
Renishaw’s Josh Whitmore presents the Jet Age Museum’s restoration team with the new Hawker Typhoon brackets
The Hawker Typhoon – or “Tiffy” as it was affectionately known to the Royal Air Force (RAF) – was a British single-seater fighter-bomber manufactured almost exclusively by the Gloucestershire Aircraft Company.
Designed and built during the Second World War to match the performance of the formidable German Focke-Wulf Fw 190 at low altitudes, its added ability to act as a ground-attack aircraft cemented the Typhoon’s place as a wartime hero.
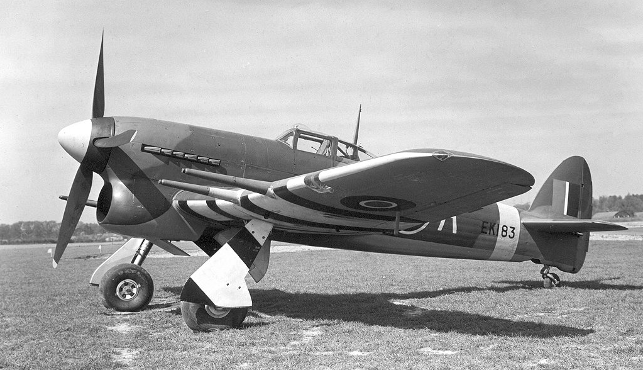
A RAF Typhoon — or ‘Tiffy’ — in its heyday
With only 3,317 Typhoons ever made, few have lasted, with none currently in flying condition, so in 1998, when an almost complete – but exceedingly corroded – cockpit section was found at a scrap yard in Wiltshire, volunteers vowed to restore an aircraft with a rich national and regional importance.
Local to the birthplace of the Typhoon in Gloucester, the Jet Age Museum has taken on the project, pushing forward with the work needed to make it display ready.
Cockpit connection
Key to the structure was a set of brackets, for which the originals were missing, and replacements could not be sourced anywhere.
Such was their scarcity, the museum was relying on a set of authentic 1938 drawings of the part and a borrowed set for a limited timeframe.
When traditional manufacturers failed to accurately reproduce the parts, the team turned to nearby Renishaw.
Eager to help, the global engineering company figured it could produce the unconventional brackets for the cockpit using the latest metal 3D printing technology.
“The Hawker Typhoon is an incredibly important part of Gloucester’s heritage,” explains Trevor Davies, Typhoon sponsor coordinator of the Jet Age Museum. “Our workshop containing the Typhoon cockpit is less than a mile away from where they manufactured the original aircraft in the 1930s.To bring an original Typhoon back to the city would not only be an incredible engineering achievement, but would be like recreating history.
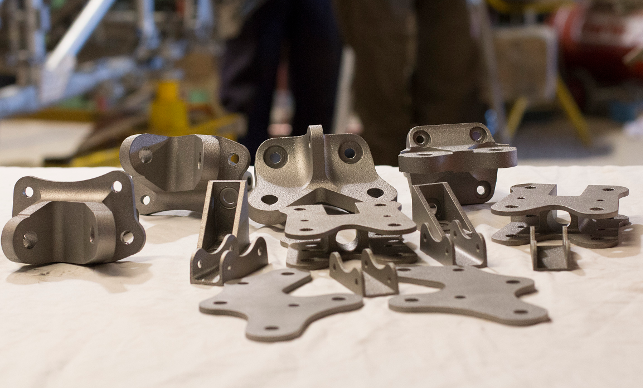
Renishaw 3D printed replacement cockpit brackets from aluminium — the same material as the originals
“The unique shape of the brackets meant that although we had the original drawings, CNC machining companies weren’t confident they could produce an accurate finished part. When we heard about Renishaw’s additive manufacturing capabilities and the design flexibility the technology offers, we got in touch hoping the company could help us.”
The original drawings the Jet Age Museum have for the Typhoon date back to 1938 and all the measurements are in imperial units, while one drawing was completely missing.
“We had to estimate the dimensions from the incomplete set of original drawings – using conventional measurement tools and equipment such as a digital vernier and shadowgraph we were able to obtain most of the missing critical dimensions, while estimating non critical ones, then convert them from metric to imperial,” describes Joshua Whitmore, a development technician at Renishaw.
“The process was more time consuming, but we managed to produce prototypes after about two weeks.”
Modern means
Using the original drawings and additional measurements Renishaw built 3D digital models of the Typhoon brackets using Siemens NX 7.5 to produce digital replicas of the parts.
Once the modelling stage was complete the engineers 3D printed prototype parts in plastic polycarbonate. Once delivered to the Jet Age Museum’s workshop and fitted to the cockpit the team could make sure the fit was correct, and any changes could be swiftly noted and made to the digital model.
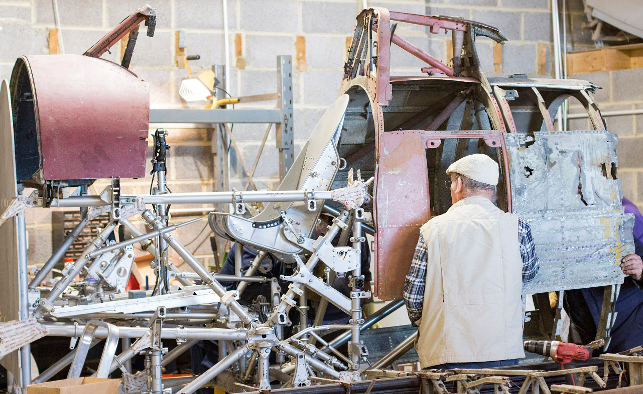
The Typhoon cockpit will form a part of Gloucester’s proud aviation history at the museum
When the engineers confirmed the parts were accurate, Renishaw proceeded to manufacture the final builds in metal.
The Gloucester Aircraft Company originally made Typhoon cockpit brackets in aluminium because of the metal’s physical properties: low weight, high strength and malleability.
Renishaw stuck to the original materials, this time producing the metal brackets from aluminium powder in four separate builds using one of its AM250 additive manufacturing machines.
Once the build was completed and the parts removed, the brackets were surface finished using a mixture of bead blasting and hand finishing techniques.
“We can’t put a price on what Renishaw has done for the Typhoon, the Jet Age Museum and the local community,” beams Davies. “We would not have been able to reproduce these brackets without additive manufacturing technology – the parts are too unconventional, a little bit like the Typhoon itself.
“By combining the old and new, Renishaw has helped keep a project started in 1998 alive and well and has brought one of Britain’s iconic fighter aircraft back home.”
Renishaw helps with a classic Hawker Typhoon restoration project
Default