The motorcycle industry faces the huge technical and commercial challenge of producing electric sports bikes that offer performance equivalent to their petrol-fuelled counterparts. Stephen Holmes learns how White Motorcycle Concepts is blending aerodynamics and innovation to take journeys further
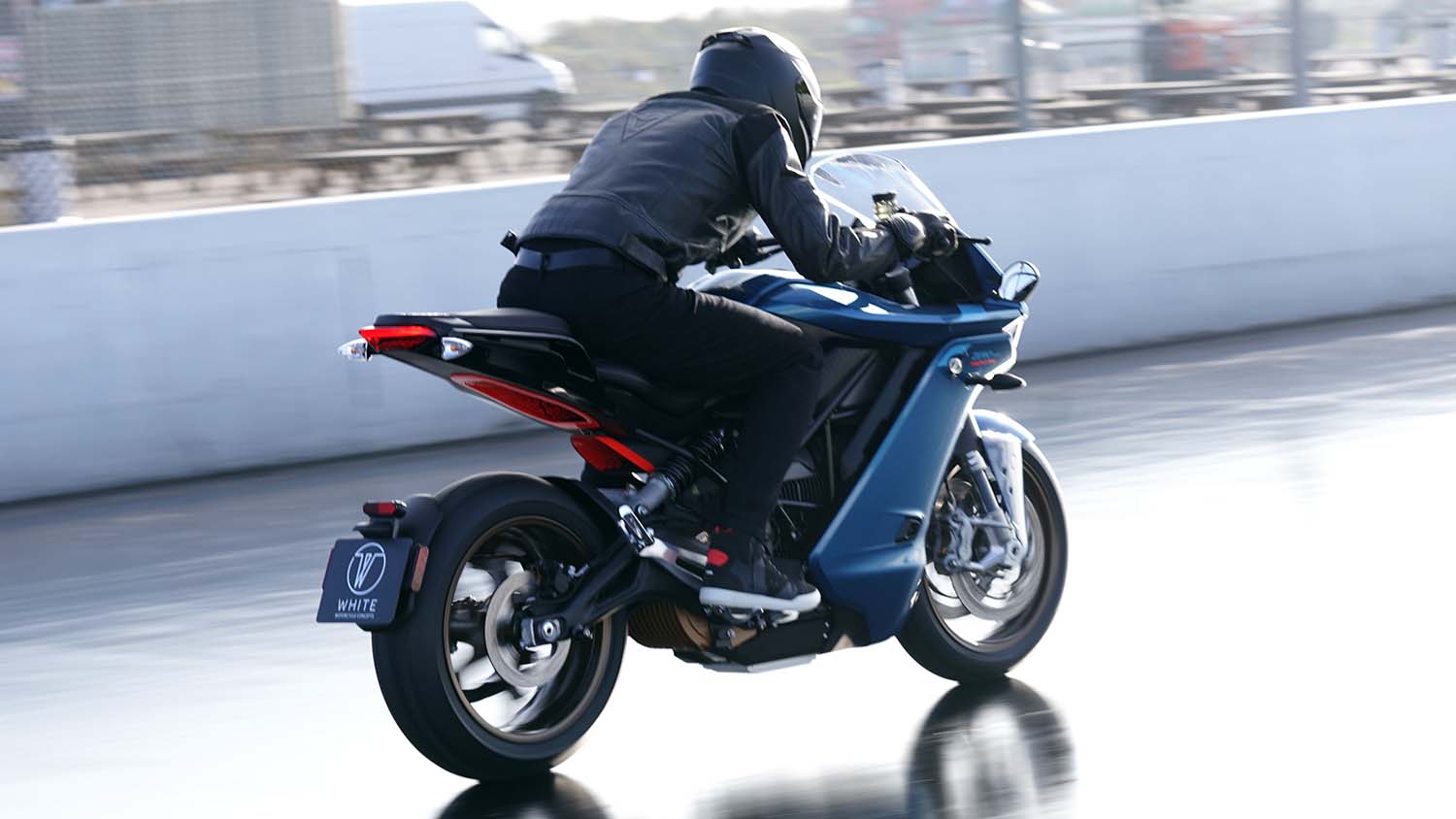
Cars have come a long way since the first Ford Model T was built back in 1908, with modern-day counterparts quite obviously larger and more curvaceous. With motorcycles, that’s not so much the case. Today’s motorbikes follow many of the same design and engineering principles as their early twentieth century predecessors.
