Fortify has announced a new materials handling system for its Flux One 3D Printer, enabling it to process 3D printing polymers packed with reinforcing fibres, while mitigating sedimentation and aggregation while waiting to be printed.
The new Continuous Kinetic Mixing (CKMTM) is built-in onboard the Flux One, and by dodging these issues, users can better enable Fortify’s Fluxprint technology, that tunes composites voxel-by-voxel.
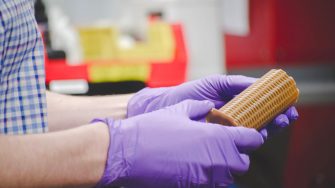
Electromagnets during the printing process apply a precise magnetic field to the composite SLA resin, while a digital light processing projector selectively sets areas of the resin, repeating multiple times within each layer to achieve different composite alignment directions.
“Developing Continuous Kinetic Mixing was an integral part of Fortify’s strategy. It will play a critical role in manufacturing functional parts,” said Fortify CEO and Co-Founder Josh Martin.
The company has recently expanded its successful use cases to include metal injection moulding, where it has blended ceramic fibres with resin to manufacture tooling able to withstand the extreme temperatures and pressures of the moulding process.
Fortify claims that its platform is the industry’s first to include onboard mixing and magnetic alignment technology, and will begin to ship the Fortify Flux One this summer.