Today’s consumers are more eco-conscious than ever and are making purchasing decisions based on a product’s sustainable credentials.
As a result, manufacturers, brand owners and retailers are responding by incorporating ethical principles into production processes and using this ‘added value’ to promote their brands and build customer loyalty.
Take Coca Cola for example. This soft drinks giant has seen the commercial advantage in manufacturing its products using recycled materials and, as such, it’s using a minimum of 25 per cent recycled polyethylene (rPET) in all its plastic bottles in Great Britain.
Generally, consumers want to ‘do their bit’ for the environment and tend to trust brands that can help them do this.
This opens up opportunities for product designers and specifiers of materials to drive towards sustainable product design in a move away from the traditional linear model of ‘take, make and dispose’ towards a circular economy.
WRAP, (Waste and Resources Action Programme), which was set up by the government to promote sustainable waste management, describes the circular economy as “an alternative to a traditional linear economy (make, use, dispose) in which we keep resources in use for as long as possible, extract the maximum value from them whilst in use, then recover and regenerate products and materials at the end of each service life.”
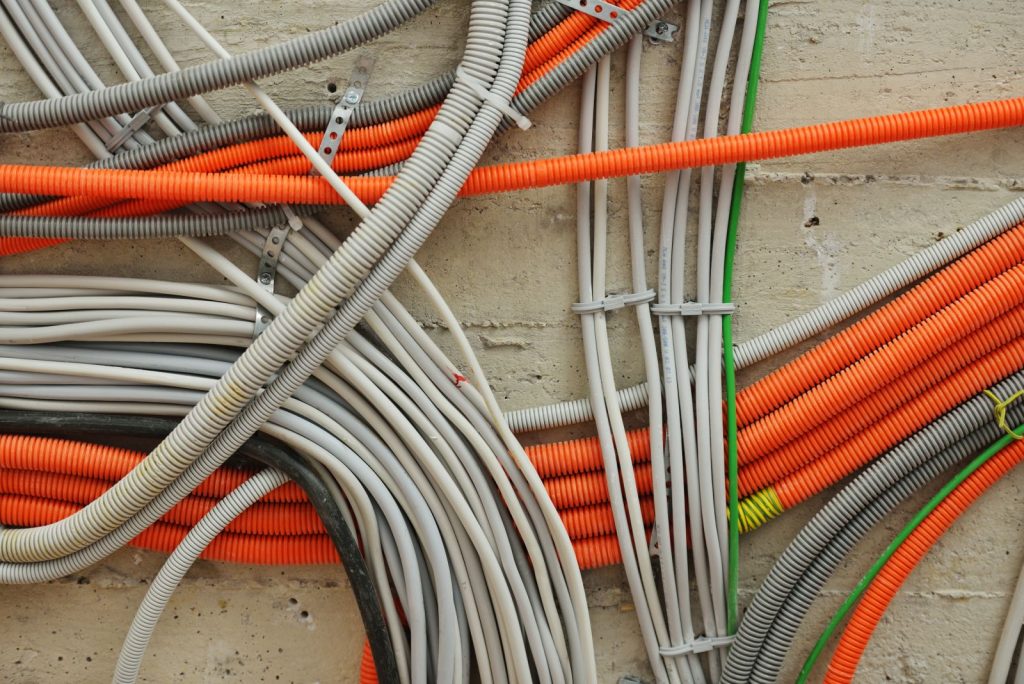
Dwindling virgin materials
Raw material scarcity needs to be considered and recycling existing polymers ensures a sustainable and consistent supply for the future, reducing the reliance on dwindling virgin materials.
It is also a low-carbon choice. Typically recycled polymers have about 50 to 75 per cent of the carbon impact compared to taking oil out of the ground and making a virgin polymer – depending on the virgin polymer types.
The high quality of recycled polymers and their greater availability ensures a reliable and sustainable supply of locally-sourced recovered materials – a viable alternative to virgin materials and the more environmental choice for new plastic goods.
End users that enter into a long-term supply agreement with an integrated recycling business, such as those in the end-of-life vehicle or construction products sectors, can benefit from a reliable local feedstock.
This shorter, lower risk supply chain from UK-based recyclate suppliers makes future production planning easier.
Another advantage of using recycled plastics in durable goods concerns multiple re-use. Design for recyclability is crucial.
If the component design is right, plastics can be recycled many times through a wellstructured end of life re-supply chain. PVC-U windows, pipes and building products are great examples.
Designers need to understand the design principles that enable the efficient release and recovery of materials during the recycling process. Equally, they should recognise the ‘black marks’ that apply to poorly designed products and wrong combinations of materials.
Many everyday products have simple design-forrecycling guides, created by recyclers, which explain the ‘dos and don’ts’ of good design for recyclability.
Recycled plastics can be used in many innovative applications and manufacturers are using them effectively in engineering products across diverse sectors. For example, Manchester-based Axion Polymers is using recycled plastics derived from endof-life vehicles to make new automotive-related products.
The BMW Mini air vent that controls air entry and exit/pressure in the cabin is made from Axpoly r-PP51, a black polypropylene (PP), for instance. The polymer is also used in wider manufacturing industries, including water treatment, horticulture and retail goods.
Axion utilises its extensive in-house capability to recover and refine recycled materials from end-of-life vehicle shredder residue, providing a consistent product from a guaranteed feedstock supply.
“Creating new manufactured products using materials resources that are ‘mined’ from closed-loop recycling routes provides a novel and environmentally responsible approach for vehicle producers that is both sustainable in the long term and lower cost,” says Axion Polymers director Keith Freegard.
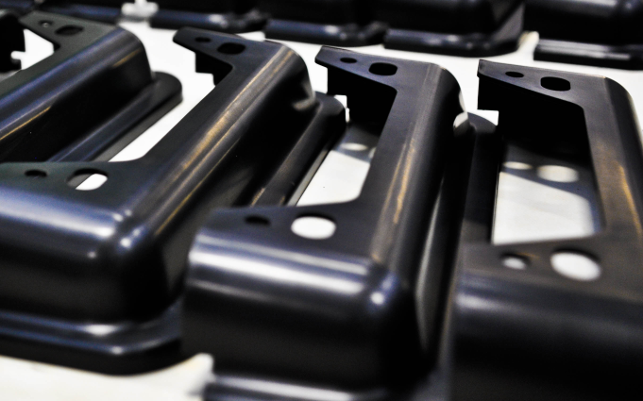
Versatile materials
Another example is VEKA Recycling, which is processing post-industrial and postconsumer PVC window frame material to a high standard of purity at its Kent site.
The finished products, 100 per cent recycled PVC pellet and micronised (pulver), are suitable for a wide range of manufacturing and extruded plastic goods, from building, roofline and cabling/ducting products to new windows.
PVC is a versatile material that can be readily recycled many times with no loss of performance, making it an ideal choice for use in building products.
“Recycled PVC offers clear advantages of reliable consistent supply and, of course, improves the environmental credentials of manufacturers’ products.
In releasing the reliance on virgin polymers, we are giving longer life to plastic,” says VEKA Recycling commercial director Simon Scholes.
For those keen to start sourcing recycled materials, a good place to begin is with the many plastics recycling companies listed in the British Plastics Federation’s members directory.