Aerospace is rapidly adopting additive manufacturing in all areas, from space rocket components to aircraft interiors. We asked Vinu Vijayan, aviation and space specialist at EOS, how the technology demands of companies in this sector are changing and where they’re planning to take us in the future
Q: The aviation industry was hit hard by the pandemic. What trends are you seeing now, coming out the other side?
A : I think that additive manufacturing (AM), contrary to other technologies, saw opportunities even during the crisis. The space industry has been substantially more resilient, and we see that the adoption of AM is substantially increasing. There is a really strong movement, from single-laser systems to large multi-laser systems, indicating that customers want more parts or bigger parts.
We have been working with big companies and names in the space industry, but also with start-ups that are contributing towards the new space economy. The startups have begun investing in in-house manufacturing AM capabilities. That’s a key enabler. Earlier manufacturing had to be undertaken with select external companies with specific established infrastructure and competency, because it was too complex to be done internally. We saw this new space evolution happening in the US first, but it has now reached Europe, India, China, Japan and Korea.
We see a lot of movement on the metal side, but also on the polymer side. Many aerospace qualifications are well underway, and aim to replace parts with additively manufactured components based on process-level qualifications, where the system as well as the material will be qualified. Apart from this, issues such as taking a circular-economy approach through elements such as a good processes for powder lifetime management are becoming very tangible and relevant, with research underway now.
Q: What is the ecosystem like for aerospace start-ups?
A : All these aerospace-related start-ups have capexintensive ambitions – they need the funding. But what additive gives them is the ability to try out their concepts substantially faster.
Even though AM might appear to be an expensive technology at first glance, if you’re not looking at producing the same parts for the next five years, without too much complexity, then in comparison to traditional technologies, the initial steps that you need to take are not so expensive. There is no need to invest in long-term fixed assets, tooling and so on, which means they can focus on their concepts and possibilities, rather than worry about manufacturing bottlenecks.
So, I think that business model, product and design innovation are the focus, for which AM is an enabler.
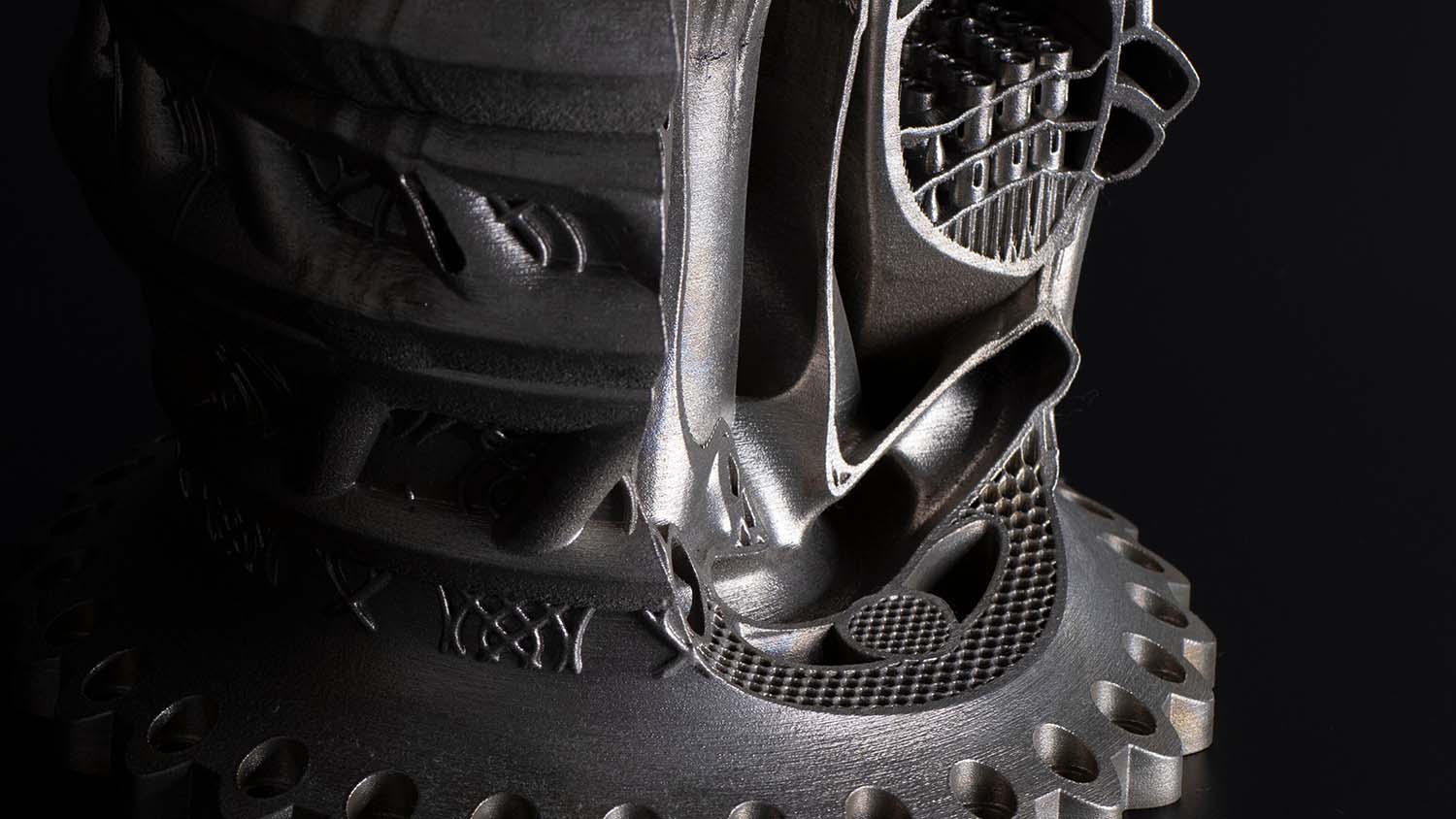
Q : What is EOS doing to help with qualifying parts?
