DEVELOP3D spoke with three ceramic 3D printing vendors about the rapidly growing sector, the materials that designers need to know about and the industries set to benefit from additive manufacturing’s widening use of ceramic materials
The material properties that ceramics can offer have long been desired by designers and engineers, but the complications and costs involved have usually seen them opt for cheaper and more easily available plastics and metals.
Until now, that is – because a new breed of ceramic 3D printing technologies is making previously impossible shapes a reality. At the same time, the prospect of parts capable of withstanding higher temperatures and more resistant to corrosion, wear and pressure, is starting to change how many products are considered by designers.
“When it comes to conventional forming methods, such as milling, pressing and injection moulding, companies are often limited to designing parts that can be produced, instead of parts they want to produce,” says Isabel Potestio, head of sales and marketing at Austrian ceramics 3D printing company Lithoz.
“The design freedom offered by 3D printing is, in this area, simply unparalleled, allowing designers to focus more on functionality when coming up with new concepts.”
Problems are getting solved along the way. In the past, ceramic materials before sintering proved too fragile to machine or mill. After sintering, they became too hard to cut quickly or cheaply.
At XJet, nanoparticle jetting technology is being used to address such issues, explains Dror Danai, the Israel based company’s chief business officer. XJet’s process, which features an innovative water-soluble support material, is allowing for more complex parts to be produced with ceramic materials.
“The manufacturing process has limited the use of technical ceramics in the past,” says Danai. “With the ability to additively manufacture ceramics, businesses can enjoy all the acknowledged benefits for applications that weren’t previously possible.”
Material challenges
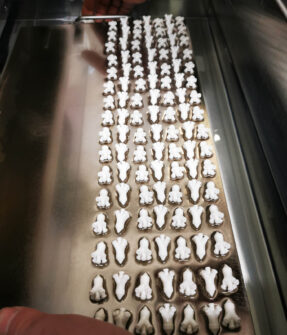
Meanwhile, materials are constantly improving, says Trent Allen, CEO of US-based AM ceramic powders manufacturer Tethon 3D. Key materials that designers should know about include what he calls the “bread and butter of the ceramics world”, Alumina, along with materials such as Zirconia for more hard-wearing uses.
“As the aerospace and space industry grows over the next few years, I think you’ll see more ceramic carbides and unique ceramic metal matrixes (Cermets) come into the market,” Allen predicts.
The use of full ceramic resins, he adds, may eventually enable 3D printing to fulfill its promise of becoming an industry more focused on sustainability, moving away from more toxic and harder-to-recycle polymers. “We are printing with dirt, essentially,” he says of the current situation.
It’s not just about the material, of course, but also the density of materials achieved, adds XJet’s Danai. “The ceramic AM industry, and especially XJet, has more recently achieved the right density and mechanical properties that open the doors for large acceptance of the technology,” he says.
Exciting applications
A key aim for all vendors at present is helping more sectors find new and exciting applications. Executives from all three companies – Lithoz, Tethon and XJet – point to the aerospace, defence and machinery sectors as areas where the most interest is seen, but other sectors are intrigued, too, particularly for electronics applications, such as the manufacture of semiconductors, because of the excellent insulation properties of many ceramics.
Another potentially huge sector for the technology is the manufacture of custom medical implants, with the bioresorbable properties of some ceramics making them more suitable for implants than current metals. Lithoz’s Potestio explains that ceramic implants made of materials such as tricalcium phosphate or hydroxyapatite dissolve in the body as the organic bone heals and grows. “As such, ceramic implants promote bone healing and the need for a second surgery to remove the implant is completely eliminated,” she says.
Education of potential users is the biggest challenge at present, given how rooted design and engineering is in traditional manufacturing methods and materials. “I don’t think a lot of designers and engineers know they can 3D print in ceramics yet,” says Allen.
Tethon introduced its Bison 1000 desktop 3D printer for users to experiment with the various resins and ceramic fills it produces. Despite it being the best-selling purpose built ceramics printer, most of its customers seem to come from defence and aerospace materials R&D labs. Getting this technology into the hands of designers for front-end change is the next step.
Software also has a role to play, says Danai. “Design for AM allows improved geometry, such as savings of weight, overcoming design challenges – solving flow issues for example – and other values that make this a more attractive and more affordable solution for complex applications.”
Potestio agrees and cites rapidly modernising supply chains as a complementary shift, with the increasing digitalisation of industrial part production proving a necessity at a time when the Covid-19 pandemic continues to disrupt global supply chains.
She says: “As more and more interconnected production sites are being created all over the world, the entire production chain is rapidly being redesigned.”