You could be forgiven for thinking that the yachts used in competitions such as the America’s Cup sail on the water. In fact they ‘fly’ above it reaching speeds of 55 miles per hour — often faster than the speed of the wind. The force generated from the rigid wing sails together with the speed produced, lifts the catamarans out of the water to be supported on tiny blades of carbon fibre. It’s a spectacle that defies logic.
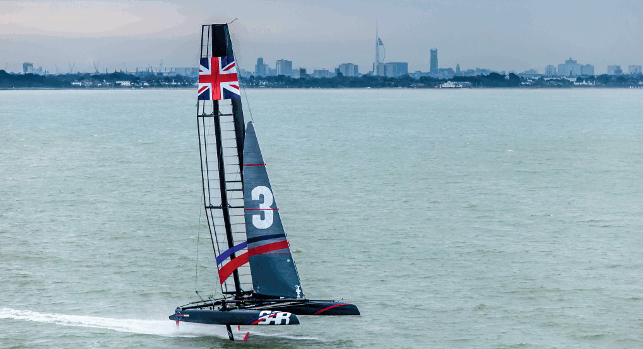
Ben Ainslie racing will attempt to win the 35th America’s Cup in hyrdofoiling catamaran
Sir Ben Ainslie, a British sailor with a mantelpiece full of sailing trophies not to mention four gold Olympic medals, has lived and breathed sailing for most of his life.
In 2013 he was part of the Oracle Team USA crew that sailed to victory ahead of Emirates Team New Zealand in the 34th America’s Cup. Although it was a glorious moment lifting the trophy above his head, he did think “wouldn’t it be even better if it was with a British team”?
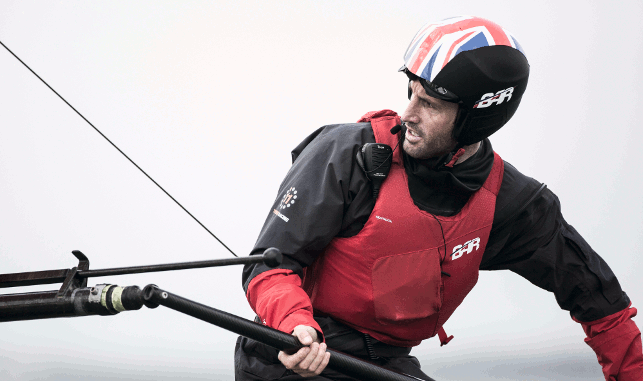
Sir Ben Ainslie, BAR team principal and skipper
And so the idea for Ben Ainslie Racing (BAR) was hatched with the intention of bringing the America’s Cup back to Britain (see box piece below). With private investors and corporate partners onboard, Ainslie assembled a sailing crew, a design and engineering team, boat builders and racing support.
Then on 11th June 2014 his £80m America’s Cup project, which includes a £7.5 million grant from the government, was launched at the National Maritime Museum in London in the presence of the Duchess of Cambridge.
Design race
The way the America’s Cup works is that the previous winner can decide on the design parameters of the yacht as well as choose a location and date for the next challenge.

Testing the AC45 prototype in the waters of the Solent from the team’s temporary base in Southampton
So, Oracle Team USA has decided that the 35th America’s Cup will take place in Bermuda in June 2017 in 62 foot hydrofoiling catamarans.
As the America’s Cup is as much a design race as a sporting one, one of the first job roles Ainslie wanted to fill was that of technical director and he knew the perfect man for the job — Andy Claughton, an experienced America’s Cup designer who has been involved with the competition since 1983. Ainslie met Claughton when they were both part of Team New Zealand for the 2007 America’s Cup.
“This is a great opportunity because in my lifetime the stars have never aligned as well as this for an America’s Cup challenge.