Aerodynamics, in particular, have not been given the same consideration in motorcycle design as they have been in car design, which is big on drag coefficients and slippery forms that cut through the air.
The lightweight build and power offered by a motorbike, by contrast, means there has been little need to tinker with the design formula, and fairings are frequently created to look fast but add little in terms of airflow around them.
With electrification, however, that’s starting to change. There’s a major need for shapes that offer both the performance and range that riders crave and deliver an endorphin rush when it comes to accelerating out of a corner or expertly navigating a winding mountain pass.
“At 60 miles per hour, a bike uses 80% of its power to overcome air resistance,” notes Ian Hird, commercial director at White Motorcycle Concepts (WMC). Unlike a car, he adds, where the ‘blob’ – in other words, the driver – is encased within a steel structure that can be made more aerodynamic, the ‘blob’ on a motorbike is clearly located on the outside of the structure.
WMC boasts over 22 years of top-level motorsport experience, collaborating with the best technical specialists in F1, sports cars and MotoGP, and is now on a mission to revolutionise electric motorcycle design.
One of its first targets is duct technology, which funnels air from the front of the bike via a specially configured channel. This runs from behind the front wheel through the heart of the chassis and expels air over the rear wheel.
“Duct technology is very simple. It’s a fairing,” Hird explains. “There’s not a lot to go wrong. It doesn’t add a lot of weight to the bike and it doesn’t need maintenance. It performs the same on Day One as it does on Year Five, and it doesn’t degrade over time, whereas batteries do.”
But by reducing resistance, and thus easing the burden on batteries, a fairing can have a real impact not only on an electric motorbike’s range, but its top speed as well. The more aggressively a bike is ridden, the better the duct’s performance – the opposite situation from a battery, which drains quickly if pushed hard.
