Passengers may take them for granted as they walk from the terminal onto a plane, but passenger boarding bridges play a vital role within airports. Otherwise known as fingers, these glass and steel load-bearing structures feature numerous tunnels to enable comfortable boarding.
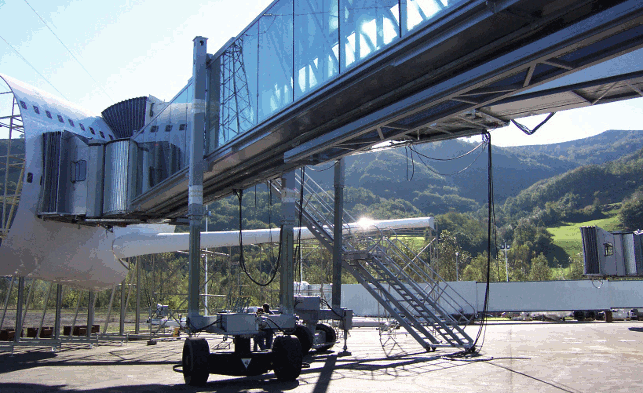
Lift-and-drive system connecting a passenger boarding bridge to an aircraft
Spanish manufacturer ThyssenKrupp Airport Systems designs and builds these structures. To date it has installed more than 3,000 of them at airports around the world.
A crucial element of the bridges is the drive system frame, or the bogie, that has to support 50 metric tonnes of structure while providing the forward, backward and lateral movements needed to dock to the aircraft.
The bogie originally used in ThyssenKrupp passenger boarding bridges was designed in Germany 20 years ago using hand calculations. The limitations of manual design methods meant that prototypes had to be constructed and tested in evaluating each design iteration.
Testing identified problems with early design iterations but provided limited diagnostic information,so engineers had to rely on intuition to modify the design. The time required for physical testing limited the number of load-case scenarios that the engineering team could evaluate. Historically, it took 18 months to iterate to a bogie design that met specifications.
Recently, ThyssenKrupp invested in Ansys simulation tools, specifically Ansys Workbench, Ansys DesignModeler and Ansys Mechanical.
Workbench provides an integrated environment to substantially reduce the time required to prepare models for analysis, including defining loads, constraints and contacts. DesignModeler delivers a fully parametric environment for defining and editing design geometry so that design engineers can evaluate many different design variations in a short time.
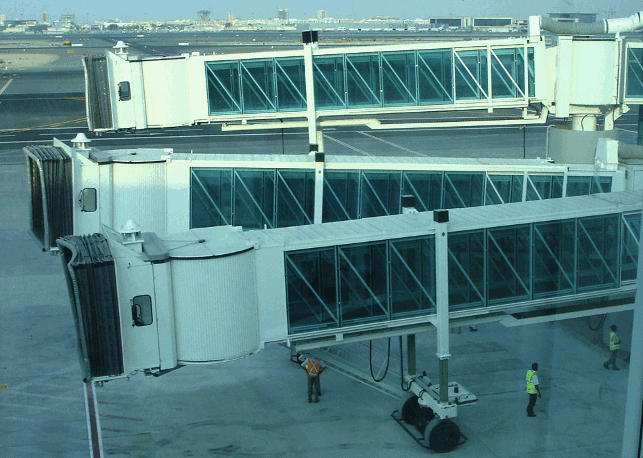
Triple-stand passenger boarding bridge (PBB) at Dubai Airport
Ansys Mechanical offers the ability to analyse the wide range of physics — stresses, deformations, vibration characteristics, reaction forces and residual strains — required to determine performance of a
passenger boarding bridge.
Redesigning the bogie
Recently, the decision was made to redesign the bogie using simulation as an integral part of the design method. As a first step, the original CAD geometry was transferred into DesignModeler.
At the same time, physical tests were carried out to validate material properties and determine loads based on the original design.
Engineers used Ansys Mechanical to evaluate the stress behaviour of the original part and the effects of design changes, such as increasing the radii in high-stress areas. Steel was chosen over cast iron as it provides better control over material properties.
ThyssenKrupp engineers then created a new design of the part in DesignModeler. The model of the previous design used all solid elements because of the complex geometry of the cast part. It had a total of 1.3 million nodes.
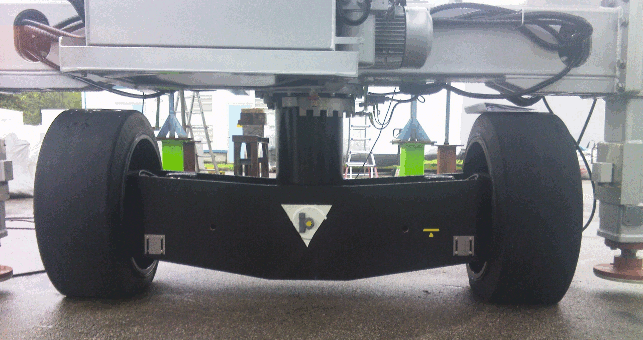
Lift-and-drive system
The model of the new design with a combination of shell and solid elements used only 300,000 nodes. Running this analysis with all solid elements would have taken about 12 hours per load case. The use of shell elements reduced the solution time to three hours per load case.
Engineers added constraints and loads to the model and simulate edits behaviour. One of the more complex load cases involved jacking up the bogie to change one wheel. When the jack rises, the bogie flexes under bending loads, and the load is transferred along the lift jack opening. A nonlinear contact was used to maintain the contact at the right location as the part flexes.
Using Ansys DesignModeler, the engineering team reproduced stiffness and other behaviours of this complicated component while defining many load cases and taking nonlinear material and contacts into account. It performed stress and buckling analyses, to determine if interior ribs were required, then validated the forward, backward and lateral movements of this part.
The interaction between the wheels and the apron surface was analysed for different combinations of material stiffness and contact conditions.
Optimising the design
Once the analysis identified the part’s problematic zones, engineers added and removed material manually; they also used the shape optimiser within Ansys Mechanical to improve the geometry.
An envelope of the initial volume was defined to determine the location of the fixed points where the bogie attaches to the wheels and lift. Loads and fixed supports were applied. The software approximated the initial structure as a large volume. Material was then reduced at locations with low stresses, resulting in a more optimal structure.
The resulting optimised design weighs ten per cent less than the original design while providing an allowable load of 80 metric tons (88 tons), 33 per cent more than the previousgeneration design.
Engineers ordered a prototype of the new design and performed component-level physical testing that verified the simulation results.
Confident in the design results, rather than prototyping just the drive system, a complete bridge with the new bogie design was built.
Testing showed that the design worked perfectly, so it went into production only three months after the beginning of the design process — reducing design time by almost 89 per cent from the hand-calculation build-and-test method used for the original design.
In just a few months, ThyssenKrupp engineers thoroughly evaluated the bogie’s behaviour under many load-case scenarios.
The result is a product that far exceeds design specification at a manufacturing cost equal to the previous design.
Ansys simulation tools help ThyssenKrupp Airport Systems create passenger boarding bridges
Default