The new HP Universal Build Manager software aims to solve some of the complex and heavy computation involved in additive manufacturing.
This is also the first time that a software application has been launched built on Dyndrite’s much-vaunted accelerated geometry engine.
HP states the Universal Build Manager is a first of its kind solution which leverages proprietary HP software and data innovation, and the Dyndrite Accelerated Geometry Engine.
The new additive manufacturing build manager takes advantage of the GPU-accelerated processing and Python scriptability inherent to Dyndrite’s engine.
HP claims that the combination enables users to simplify and automate build preparation across their additive manufacturing technologies at supercharged speeds.
The goal, it would seem, is for HP to provide a singular platform in which an organisation looking to take advantage of additive manufacturing at scale can manage its part production preparation processes – and do some in a very efficient manner.
The company is looking to offer this solution to those companies using a lot more than just its Multi-Jet Fusion machines – with the UBM software supporting all manner of production methods and machines, from MJF to FDM, from BJT to LBPF, from SLE to EBM.
While it’s all well and good discussing process support, what this really needs is support and integration from the vendors developing those machines and this is where things get really interesting.
Out of the box, HP’s UBM software will have immediate support for a range of additive manufacturing hardware vendors, including Aconity 3D, Aon3D, Aurora Labs, EOS, ExOne, Open Additive, Photocentric, Plural AM, Renishaw and SLM.
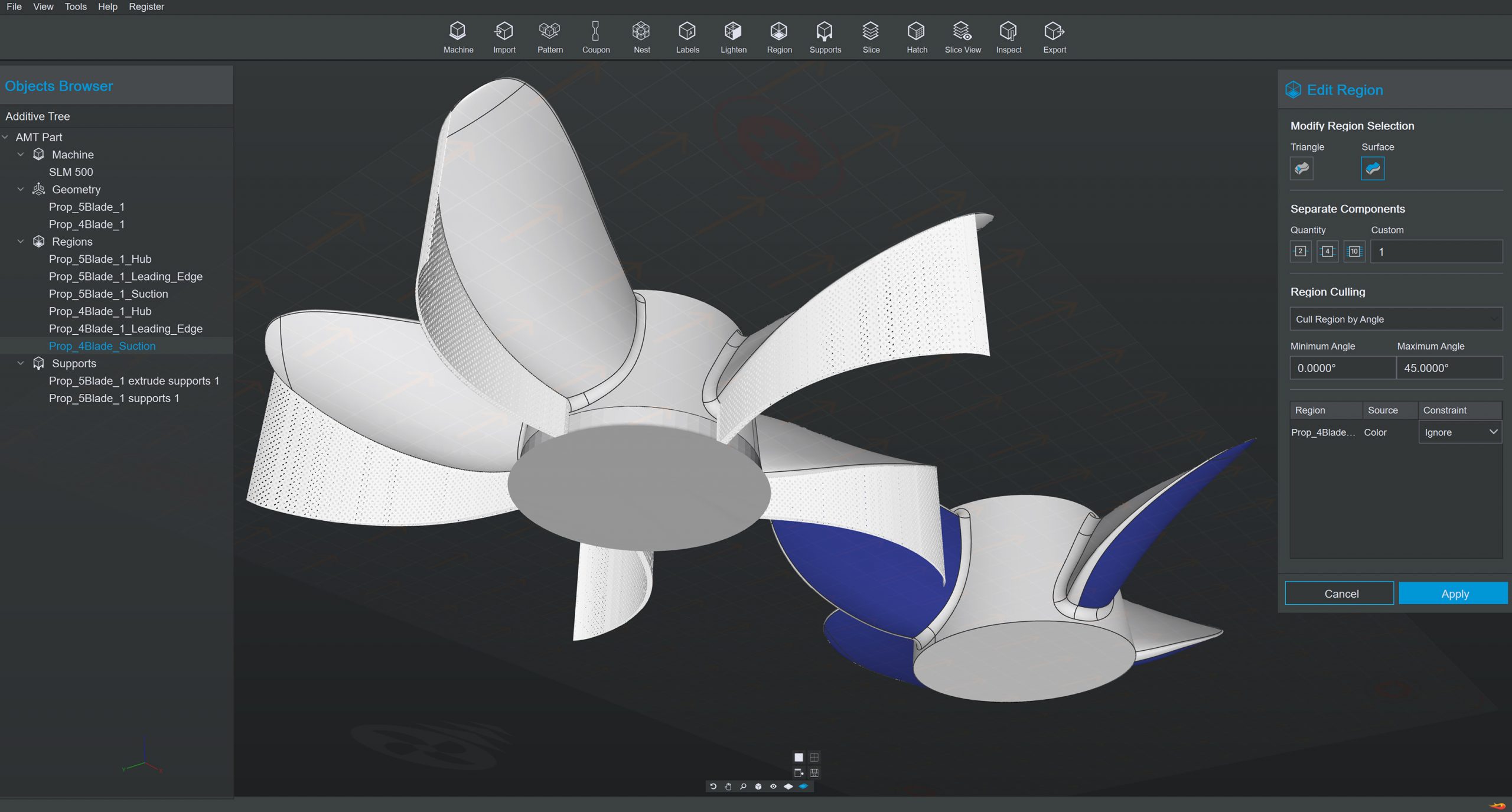
“We are addressing software challenges in the additive industry that have prevented it from becoming mainstream and are providing capabilities to help customers accelerate the journey to digital manufacturing,” said Ryan Palmer, global head of software, data and automation, HP Personalization & Industrial Business.
“The new HP Universal Build Manager simplifies, automates, and delivers a digital-first approach to manufacturing. This solution will enable customers to explore new areas of complexity and value, push the boundaries of sustainable production, and automate critical steps in their digital workflow.”
The software is also the first time that Dyndrite’s much-discussed-but-rarely-understood technology has been brought to market as a commercial product, something that Dyndrite’s CEO and founder Harshil Goel is clearly relishing.
He said: “Going forward, this moment will be recognised as the point where the additive manufacturing market broke away from the status quo of legacy technologies and file formats.
