A spin-off from GM-Fiat’s powertrain venture, Punch Torino is a leading R&D engineering facility for internal combustion engines and propulsion systems. Now part of Belgium’s Punch Group, the company continues to support GM and a growing roster of manufacturers and startups in diverse technology projects that include gasoline, diesel and hydrogen engines.
Punch Torino builds a variety of prototype engines for its clients and develops and tests new components for existing engine designs. During the build process, engineers must install a timing chain that connects the engine’s crankshaft to a pair of camshafts. When they rotate, lobes along their length open and close the valves of each cylinder to let fuel and air into them at the right time.
As the timing chain sprocket is tightened, the camshafts must be kept completely stationary in a defined position to guarantee the perfect synchronization of the timing system when the engine is running. If the camshafts aren’t locked in place, the valves may open and close at the wrong times, damaging or destroying the engine.
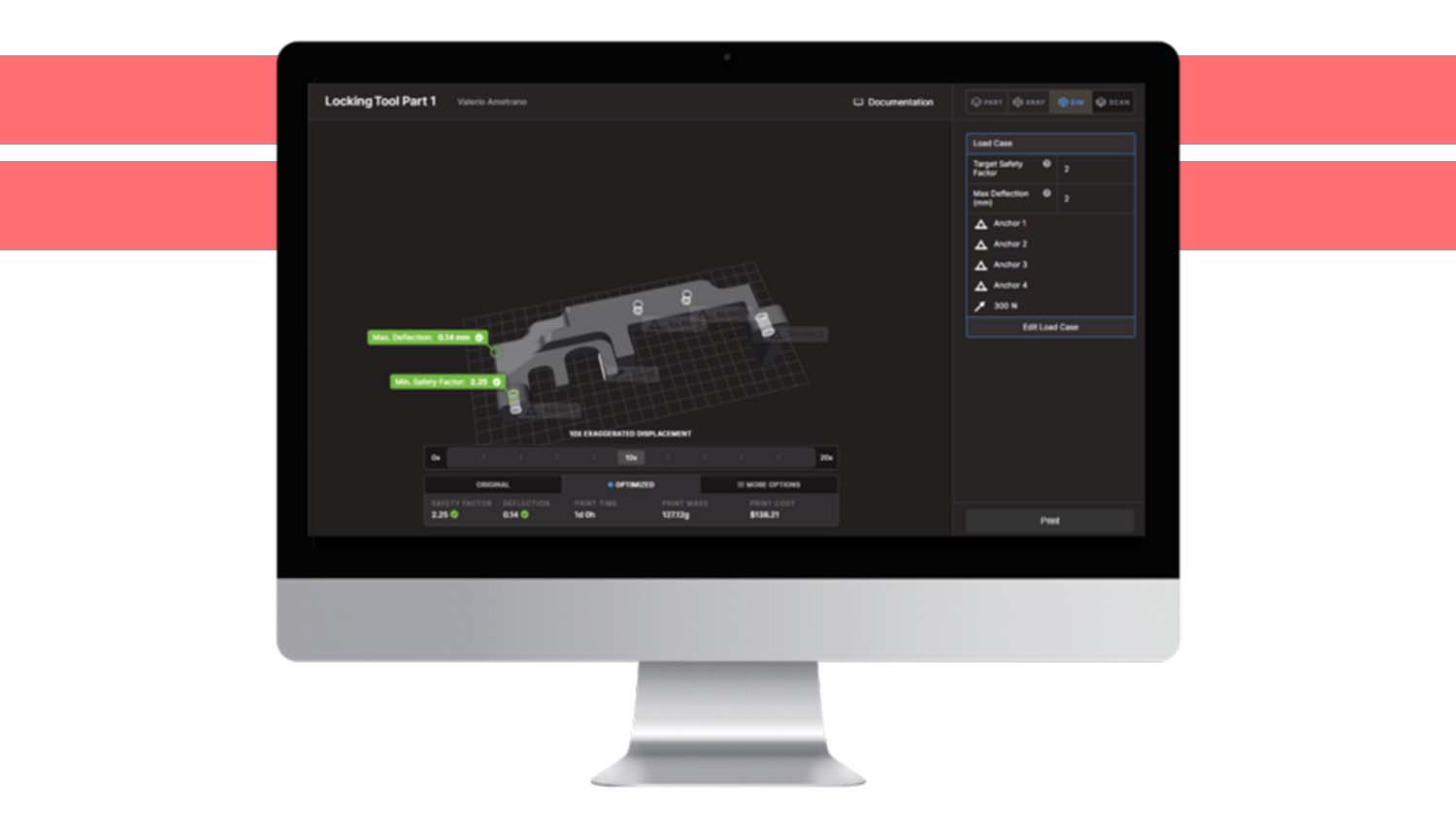
To prevent the camshafts from moving, Punch Torino’s engineers have designed fork-like camshaft locking tools, built using Markforged Onyx filament with fibre reinforcement. The camshaft locking tools are currently built using a Markforged X7 using Onyx with carbon fibre reinforcement.
