Stewart-Haas Racing is a hub where smart mechanics, cutting-edge aerodynamics and ingenious engineering all come together. Stephen Holmes ventures to the heartland of NASCAR development to find out what it takes to cross the finish line first
The huge main hall at Stewart- Haas Racing is a hive of energy. Mechanics and engineers swarm around four NASCAR Cup cars in the final stages of assembly, as the clock ticks down to the next race.
Heads are buried deep in engine bays, trolleys rattle along filled with parts, and vital measurements are taken, ready for the cars to be loaded into specially built haulers and driven to the racetrack for the fast-approaching weekend. This team has experienced the kind of success you’d expect from one co-owned by three-time NASCAR Cup Series champion Tony Stewart and Gene Haas, an automotive obsessive and founder of Haas Automation, one of the world’s largest CNC machine tool builders.
Starting out with two Cup cars in 2009, Stewart-Haas Racing has now won over 70 races across the Cup and Xfinity series. Today, it has four cars in the Cup series, two in Xfinity. All of the drivers – each with their own car, engineers, mechanics and race staff – share the facility in Kannapolis, North Carolina, elbow-to-elbow with their race day rivals. Located a short sprint north of the Charlotte Motor Speedway track, the area is home to many NASCAR teams and the beating heart of the sport.
The cavernous main garage of Stewart-Haas Racing is flanked by numerous workshops and storage facilities, with an annexe for the shorter and lighter Xfinity cars, a pit crew training area and storerooms filled with row after row of components and spares.
Giant pennants dangle above the main atrium where the Cup cars are fettled and fixed. Acknowledgements of two Cup titles, two Xfinity championships and victories that include globally known races such as the Daytona 500 and Brickyard 400 hang from the rafters alongside many others.
“We like to hang banners here in our shop,” says Reneau Van Landingham, production manager at Stewart-Haas Racing, pointing to the ceiling. “We are literally measured by the performance that we have throughout the race. That’s why we’re all here. We’ve got an engineering group and the fabricators that are all working together towards that end.”
While the entrance lobby and gift shop that overlook the main garage are open to the public, NASCAR is as secretive as any other motorsport. At Stewart-Haas Racing, high-level CFD simulation and engineering work happens very much behind the scenes, in an upstairs room overlooking the garage floor. Mirrored glass, reflecting the winners’ banners hung opposite, keeps even the keenest eyes from prying.
Measure up
Car specifications are governed by NASCAR’s rulebook, yet each track that the drivers face is unique, varying in length, banking angles and climate. That means that every car must be designed and built specifically to tackle it.
We don’t just build one car and race it all season. Every weekend, there’s a new track and new cars to race on that track Reneau Van Landingham, Stewart-Haas Racing
“We don’t just build one car and race it all season. Every weekend, there’s a new track and new cars for that track. And when the cars come back here after the race, they’re completely torn down and rebuilt for the next race,” says Van Landingham.
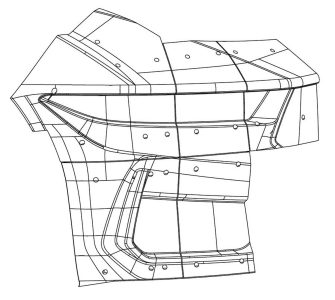
With races running from February through to early November, the Xfinity Series races take place 33 times a year, with five or six weekends off. The Cup Series boasts 40 races in a season, including a 30-race stretch of racing every weekend. By way of comparison, Formula 1 teams typically race bi-weekly, 24 times a year.
Stewart-Haas engineers responsible for preparing the cars also head out to the tracks, so any race delays due to adverse weather severely impact the cars’ development schedule.
Aerodynamics is a big component of the performance equation, with body panels assembled precisely and fixed to cars to enable the best possible performance. Short tracks have different specifications compared to longer tracks, and a Speedway track will be different to a road course, so every millimetre of the car’s surface is optimised to suit.
All the body panels used in NASCAR are made from carbon fibre-reinforced plastic that provides more race durability and cost savings than the stamped steel of old, with Stewart-Haas working with a specialist fabricator to turn around parts in time for each race.
Each panel, its placement and how it’s mounted on the car has to comply with a NASCAR-specified range, giving teams room to play with that amounts to just 300/1000ths of an inch – or 7.62mm.
Cars are scanned throughout the build process, with portable Hexagon Romer Arms being used to capture individual part data, and then in the team’s optical scanning station, using a replica of NASCAR’s on-track Hawkeye system, meaning that every car should make it to the starters flag without a snag.
Next time faster
In preparation for the 2024 season, Stewart-Haas Racing’s aerodynamic engineering team played a critical part in determining the best performance design for the Ford Mustang car that all Ford-badged teams race.