Motorbike batteries, meanwhile, present a problem, because their size is limited by the form factor. (With cars, by contrast, the design can be bulked out to accommodate larger batteries.) But battery energy density can be expected to keep rising and this shift will open up greater volumes of space within a bike’s structure to fit a larger duct.
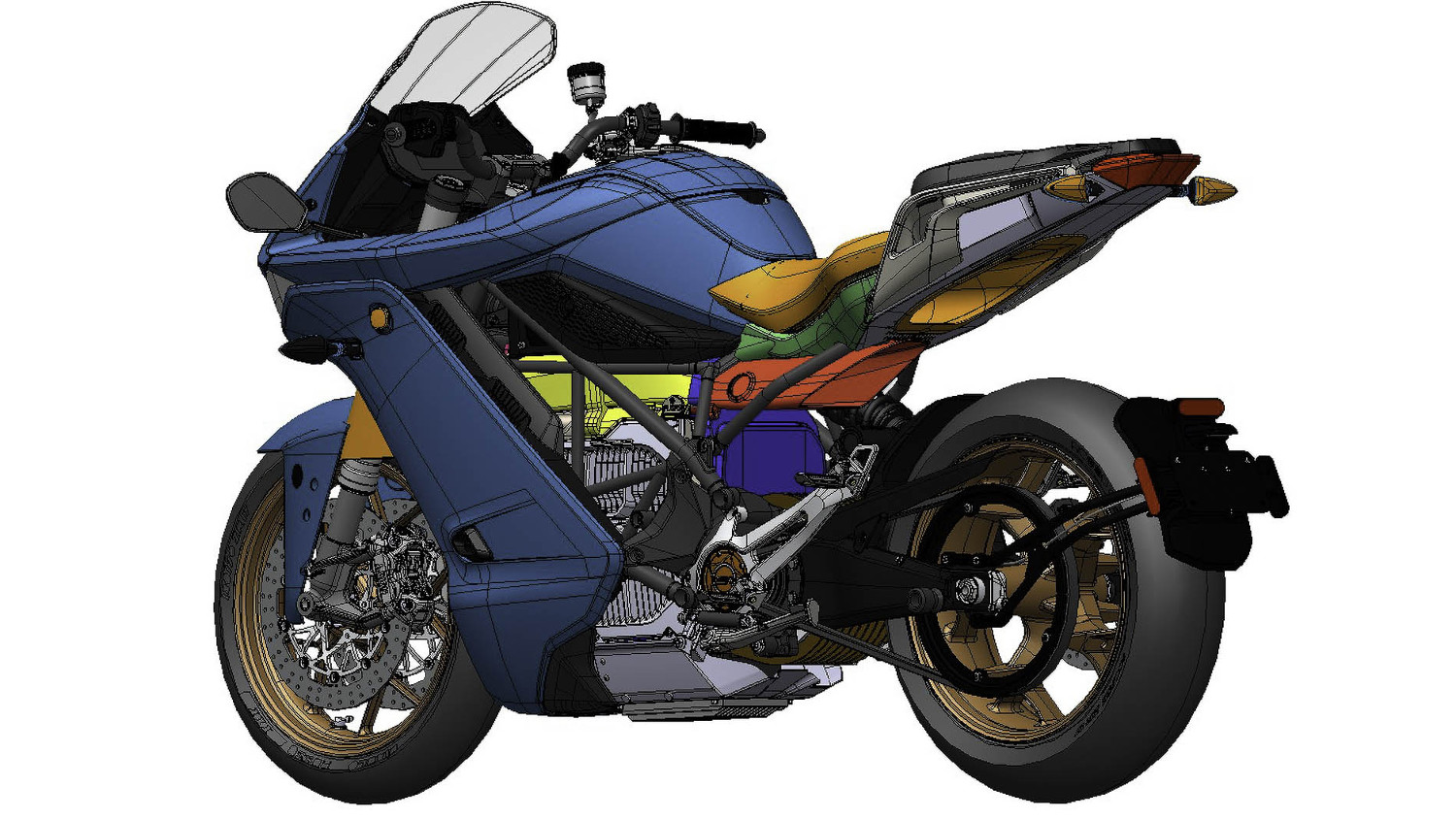
Mind the gap
Appraising WMC’s first public example of its innovative take on duct technology – incorporated in the WMC250EV – Hird acknowledges that the gaping duct that flows the full length of the bike is a pretty unmissable feature. “It’s relatively difficult to hide a hole!” he jokes.
But as a result, the WMC250EV is capable of twice the mileage on the same electric charge as compared to competitors. It’s also designed as a world speed record EV bike, capable of achieving more than 250 miles per hour.
“It’s quite copyable,” he says, but points out that WMC has a broad patent in place that covers two-, three and four-wheeled motorcycles in the UK, US, Japan and Europe.
This protection is vital, given that the company’s goal is not to produce bikes, but to work as a supplier to major motorcycle OEMs, and in that way, act as a catalyst for innovation across the industry.
“Ultimately, we’re not going to compete with a Honda or something like that. We will never win that war, so we position ourselves as a technology provider. What we wanted to do was get some proof points and build our credibility before we then start full-throttle engagement with the OEMs to incorporate the technology,” he explains.
Once WMC had got the attention of these big-name OEMs, the next task for the company to tackle was to help ‘draw the dots’, by translating a land speed-record design into a mainstream model, and demonstrate a working proof of concept.
