Formula One (F1) is fast-moving business – around 90 per cent of the components within an F1 car will be redesigned over the course of a racing season.
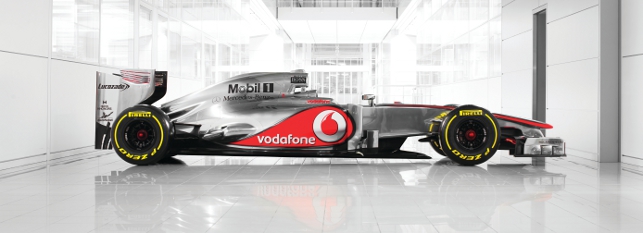
The challenge for the design teams is to take complex forms created in CAD and manufacture those components in a way that is not only dimensionally accurate, but which also meets rigorous weight and strength criteria.
It’s at the McLaren Technology Centre in Woking, Surrey, where the McLaren Racing team designs and develops the Vodafone McLaren Mercedes Formula One cars.
In order to design cars that win races, the designers and engineers use the most advanced technologies and processes. This includes 3D measurement technologies and since 2010 Faro Technologies, provider of computerised measurement devices and software, has been the McLaren Group’s official sponsor of measuring systems.
Kitted out
The first FaroArm went into the composite inspection area followed by the Laser Line Probe, which is an attachment on the end of the Arm that’s used for non-contact measurement. It enables the user to scan the surface of a pattern, taking millions of points.
“Using that cloud of data it shows the operator a colour map deviation that enables them to easily compare the item with the CAD model.
In simplistic terms, where the cloud goes green, that area is within tolerance. If the colour map turns red that signifies an excess of material, and blue shows that it’s too low,” explains Andrew Tagg, regional manager UK at Faro.
The next stage of the collaboration was bringing Faro Gage into the machine shop.
This contact mechanism uses a ball probe to enable the user to check the geometric dimensions in 3D. “By enabling you to quickly check a machine tool or within a cell of machines, this eliminates all the bottlenecks you get with traditional methods,” comments Tagg.
“Our aim is to speed the process up, get results quicker. A process that would have taken hours now takes minutes. Rather than reams and reams of paper with values on, you have a graphical display that’s easy to interpret.”
Head of quality at McLaren Racing, Alex Smith, explains that Faro measuring systems are used for a number of purposes in the company: “Fundamentally, at the front line, we use it for quality control – to ensure that parts meet their design specification and intent. We’ll use the equipment on both carbon fibre and metallic components, as well as the patterns and moulds that are used to create carbon fibre components. Pretty much every part that comes through the business, in fact.”
Since partnering with McLaren Racing, representatives from Faro have been into many areas of the Technology Centre including the wind tunnel inspection area where the FaroArm is also used.
“The FaroArm can be used to set the datum on what the aerodynamicists call the ‘spine’ on the wind tunnel car, and they provide a live digital readout for precise positioning of the components on the spine.
That’s a benefit in terms of speed and accuracy, as well as flexibility, because those parts can be readjusted to very precisely defined co-ordinates,” explains Tagg.
Analyse that
The McLaren team uses the data generated from the Faro interface to inform it about the quality of the components and whether there are any defects.
The data can also be analysed to indicate how capable the manufacturing processes are. “That gives us a lovely feedback loop right the way back to the design process,” says Smith.
“We can have discussions with the designers about tolerances and getting everything right first time so that we have a good yield of parts.”
Two way street
This partnership has benefits for both companies.
For Faro there is a tangible benefit in terms of feedback from a customer that is operating at the very limits of technology.
“They’ve helped us develop our software, providing fantastic feedback that has driven through a lot of performance improvements, such as shortcuts for commonly used subroutines,” says Tagg.
Equally, McLaren Racing is keen to push boundaries with the very latest technology developments. “I always look to get the latest Faro products into the building and I know they’re equally keen to test their new developments in such a demanding environment,” concludes Smith.
Faro’s 3D measuring systems help McLaren push the technology boundaries
Default