“Even before we founded Dyndrite we knew we needed to work with industry leaders like HP centered on pushing digital manufacturing forward. We are excited that HP shares our vision for software disruption and look forward to collaborating to push the boundaries of our innovation.”
Hyperbole aside, this is an interesting move: Dyndrite’s technology looks impressive, modern (the GPU support is interesting) and affords some interesting automation capabilities.
It’s good to see being used, rather than pontificated about. We should, perhaps, temper this with a little more understanding and realisation that Dyndrite and HP are both newcomers to the additive game. There are other organisations out there that offer analogous capabilities and have done for decades. Also, HP need to convince the other machine vendors to sign up to this and implement support for it.
The reality is that there are serious challenges to be addressed if additive is to truly start to compete with more traditional methods of manufacturing and part of that is a process management piece.
Can the data that designers want to produce be manufactured in a timely, robust and repeatable manner that truly supports the benefits they could derive of more complex geometries and material definitions, of more customisation and automation?
Can production across large scale additive be managed in a manner that accounts for the problems of repeatability, of the need to finesse each build based on the peculiarities of the machine, of the material and the parts being built? Can we truly design for additive manufacturing and take advantage of all those promises if much of the final definition of those parts is done at the pre-production stage?
This isn’t just a question of buying a singular, monolithic build prep software to run on all of your machines, it’s way more complex and something that HP’s Anthony Graves, a senior director, head of product and strategy, digital manufacturing, picks up on.
“Where there is a mission-critical need for parts, at low volume, additive meets the need,” said Graves.
“The ability to pivot immediately between jobs, without the need for tooling, with no Minimum Order Quantities (MOQs), makes additive a critical asset. But now we have to fix the problems and scale the solution.
“Our mission is to unlock the promise and potential of additive manufacturing through high performance, scalability, and automation. In this world quality and accuracy of parts has to become the norm, not the exception, and Dyndrite and HP can deliver on all of that.”
“We want to leverage modern technologies and innovate on them to enable additive to scale and reach its potential,” continued Graves. “We want to become a leader in supplying industry-wide and universal software solutions for digital manufacturing, for everyone – end users, enterprises, OEMs and ISVs.”
HP’s Universal Build Manager will be going into beta shortly and you can apply to gain access here.