A new model on the production line drives a need for new tools, jigs and fixtures. At Audi Sport, design automation and 3D printing technologies gave the E-Tron GT a smooth factory roll-out
German automaker Audi reserves its Audi Sport Bôllinger Höfe facility for the manufacturing of prestige models, including the high-performance Audi R8 and the fully electric Audi E-Tron GT.
Located in Heilbronn, Germany, the factory’s assembly line transports cars from station to station, where order-specific parts are installed. Every station has a limited time to complete tasks and much of the assembly work is carried out by hand. Audi Sport offers equipment lists exclusive to Audi RS models, while also fulfilling bespoke requests for individual customers.
The mechanics’ workflow is optimised to maintain quality and speed along the line, with custom tools, jigs and fixtures playing a huge role in this process, making tasks easier and more ergonomic.
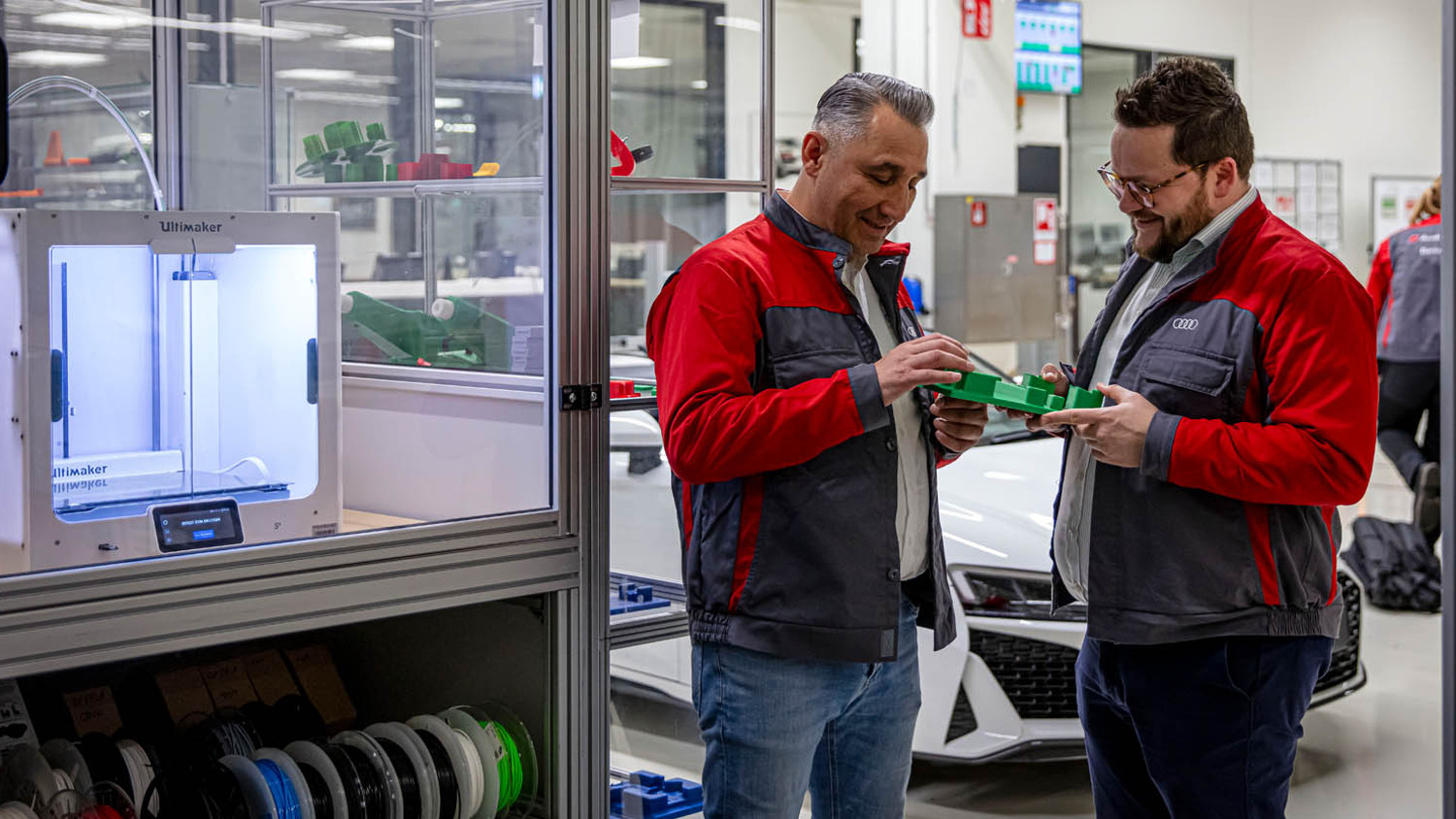
Some tools help align parts during installation – easing a roof panel into place, for example, or fixing badges in the correct spot on a car’s exterior. This increases the consistency and quality of the final products, while saving minutes per unit.
