Using cutting-edge materials, Carnot has designed a new internal combustion engine that burns fuels – both fossil and sustainable – far more efficiently, allowing the most arduous of journeys to exert less impact on the planet
The internal combustion engine has acquired a negative reputation in recent years as a high-emission, unsustainable source of power. However, a lot depends on what fuel is chosen, according to Carnot co-founder Nadiur Rahman. Based in London, UK, Carnot’s focus is producing ultraefficient net-zero power generators capable of operating at 70% efficiency on a variety of fuels, such as green hydrogen, ammonia and sustainable e-fuels.
“We are revolutionising the internal combustion engine to bring it into the twenty-first century, making it cleaner, cheaper and more efficient,” says Rahman, who in addition to acting as COO, also leads the modelling of gas flow simulations.
Engines typically come with cooling systems that stop metallic components from melting. This is a source of waste for the fuel energy that is put in, resulting in efficiency rates of around 30% to 35%.
Carnot’s design instead uses advanced technical ceramics and superalloys capable of operating at higher temperatures, eliminating the need for cooling completely, as well as for lubrication systems.
Because Carnot generators and propulsion units are created to be as lightweight as possible, while offering multi-fuel capability, those purchasing them can be confident that, even if they choose to run them on standard fuels today, they will be ready to switch quickly to the fuels of tomorrow.
Targeting its engines at the hardest-to-abate sectors first, the company has won over £5m of grants to support the development of its technology for use in marine, long-haul road freight and the creation of primary offgrid power sources in rural locations across the world.
“These markets are facing an unprecedented shift and rapidly looking to innovation as a tool to achieve net zero,” explains Rahman.
“We’ve won £1m to turn rice straw biomass into energy in Lombok Island in Indonesia, a £500,000 grant to decarbonise auxiliary power in marine applications, and a £2.3m boost to build an engine demonstrator in conjunction with Carisbrooke Shipping, Brunel University and the Manufacturing Technology Centre.”
Carnot // Scaling up
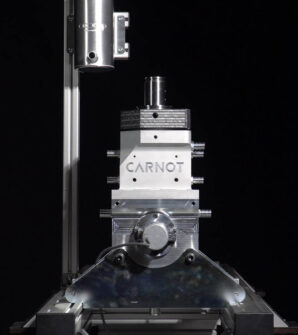
Founded in August 2019 with a very initial outline and sketch of how the proposed technology might look, Carnot has quickly accelerated its design and engineering phases. The team developed the design using PTC Creo, putting the CAD model and its connection to Windchill PLM at the heart of the process, says Rahman.
The company has been supported in the development stage by PTC partner PLM Central, which encouraged the founders to switch to PTC’s Creo cloud-native CAD software to help with design iterations and to scale up.
The founders say this was a pivotal moment in the startup’s development, with the software allowing it to handle large models and up to 250 different parts – a previous painpoint that created additional costs and extended lead times.
“PLM Central gave us the necessary tools to bring our sketches to fruition. Once parts are modelled and engineering drawings are created, we have the parts manufactured followed by an extensive and rigorous testing programme,” he says.
Having started life as just the three co-founders – Rahman, Archie Watts-Farmer and Francis Lempp – Carnot’s design and engineering team has since grown to 12 members, many coming from cutting-edge engineering teams in the aerospace and automotive systems. It includes members with in-depth knowledge of FEA and CFD simulation.
This expertise has enabled Carnot to accelerate development while minimising cost and time, enabling tests to be performed virtually and optimising performance before the company commits to large manufacturing spends.
Physical prototyping is still a key cornerstone of Carnot’s development lifecycle, with much of its key engineering principles rooted in systems engineering and aerospace, while the team looks to combine this approaches with the agility and speed seen in motorsport development.
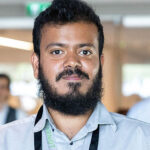
Much of the team works remotely, says Rahman, who in his role as lead designer, found himself losing track of where the team was with changes and iterations. “That’s why Creo has been such a gamechanger and, without doubt, helped us accelerate the development of the Carnot technology by months, if not years,” he says.
“What we didn’t fully realise we were going to get was world-class data management through PTC Windchill. This basically gave us the capability to standardise data from day one and will be increasingly important as we recruit more designers and open collaboration up to suppliers and partners.”
In 2024, Carnot’s design will enter an advanced prototype stage. “The appetite is there,” says Rahman. “Our next challenge is to scale up deployment and start proving our engines in real-world environments.” Once out in the wild, it’s hoped that the internal combustion engine can begin to rehabilitate its chequered history, while continuing to take humankind to the furthest reaches.
This article first appeared in DEVELOP3D Magazine
DEVELOP3D is a publication dedicated to product design + development, from concept to manufacture and the technologies behind it all.
To receive the physical publication or digital issue free, as well as exclusive news and offers, subscribe to DEVELOP3D Magazine here