Those that have been kicking around with rapid prototyping (RP) technologies for a while will be familiar with Laminated Object Manufacturing (LOM).
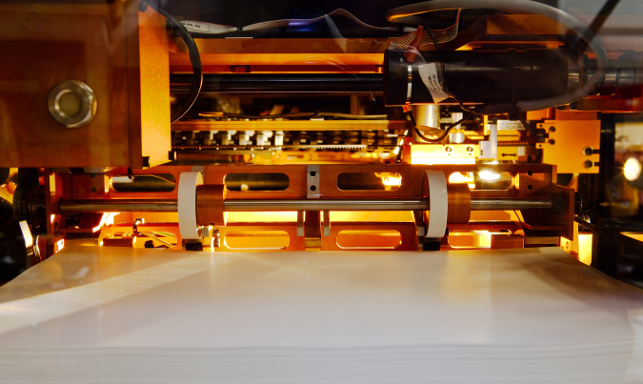
The Matrix 300 in action
Back in the days when stereolithography (SLA) machines were the height of sophistication, the Helisys LOM machines gained ground due to the harder wearing nature of the models they produced.
By combining roller fed sheet material with a laser optic set-up to cut the shape of each layer, the machines could build up a model using paper. The resulting models were much tougher than the brittle and UV sensitive SLA models of the day.
But due to a number of reasons, Helisys went out of business at the turn of the millennium and that rather distinct smell of laser burning paper disappeared from workshops.
So it’s interesting that a decade later, Irish start-up, Mcor Technologies, is bringing back the same core principles, but mixing them with drastically lower cost processing hardware and a different business model.
Mcor’s Matrix 300 has a build volume of 277 (x) x 190 (y) x 150 (z) mm and works in the same way as most RP systems – it builds up a model using layers of material to create a 3D form in slices or layers.
In this instance, the machine is using pretty standard 80 gsm A4 paper. The system loads the first sheet and uses a roller cutter to slice in the form of the first layer. A roller then applies a layer of adhesive, the next layer is added, sliced and the process continues.
The machine builds at a rate of around 5mm an hour, depending on layer complexity, which means around 30 hours for a full volume build.
In comparison to other prototyping systems, layer thickness is around 0.1mm and the resolution is the same (essentially the turn point of the blade).
Due to the enclosing nature of the build process, parts can be stacked in a single build and the SliceIT software will automatically add the break out cuts to assist with the weeding process. This is perhaps the one downside of the system.
With a ZPrinter the finished part is removed from a build cake of unused powder and similarly, a FDM part is removed from its support structures, but with the Mcor process the model is essentially removed from a block of paper.
The cuts in the layers will help speed up removal and so will the adhesive that is only added where needed.
That said, it will still take around an hour to work on a complex part with internal forms. The end result is a good, solid prototype.
While there are some finishing techniques that can be applied, the nature of the process means that the user doesn’t have as many options as with an SLA or sintered part.
The options typically advised include dipping in cyanoacrylate (that’s super glue to you and me), spraying with primer, lacquer, infusing with wax or using any non water-based finishing technique normally applied to wood.
Prototyping as a service
There’s much talk in the product design field of product provision as a service.
When you buy a printer, are you buying a printer or the ability to print something on paper? When you buy a car, are you buying the car or the ability to drive from one point to another? For the production of prototypes this also holds true.
When a company invests in a RP system, it usually means that the need for such items has outstripped the cost of outsourcing that work to a bureau. But that means taking on the costs associated with maintenance, materials and consumables.
Mcor has flipped this on its head. Instead of buying the machine and consumables, the user buys the ability to print prototypes on it.
Essentially, starting at £7,500 per year, MCOR will deliver the machine and all the consumables needed, excluding paper.
Maintenance is, of course, included within the price for the duration of the contract.
Conclusion
The Matrix 300 is a welcome return to a fantastic build process for prototypes. Yes, it doesn’t have the fanciness of an SLA or an Objet machine or the strength of an FDM part but the parts out of this machine are tough and accurate.
They have a heft to them that’s ideal for tossing concept models around a design review. For many, outsourcing prototype building is more about having access to a range of technologies, rather than pure cost and flexibility of an in-house system.
But if you can make good solid use of the output from the Mcor process, then the way that the company has structured its product/service offering is compelling and worth further investigation.
Product | Matrix 300 |
---|---|
Company name | Mcor Technologies |
Price | £7,500 per year |