The Guild Guitar Company is combining vintage appeal with fresh new design thinking to reach new audiences. We speak to Josh Chapman, Guild’s director of product management, to find out how it gets the balance right
Guitars from The Guild Guitar Company have helped to create some of the greatest music in history. From the New York jazz scene of the 1950s, to Richie Havens’ legendary performance at Woodstock, to the heavy riffing of Seattle’s Kim Thayil of Soundgarden.
Founded in 1953, Oxnard, California-based Guild Guitar Company is still building on its long-standing reputation for creating iconic acoustic, electric and bass guitars. In fact, under the ownership of the Cordoba Music Group, Guild Guitar Company has undergone something of a rebirth.
It still sends vintage designs, built on the principles of craftsmanship, quality and value, to guitar stores around the world. But, at the same time, it has also been developing a new range of products that combine both vintage styling and new features to appeal to a new generation of musicians and instrument owners. As the company’s slogan makes clear, whether the design is new or old, a Guild guitar is “Made to Be Played.”
To learn more about how Guild Guitar Company brings its products to market, we spoke to Josh Chapman, director of product management for Cordoba Music Group.
Chapman’s personal journey reads like something out of a Jules Verne novel. From high school in Kazakhstan, via studying business and guitar design in Minnesota and working for one of the US’s largest instrument retailers on guitar repairs, he’s since risen quickly through the ranks at Guild Guitar Company to where he is today.
“I was initially hired as a finish technician in the factory. There’s 1,000 or more guitars out there that I’ve worked on. After implementing some quality tracking ideas into the factory – using coloured tape in our finishing room, because we didn’t have a good system for marking when a guitar needed touch-ups or was ready – I ended up having a serendipitous meeting that caught the attention of Jon Thomas, our president. He approached me after the meeting, asking about my background and what I wanted to do,” he explains.
“This was my chance to tell him about my background in guitar design and how that’s where I’d rather be, but that I understood I’d need to work in a factory for a year before I could implement any changes or create a design,” he continues.
“As a result, over the next year, I was working partially in the factory and partially on the development team. I came over to the design team as a specialist, but ended up becoming the director of product management, covering all of our brands: Cordoba, as well as Guild Guitar Company, DeArmond pickups and HumiCase cases.”
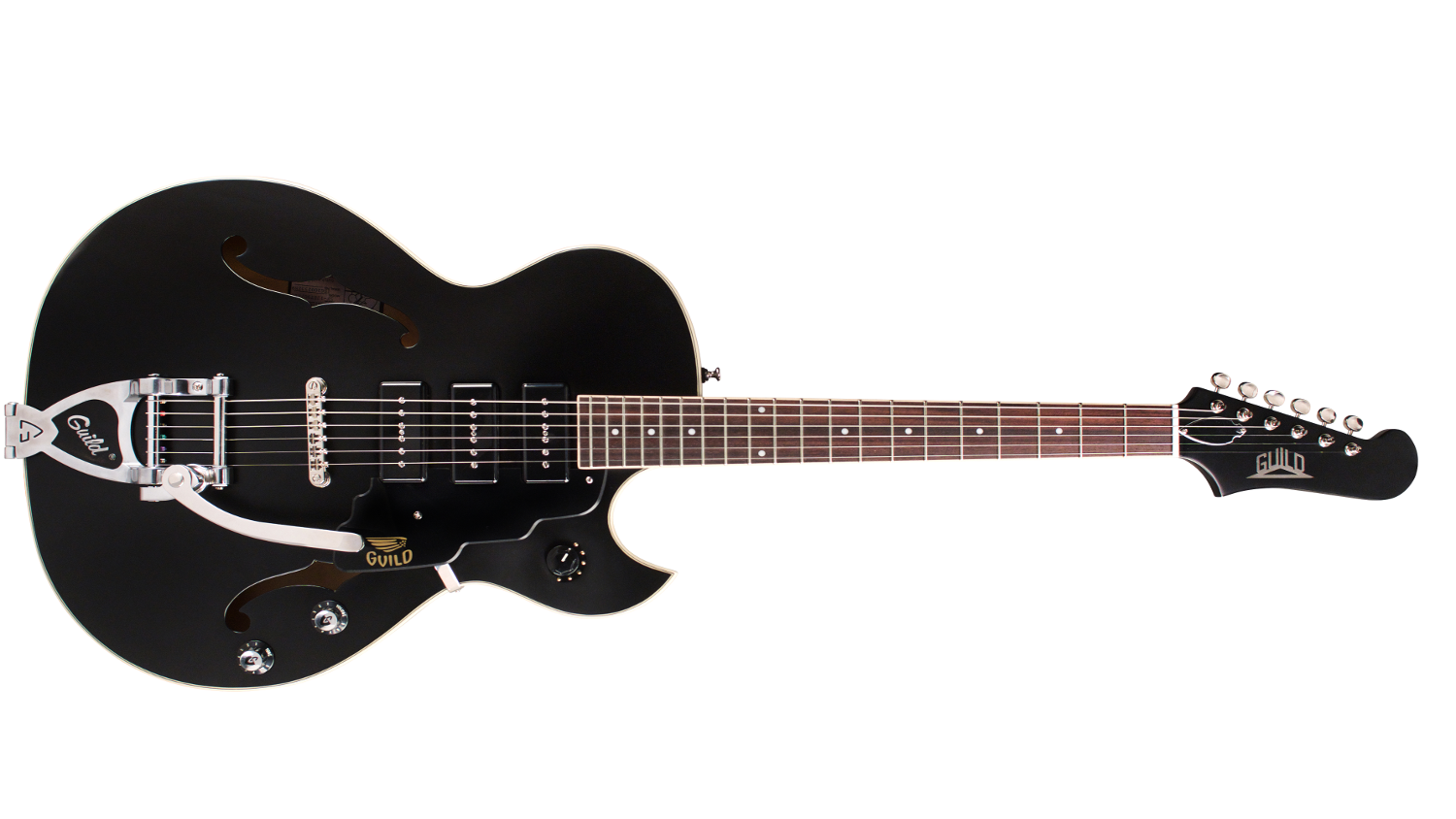
Guild Guitar – classic appeal, clever new tricks
