Boom Supersonic is leveraging advanced technologies – such as CFD, composites and additive manufacturing – to create new era of supersonic commercial flight. Stephen Holmes visits Hangar 14 to find out how designs from 50 years ago are still influencing supersonic flight today
This story begins with Concorde. The jewel of commercial aerospace design, making supersonic flight a reality for the public, and a creating a legacy that has inspired many.
Nearly 50 years after its first flight, and close to 15 since it was packed away as a museum relic, few have tried to fill the void left behind.
Economy of flight, cost-per-passenger, aircraft turnaround, and mounting regulations have deterred so many, yet now a handful of contenders are mounting a renaissance of supersonic travel.
Given all the technological achievements made since Concorde’s original 1960s designs, it’s not hard to imagine why the design team inside Hangar 14 of Centennial Airport, just south of Denver, Colorado are so excited.
Boom Supersonic plans an aircraft that will fly 45 passengers distances of 4,500nm, using three engines to push the craft to Mach 2.2 – 2.6 times faster than any commercial flight today, and 10 per cent further and faster than the Concorde.
It has pedigree, coming out of the Y Combinator seed accelerator – investors in Airbnb, Dropbox, and Reddit – has an advisory board of former Lockheed Martin Skunk Works managers and NASA test pilots, plus pre orders for 76 planes already – with Virgin Atlantic requesting the first 10 aircraft.
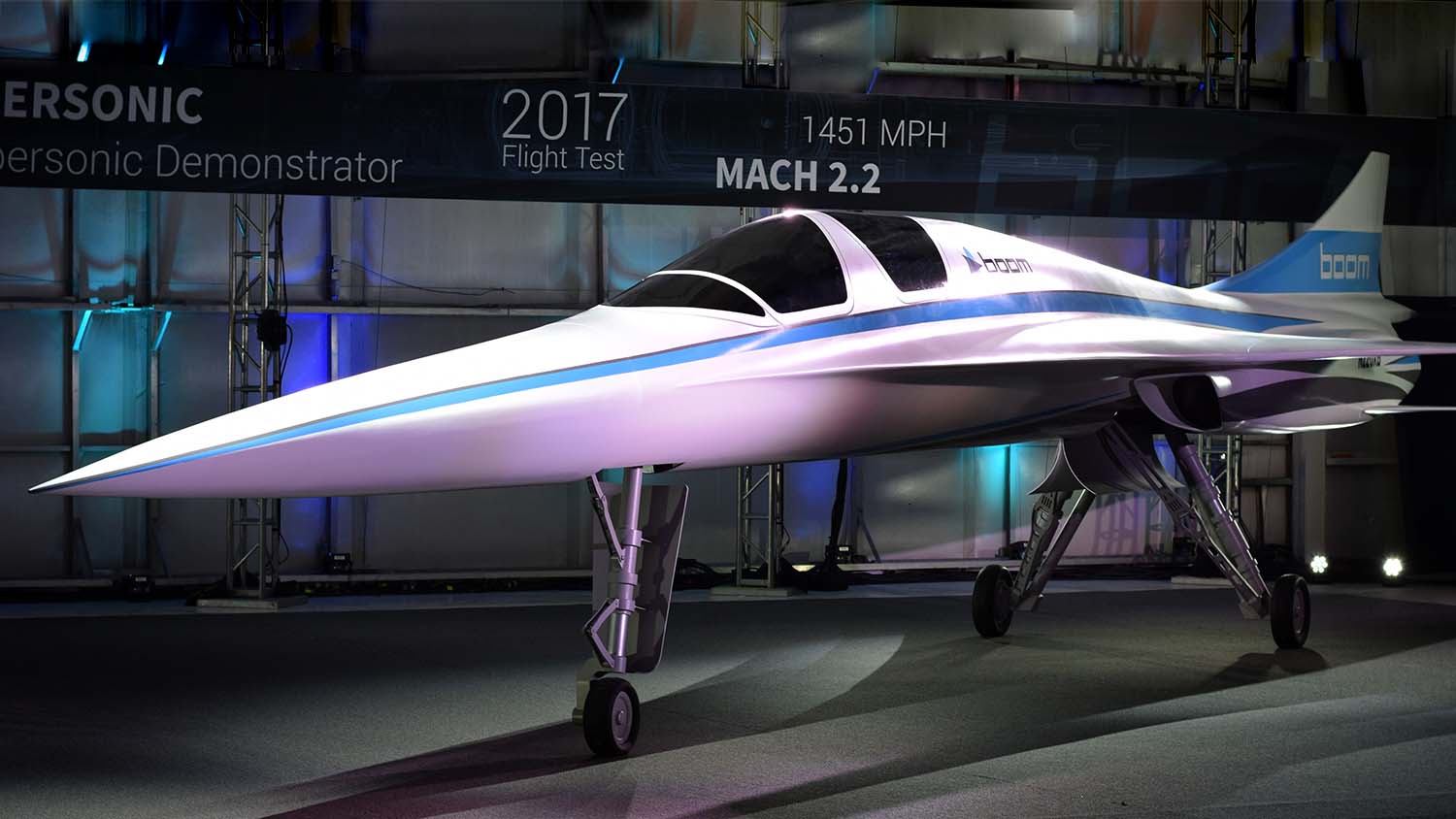
Boom Supersonic: Making supersonic flight accessible
“We’re trying to bring back supersonic air travel, and to do it in a way that regular people can afford to do it,” states Boom Supersonic co-founder and chief engineer Joe Wilding.
“The problem with Concorde was although it was a technological success, the planes flew very well, but it was a very expensive airplane to fly. [In today’s prices] it cost around $20,000 for a round trip ticket from New York to London. That’s somewhere in the order of four-times what it would cost you to fly today on a business class seat, or 20 times the cost if you were flying economy.”