The team began this work by looking at the other end of the spectrum, hunting for an existing bike, currently available in the market, which could offer the kind of space that WMC’s duct would need. The best candidate was judged to be the Yamaha Tricity, a 300cc three-wheel urban bike, which comes with a large under-seat storage bin designed to hold two helmets.
To this machine, WMC’s team managed to add its duct and create a hybrid working in conjunction with Northamptonshire Police. From there, they worked with Mahle Powertrains to redevelop the Tricity as a fully electric, three-wheeled motorcycle with a 100- mile range, intended to serve the needs of police and emergency first responders.
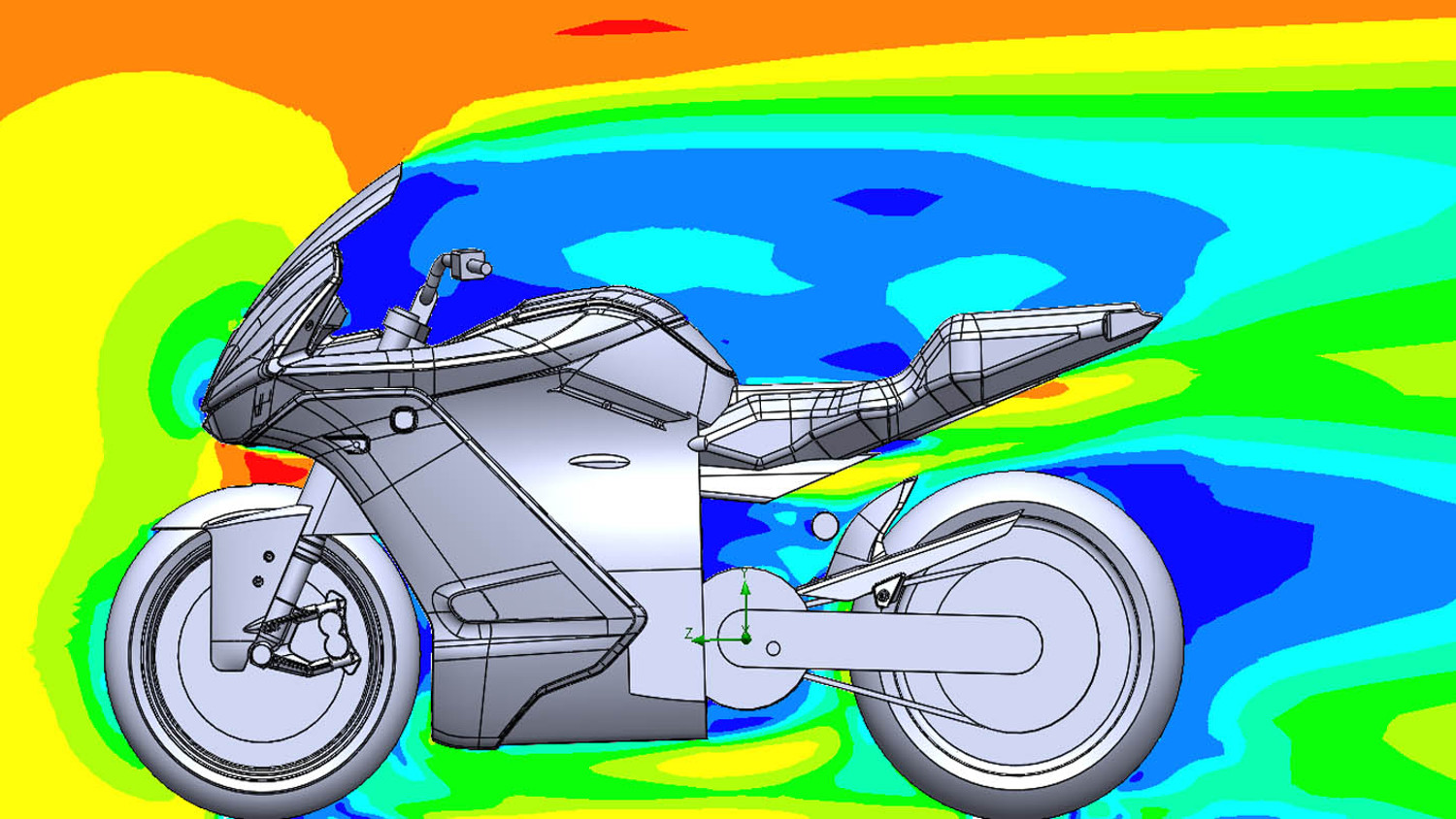
White Motorcycle Concepts – Design deliberations
With this success under its belt, WMC subsequently partnered with US-based EV bike company Zero to tackle a two-wheeled fully electric sports bike project with a reengineered SR/S. Its first project developed entirely in-house, the team explored over 39 duct designs and eight front fender designs in order to optimise the bike’s aerodynamics.