Quality control tools make sure all cars from Audi meet the highest standards. Custom jigs are mounted to parts of the car to measure alignment and tolerances. Audi Sport created a custom jig to focus the head-up display (HUD) on the dashboard of the car. The jig uses two lasers projected on the installed HUD. When the lasers align, it means the reflective glass is installed properly.
Many parts need to be assembled before they are installed. Tubes need to be attached to a central fluid plate, cables and heatsinks must be added to a central control unit, and so on.
Audi Sport uses hundreds of fixtures to hold parts in place for easy assembly. Not only do these fixtures save hours, but they have a big impact on the consistency of production. Many of these fixtures are also designed to have a positive impact on ergonomics for the worker.
“We produce nearly 800 tools and jigs and fixtures for our factory here,” says Cem Guelaylar, Audi Sport’s 3D printing expert. To outsource a part takes several weeks or even months, he says, depending on the supplier and the process.
By 3D printing parts in its own factory, Audi has slashed that timeframe dramatically. “It has helped us to get these tools in a very short time,” says Guelaylar. “The workers come to us and say, ‘I need a fixture to assemble the cars.’ It takes one day to get this tool in their hands.”
When the new Audi E-Tron GT was introduced, the Bôllinger Höfe factory needed almost 200 new tools, jigs and fixtures to get production underway.
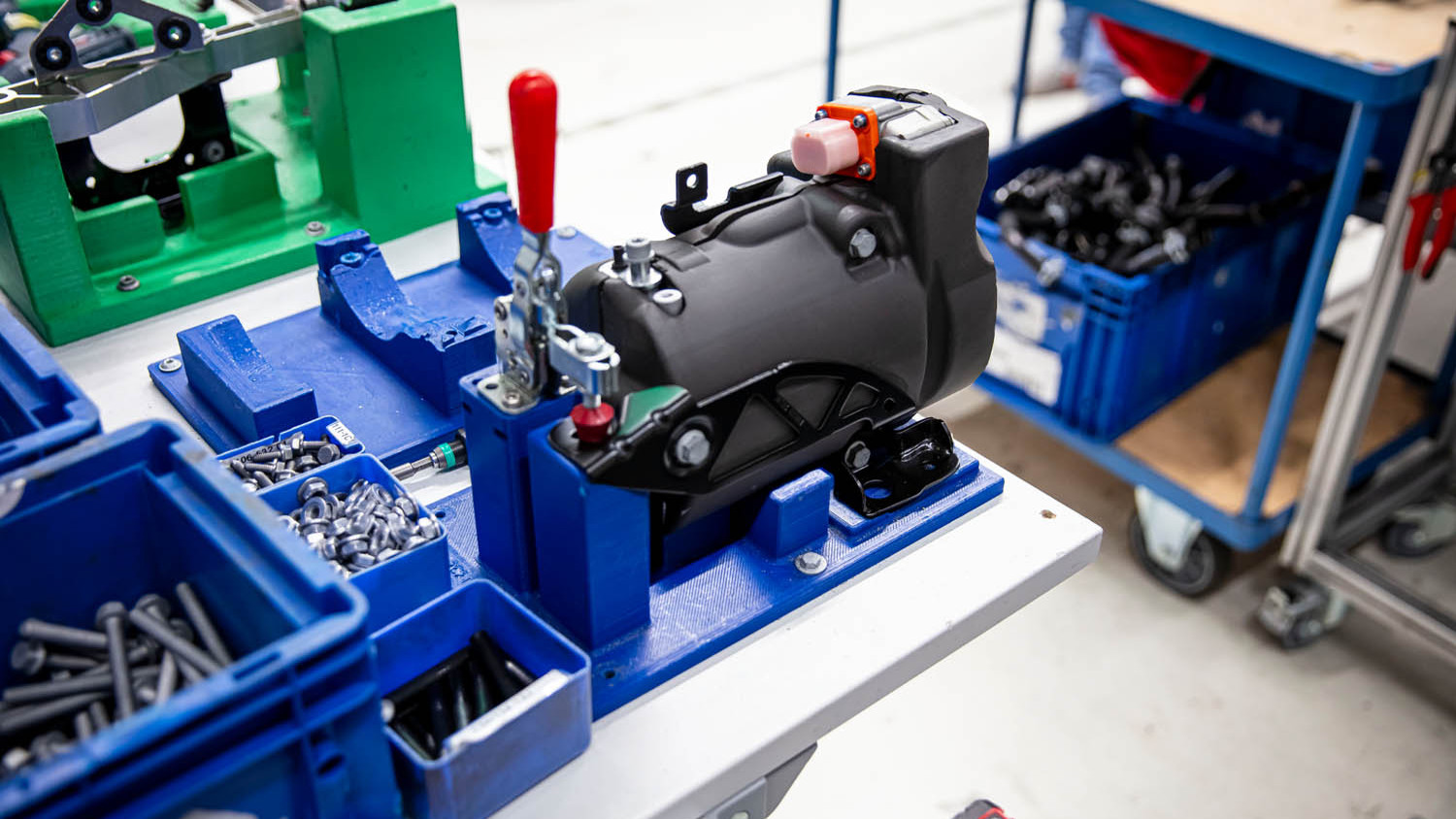
To develop the parts as quickly as possible, Audi Sport’s engineers turned to Trinckle Fixturemate to create the fixtures for assembly. A CAD model of the part is imported and positioned in the Fixturemate software, which creates an accurate holding fixture around. The user then adds supports and holes where needed so it can be mounted to a desk or bracket.
A library of off-the-shelf tools such as clamps helps the engineer quickly build the necessary fixture set-up digitally, with Audi’s team able to quickly design tools in 10 to 20 minutes on average using Fixturemate.