A : For EOS, it is important as the first step to establish a healthy level of confidence and trust in the technology, which means that we are investing time and experience with clients to qualify material, systems and processes, not just partially. And then, once you have confidence on that level, we are trying to enable the end users of the technology, such as an airline, by building up the data needed to give them confidence in the process controls.
On the materials side of things, we can test and establish industry-standard technology readiness levels, providing the data required to have a minimum level of compliance. This is then guaranteed through the quality control processes we have.
Where an organisation is using distributed manufacturing, our systems can include functionality that enables secure digital rights management. This enables a customer to create a process for a 3D-printed part that can be sent to any hub to be printed, and the customer can be confident that nobody has tampered with it.
Q : What do you find most exciting about the future of additive and aerospace?
A : The most exciting part of additive manufacturing in aerospace is that it is constantly transforming the way components, sub-assemblies, and even complete systems are designed and manufactured. AM is transforming many parts of industry in an almost irreversible manner. This is happening both by increasing the footprint of AM (both in terms of size of parts and number of parts) and reimagining the design space.
The other side is where you’re looking at the upstream process. There is a limit to what a human designer can do there to use additive manufacturing to its maximum potential, and this is where companies like Hyperganic come in. The design for an aerospike engine that we showcased together recently hasn’t seen a single day of CAD – zero CAD! It was completely algorithmic.
Algorithmic design is super-focused on performance. It lacks the bias of a designer who’s scared to try out things. The designs are then sent directly to our 3D printing system. The aerospike component was a case of a first-time-right print. Technology like this is creating components that are from a completely different solution space, a space that is almost inaccessible to us as humans.
www.eos.info
About the Interviewee
Vinu Vijayan is responsible for Aviation & Space within EOS for the EMEA region.
He originally comes from the aerospace industry, having worked for companies such as Airbus, with several years of leadership roles in aerospace, manufacturing, sales, business development & project execution.
Vijayan graduated with a Bachelor’s degree in Mechanical Engineering, followed by a Master’s in Automation & Robotics (Flight system identification) in German, and an MBA from the Collège des Ingénieurs, Paris.