To tackle this hurdle Wilding believes the answers are to be found in technology, bringing the cost of a cross-Atlantic flight close to that of a present-day business-class rate.
Eventually, the goal is to allow this to creep down to economy flights as technology and processes improve.
“That’s a few decades away probably, just due to the technology we have, but it’s certainly feasible if you keep on the technology curve,” he points out, before modestly adding: “There’s really nothing earth-shattering that we’re doing. We’re taking a very sensible approach and using the advances in the technology that have occurred.
“We don’t really have any big ‘secret invention’ or anything like that; we’re just leveraging the state of the art in aerodynamics, materials and propulsion.”
Defining the design of Boom Supersonic
Concorde is clearly a big inspiration for the design of the Boom Supersonic project, if only for the fact that it worked so well. “A lot of the things they solved 40 years ago ended up being a good way to solve a problem [even now],” explains Wilding.
With Concorde providing reliable benchmarks for supersonic flight, key points around the design were already clearly defined, such as the long, pointed body and delta wing, yet other aspects were calculated in a more traditional approach to design thinking. Such as: how big do we make it?

Concorde seated between 92 – 128 passengers, and one of the problems with a plane that big running with such high operating costs, was that it was hard to fill all the seats, and so only a few were ever built.
Boom from the very beginning analysed the most travelled business routes around the world, using this to determine the optimum size.
Settling on a craft around half the size of Concorde will allow Boom access to over 500 routes where it could fly at least one flight a day, boosting the market size and the number of planes it would allow the company to sell.
“In some ways, what we do is not a lot different to somebody designing a consumer product or anything else we certainly have sketches on pieces of paper that go back to the very beginning.
“In the end, we’re very data driven and high complexity analysis driven, but everything still starts with a very simple idea, a lot of times on paper or a really simple CAD model.
“The early stages were pretty basic, and I would say that over time we’ve refined the level of fidelity and complexity of the analytical and CAD models.”
Boom’s design process is heavily dependent on 3D CAD and simulation software, while the role of other digital technologies, such as 3D printing and composites layering will prove critical for fabrication.
“You look back to Concorde’s time in the 60s/70s and there were no computers and everything was done with a hand-drafting board, with slide-rules and a lot of physical testing – whether in a wind tunnel or structural testing.
“Now we can do almost every piece of that in a computer simulation. Whether it’s simulating a composite structure, or a metallic structure, computational fluid dynamics, simulated airflow, or thermal models or schematic models of mechanisms – all of that can be done.”
The simulation tools used are proprietary to Boom Supersonic, given that fewer engineers are looking to tackle challenges posed by supersonic airflow. While most give the engineering team “very good answers”, there’s still an occasional need for physical testing, with wind tunnel work having helped calibrate early models.
Some structural testing is required for the critical components, yet Wilding assesses that around 90 per cent or more of the development is done digitally, giving them a huge advantage from a cost and time standpoint.
“When we’re done here, we’ll have developed this airplane in probably a third of the time that it took Concorde – from first concepts through to flying passengers,” he evaluates.
Baby boom demonstrator
The next stage is the company’s XB-1 demonstrator – a one-third scale ‘Baby Boom’ that will undergo test flights to showcase its design efficiency, lightweight materials and ‘super-cruise’ propulsion system.
It’s hard to comprehend that this company, building such a craft, is still a start-up, similar to many in the modern era that use digital tools and computer processing power to tackle a once off-limits industry.
“There’s a long history in aerospace of building demonstrators,” says Wilding, citing Scaled Composites, famous for building the Ansari XPrize winning Spaceship One, but admits that the process has become less prevalent.