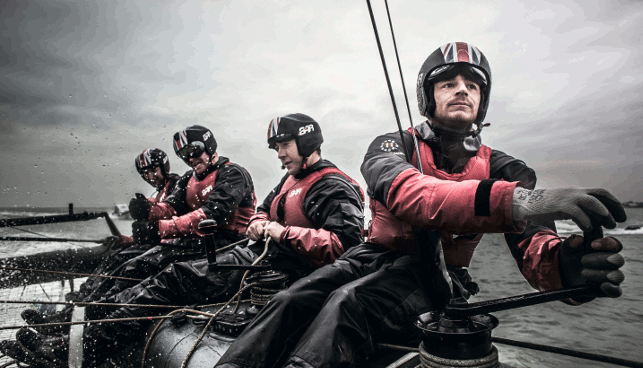
Ben Ainslie assembled a hand-picked sailing crew to help him win the 35th America’s Cup in Bermuda in June 2017
“We have a very talented skipper, committed investors and we are racing in a new class of boat, which to some extent levels the playing field. Also, it’s a very expensive boat to build and the fact that we are racing in Bermuda has prevented more teams from entering. So, it’s the best shot we are going to get for a while,” says Claughton.
On the wing
With tight design specifications, to the naked eye the yachts will all look very similar especially with ‘one design’ components such as a common wing sail geometry. These sails are rigid, rather than traditional cloth, and in many ways mimic how early airplane wings were made — stiff ribs and a covering.
“This is not new technology, it’s absolutely the kind of stuff the Wright Brothers wrestled with in the early 1900s. There is a lot of data on the performance of these kind of wings but what’s new is putting them on a racing yacht,” says Claughton.
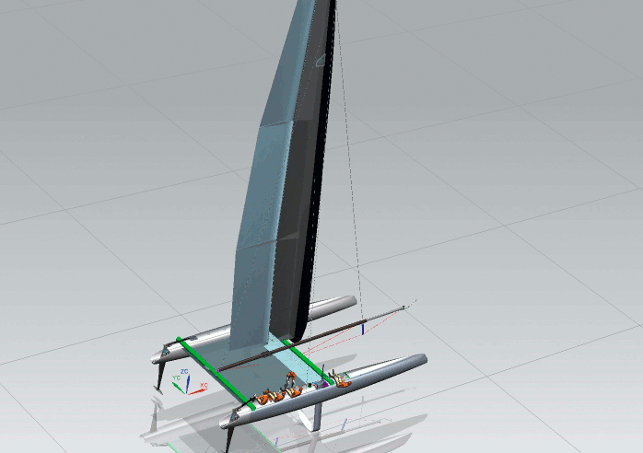
The BAR design team use Siemens NX during the design and development process
“To adapt the wing for sailing you have to give it a degree of controllability so it has an adjustable camber control and you can control the twist or the wash out of the wing from the platform. For this reason it is quite unusual compared to an airplane wing because you are actually adjusting the shape the whole time. It is never going to go mainstream but it is fantastically efficient.”
The speed produced by these wing sails lifts the catamarans out of the water on the hydrofoils that the boats ‘fly’ on. About the size of a stand-up paddle board, these carbon fibre hydrofoils extend down from the bottom of the hulls to carry the entire weight of the catamaran.
“Once you can take all the weight of the boat on the hydrofoil and the hulls are out of the water, you have none of the drag of the water flying past the hull so it is very efficient,” explains Claughton.
Technical partnerships
To gain a competitive advantage, BAR has also turned to the design and engineering expertise from other industries.
As Claughton says, “One of the things we have set out to do with BAR is to engage with the UK technical community outside of the marine industry. I think that is going to prove very valuable for us in terms of the sophistication of solutions we can get onboard the boat.”
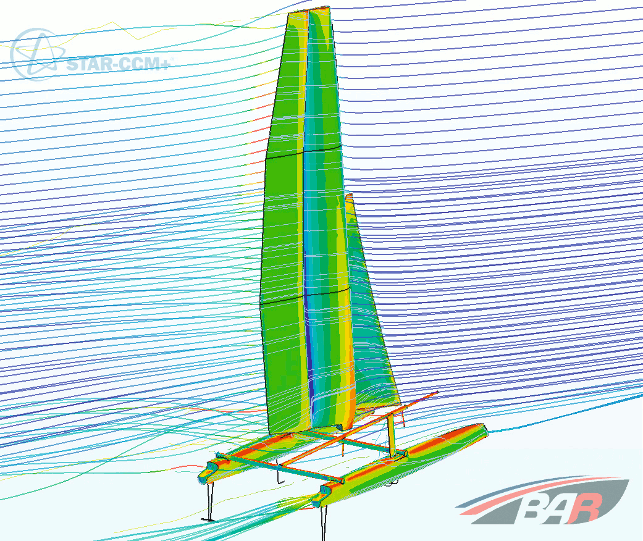
For computational fluid dynamics (CFD) work, BAR use STAR-CCM+ from CD-adapco
Motorsport, in particular, uses many of the same principles and faces similar challenges, specifically in Formula One where the rules also curtail major changes being made to the design, meaning that a lot of effort goes into making quite small improvements.