During the tightening process, the tools must withstand torque up to 120-newton meters and must not allow any degrees of rotation. Valerio Ametrano, Punch senior pre-production engineer, estimates that each one takes approximately 18 hours to print.
If a locking tool breaks during this critical tightening process, the torque on the camshaft will cause it to rotate out of position. The team would then need to loosen or remove the timing chain, re-secure the camshafts and begin the tightening process again.
While 3D printing has sped up the original process, waiting for a new locking tool to be 3D printed could delay the team by a day or more, especially if it caused them to miss a build window for a new engine.
During the engine design process, engineers often make frequent, small design changes to engine components, especially during the early stages of engine development. Each time, the team must tweak the design of the camshaft locking tools and print new ones. Often, the engineering team may test multiple camshaft designs at the same time. Each one requires a slightly different tool design.
In the past, the process of designing camshaft locking tools required a lot of trial-and-error work – there wasn’t an accurate way to predict if a tool would be stiff enough and strong enough to withstand the torque loads placed on them. Engineers had no way of knowing if a design change to the locking tool could compromise its structural integrity, while FEA analysis isn’t designed for 3D-printed parts, the team had to make many assumptions and approximations to design jigs that met all of their requirements.
The team at Punch Torino says it was able conquer this through its use of Simulation from Markforged. Prior to using it, a new camshaft configuration could require printing and testing up to 8 jig designs to get the configuration right, Ametrano recalls.
For example, a change in geometry or dimensions (lobe, length, diameter, etc.) of the camshaft may have required a slightly different fork shape to hold it in place. Yet, the revised locking tool design didn’t quite conform to the shape of the shaft and allowed for too much camshaft rotation. This could result in printing multiple iterations of tools until they landed on a configuration that worked.
After they started to use Simulation for Markforged, they were able to reduce the average number of locking tool design iterations from 8 to three, at least at first. According to Ametrano, when the team was first learning to use the new simulation tool, they went through some trial and error to correctly characterise the boundary conditions, force modulus and deformation the locking tool was exposed to. Now that they have this data dialed in, they can usually simulate and print a typical locking tool in a single iteration, he points out.
He estimates that Simulation for Markforged not only saves the team an average of 18 hours per jig but also the engineering time required to modify the part designs; this is now managed within the software. In addition, it frees up a significant amount of printer time that was previously dedicated to producing multiple iterations of camshaft locking tools.
Ametrano first validates the part in Simulation and then uses the software to optimise the print settings and the placement of carbon fibre. He often experiments with several configurations of manually-placed fiber, comparing the estimated deflection and safety factor of each one.
Using Simulation, the designers can see in a matter of minutes how different fibre layouts impact the part performance, helping identify the best-performing configuration for printing quickly and easily.
During the early stages of engine development, engineers sometimes make frequent changes to camshaft designs. If the changes are minor, the team modifies the design of the camshaft locking tool, while keeping the previous use casein Simulation for Markforged to verify that it will still have the required strength. If design engineers make major changes to the camshaft designs, the team must redesign the locking tool and re-do the simulation based on the new design.
Engine builds require the PUNCH Torino team to gather a large number of components and tools in one place so they can assemble up to 10 of them within a limited time window. Simulation from Markforged helps ensure that the camshaft locking tools are correctly configured and ready to use when they’re needed. A poorly configured tool can break under pressure, delaying an engine build for a day or more, Ametrano emphasises.
In addition to designing and prototyping engines for different worldwide OEM automakers, Punch Torino now sells its 3D printing expertise to several industrial and technology clients. A logical next step is to use Simulation from Markforged to help streamline the design optimisation and build process for their parts, timing things just right for the R&D experts.