Turning a legacy of track victories into successful road going business is historically the way to motoring success. From Ferrari to McLaren, it’s a well-worn route that has served many well.
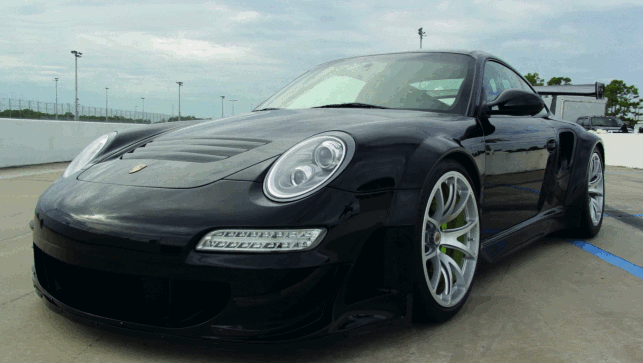
Porsche 997 Turbo with FDM-enabled components
Champion Motorsport’s racing legacy includes a win at the 24 Hours of Le Mans and five straight American Le Mans Series LMP1 championships: two as a private team and three as an Audi Sport North America factory team.
With the trophy cabinet suitably stocked, the team is now using its racetrack knowledge to develop and manufacture aftermarket performance upgrade parts for sports cars.
Producing the likes of exhausts, wheels and turbochargers, boosting power levels and shaving off weight, the parts increase the car’s abilities.
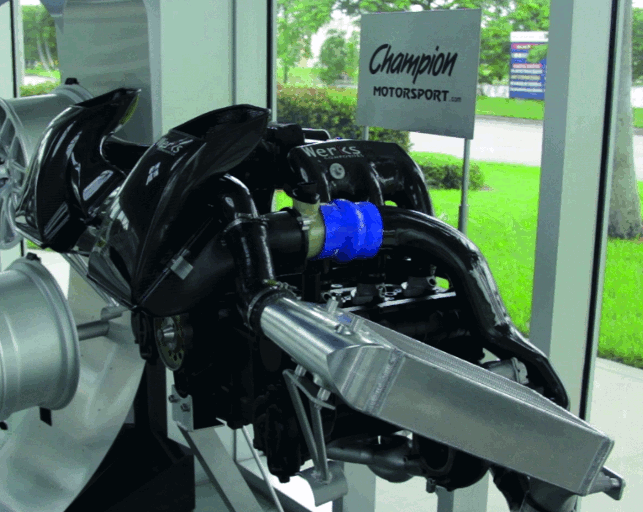
FDM soluble core-enabled components on an engine
An example is Champion’s carbon fibre turbo inlet duct for the Porsche 997 Turbo.
By constructing the duct from carbon fibre, Champion was able to increase the duct’s interior dimensions while keeping the outer diameter at factory specifications. The result is better airflow through the duct, leading to improved engine performance.
The new design is also lighter than the original part, which further enhances performance.
“Producing complex tubular composite components, such as the turbo inlet duct, is very challenging,” says Chris Lyew, lead mechanical engineer, Champion Motorsport.
“The performance of the vehicle depends on a smooth internal surface while the customer expects a beautiful external surface. The part also needs to be very strong to last the life of the vehicle.”
Achieving a smooth interior and exterior surface finish with tubular composite components is almost impossible using conventional tooling.
If the part is moulded in a single piece, the interior core can be trapped inside the tube, unless it is made of a material that can later be washed away like a sacrificial sand core.
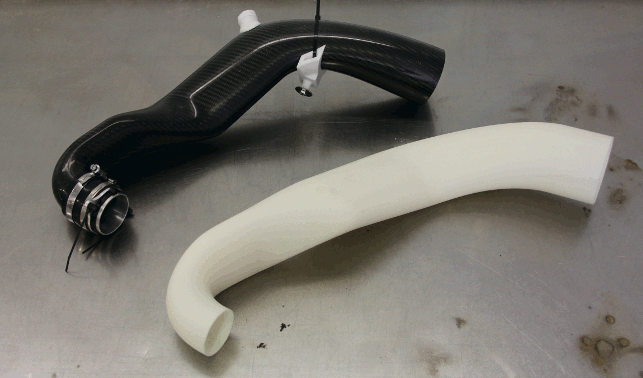
Composite turbo inlet duct (black) made with FDM soluble core (white)
An alternative is to mould the tube in two halves, the disadvantage of this being that the two halves must be bonded together after moulding, resulting in a part not as strong as one with single-piece construction.
In both cases, a good surface finish is only obtained on one side of the part.
Over time, Champion tried different methods for producing inlet ducts but was unable to attain a seam-free part with high quality surface finish on both the outer and inner surfaces.
Already using a Fortus 3D printer to make conceptual and functional FDM prototypes during the design process, the idea struck to try using it to make soluble cores for moulds.
After some tests, they perfected the technique; making its ducts in a single piece by laying up carbon fibre on an FDM printed soluble core.
An excellent external surface finish was achieved by combining the soluble core with an external clamshell mould, while the core can be easily dissolved away in a solution bath after the carbon fibre resin was cured.
This solution for the turbo inlet ducts has also been transferred to a number of other tubes and pipes for the Porsche engine — not only improving the performance of the part, but the production speed by providing a reliable automated process.
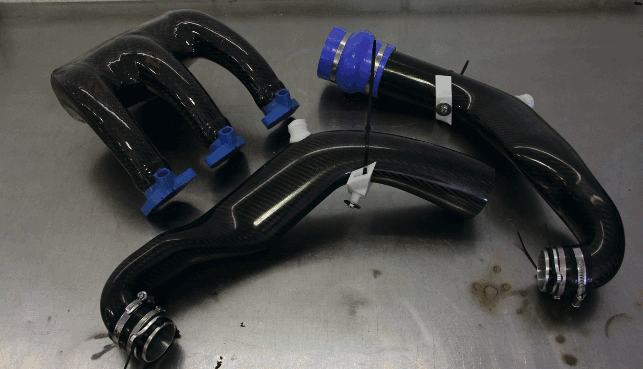
Complex composite ducts made from FDM soluble cores
“We substantially improved the quality of our carbon fibre turbo inlet ducts and other aftermarket parts by making them with FDM soluble cores,” says Lyew. “It’s now possible to mould the inlet duct in a single piece that is much stronger than parts produced by bonding.
“Every FDM soluble core is exactly the same so it’s easy to maintain the internal finish of the duct as well.”
By using 3D printing to produce the soluble cores, Champion has also opened up a new world of design possibilities, knocking away the barriers that have traditionally got in the way of improving its design and manufacturing capabilities.
Stratasys.com
3D printed carbon fibre parts at Champion Motorsports
Default