Uddeholm are the Swedish experts in all things tool steel, so who better to investigate new methods of 3D printing cold steel moulding tools. Stephen Holmes finds out how GE’s Arcam additive manufacturing process is producing interesting results
With metal additive manufacturing rising fast as a technology for plastic injection moulding tools, many companies using the technology to exploit opportunities to save cost and increase productivity through shorter cycle times and challenging conventional ways approaching conformal cooling.
These hot work applications tools, including dies for high pressure die casting, are growing, but the cold work tooling sector, is a lesser explored sector.
With the increasing demands for lightweight products, more and more advanced high strength steel sheets are being used. This places a higher demands on the tool steel used to punch, form and trim the sheet metal parts and also on the quality of the parts, so there are no burrs or stress concentrations that can risk the use and life of the produced part.
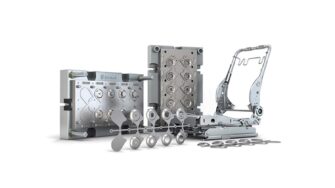
Swedish high alloyed tool steel producer Uddeholms AB has been investigating the uses from its headquarters in the town of Hagfors.
Uddeholms explains that the most important property of a cold work tool steel is the good wear resistance, a trait usually achieved by a significant amount of carbides within a hardened microstructure.
Forming carbides is driven by specific alloying elements and controlled by the carbon content. Therefore, cold work tool steel grades are highly alloyed steel grades and have a high carbon content.
This causes problems when trying to produce tools using 3D printing – the high alloying content is highly susceptible to cracking during rapid solidification, as in welding.
Cold work tool steels are non-weldable materials – which rules out powder-bed AM technologies that are based on welding principles (a high energy beam for melting).
In addition, segregation effects during solidification and subsequent heat treatments can lead to inhomogeneous distribution of carbides, which can lead to poorer wear properties.
With lasers ruled out, Uddeholms decided to investigate GE Additive Arcam’s electron beam melting (EBM) process, which while still hot, the electron beam can be used both for heating (if it is defocused) and for melting (focused). This allows the possibility to control and maintain temperatures during processing to prevent crack formation.
