At Eschbal, a Swiss manufacturer of window systems, introducing in-house 3D printing from Sintratec has shed new light on ways to optimise its design and manufacturing processes and make them more sustainable
As winter nights draw in, capturing as much of the previous day’s sunlight and warmth as possible is key to a comfortable, cosy indoors.
Known for its elegant and slim frame profiles, which increase the amount of light entering a room, Switzerland-based Eschbal designs and manufactures all its windows within the region for the local market.
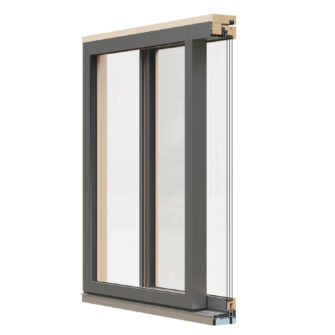
Its Sirius window brand uses local wood and recyclable aluminium. This has a positive effect on the product lifecycle, helps to create jobs and apprenticeships in Ober-Ohringen where the company is headquartered, and fosters customer intimacy and improved product quality.
The Eschbal R&D team creates designs that maximise the surface area of glass, letting in more light while maintaining excellent thermal properties, and develops custom solutions so that the company can quickly respond to individual building projects.
Physical prototypes are indispensable to the design team, according to Eschbal technical manager Michael Ebnöther. Before investing in expensive tooling for injection moulding, the development team needs to have a physical part that its members can test and verify. It’s crucial that 3D-printed SLS prototypes have very similar properties to injection-moulded parts.
Internal demand for faster prototyping led the team to acquire its own 3D printer, with the Swiss company opting for another local brand, installing a Sintratec S2 at its production facility.
Compared to its previous process of using external suppliers, the ability to 3D-print SLS parts in-house saves Eschbal several days of development time, enough to run several iterations of a design idea.
“In terms of design, 3D printing gives us much more creativity. We can now develop things that we hadn’t even thought of before,” explains Ebnöther.
“With the SLS process, we were especially impressed by the tolerances of up to 0.1mm and the surface quality. In addition, other technologies such as FDM cannot deliver the quantities we need. With the S2, we can print up to 100 parts within 24 hours.”
Light as air
To achieve the lightest possible frames while maintaining strength, Eschbal’s design team has been developing new optimised connector designs, producing prototypes in PA12 on the S2.
This has allowed them to iterate on a connector’s form and verify it as they progressed. “As a result, we were able to reduce the weight of the new connector by 33%,” says Ebnöther. “It is simply easier, faster and cheaper to push the boundaries.”
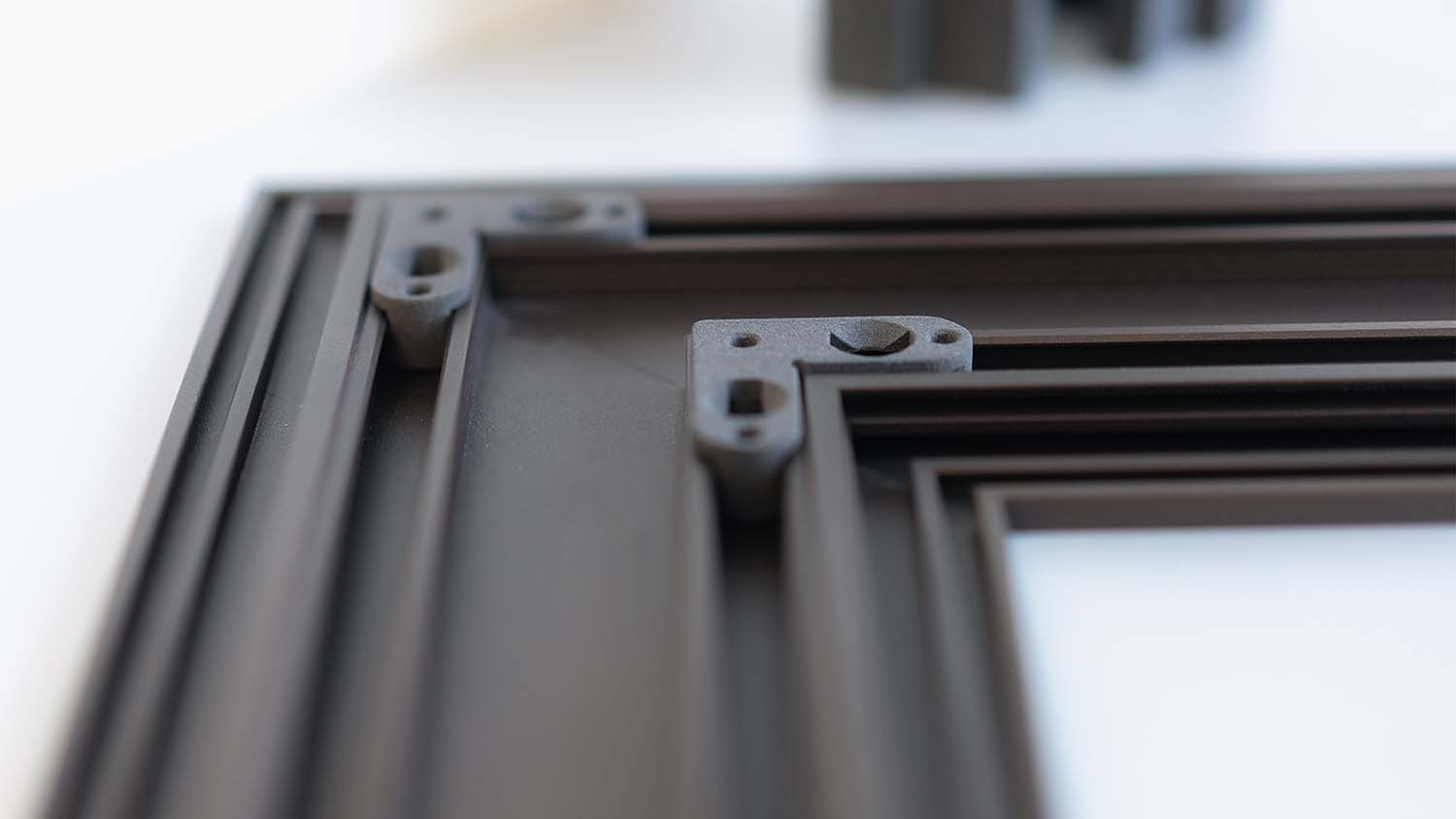
For small quantities, Eschbal also uses the S2 to manufacture series parts. For example, in the case of a reinforcing element that is only required for particular combinations of frames, it would not make financial sense to cut tooling for injection moulding. The component can instead be produced on demand on the S2.
Members of Eschbal’s production department are also grateful for the SLS printer. Tools and auxiliary materials such as jigs and fixtures for its CNC machines were previously commissioned from an external supplier. Now, they’re 3D-printed in-house to precisely fit the corresponding profile, too.
Cheaper and faster, in-house SLS prototyping has opened a window to more responsive designs and sustainable production.
This article first appeared in DEVELOP3D Magazine
DEVELOP3D is a publication dedicated to product design + development, from concept to manufacture and the technologies behind it all.
To receive the physical publication or digital issue free, as well as exclusive news and offers, subscribe to DEVELOP3D Magazine here