lot of interest too from various industry bodies and authorities.”
The helmet with a skin that helps save your own