Solukon has announced that its polymer post-processing system SFP770 is now compatible with EOS P 1 and P 5 series SLS manufacturing systems and can accommodate building boxes from other leading printers.
The German post-processing system manufacturer also announced that its SFP770 unpacking device has been successfully patented.
Solukon introduced the SFP770 in the fall of 2020, presenting it as a postprocessing system for plastic parts manufactured by a P 7 series EOS printer.
Solukon said that the SFP770 was developed after an automotive customer approached its team with the request to be able to both unpack and clean polymer components automatically, without the user coming into contact with the plastic powder.
The system was created by Solukon CEO and CTO Andreas Hartmann in just a few months, with consideration for every requirement, such as compact design and maximum flexibility.
Solukon said that SFP770 is globally one-of-a-kind as it is the only system to include both an automated unpacking station and a cleaning station for SLS components in just one system.
The station should be compatible with EOS P 7 series systems and encompasses the 3D printer’s entire build box, thanks to the new adapters, the SFP770 can now also integrate build boxes from P 1 and P 5 EOS printers.
Solukon described the SFP770 process as straightforward: the loading phase is done by placing the build box in the system by a lift truck.
For the unpacking step, a vibrating sieve cover is placed over the inserted build box, which then rotates gently overhead following an optional programmable process, gradually separating the components from the powder. The loose powder is extracted from the sieve cover directly and without contamination and conveyed to a recycling unit or storage silo.
Once the unpacking process is complete, the build box rotates towards the basket and opens the sieve cover. The sieve cover now functions as a slide and the parts are slipped carefully into the basket. If necessary, users should be able to pause the automatic transfer process, to manually remove certain components that should not be cleaned automatically.
After transfer, the system can immediately be loaded with a new build box, while the components from the first batch are cleaned in the second half of the system, the basket.
Finally, for the cleaning phase, the basket rotates in the direction of the blasting unit and begins turning. The glass bead blast and ionised air cleaning process is fully automated and removes residual powder. Process parameters, such as rotation angle, blast intensity, distance or basket rotation, can be easily programmed online by the user.
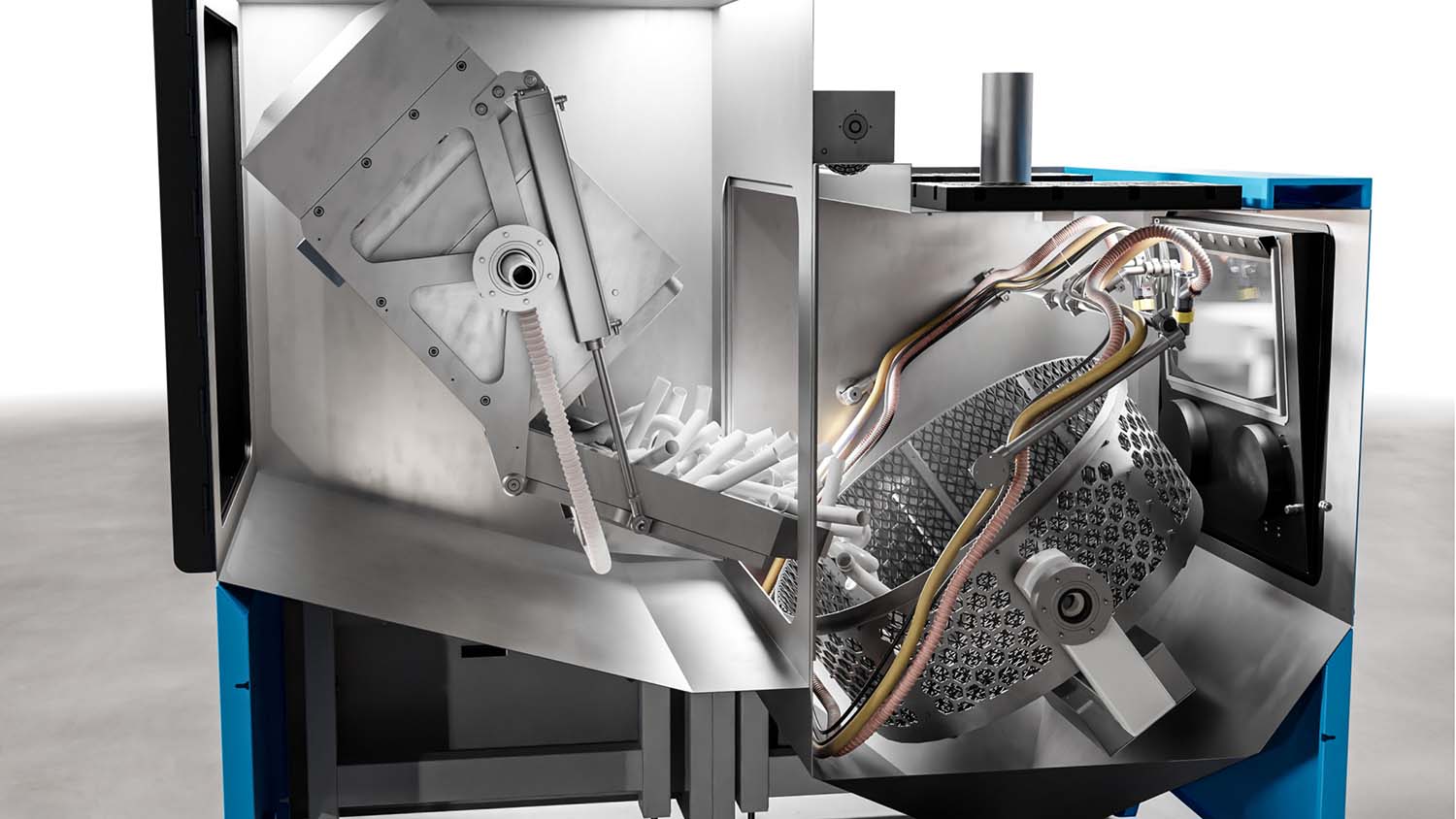