To tap into the expertise and experience of this industry, BAR has joined forces with Red Bull Advanced Technologies (RBAT), a division of the Red Bull Formula One group.
“Yacht racing has become very much like car racing in that it is very seldom that you are actually going at a fixed speed — you are always either decelerating into a tack or gybe, accelerating or going round a corner. So we are hooking into their expertise with
that,” says Claughton.
In-house the BAR team has struck up a partnership with a variety of technology partners including Siemens. Its NX tools for CAD and Teamcenter for product lifecycle management (PLM) forms the digital backbone of the boat development process.
The design process begins, like most others, with sketches. When the final concept is agreed upon, it is modelled up in NX. The challenge, however, with this project is not only the sheer number of components but how those components have to fit together in quite a constrained space.
“There are tens of thousands of individual components many with control systems running to several hundred thousand and in the controls there will be several hundred thousand lines of computer code. So, there is a lot going on behind the scenes,” says Claughton.
Importance of simulation
The in-house design team, which is currently 25 strong, does not work in isolation on individual parts of the boat but rather their skills are grouped in terms of stress analysis or computational fluid dynamics (CFD) with each aspect of the design drawing on those skills.
“We try to keep a very integrated design method and that is one of the things the Siemens software lets us do — anybody anywhere can always access the most up-to-date version of the design,” comments Claughton.
As the rules prohibit actual sailing of the 62 foot catamarans until around five months before the competition, although the team have been able to make 45 foot prototypes, most of the important early design decisions will be based on data from CFD simulations.
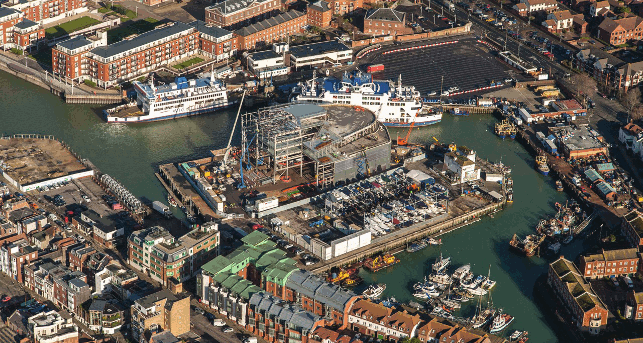
The construction site of the new headquarters and BAR Visitor Centre in Portsmouth, which will be completed in May 2015
These simulations are particularly vital for yachts travelling at the speed that the America’s Cup challengers race because it’s less about hydrodynamic drag and more about aerodynamic drag. So, another important partnership for BAR has been with CD-Adapco, provider of the CFD simulation tool STAR-CCM+.
“There is no automation of the control of the boat, it’s only the helmsman who is adjusting the angle of attack of the hydrofoils that is controlling the ride height and also stopping the boat capsizing. It’s a real handful but as the tips of the daggerboards [a retractable centreboard] are interchangeable, we can make them a different shape.
“Some shapes are very fast but hard to control whilst other shapes are more easily controlled but are slower. So, this is one example of how CFD is helping us come up with the best solution,” explains Claughton.
Making sure the product works in a virtual environment and having confidence in the simulation tools does mean that less money is spent on building physical prototypes.
When prototypes are made, the team either relies on its own in-house 3D printer or sends the files to additive manufacturing bureaux to produce the prototypes.
The final parts are then manufactured by companies throughout the world and the AC45 testing boats are assembled in-house.
The sailing crew then takes it into the waters of the Solent and gathers data for Claughton’s team who then make any revisions and tweaks to the CAD models.
