Magic touch
German company Trumpf recently unveiled its latest bending machine – the TruBend Series 5000.
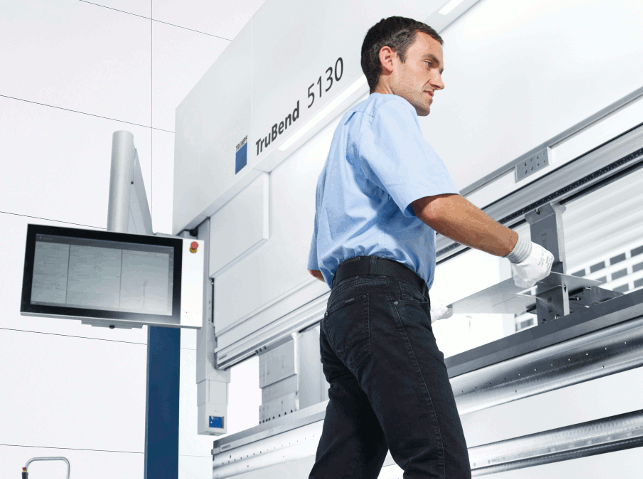
The new Trumpf TruBend Series 5000
The clue’s in the name as to what this machine tool does – essentially fabricate and bend metal parts. Unlike punching or laser cutting, bending involves 3D manipulation of the part.
In this latest incarnation of its Trubend Series, the designers, which are based at the company’s location in Pasching, Austria, where all of its press brakes, automation solutions and press brake tools are produced, were keen to make the machine more productive and user-friendly.
This all purpose machine is equipped with a new On-Demand Servo Drive that features four-cylinder drive technology. The benefits, according to the design team, are that it’s extremely quiet in operation, delivers more productivity than a conventional drive and is eco-friendly as it consumes energy only during the bending process itself.
In the design of this new version, the designers also were keen to put the needs of the user first and the outcome is a range of ergonomic components that will assist in the machine’s operation. The most notable of these is the MagicShoe, a work shoe fitted with smart sensors. This means that the operator can move around and initiate the stroke wherever they are standing at the machine.
Dragging and relocating foot pedals is now a thing of the past with the space in front of the machine remaining clear.
Another new feature is the Touchpoint Trubend control with a user interface that is simple and intuitive to use, and has been optimised by the designers for everyday work processes.
The machine can be operated without a mouse, using a 21.5 inch monitor that is equipped with a multi-touch function that can be used with work gloves.
Trumpf obviously expects big things from this machine as it recently invested 30 million euros in the enlargement of the Austrian site, which includes a new development centre.
At the official inauguration of the site in October 2014, Armin Rau, managing director of Trumpf Maschinen Austria, said, “With the extension we react to the increasing challenges on the world market and the growing product variety in the field of bending at the site in Austria.
“At the same time we want to ensure an ideal production environment for our new machines such as the TruBend Series 5000 and Series 3000.”
Up to speed
Haas is a big player in the machine tool world boasting that it sells a machine every 8 minutes of every working day.
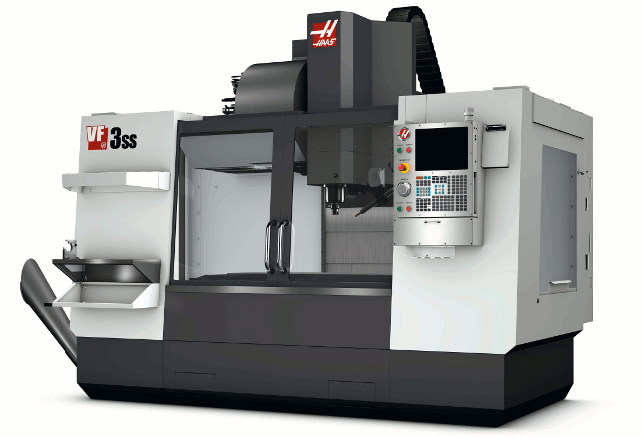
The new Haas VF-3SS vertical machining centre
So, it’s not surprising that its range is somewhat large. At its US headquarters in California the design and engineering team create a full range of metal-cutting machine tools including CNC machining centres, lathes and rotary tables.
The team’s latest offering is the Haas VF-3SS Super Speed Vertical Machining Centre (VMC). The clue’s in the name as to why this CNC VMC will be an asset to the machine shop: it’s super speedy.
Classed as one of its medium-sized verticals, the VF-3SS is based on the VF-3 platform, which has a rather compact 1,016 x 508 x 635 mm envelope.
The machine includes a newly designed 24+1 side-mount tool changer that has been constructed using lighter materials and a high performance servo motor for below 1.6 sec tool-to-tool changes.
Another new feature is that its directdrive spindle system couples the drive directly to the spindle rather than using belts. This innovation means less vibration, less heat and less noise than other drive systems.
Two in one
Global machine tool manufacturer DMG MORI has launched a machine on the market that is currently unique – the Lasertec 65 3D.
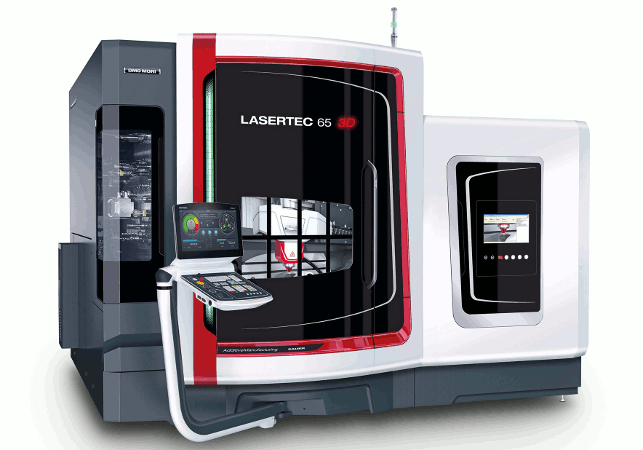
The LASERTEC 65 3D
This machine is not only a fully-fledged 5-axis milling machine but also offers laser disposition welding by means of a powder nozzle.
It is based on a DMU 65 monoBLOCK machine and has been developed by Sauer Lasertec in Pfronten, Germany, in collaboration with DMG MORI USA.
The team’s thinking behind this hybrid offering, which combines two processes – metal deposition and metal removal – is that in times of ever shorter product life cycles and increasingly more complex components, generative manufacturing processes can help companies to produce new and innovative products more quickly.
“Thanks to the fully automatic changeover between milling and laser operation, the Lasertec 65 3D is suitable for the complete machining of complex components with undercuts as well as for repair work and the application of partial or complete coatings for mould making and mechanical engineering,” says Friedemann Lell, of Sauer Lasertec.
A look at the latest machine tool developments
Default