Speed of delivery makes all the difference with custom products – and in-ear monitors are no exception. At ACS Custom, a fully digital workflow is used to produce earpieces for professionals
ACS Custom produces in-ear monitors (IEM) responsible for keeping musicians tied to their music when performing live on stage. Made from soft, medical grade silicone, each IEM is created on a bespoke basis for the customer, in order to provide the perfect fit.
Since customers often need fast access to these made-to-measure products, ACS Custom has built its business, based in Banbury, UK, around an entirely digital workflow, according to managing director, Andy Shiach.
“When we decide we want to make a product, we can design it and 3D print it within the space of a couple of days. Then, if we realise we need to revise our design, we can do that immediately,” he explains.
“If we had to tool and injection-mould the products we make, the time and costs involved would be prohibitive.” Instead, the company can go from a design concept to a final product in as little as three to four days.
All of its IEMs proudly feature state-of-the-art Knowles drivers and ACS’s own proprietary crossovers to ensure artists hear the music as it was intended to be heard.
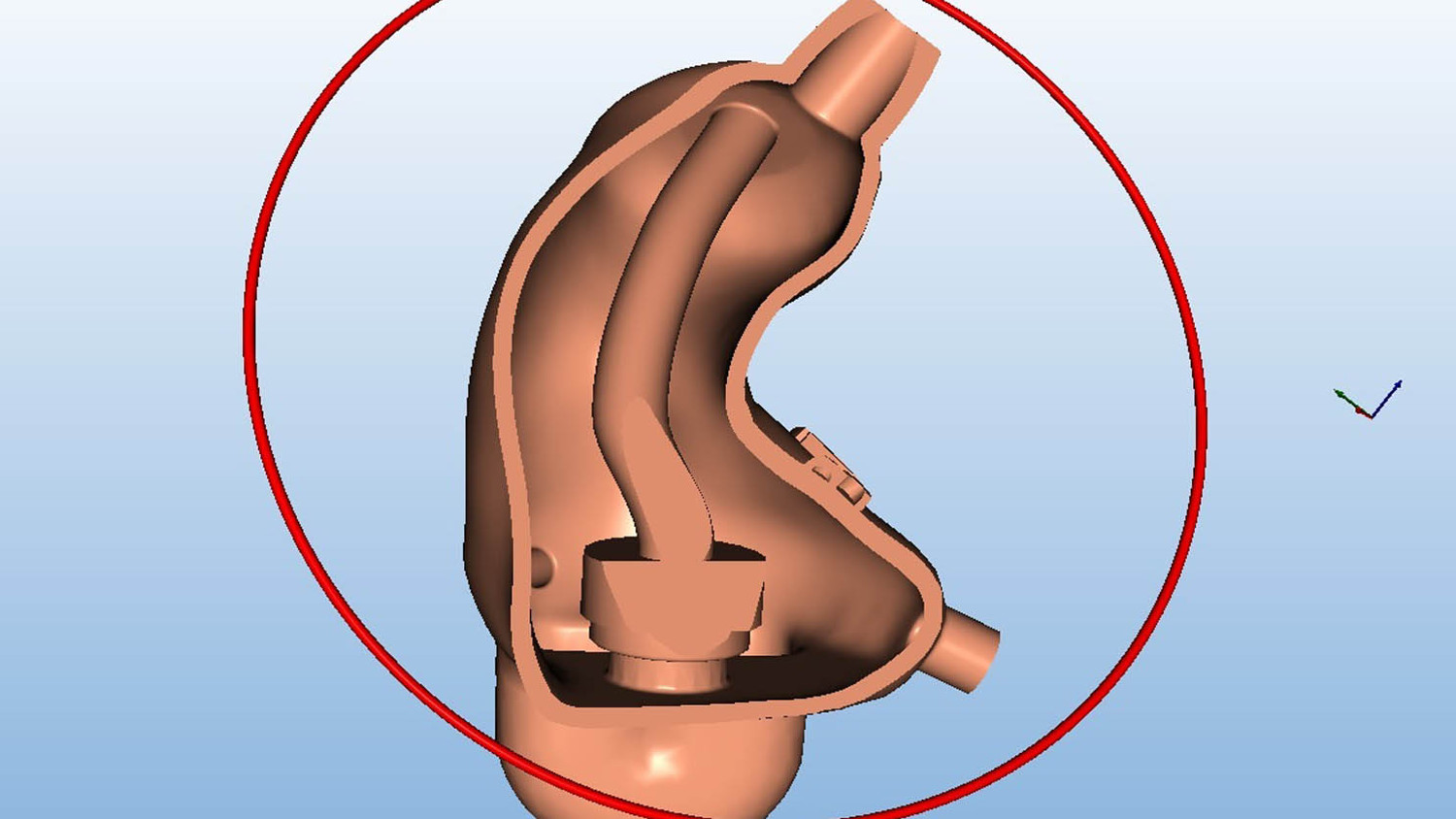
ACS Custom – Inside knowledge
For its earpieces, ACS Custom 3D-prints parts for eggshell casting, taking advantage of the ability to print ultra-thin walls using its 3D Systems Figure 4 Standalone to create moulds for injecting silicone.
Here, the material used is Figure 4 Eggshell-AMB 10 material. Once injected, the 3D-printed mould can be broken and peeled away – like an eggshell – to reveal a silicone part that ACS Custom then post-processes, marks and finishes.
The digital workflow isn’t just efficient. It also enables the company to tackle larger and more complicated products than ever before, according to technical director Dan Bennett.
“We can now print geometries inside the silicone moulds, whereas before, we would have to drill it all out by hand,” he says. “What’s more, the dimensional accuracy of the Figure 4 printer ensures we don’t need to do as many iterations or build tolerances into the parts.”
3D Systems’ 3D Sprint software plays a key role in attaining the surface quality required, says Bennett. “When the outside surface quality is important, we can reduce the touchpoint size and position of supports really accurately.”
The digital workflow is also what enables ACS Custom to give its customers an ‘anytime assurance’ that lost or damaged products will be replaced precisely to original specifications.
“If we did this by hand and you ever needed a replacement, it would never be identical to the one you lost,” says Shiach. “With 3D printing, we can absolutely recreate the same article.”
For ACS Custom, the digital workflow drives business success; whether it’s helping out an existing customer needing a replacement, or attracting a new client wanting a bespoke item.