The first step, Hird explains, was defining where the intake hole might best be placed. With the land speed bike, the highest air pressure was found on the nose of the bike. But with aero rake testing – a method similar to that used by Formula 1 teams – the nose cone area proved relatively aerodynamic. In fact, it showed that a bigger problem was air getting trapped behind the front wheel and being pushed under the bike before hitting the rear tyre and creating drag.
“It’s not just a case of putting a hole through the bike and there you go – you’re off! It’s about looking at everything and how it all has an impact,” says Hird. “Air is inherently lazy. It just does the easiest thing, so you have to guide it and manage it.”
This finding led to a lot of work around the bike’s existing fairings and around the duct openings. On its back side, a lip was added to the front fender to flick air up and into the duct aperture, while shrouds were added to the front forks to help smooth the air.
The bifurcated exit, meanwhile, fires clean air effectively into the turbulence created behind the rider, further reducing drag.
Overall, the design delivers a 10% increase in aerodynamic efficiency, equating to a 9% increase in range at highway speeds.
The duct itself passes through the internal architecture of the bike via the cleanest path possible, but it still has obstacles to navigate, including the battery. Unable to change such a feature meant that the WMC team had to guide the airflow along a less-than-optimal route – but as Hird explains, even a subtle change to something like the battery casing’s shape could provide a further 3% boost in efficiency.
“The 10% that we’ve got is compromised, because there are certain points that are fixed in the bike that we can’t move. We can’t break into the battery casing, for example,” he says. “The other bit we didn’t do, because we ran out of time, was to chase around the rest of the bike and look at how other parts could be made more aerodynamic. Just from a finger in the air [appraisal], we reckon there’s maybe a further 3% to 5%, maybe even 6%, gain from looking at external parts as well. So we’d like to get to 20%.”