In order to explore how Chapman and his team take a guitar from concept to reality, we focused on the brandnew Starfire 1 Jet 90 – an instrument that combines classic Guild Guitar appeal with some clever new tricks up its sleeve.
As Chapman explains, there are four major aspects to consider when it comes to guitar design. The first is string physics – and this is the easiest part. In other words, you have a string and it vibrates.
In the case of an electric guitar, it vibrates over a pickup and that generates a sound. So, the first thing to consider is angles and ensuring there is enough room for the string to vibrate as you work up the neck. All of this determines how the strings fit and the noise they produce.
The second consideration is playability. This is a word that’s used a lot in the guitar industry and Chapman sees it as an amalgamation of everything a musician thinks about when playing the guitar. Does the shape fit the body? Does it balance on a strap? How does the neck feel in their hand? Can they make a chord?
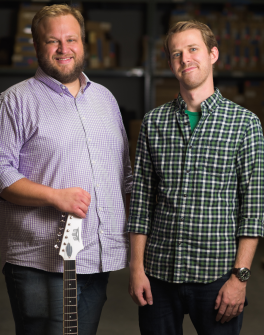
As he puts it: “When we’re drawing that cool shape, does it translate into the physical world and can it be used comfortably?”
The third consideration is tone. With an acoustic guitar, that really means shape, braces and selecting the right wood. With an electric guitar, a lot of the tone comes from the electronics. Anyone engaged in the world of guitars will have heard the term ‘tonewood’, where specific wood varieties are credited with near-mythical tonal properties. Chapman, however, bucks against this school of thought. “I believe that 90% of the tone of an electric guitar comes from the pickups and electronics,” he says.
The fourth and final consideration is controls. Again, the guitar industry has been through conspicuous electronics-led phases in the 1980s and 1990s, from the headless guitars favoured by Reeve Gabriels and the synth-heavy prog rockers to the all-encompassing ‘hair metal’ abominations.
Chapman agrees that controls are key, but within the right context. “You’ll often find that a lot of those controls and switches have never been used by a musician on stage or in the studio, so you’re balancing giving musicians what they want but also giving them only good sounds.”
Guild Guitar – Mixing nostalgia and freshness
According to Chapman, Guild’s design process is one that mixes together modern agile methods of development with Guild’s long-standing expertise and its iconic back catalogue.
“In the grand scheme of things, we work in an agile development manner. We do a lot of runs or sprints, where we come up with a concept or idea for a new product; then we think about the individual components,” he says. “We don’t roll through a step-by-step process. We’re more shooting from the hip and experimenting to solve the things we’re not sure about.”
