Powered wheelchairs give their users considerable freedom in their daily lives, but what about those who want to adventure further and live with even fewer limitations? Stephen Holmes speaks to the team at Freedom One Life about how its latest design opens up new horizons for users
A powered wheelchair is a lifeline, connecting its user to a more empowered existence – but that’s not to say that current designs don’t come with certain limitations.
When Alex Papanikolaou became frustrated with his own powered wheelchair, the various alternatives he tried either restricted his activities due to their limited ranges, or worse still, were prone to breakdowns. In other words, he had to plan his day around battery life. The fear of getting stranded somewhere remote made long trips a concern. The prospect of being able to escape paved surfaces for the thrill of off-road adventures was nothing but a distant dream.
After speaking with other wheelchair users, Papanikolaou began to question why wheelchairs couldn’t be designed differently, leading him to set up Freedom One Life in 2012.
His initial vision grew into a fully-fledged design and engineering team, based in Glasgow and focused on tackling the four main issues around powered wheelchairs: battery performance, mechanical reliability, comfort and convenience.
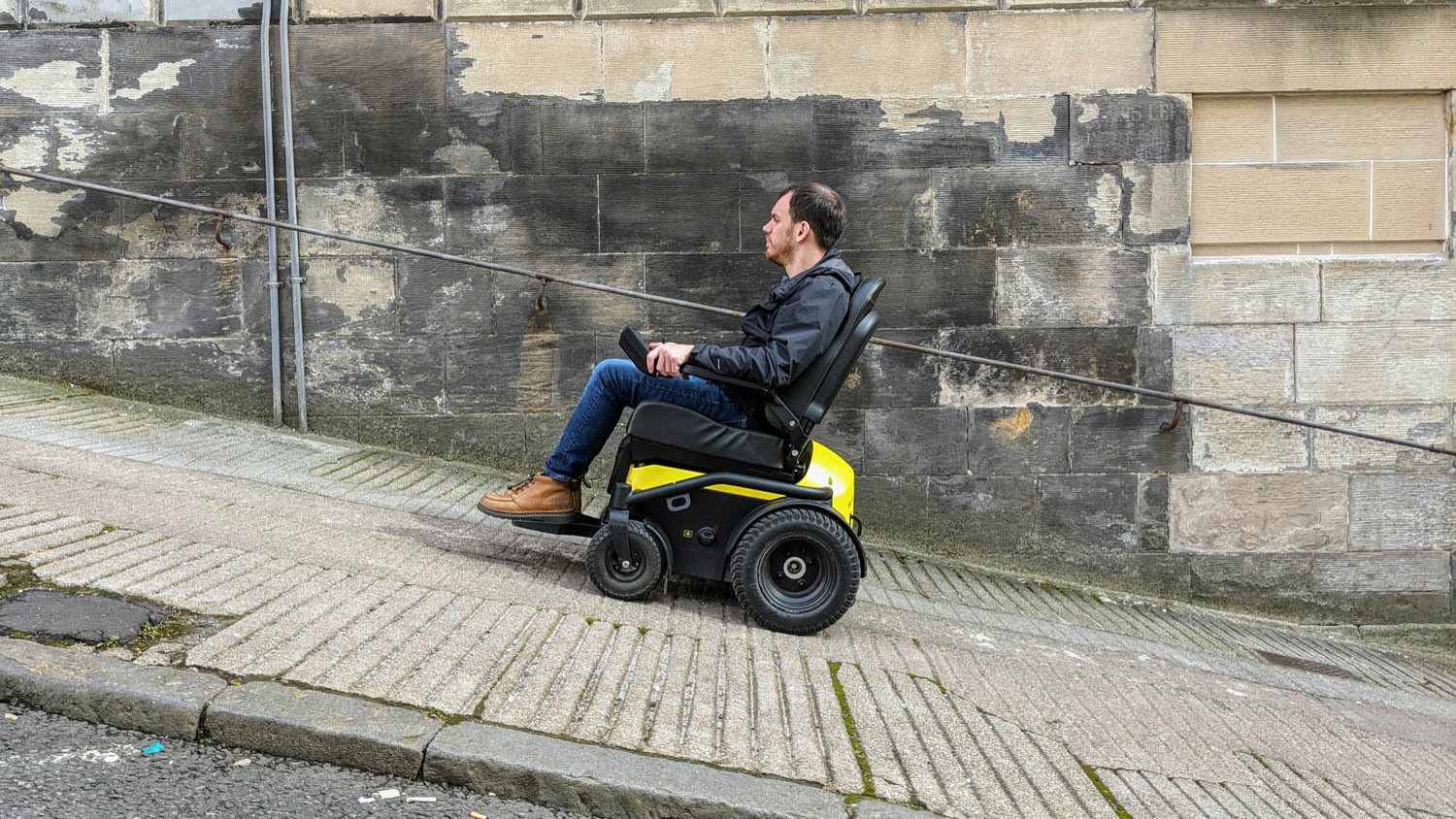
Powering up
Papanikolaou‘s concept for the perfect chair was already well underway when Scott Savage joined the company as technical director in 2018. His job was to help in the push to get the product to market.
