New coatings and materials are transforming the 3D printing of micro components for innovative products — and the revolution has only just begun, writes John Kawola of Boston Micro Fabrication
The 3D printing industry has recently faced challenges, with companies in the sector experiencing declining stock valuations, fundraising struggles and corporate restructuring. However, it is important to put this turbulence into perspective.
We may not be seeing the same explosion in 3D technologies that we saw 20 years ago, but that doesn’t mean the industry is stagnant. In fact, new collaborations and new applications for these platforms are actually expanding the value of 3D printing in many industries.
A lot of progress has been made. Despite initial challenges, 3D printing has evolved from providing expensive prototypes for big companies to accessible tools for engineers of all kinds. In the last 15 years, major advancements have been made in manufacturing applications, particularly in sectors such as dental and aerospace. Although at times there may have been excessive venture capital investment and unrealistic expectations – my own opinions included –the industry has moved forwards relentlessly.
It is now crucial for 3D printing companies to build sustainable businesses and to focus on providing their customers with valuable tools and options. As we continue to innovate, the additive manufacturing industry will play an increasingly vital role in pushing production into the future and solving real problems.
Unique value at the micro scale
One way this progress shows up today is in the identification of specific use cases that are uniquely enabled by 3D printing, and then the layering on additional technologies or functionality, in order to expand the possible solutions to which 3D printed parts might apply.
I am part of a company called BMF, where we are focused on very high-precision and high-resolution 3D printing – a capability typically valuable in the making of small parts with fine features and tight tolerances.
The move toward miniaturisation in many industries has opened doors for 3D printing at this micro scale, empowering engineers and scientists to push back the frontiers of innovation in their industries.
As technology becomes smaller, precision becomes paramount. This is where 3D printing excels, accelerating innovation and efficiency
While 3D printing was initially hyped for its potential in consumer applications, its true impact lies in product development by companies. Popular printing techniques have been re-engineered to support the production of large-scale products like homes, cars, even planes. And we’re also seeing a flurry of opportunities for 3D printing at the micro scale, where high-precision requirements make traditional manufacturing techniques less than ideal.
As technology becomes smaller, precision becomes paramount. This is where 3D printing excels, with its on-demand, cost-effective and customisable nature, which accelerates innovation and efficiency.
Additionally, when considering traditional production techniques such as moulding, the number of units needed in some of these highly specific applications does not always warrant large-scale manufacturing approaches. Instead, 3D printing can be used in these cases to deliver more precise, cost-effective parts.
Sparking innovation
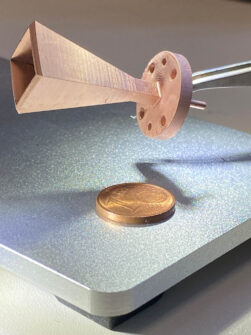
Beyond finding new applications for traditional 3D parts to replace manufacturing or production, new collaborations are expanding the limits of what these parts can do. For example, we recently expanded the functionality of our precision 3D micro parts by coating these materials with environmentally resistant metallic or non-metallic conductive coatings.
By partnering with micro component and coatings expert Horizon Microtechnologies, we have been able to create an end-to-end offering that begins with initial product design through manufacturing, giving more flexibility for companies in need of highly versatile product development resources.
These coatings expand the possible use cases for our parts, while delivering the same high level of precision our customers require. Now, we can wholly or selectively coat micro-parts with a non-metallic conductive layer. We can add environmental resistance to parts, enabling the creation of microscale devices that are more durable, reliable, and better suited for use in harsh environments, characterised by aggressive chemicals or high temperatures, for example. And we can wholly or selectively coat micro-AM parts with copper. This helps broaden the use cases for micro-3D printing technology across new industries and applications.
Beyond surface coatings, new printing materials are also pushing the boundaries on innovation. Properties demonstrated by, for example, electrostatic discharge (ESD) safe materials are important, because they prevent damage to products during the production process. Creating ESD-safe materials – either by taking precautionary measures or by using materials that are themselves ESD-safe – can save time and money, as well as increase the efficiency of workflows and operations.
We recently worked with Mechnano to offer its Formula1μ ESD for use with BMF’s 200 and 300-series 3D printers. What sets this cutting-edge, black, rigid, static-dissipative photopolymer resin apart is its unique formulation, which utilises Mechnano’s proprietary ‘discrete carbon nanotube’ technology. This now delivers the highest tensile strength option available on the BMF platform and is the only resin that dissipates static electricity.
With the dual increase of electronics usage and decrease in chip size, the applications requiring micro-ESD parts are growing daily.
Shrinking products
In all the areas where we supply our platform, we’re seeing miniaturisation as a key driver in the products that customers are developing, especially in OEM industries such as electronics, optics and photonics and medical devices. Many of these products are highvalue and, due to stringent requirements, are uniquely enabled by our technology.
Such previously impossible applications are opening doors to entirely new industries and applications for 3D printing technologies. As we continue to push the bounds of innovation through our own Research Institute and new collaborations, the book of use cases uniquely enabled by high-precision, small-scale 3D printing will not only continue to expand, but become a necessity.
Soon, micro AM parts will solve puzzling design and manufacturing dilemmas that have long hindered product advancement. So, while 3D printing overall may no longer be the big story, it’s solving real problems and fostering a wealth of innovation.
About the Author:
John Kawola is Chief Executive Officer for Global Operations at Boston Micro Fabrication (BMF).
He has more than two decades of business leadership experience across the additive manufacturing, 3D printing and materials science industries.
BMF is focused on introducing and scaling micro-3D printing technology to a range of industries that demand a high level of resolution and precision
This article first appeared in DEVELOP3D Magazine
DEVELOP3D is a publication dedicated to product design + development, from concept to manufacture and the technologies behind it all.
To receive the physical publication or digital issue free, as well as exclusive news and offers, subscribe to DEVELOP3D Magazine here