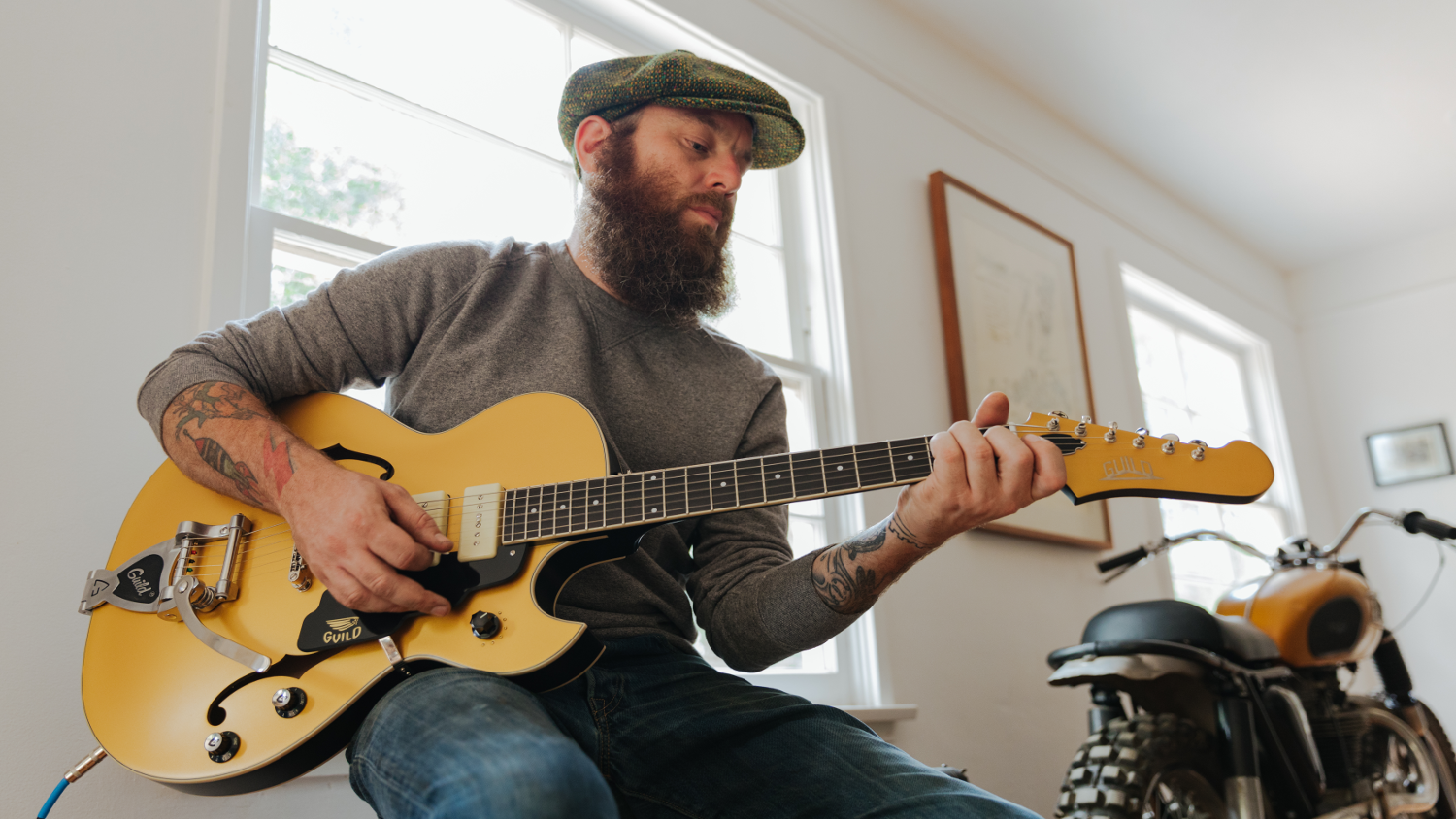
At the same time, the team takes its inspiration from the past, where appropriate. “Much of what we do when developing new products involves picking the vintage designs that work together and finding new inspiration.
“Guild Guitar Company hasn’t had a lot of new models for the last 30 years, and we really wanted to release something that was new, that was fun, and that would bring people to the brand and announce that Guild Guitar Company is back in the game and making instruments. At the same time, we wanted it to look and feel like a Guild guitar,” he says.
“You can see that in the way we paired the headstock with the body. These are two shapes that already existed in Guild. The headstock shape came from an S-50 Jetstar from the 1960s. The Starfire single-cut body shape was also first seen in the 1960s.
“We’re pulling from some very old designs – but we didn’t just match them up because they looked cool. We wanted to make a guitar that used the tremolo and vibrato tailpiece that was aimed at the rockabilly, to produce blues with a tone that someone could really go crazy with and have a lot of fun with.”
A lot of the company’s guitars are more classic, “aimed towards a jazz bar or something like that”, he says. “We wanted to give our younger customers something that was new and exciting, but also offers a different tonality and different style, while clearly still Guild. It’s not just about looks; that six-in-line headstock and the way that the strings come through the nut is going to be a little better when you’re using your vibrato and it won’t disrupt the tuning.”
