Setforge, a brand renown for its hot forged component manufacturing across construction, aerospace, and transport has revealed how it has delved into carbon fibre-reinforced polymers as it looks drop weight from the parts it builds.
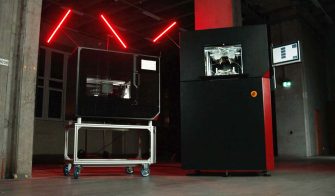
A subsidiary of Farinia Group, Setforge’s specialisation has been in forging using standard metals such as steel, aluminium, and titanium for over a hundred years. But with the shift to reduce waste materials and develop lightweight components for better fuel economy and electric vehicles, the company collaborated with 9T Labs for efficient composite parts.
9T Labs explains that is has collaborated with Setforge to apply its Red Series Build and Fusion modules to create an efficient additive manufacturing process alternative to the traditional manufacturing of suspension brackets.
Using carbon fibre-reinforced polymer (CFRP), 9T Labs Build Module produces a fibre layup using its Fibrify design software, which is linked with commercially available structure simulation software, in this case Ansys, to place carbon fibre materials where needed to achieve optimal quality output while reducing excess material waste.
The software allowed for the solid part of the bracket to be reinforced with straight fibres and additional surrounding bands to the reinforce holes, using the 9T Labs Build Module 3D printer to produce the parts.
A separate Fusion Module applies heat and pressure to fuse the preform part to produce a high fibre volume of up to 60%, and a reduced void content (<1%), strengthening components.
Setforge says that the benefits of continuous carbon fibre over metal includes a tensile modulus of 230GPa above that of steel (~210), with increased advantages in stiffness and low weight – 1.79g carbon fibre density compared with 7.7 – 8.1g steel density – that can be tuned along with all processes using the Fibrify software.
The team say that the ability to tune part processes has streamlined production. Digital prototyping and structural validation have helped reduced the costs by 22 per cent and removed slower traditional prototype iterations.
The CFRP suspension brackets weigh in at 307g a reported 67% saving on metal alternatives.
With streamlined serial production in mind, 9T Labs’ collaboration with Setforge is anticipated to expand production volume up to 20,000 composite parts a year. Along with Setforge’s current markets it’s hoped that additive manufacturing will open new market opportunities, including luxury products, sports equipment, exoskeleton and drone sectors.