3D Systems has added a glut of new technology to see out 2020, with key new 3D printers – including the new SLS 380, new metals DMP Flex and Factory 350 models, and materials for industrial applications.
The SLS 380, says 3D Systems, delivers high levels of repeatability, improved throughput, and reduced operating costs for more effective, efficient digital manufacturing.
The new SLS 380 features a custom algorithm that manages 8 separately calibrated heaters, together with an integrated high-resolution IR camera that captures over 100,000 thermal data samples per second to manage, monitor, and control thermal uniformity within the build chamber.
A partnership with AMT enables users to use PostPro for cost-effective batch production parts on the SLS 380, helping maintain levels of throughput, consistency and part performance.
As part of this new platform, 3D Systems is also introducing a new Material Quality Control (MQC) system, the MQC 600.
The MQC ensures an optimal ratio of fresh to recycled material and the MQC 600 is optimised to deliver material to up to four printers simultaneously, minimising material waste and eliminating operator intervention. The company is planning general availability of the SLS 380 for the first quarter of 2022.
As the company continues to build out its enterprise offering, new dual laser DMP Flex 350 and DMP Factory 350 models reduce build time, accelerating 3D Systems’ appeal to healthcare and industrial production applications.
The two lasers are claimed to help reduce build times by up to 50 per cent and lower cost, while maintaining the benefits of its solo laser sibling, like its quick-swap build modules, integrated powder recycling and a central server to manage print jobs, materials, settings, and maintenance.
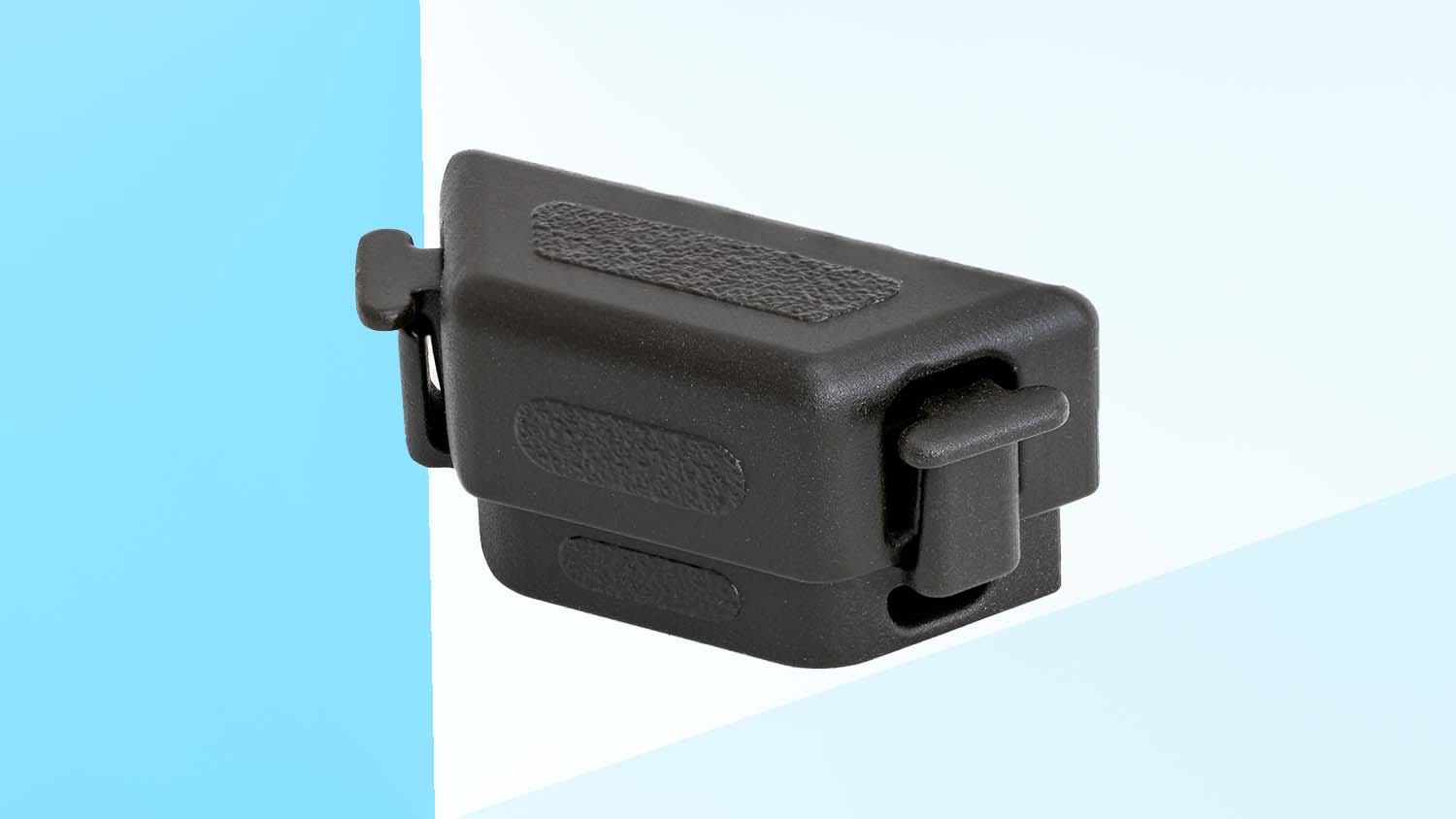
Additionally, the unique vacuum chamber significantly reduces argon gas consumption while maintaining excellent oxygen purity (<30 ppm). The general availability of these printers is anticipated for the first quarter of 2022.
On the materials front, 3D Systems announced Figure 4 Rigid 140C Black, a two-part epoxy/acrylate hybrid material, designed to deliver production-grade parts with long-term mechanical stability in various environments. Made with patented filler, its developers say the material provides toughness compared to injection moulded polybutylene glass fibre (PBT GF).
Figure 4 Rigid 140C Black has a 124°C @1.82MPa HDT which will make it a very attractive for engine bay and internal cabin automotive applications including end-use clips, covers, connectors, housings and fasteners, electrical latching, and board connectors.
At the launch, the Figure 4 Rigid 140C Black was said to have been tested to the equivalent of 8 years indoor and one and a half years in outdoor environments ‘per ASTM D4329 and ASTM G194 methods’. A required three-hour thermal post-cure at 135°C has the benefits of not needing to pack the parts in salt, as is required for other similar materials available on competitive systems.
Additionally, the cure time is said to be approximately 75% shorter than the 8 to 12 hours required for similar materials available on competitive systems.
“We’re excited to be able to meet with our industry colleagues, collaborators, and customers here at Formnext and introduce new product enhancements in our additive manufacturing portfolio,” said 3D Systems additive manufacturing CTO Dr. David Leigh.
“We remain committed to investing in our core technologies that help our customers tackle the toughest production applications. As we approach the end of the year, we’re looking forward to the future with great anticipation and the realisation that we can’t accomplish this by ourselves. We see tremendous opportunities to collaborate with others in the industry to bring together our products and expertise – fundamentally transforming the solutions we provide to help change the world of additive manufacturing.”
Other upgrades include a larger build plate and enhanced laser for the DMP Flex 200, which promises a ‘industry-leading’ surface finish, and accuracy primarily for medical and dental applications.