“The design work began with several detailed discussions with Alex about the prototypes that had been developed up to that point, as well as his lived experience as a powered wheelchair user,” Savage explains.
“It was important to find out what had worked, and what hadn’t. Learning from each prototype is an important part of product development. These learnings allowed me to build the design brief and specification for what would become the Series 5.”
A powered wheelchair comprises a large number of components, so breaking the large design task down into smaller sub-projects was essential to ensure realistic timelines could be set and met.
The design work began with understanding the chair’s pre-selected components: its motors, wheels and charger. “From here, some detailed space envelope exercises were conducted, to work out how best to configure these parts within chassis concepts, while maintaining the required width and length of the final chair,” says Savage. Solidworks was used to create the detailed 3D CAD models for assessment, he adds.
“Once we had this nailed, it was easier to tackle each sub-project using the same process – starting with sketches, selecting the strongest concepts, then moving on to Solidworks for detailed design.”
Savage says the development of the chassis was the most challenging part of the design. “It was the first part and the most important part. While designing the chassis, my mind had to be thinking several sub-projects ahead, to provide space, anchor points and strength to various locations and ensure that the end project assembled and performed as expected.”
With a huge number of factors needing to be considered for every component and its role in the complex assembly, remaining mindful of all assembly interactions and user requirements was a tricky task. A team of three designers built the Series 5 chair to accommodate the biggest battery manageable. Savage says it is capable of delivering three times the range of its nearest competitor, with over 40km of real-world use on a single charge.
To put this into action, high-torque motors and lowpressure tyres give the user confidence to navigate tight spaces, comfortably cross uneven terrain and climb steep hills.
The mechanical design of the Series 5 ensures that all electrical components are concealed behind car-like body panels. These protect them from the weather and from being snagged on objects while moving.
Real-life challenges
In the early stages of prototyping, 3D-printed parts proved useful. Prototypes were produced for assessing component placement as well as general aesthetics, before the team turned to 5-axis CNC machining and vacuum casting to produce short runs for real-world testing. This enabled them to iron out any problems before committing to production tooling.
Reliability has since been proven by over 20,000km of real-world testing. “Having a user as the founder of the business allows us to test all new features to their extremes in real-world situations,” says Savage. “We found problems along the way and we fixed them so that other users don’t have those experiences.”
The Series 5 is fitted with elements that reflect this evolution, from the single cable on-board charger that takes away range anxiety, to drive settings that can be changed by the user without the need for a visit from an engineer. A rain-mode screen means that users no longer have to worry about controlling the chair and its settings in bad weather, making it usable come rain or shine.
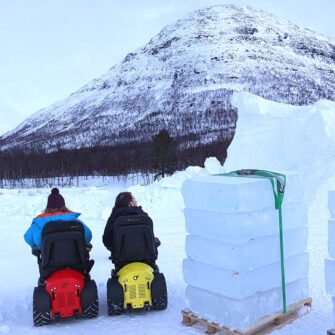
The electric seat can be raised in height by 300mm to help wheelchair users access places that might otherwise be hard to reach and to make face-to-face conversation possible. With 50 degrees of tilt, the occupant can easily find a comfortable angle.
All components had to be strong and robust, of course — not just for day-to-day use, but also so that the wheelchair qualifies for use on board a moving vehicle. For this, the final design for the Series 5 had to undergo crash tests, being strapped to a sled using its four-point tie-down system, then accelerated up to 30km/hour, before subjected to an instant stop.
“The huge forces involved in this testing made it highrisk, and simulation played a vital role in mitigating that risk,” says Savage, explaining that the team relied on the simulation software included in its Solidworks package from reseller TMS to undertake the bulk of its FEA analysis.
“We were able to ensure that the tie-down points and the chassis were able to absorb all of the forces and to make any design changes before undertaking the costly and somewhat scary crash test.”
Thanks to these FEA simulations, the Series 5 passed first time.
After years of development, refinement and continuous improvement, the Series 5 sees Freedom One Life ready to begin fulfilling orders around the world, enabling its customers to follow whatever path they choose.