Tower Tool, a company specialising in moulds for rubber seals, recently completed its largest project – the cargo-door seal for the freight version of the Boeing 777.
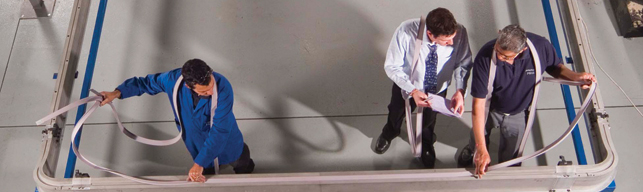
The seal for the Boeing 777 was produced by Tower Tool using Delcam software
The seal measures three by three metres square and has a small and variable cross-section. Like many of the company’s projects, the moulds and the associated checking fixture were supplied to Meggitt Polymers and Composites.
“When the Boeing representative visited us, he seemed a little nervous about having a relatively small company responsible for the tooling for such a critical component,” admits Myles Ball, Tower Tool’s managing director.
“He was a lot happier when the first seal was delivered in 18 weeks, six weeks earlier than the norm for a seal of that size. In addition, the seal fitted perfectly and worked first time.”
Tower Tool has specialised in moulds for rubber products, in particular for aerospace seals, since it was founded in 1957 in the centre of Leicester.
The company took its name from the nearby clock tower. It moved to its present site in 1995, where it has bigger and better premises. Meggitt, together with GKN and Trelleborg, are the company’s major customers, but it also undertakes work in other transport sectors and for medical applications.
Sound investment
Unlike many customers who have bought Delcam software after a recommendation from an existing user, Ball first invested in the software in 1998 after speaking to a company that had decided on a cheaper CADCAM package. “The owner told me that he had made a big mistake and that he wished he had paid the extra for the Delcam system,” he remembers. “From that moment, I knew I had to have Delcam software. The demonstration convinced me; the software seemed to be far more intuitive than the other packages I’d seen.”
Ship shape
Comments from a Delcam user were important when new engineering manager, Andy Lowe, arrived at Tower Tool and began using the PowerSHAPE design software.
“I found PowerSHAPE to be very different from the system I had used previously but a sub-contract draughtsman that we used told me it was the best system for tooling design so I stuck with it. Ironically, I became so much more productive once I got used to the different way of working that we didn’t need to subcontract as much of our design work,” says Lowe.
“The flexibility of the software is important to us,” adds Ball. “For some projects, we are supplied with a fully-detailed CAD design of the seal so we use PowerSHAPE just to create the mould.
At the other extreme, we can be sent drawings of two adjacent parts and are told to create something to fill the gap between them so we need to design the seal from scratch. PowerSHAPE also makes it very easy to make checking fixtures from the tool designs.”
A cut above
“The PowerMILL CAM system also gives us many benefits, not least the ability to machine undercuts in three-axis by using special cutters,” he continues. “The flexibility of rubber means that undercuts are far more common in rubber moulds than in those for plastics.”
But for Ball, even more important has been the support that the company has received from Delcam. “Whenever we have any problems, the help-desk staff go out of their way to help us. The regular training days are invaluable in keeping us up to date with developments in the software and the latest design and machining techniques,” he concludes.
www.delcam.com
www.tower-tool.co.uk
Small screen
Korean mouldmaker Young Shin Corporation specialises in the manufacture of plastic moulds for LCD televisions for major brands such as Samsung, Toshiba, Hitachi, Sharp and Panasonic. Four years ago the company implemented eight seats of Delcam’s PowerMILL software in a bid to reduce the delivery times for its moulds and also to cut its manufacturing costs.
Following this successful implementation, further orders took the total to 18 seats of PowerMILL, including two for continuous five-axis machining, plus two seats of Delcam’s feature-based CAM system, FeatureCAM, to generate programs for gun-drilling, and one of the PowerINSPECT inspection software for On-Machine Verification as part of the company’s quality-control procedures.
The use of PowerMILL and the switch to shop-floor machining have led to a significant increase in productivity. Previously, the machine operators would often have to wait for many hours to get NC data from the CAM office. These delays have been eliminated now the operators generate their own programs, so shortening the overall production time.
Furthermore, because the operators are very experienced in the latest machining techniques, they are better placed to decide upon the most appropriate cutting tools for each part of the manufacturing process. As a result, machining efficiency at Young Shin has increased, the quality of the moulds, and of the products manufactured with them, has improved, and production times have been reduced.
www.yscorporation.en.ec21.com
PowerMILL and PowerSHAPE seal a moulding company’s success