With the original lighting parts broken and no longer available, we learn how AME-3D reverse engineered a cost effective replacement option to bring light back to a London housing development
An increasing issue for maintenance and management companies is that, while products are lasting longer through better design, manufacture and materials, sourcing replacement parts when they finally do fail is an issue.
The car park and entry lights of one of London’s residential developments managed by Towndate Property Management had seen a gradual deterioration in recent years after 30 years’ worth of UV light damage, before one light lens finally failed completely, cracking badly.
Towndate found that off the shelf replacements were not an option, with the OEM having closed down years earlier.
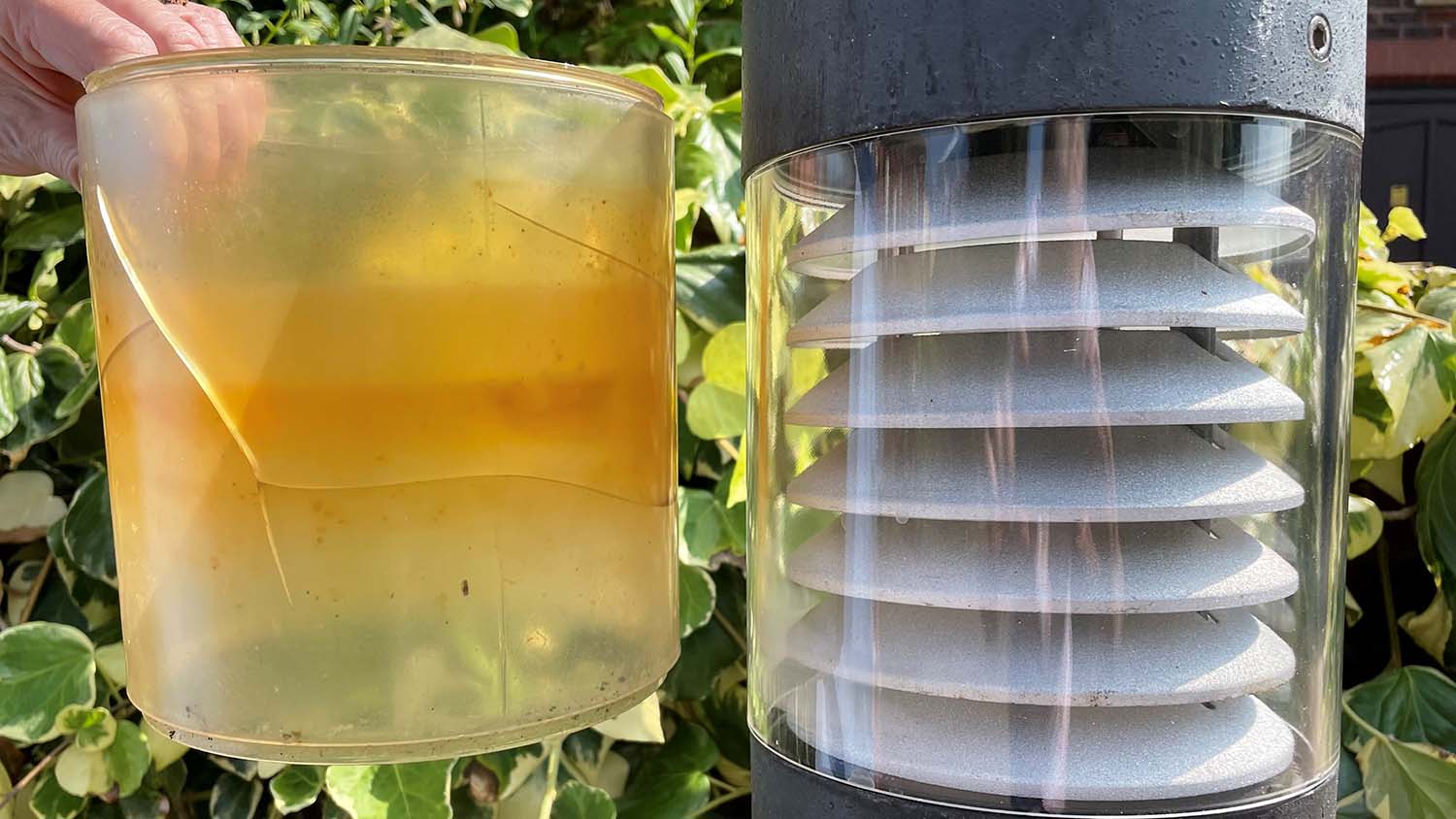
The reality of what had began as replacing a few plastic parts became an increasingly costly option – fully replacing all the bollards, rewiring the electricals, digging-up the car park and pedestrian entryways, and several weeks’ worth of disruption to all residents.
Thankfully Towndate thought to investigate an alternative, less costly method of sourcing the replacement lenses.
Working with AME-3D, a 3D Printing and low volume production bureau, one of the cracked light lenses was sent to the team to investigate, review and reverse-engineer.
As the light needed to be clear and would be exposed to years of UV light, AME-3D recommended using a UV stable resin system that could future-proof the lenses from yellowing and eventually becoming damaged to the same extent again.
AME-3D created a finished master that was then used that to create silicone tool, then employed their vacuum casting technology to cast the lamp lens mouldings.
After the finishing and tooling processes were completed, new lenses were delivered and installed at the housing development, reducing cost and waste, and leaving Towndate in a better position to repair and mend in the future.