Vertu luxury mobile phones are designed, engineered and tested virtually before real life testing and skilled assembly all under one roof near Farnborough, UK . Tanya Weaver looks at the tools that have enabled the company to compress its product development cycle
What would be a product designer’s dream brief? How about to make the highest quality product possible utilising the best materials and technology?
This is exactly the brief Hutch Hutchison was handed when he was at Nokia in the late 1990s. He was given carte blanche to work on a project creating the world’s first luxury communications handset, Vertu.
“At the time Nokia was number one and we could get funding for crazy new ideas. So we set off to tackle the high-end. Not necessarily to build luxury phones but better phones. To see what happens when you don’t worry about how much it is going to cost,” remembers Hutchison, Vertu’s head of design.
Having researched and interrogated the luxury sector, with particular early inspiration coming from the watch industry, Hutchison and his team set about designing the first Vertu phone. All the parts would be custom made, even down to the screws that held the phone together.
In 2002 the Vertu Signature was launched. It featured over 400 components including ruby bearings and a sapphire crystal screen. The latter was certainly a key differentiator and Vertu prides itself on pioneering the use of sapphire in the mobile phone market.
Impervious to anything less than diamond, sapphire is strong, highly scratch resistant and optically perfect.
However, it can be brittle and over the years Vertu has worked very closely with its supplier on defining how the sapphire should be cut and polished to improve its strength.
Today, alongside the latest Vertu Signature collection, with a starting price of £9,600, there are two further models. The Signature Touch, a smartphone version of the Signature, was launched in June 2014 and has a starting price of £6,750. Then in October 2014, the more unisex lifestyle smartphone, Aster, was launched with its starting price of £4,200.
Kicking-off product development
The start of the product development process begins with pen and sketchpad. With the Signature Touch the brief was to keep the same design language as the Signature but with five inches of screen to accommodate.
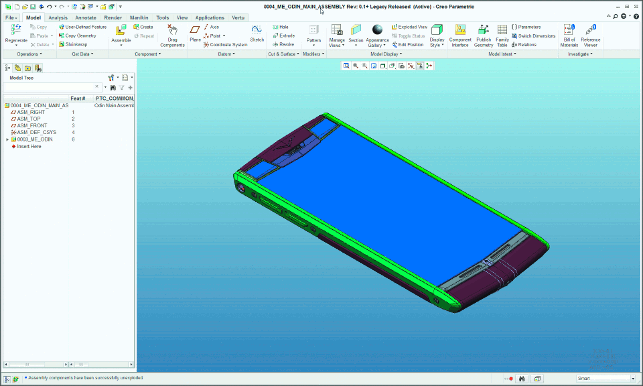
With their initial concepts, the industrial designers will loosely assemble the building blocks of the design in terms of where the different components, such as battery, PCB, SIM card, antennae etc., need to be. “We leave it roughly at that because you can lock things too soon by jumping into engineering mode too quickly and destroying the creativity,” says Hutchison.
From these concepts, the models will be generated in CAD. The industrial design team, having used many CAD systems over the years, have settled on Rhino as it’s easy and light, according to Hutchison.
Rough physical models will be made and shown to the board of directors to get their buy-in into the new design.
The chosen design will then be further enhanced by the designers in Rhino before the model is shared with the mechanical engineering team, who take it into PTC Creo.
However, it’s by no means a case of the designers handing their design over the wall to the engineers, so to speak; it’s a very collaborative process.
“Today, with increasing pressure to compress the product development cycles, no one has the luxury of developing products in a serial fashion anymore,” comments Tim Draper, Vertu’s CAD systems manager.
“The way that our mechanical, hardware, simulation and software teams all work and develop the products is by simultaneously working alongside and in parallel with the industrial designers.”
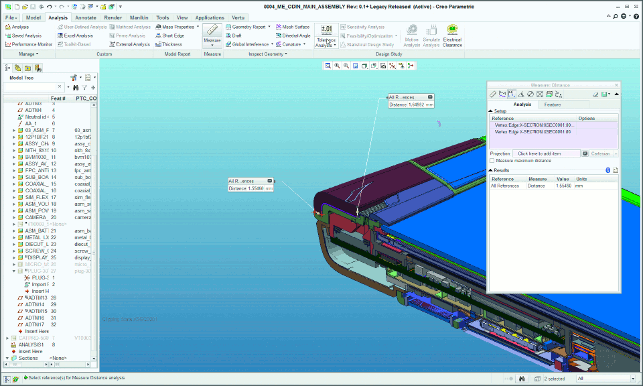
Draper came into the company in 2012, around the time that Vertu became independent from Nokia. His brief was to build an independent CAD and PLM system that would allow Vertu to speed up its product development process.