“I would say it’s become less popular for a bunch of reasons. For one, aerospace has kind of got to a maturity level for the most part: If you look at Boeing, its planes are very evolutionary not revolutionary at this point. They’re not going to build a half-scale 787 to prove that they can do it, when they know they can do it.”
However, as a start-up, Boom Supersonic has two key reasons to take this route: experience and funding.
“It’s very, very risky for a company to build a 175,000lbs airliner as the first thing that we ever build. Nor do we have the funds to go and do that!” says Wilding, adding that the process allows them to develop the team, build up its processes and raise money to continue on a larger scale.
Simulation software has influenced the design of the external lofting of the two-seater demonstrator aircraft, but then the shapes are imported into Solidworks for all the other components to be added.
It has already been announced that the XB-1 will fly with hardware from General Electric (engines), Honeywell (avionics), Tencate (carbon fibre), with composite structures fabricated by Blue Force.
“The demonstrator is a much simpler smaller airplane than the full-scale production aircraft,” explains Wilding.
“I’ll admit that we’re kind of stretching the bounds of Solidworks, but it’s feasible and I’ve seen other aircraft of this complexity done in Solidworks before.
“As we move into production mode we will probably use CATIA at that point just because of the levels of assemblies we’ll have and complexities of some the parts don’t lend themselves to a package like SolidWorks.”
The team are currently finalising this design, and have already moved onto manufacturing some test parts.

Additive manufacturing on the horizon
Digital fabrication forms the next step in the journey, with additive manufacturing high on the list of technologies to use in this process.
Boom is currently working with an external company on designing potential metal 3D printed parts for engine components like adjustable fuel nozzles, yet the core of the focus is based around composites moulds and layering.
A recent partnership with Stratasys is bringing in further expertise, utilising 3D printing in its Ultem material to form moulds and soluble cores for composites moulding, as well as end use parts.
The 3D printed moulds will work hand-in-hand with advanced fibre placement, laying down composite materials using 5-axis robots for maximum strength and rigidity, in much the same way as is done for military jets and the composite parts for Boeing’s 787 aircraft.

The process alongside the custom printed moulds, jigs and fixtures will allow Boom to tailor fibre direction and ply placement for parts with robotic precision and repeatability – details required for travel at supersonic speeds.
“3D printing is something we’ve started to explore for tools for all the smaller parts, and it looks to be very appealing. I think we’re going to be leveraging that quite a bit as we build the demonstrator,” says Wilding, adding that the demonstrator especially will benefit from end-use printed parts. “Certainly, things in the cockpit that we consider ‘nonstructural’.”
This extends to a long list of potential items, from instrument covers and glare shields, to the control stick for the pilot to grip.
Parts that have complicated geometry that would be hard to machine, or that you don’t want to spend a ridiculous amount of time and money building another way.
With testing scheduled for 2018 in southern California, time is of the essence, and advanced design and fabrication methods will be key to Baby Boom reaching take-off, all with the possibility of connecting the world with supersonic flight once more.