The Ford Mustang Dark Horse project needed not only to reflect the key sponsor’s latest roadgoing vehicle incarnation, but also to be able to handle the requirements of NASCAR racing and meet the race authority’s guidelines.
For submission projects, the Stewart-Haas Racing team works alongside Ford’s industrial designers and the styling group to get a preview of what the next year’s Ford Mustang will look like. “We usually say, ‘Wow, that looks really great! But it’s not going to perform the way we need it to perform on the track at 185 miles per hour!’” laughs Van Landingham.
It’s down to the designers and engineers at Stewart- Haas Racing to encapsulate the spirit of the new Mustang, retaining the many distinctive lines and angles of its styling, while adapting it for the aerodynamic demands of stock car racing.
The whole process can last for months, with back-andforth discussions, designing and testing prototype parts both in CFD and in the wind tunnel that can improve downforce on the car.
What’s vital is that the end result of that process still retains and reflects the Mustang’s unique style. As Van Landingham puts it, Ford wants its cars “to win in the races on Sunday, and for people to go and buy those Mustangs on Monday.”
With that in mind, once CFD analysis has identified the most favourable designs and configurations, engineers then convert the CFD surface meshes into solid CAD models, before dividing designs into large tiles that can be 3D printed using a 3D Systems ProX 800 SLA 3D printer.
Once printed and assembled, the tiles are designed to be attached to the sub-frame chassis of a full-scale car before being tested in Haas Automation’s Windshear wind tunnel, based at nearby Concord airport.
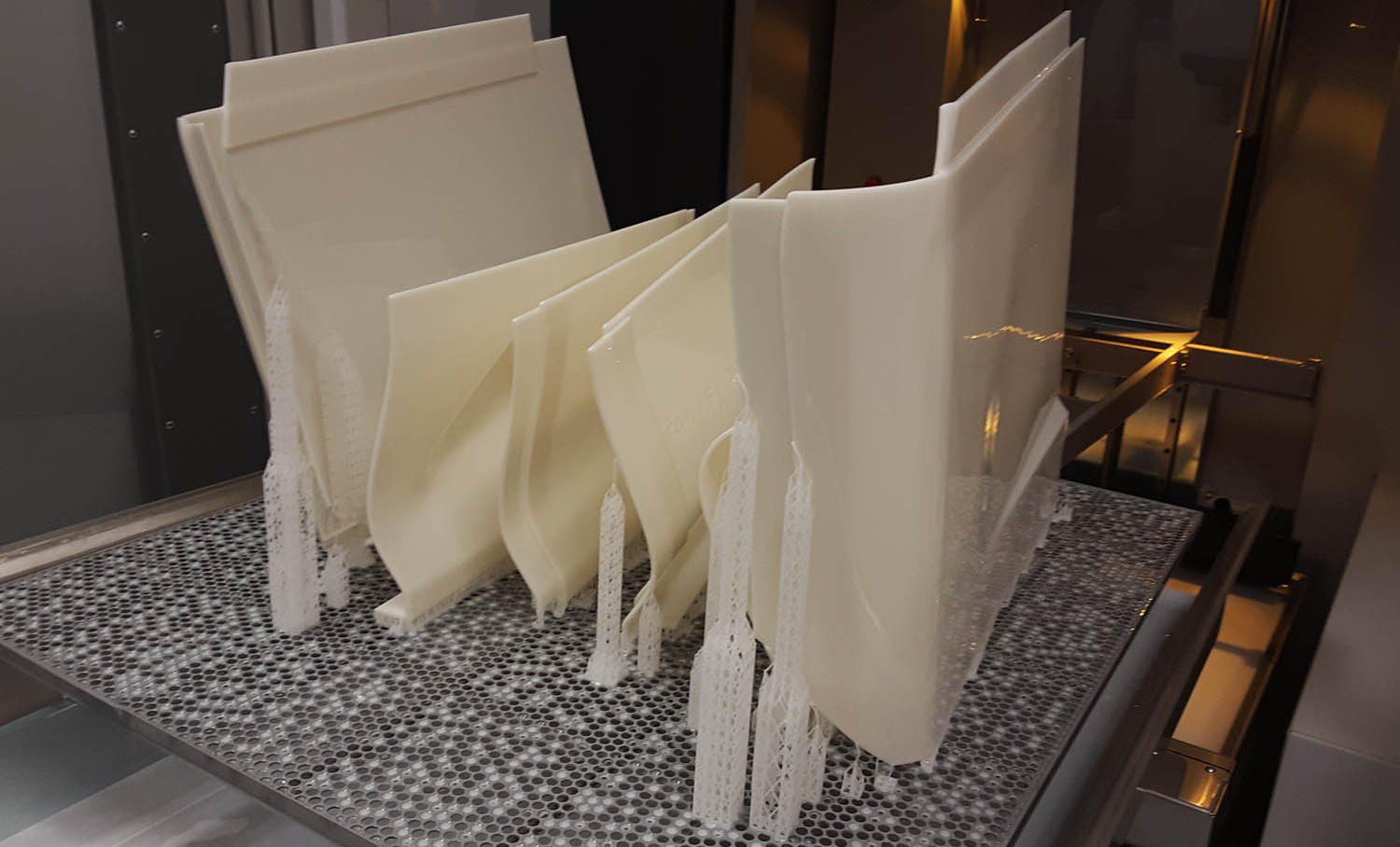
Sprint to the finish line
Travis Jack is a mechanical engineer from the aerodynamics department who runs the team’s 3D printing lab. Overseeing a range of 3D printing technologies, including the ProX 800 SLA and a Figure 4 Standalone unit also from 3D Systems, he has FDM machines and more at his disposal.