Draper’s aim was to make Vertu a 3D digital-centric company. So, in July 2013, having reviewed its inherited Catia CAD system from Nokia, Vertu made the decision to go with a software tool from a different vendor – PTC Creo for CAD and PTC Windchill for PLM.
“We did spend some time reviewing the inherited tool before we decided to take a brave step, which was to build something new and we haven’t really looked back since,” adds Draper.
Collaboration partners
A key reason for choosing these PTC tools was that it would not only enable collaboration internally within Vertu but externally with suppliers too.
Building and designing a phone is not exclusively a Vertu process. We have technology partners from across the world that we work with.
“Creo is used extensively in our supply chain and by selecting it we can enable these partners to easily work with our hardware and software teams, using a single digital representation of the design,” states Draper.
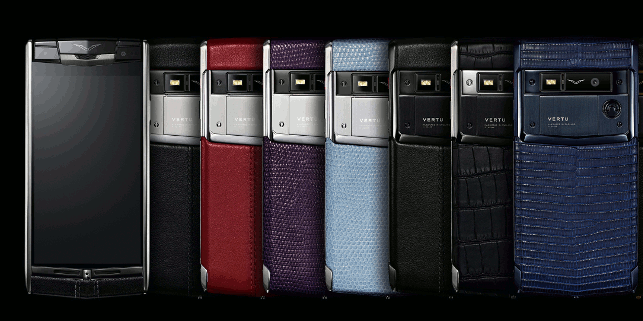
The Signature Touch launched earlier in 2014 comes in a range of finishes and materials, which can be personalised by the customer
To further aid this collaboration, in January 2014 Vertu implemented Windchill. From the previous system of exchanging STEP files on a twice daily basis, now its partners can log into the Windchill PLM system and check in and out models alongside Vertu’s own engineers.
“We have a global team of engineers developing chassis and PCBs as well as external components and mechanical parts, and Windchill allows us to keep it all in sync. Every day we can reassess our designs against new and evolving, best-in-class circuit board designs.
“The introduction of Windchill has really revolutionised the way that we are working in terms of speeding up the process,” says Draper.
Vertu’s top down design process
Draper has also, over the past 12 months, been instigating a ‘top down’ design process where the industrial designers and mechanical engineers can collaborate far easier than before.
A team of surface architects have been busying themselves with building a robust CAD model where the industrial design surfaces can be tweaked without impacting the mechanical design.
“So, if we introduce a change to a surface at the top of the stack, it will cascade back through the stack and update the mechanical parts virtually and in an automatic fashion.
Every mechanical part has seed geometry as the first features in the tree which is driven by the industrial design at the top,” explains Draper.
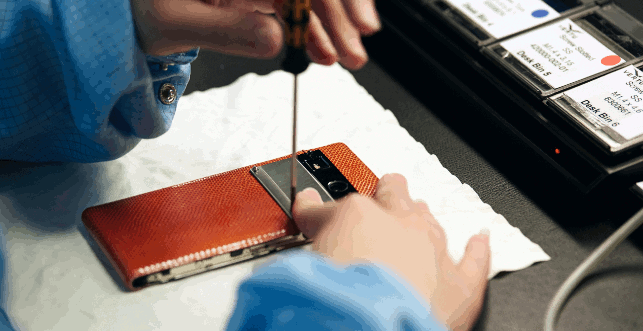
“With this linked up process the industrial designers can continue to make minor tweaks to their designs virtually, up to the point we build our first physical prototypes. So there is a very compressed, overlapped process.”
However, the challenge with designing a mobile phone is that the internal components are all so closely packed inside with half of it being circuit board, the other half battery and then 20 different antennae, all of which hate metal, and of course a SIM card and many other parts too.
“Everything is so close in a phone. It is a big bit of engineering Tetris work to lock all the pieces,” explains Hutchison.
“But it’s wonderful when you have a challenge and have to design a beautiful mechanism to overcome it. For example, in the Vertu Signature the SIM card started life behind the battery and then got chased all the way round the phone.
Eventually we housed it in the top of the phone, and when you pull down on a little lever on the side it popped out as a little surprise”
Test and test again
While this ‘Tetris work’ is taking place, at the earliest stages the simulation team is testing the designs virtually.
For instance, they use finite element analysis (FEA) to simulate mechanical strength as well as simulating RF, antennae and heating performance.
Vertu also recently invested in the CAE simulation software platform, Altair Hyperworks. One of the main simulations the engineers carry out using this tool is an automated 1.5 metre drop test.
From Creo an FEA model of the phone is set up that can be dropped at all angles to test a host of drop orientations and scenarios.