The core advantages of the SFP770, according to Solukon, include the automation of both the unpacking process and the transfer to the cleaning process, which means that the operator has almost no contact with the powder, and the flexible programming of the post-processing system.
This combination of two high-cost secondary processing steps aims to increase the acceptance and feasibility of industrial AM production.
“Because so many process parameters can be programmed, the SFP770 achieves the best cleaning results, independent of build material and without manual intermediate steps,” said Solukon CEO and CTO Andreas Hartmann. “Our system offers another advantage: parts of varying shapes and sizes can be cleaned simultaneously, which increases the flexibility and productivity of AM production.”
In addition to the cleaning process itself, Solukon’s SFP770 should also optimise the preparation of the blast material, for example, glass beads. While standard systems typically separate glass beads from plastic powder using air separators or cyclones, Solukon uses ultrasonic sieves and this should produce cleaner glass beads, resulting in almost no losses.
Thanks to new adapters, Solukon said the SFP770 can now accommodate and clean parts manufactured with EOS P 1 or P 5 systems.
“We’ve received several requests for a postprocessing system, especially for the EOS P 500,” said Hartmann. “Since the EOS P 500 is a standard plastic printer, our SFP770 postprocessing system paired with the correct adapter is now available to a much larger user base.”
Solukon has also announced that SFP770’s unpacking device is now protected by the European Patent EP 3 789 184 B1. This patent grant should underscore the novelty of this operating principle and protects the system’s high level of innovation.
Following the successful introduction and nearly two-year implementation of the SFP770 in industrial manufacturing environments, Solukon claimed it is well prepared for future integration of the SFP770 in fully automated manufacturing systems.
“We expect plastics manufacturing to trend strongly towards a focus on post-processing because it constitutes the decisive step in determining if something is truly manufactured in series or not,” said Hartmann.
“You can optimise a manufacturing process for serial production as much as you want, but if the subsequent post-processing fails to meet the same high standards, you will not have true serial production. At Solukon, we, therefore, expect to see an increased demand for automated unpacking and cleaning stations,” he went on.
“Thus, we are also ready to automate the loading and unloading steps. Discussions with international manufacturers and system suppliers are already in full swing. We are proud to be able to participate in the future of additive manufacturing in this area.”