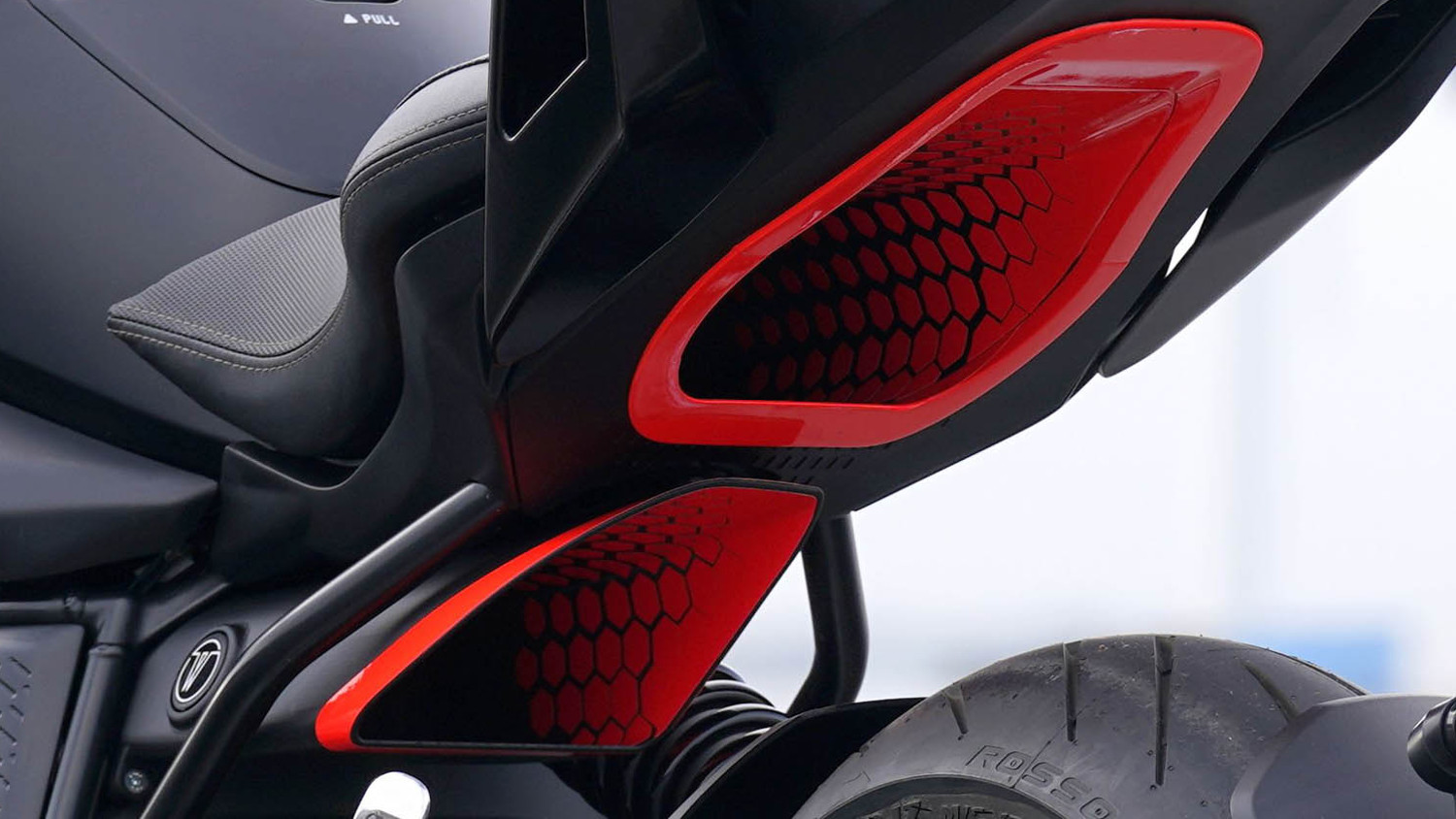
The road ahead
In future, the key to achieving greater efficiencies will be to implement the duct technology from the earliest stages of design, where WMC will work alongside engineers from a bike manufacturer. In theory, that should prove simpler than retrofitting a channel through an existing bike package.
Hird estimates that nearly 4,000 hours of engineering went into optimising the Zero SR/S ducting within the packaging constraints of the existing bike.
Zero works with Solidworks on its 3D modelling, so the WMC team adopted Solidworks too for the SR/S project. “For us, we’ll go native! We’re happy and our design engineer had good previous experience with Solidworks.”
Using Solidworks Simulation, WMC ran digital analysis to corroborate the real-world analysis derived from the physical aero rake testing.
WMC works alongside a network of partners that it has built up over the past five years, helping it to bring in extra expertise as and where needed and deliver projects to an OEM standard. One is Catesby Projects, part of the TotalSim engineering group, which was employed to assist with CFD analysis of the initial WMC250EV project.
Key to Catesby Projects process is the blending of CAD data with real-world scan data to get the full picture, which in the scenario of a motorcycle, needs to include a rider.