To develop the Dark Horse Mustang parts, Jack used 3D Systems’ 3D Sprint software to orientate the CAD models to be printed, optimising print speed, quality and quantity per build platform.
Working with Accura 25 resin allows for fast and accurate parts, he says, while the ProX 800 build volume allows for the largest parts possible to be produced. “It’s just a great tool for doing this type of thing,” adds Van Landingham standing next to the large 3D Systems ProX 800 machine.
“Then we know that the shape of a headlight is a good one, or we didn’t really like it and we want to change the radius to improve the performance. And we’ll do the whole process again.”
For this project alone, more than 2,000 parts were produced over a seven-month timeframe, with the help of Ford’s engineers in Dearborn, Michigan.
Van Landingham explains that the team has become so reliant on 3D printing that the numbers continue to stack up. “It’s no longer hundreds of parts, it’s thousands of parts,” he says. “It’s a well-ingrained tool that we use now – it’s no longer novel. It’s a critical part of our development process and all the engineers leverage it. We get uneasy if a weekend’s coming up and there’s nothing to print!”
First cut
Even for a team with strong links to its founder’s CNC machining empire, and all the metal cutting technologies you’d expect as a result, 3D printing polymers is still a “huge” part of the workflow, according to Joe Custer, Stewart-Haas Racing’s team president.
Historically, he says, engineers would dream up a part for a race car, put all their effort into it, machine the first article and then find there was a problem. As with most engineering tasks, producing a perfect part takes multiple iterations, and 3D printing a prototype early on is what helps the team achieve that perfect part faster.
“What’s happened now is that it’s almost instantaneous from designers,” Custer says of 3D printing a part. With rapid prototyping, a good idea travels further than just the design office. “Crew chiefs working with us, they understand now. The guys at the track have learned that this is unbelievable. If they truly work with our resources, they can get parts on their car way ahead of some of our competitors. The whole previous structure is out the window.”
Van Landingham adds: “Rapid prototyping means we can print the parts really quick, check the size and shape, and then we can go to machine the parts, because that generally does take longer and usually it’s more expensive, depending on the material.”
In effect, he adds, this means that, “within a one to two-week timeframe, we’re doing design, engineering, [wind tunnel] testing, fabrication, production, and it goes onto the car on the track.”
It’s a “race between the races”, he continues, with engineering groups from each team competing against each other to get parts on their respective cars faster.
This urgency comes further into perspective when you speak to drivers. “We only get 20 minutes when we show up and you really can’t change a ton [of stuff],” says Cole Custer, son of Joe, driver of Car 00 and reigning champion of the NASCAR Xfinity Series.