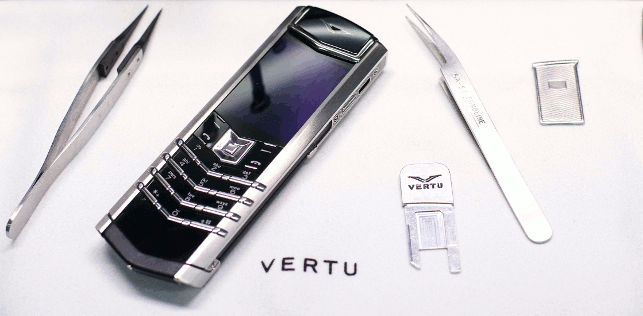
This is then simulated using Altair’s structural analysis solver RADIOSS for highly non-linear problems under dynamic loadings. The simulation runs up in the cloud using HyperWorks Unlimited, a private cloud solution with fully configured hardware and software.
Following the test, a report is run which the simulation team can review with the mechanical engineering team and a decision made as to whether any changes need to be made to the design. Again, this is a very collaborative process between different teams.
“The beauty of these tools is that you can run the simulation, find the problem, solve it and run it again.
Whereas if you are making parts, you have to wait for weeks or months until the parts are back to establish whether you’ve solved the problem. So, in that respect, the power of these tools significantly speeds up the development cycle,” says Neil Hooper, Vertu’s director of R&D and sourcing.
“I have been in this industry 20 years and it’s amazing how much quicker, better and faster we’ve got purely by having access to these tools.”
Quality guaranteed
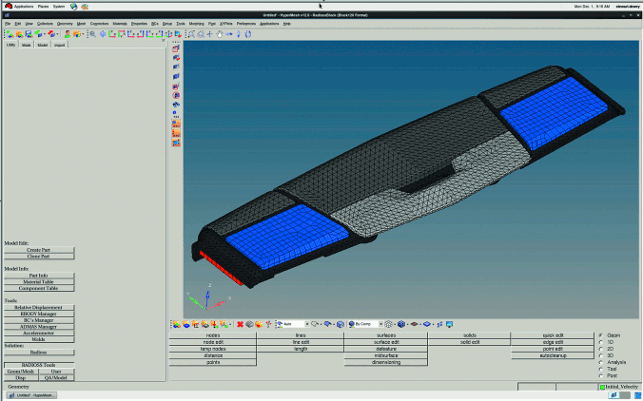
When the phone has been proven digitally, a small batch is built, several of which are then put into a real 1.5 metre drop tower in Vertu’s testing lab where they are dropped multiple times and videoed to see if and how they deform.
The results from both the virtual and physical tests correlate very well which gives the engineers confidence in the accuracy of the simulation.
This is just one of the physical tests that are carried out. There are a further 40, some of which include damp, heat, solar radiation, salt mist, bending, tension, rub and wear. A particularly brutal test is the one metre free fall tumble test where, like a tumble dryer, the phone undergoes repeated free fall with an impact at each end.
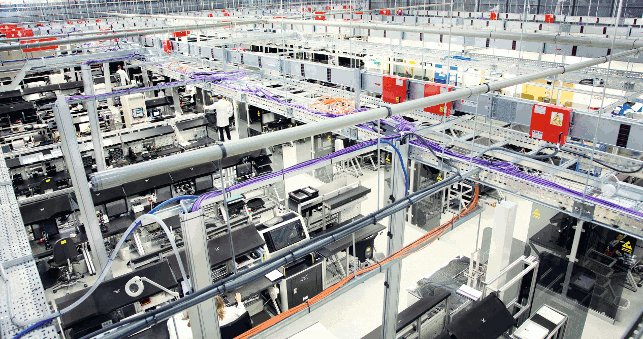
The results of these tests will be fed back to the design and engineering teams, who will tweak the design if need be before a second build is done. The idea is that the phone gets a battering but at the end there won’t be a scuff, dent or crack on the beautifully stitched leather, brushed titanium or sapphire crystal screen.
Once everyone involved in the product development process is 100 per cent happy, the green light is given on production. As there are so many suppliers and technology partners involved, the logistics chain is very complex.
When all the various components are delivered to Vertu’s facility, there is a team of approximately 50 craftsmen in the workshop who assemble the phones by hand. They are referred to as craftsmen as this is a labour intensive process that requires skill and huge attention to detail.
A nice touch is once the phone comes to the end of the build process, the scanned signature of the person who assembled it is lasered into the inside window of the battery housing at the back of the phone.
When the phone arrives to the customer it has been polished to such a degree that it is almost jewel-like and with a quality build that will ensure it will still be pristine for years to come.