For this, an Artec Leo scanner is used to capture as much detail as possible, before the rider hops off and key sections of the bike are scanned in reverse order of assembly, removing parts as it went along, exposing more elements of the bike.
“That’s to try and build up the most accurate model that we can,” says Jon Paton, managing director at Catesby Projects. “The saying ‘rubbish in, rubbish out’ is used a lot in this space. It’s really important to get the scan nice and accurate, because the simulation just doesn’t work if you’re making bits up, or the accuracy is not good enough.”
The data is then passed through Artec Studio, where it is pieced together, before being imported into Geomagic for tidying and repair. Gaps may exist in areas the scanner could not access, like a rider’s armpit, for example. For surfaces that need to be redrawn, Autodesk Alias is used to produce smooth surfaces.
CFD simulations run by Catesby Projects are based on software from its sister company, Bramble CFD. “Bramble is basically aimed at making the tricky bit of setting up the simulations easy,” says Paton, highlighting the time-consuming process of meshing models and setting up boundary conditions.
“Bramble’s aim is to try and make that workflow as simple as possible. So, we drop the geometry in [as an STL file], and the boundary conditions are set for you. We set up a kinematic model for the whole project. And effectively, it’s then one click to set simulations up. If we want to change speed, yaw, corner radius, or make it follow another vehicle, for example, it’s one click away.”
When a new design iteration of a duct came through, Paton explains, it was just a case of dropping in a new STL file of the CAD into the set up and pressing start, this being one of Bramble’s big benefits over traditional CFD tools.
Having learned from the test results on the initial land speed bike project, the engineers at WMC quickly built up an understanding of how the duct performs and how to get the best from it.
“I think on the land speed bike, we did about 120 runs in CFD to get to the optimum,” says Hird, explaining that this figure dropped to WMC performing around 50 runs for the SR/S using in-house tools. “[This approach] allows us to do fewer CFD runs, because we’ve got to the 90% mark much quicker.”
The optimised design for the SR/S was then physically built using WMC’s in-house Stratasys F370 FDM 3D printer. The parts were limited by the machine’s 355 x 254 x 355mm print bed, meaning the prototype duct had to be printed and assembled in pieces.
It’s not always rapid prototyping in a conventional, next-day sense, he stresses, as some prints take 50 hours. But having a physical prototype that can be put in front of potential clients and users is massively important, he adds, because the aim is to create prototypes that look like they came from a factory. It’s what will help sell this duct as a ‘real’ product, ready today – and not just some half-baked idea.
White Motorcycle Concepts – Future flow
Beyond improved aerodynamics, WMC’s duct technology has the potential to introduce further benefits for future bikes. Electric motorcycles have a top speed and what’s known as a ‘top speed sustained’. As Hird explains, “That’s all about clipping the temperature to make sure that the batteries don’t overheat.”
By reducing resistance, WMC’s ducts already ensure batteries don’t need to work so hard, but with a sustained flow of air moving through the bike, elements like cooling fins might be added to the battery design to work with this in-built cooling channel, helping to manage temperatures.
Another element of WMC’s patent includes an aerofoil, positioned in neutral while moving, but which can close to act as an air brake. With growing legislation around brake dust particulates and pollution, the ability to reduce physical brake pad wear, and even potentially recharge the battery via a form of regenerative braking, would introduce further, welcome efficiencies to a bike’s design. For now, the main goal is to canvass opinions on the design.
“When somebody sees it for the first time, there’s always a double take, like, ‘Are there mirrors in there?’ Or, ‘Is it a magic trick?’, because the viewer can see through to the other side!” he laughs.
“If you ask people, ‘What will a futuristic bike look like in 30 years?’, then they’ll draw you some mad space thing. The reality is that it will look similar, but the technology will be better,” he concludes. And maybe, if WMC’s design meets with widespread approval, it will also have a hole through the middle.