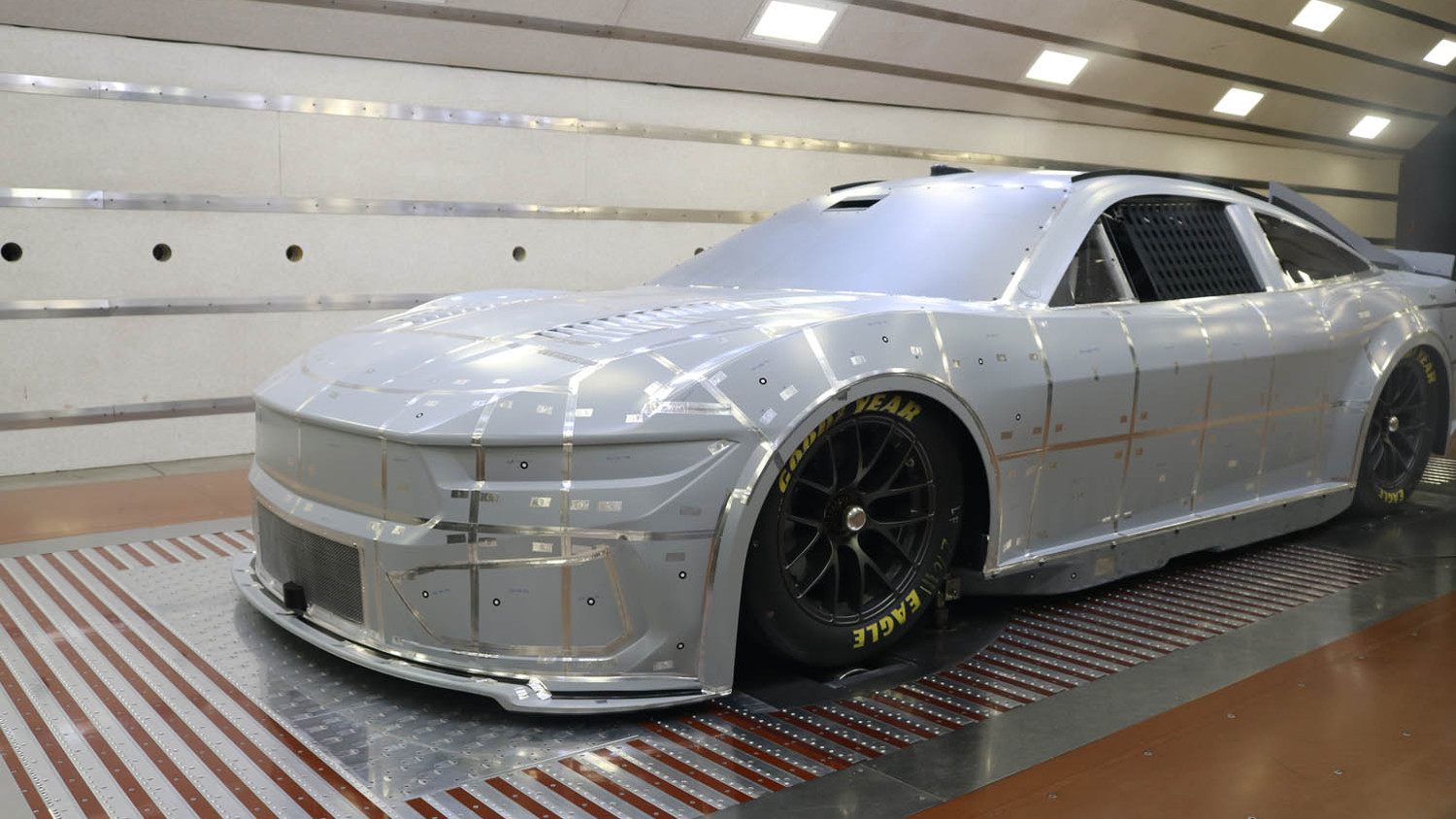
Following Covid, organisers recognised that television audiences didn’t miss the practice sessions, so whereas previously, teams had two or three hours to finetune cars at the track, now they get 20 minutes. “Everything has to be exactly right when you show up to the track,” says Cole Custer.
We don’t have a ton of sensors on the cars. NASCAR doesn’t allow it. The driver is the only one who can tell the team what’s going on Cole Custer, Stewart- Haas Racing
“We don’t have a ton of data on the cars that we can look at on the weekends. We don’t have tire pressure sensors. We don’t have load sensors. NASCAR doesn’t allow it.
The driver is the only one who can tell the team what’s going on. So, you try and give as much good feedback as you can to him, to try and make it better and interesting,” he says, pointing to Van Landingham. Car 00 has an advantage in that it is also sponsored by 3D Systems, part of a technical partnership between the team and the 3D printing giant.
His father Joe Custer goes on to explain that, sometimes, if there’s a significant cost attached to trying a new technology or material, management might put the brakes on trying it.
“But with a partner like 3D Systems,” he trails off, smiling widely, acknowledging the benefits. “They’re down the road, so there’s the personal relationship and that trust – and then turning [our engineers] loose with their menu!”
Anybody can buy a 3D printer, he adds, but when you have a 3D printer company as your technical partner, that adds substantial value, including early access to technologies, he suggests. “Even if it might just be a few months ahead, our competitors will look and wonder ‘How do they do that?’”
In racing, few advantages last for long. You might only have as long as it takes for a rival to figure out your engineering secret. But if that advantage holds up long enough for you to win that weekend’s race, that’s plenty in the fast-moving world of NASCAR.
This article first appeared in DEVELOP3D Magazine
DEVELOP3D is a publication dedicated to product design + development, from concept to manufacture and the technologies behind it all.
To receive the physical publication or digital issue free, as well as exclusive news and offers, subscribe to DEVELOP3D Magazine here