“Fixturemate helped us in a short time to bring a lot of fixtures,” Guelaylar notes. “Normally, in classic construction, we need two hours, three hours, four hours, depending on the size of the part.”
Fixturemate is very easy to use, he adds, and by using it instead of traditional CAD, the engineering team can free up members with specialist CAD knowledge to tackle more productive tasks.
“We can bring trainees and show them how to use the Fixturemate software, and they can directly work with this software and bring the fixtures in a short time.”
Once a part is designed, it is sent to the facility’s 3D printing room. Using several FDM 3D printers, including UltiMaker S5, Audi Sport produces the parts using Tough PLA. This material has flex and strength properties similar to traditional ABS, but prints more easily.
Tools are also printed for the protection of car parts, using TPU 95A, a soft material designed to stop parts from being damaged or scratched, and ESD-safe PLA is used for some more specific applications, including fixtures that handle electronic components.
Using this straightforward in-house process means that Audi Sport can produce tools within the same day and at a fraction of the cost as compared to outsourcing their production. When a part doesn’t meet requirements, it can quickly be improved and reprinted.
By relentlessly seeking more efficiency through adding automation to its in-house 3D printing capabilities, Audi Sport has reduced its tool production costs by over 80%.
By keeping production in the same carbon-neutral 40,000 square metre facility, the company can better manage its sustainability footprint, making its electric E-Tron GT’s production even better for the environment.
And by delivering parts in hours, rather than days, and putting production of prestige models into gear faster, Audi has found a quick fix for its fixtures.
This article first appeared in DEVELOP3D Magazine
DEVELOP3D is a publication dedicated to product design + development, from concept to manufacture and the technologies behind it all.
To receive the physical publication or digital issue free, as well as exclusive news and offers, subscribe to DEVELOP3D Magazine here