In addition, EBM is a vacuum process and offers protection of the material and the powder against contamination. This precision means more control, allowing the tight chemistry of the desired alloy to be kept within its specification.
High solidification rates during melting lead to a fine and homogenous microstructure which is necessary for both, carbide formation and distribution.
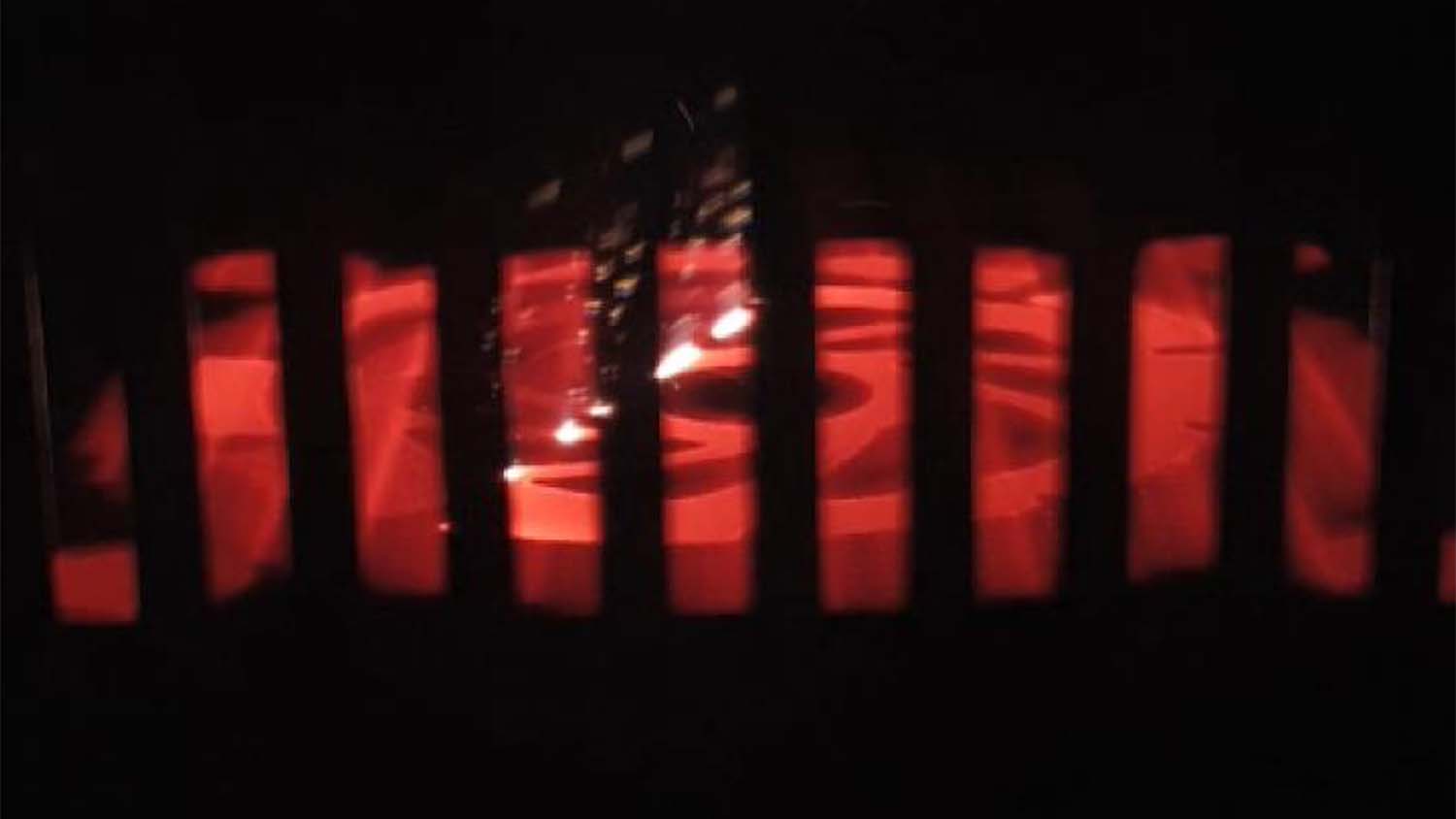
Hard metal
To unlock the potential of EBM for cold work tool steels, Uddeholm and GE Additive have developed the Uddeholm Vanadis 4 Extra powder material for EBM.
Uddeholm Vanadis 4 Extra Superclean is chromium-molybdenum-vanadium alloyed steel, originally developed as a PM-grade, has been modified and adapted to the EBM process.
The material properties of the PM version were kept and led to excellent wear resistance and good toughness, superior to traditional cold work tool steel such as D2.
By using the right conditions during EBM processing and subsequent heat treatments Uddeholm has found it is possible to achieve a hardened microstructure with fine dispersed vanadium carbides, which gives the necessary excellent wear properties combined with a good toughness.
The hardness of Uddeholm Vanadis 4 Extra reaches 64 HRC, with a compressive strength of 2700 MPa, and a toughness of 20J.
Uddeholm states that the EBM processed material has been tested in both punching and embossing operations where both the wear properties of the tool and the quality of the produced parts are very similar to the Vanadis 4 Extra PM-grade.
Solid benefits
The benefits of 3D Printing cold tool steel are different to those of hot tools – a key feature of which are the complex designs and inbuilt cooling channels.
Some of the cold tools have designs that require extensive machining, where up to 75 per cent of the material will be removed. For these parts using AM can save both time, cost and energy.
Another benefit is the reduced volume of material needed – the materials from steel mills to produce cold work tools require the availability of the right material grade, in the right size, at the right time, making procurement a tricky business.
At such times, it could mean additive manufacturing is a good complementary method to the traditional tool making. Instead of spending time chasing the right raw material, tying up capital and damaging cash flow, these tools can be printed with same properties as for the traditional tools.