“The sailing team’s input is absolutely crucial to what we do. It’s a symbiotic relationship — we can’t work in isolation from them. It would be a bit like designing a set of golf clubs and then giving them to Rory McIlroy on the morning of the British Open and saying ‘There you go Rory, you’ll be OK with these’,” smiles Claughton.
New 3D sailing simulator
The latest addition to the design office is a 3D sailing simulator, which showcases another example of BAR drawing on the experience of those outside the marine industry.
“We have the same drivers that push Formula One to work on simulators in that we are not allowed to build a full size prototype for another year. It’s also expensive to build and take boats on the water, so investing in a simulator was a logical development really,” comments Claughton.
Its use will be twofold: firstly for testing design developments by the design team and secondly for training by the sailing team. This not only provides an important feedback loop between the two teams but also an equally important feedback mechanism within the design team’s own processes. So, the models that are being used to calculate theoretical data on how a particular design of boat will perform are exactly the same models that the simulator uses.
According to Claughton, the simulator is one of the team’s most prized possessions and is in constant use, except of course when the Duchess of Cambridge came to visit in February.
The Duchess received the inside track on the team’s progress and was privy to some of the technology being used, even donning an Oculus Rift headset to view the 3D visuals at the simulator.
Bringing the cup home
So, with all this investment in in-house skills, technical partnerships and cutting-edge technology, can BAR indeed bring the America’s Cup home?
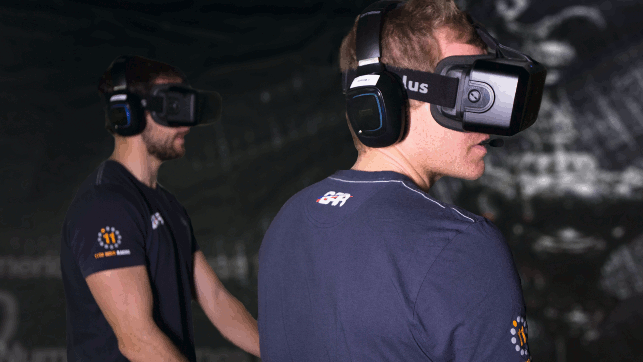
using the Oculus Rift headset to view 3D visuals at the new 3D sailing simulator
Time will tell, but in the meantime the BAR team is enjoying the experience including Claughton, who says, “It’s good to be working on a viable America’s Cup challenge and doing it with the home team and with one of the best sailors in the world – it’s an opportunity of a lifetime really.”
To witness Ben Ainslie Racing’s attempt to #BringTheCupHome, the first qualifying races — The America’s Cup World Series — will be taking place on home turf from 23 to 26 July 2015 in Portsmouth.
Tickets available: ticketmaster.co.uk/ACWSPortsmouth
History of the America’s Cup
Set up in 1851 by the Royal Yacht Squadron, the America’s Cup is the oldest international sporting trophy in the world.
The first race was a single lap around the Isle of Wight. The black schooner America won and to honour the victory, it was renamed the America’s Cup and became a challenge trophy.
As a challenge competition the defending champion has the right to set the rules, choose the venue and format of the next one.
Oracle Team USA, which won the 34th America’s Cup in 2013 in San Francisco in a 72 foot catamaran, has decided that the 35th America’s Cup will be held in June 2017 in Bermuda.
So far six teams have taken up the challenge of racing the 35th America’s Cup: the defending champion Oracle Team USA along with the challengers Emirates Team New Zealand, Artemis Racing (SWE), Ben Ainslie Racing (GBR), Luna Rossa Challenge (ITA) and Team France.
There is a lengthy qualification process to decide on the final challenger who will race against the defender. All teams will race in foiling 45 foot catamarans (AC45) in the 2015/16 America’s Cup World Series in locations around the world, including in Portsmouth on 23 to 26 July 2015.
The team that wins the ‘Challenger’ series will go on to race against the defender in a 62 foot foiling catamaran (AC62) in the 35th America’s Cup.
A British team has never lifted the trophy and the hope for the next one is that Ben Ainslie Racing will #BringTheCupHome.
With investement in cutting-edge technology will Ben Ainslie Racing bring America’s Cup home?
Default