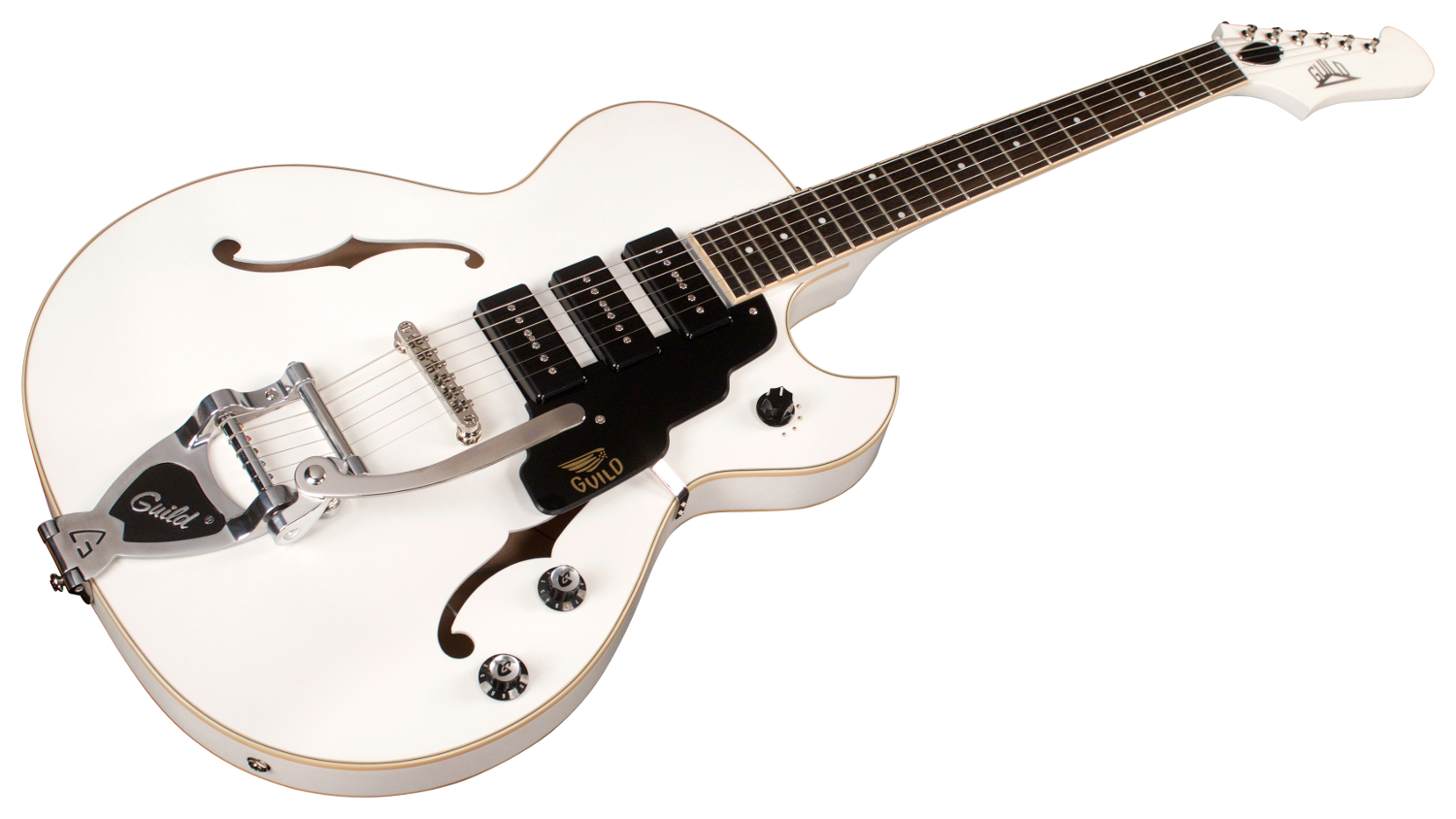
On the way to a final form, the team ran up against some issues, many of which were solved with age-old prototyping methods.
For instance, the Jet 90 features three P90 pickups (which convert the vibration of the string into an electrical signal), which Guild Guitar Company had not tried before. According to Chapman, the team grabbed a guitar in the office and added the same configuration to see how it would work. Other issues, as we’ll see, were only worked out when the guitar moved closer to production.
When it comes to shape development, both for the large iconic parts as well as the hardware details, Chapman is keen that the design team again takes inspiration from the past. “I implore our design team to take curves from our history.
“For example, if I’m working on a pickguard, I’ll open up my CAD files of previous guitar shapes and hardware, and see if I can take curves and lines from those historic pieces and utilise them on that pickguard,” he says.
“That way, it’ll look new to you, but if you were to pick up other pieces and hardware, you’ll see a very homogenous feeling, because we’ve pulled shapes and curves from these vintage pieces and used them on our guitars today, so they blend in. That’s not to say we won’t develop something new, but we will pull inspiration from vintage pieces as much as possible.”
In terms of technology, Chapman and his team use a combination of Rhino3D, Solidworks and DraftSight.
As he told us: “We primarily use Rhinoceros 3D for our design work. Rhino’s NURBS functionality is phenomenal for 3D work, but for initial instrument designs, a lot of our plans are in 2D, much like instrument plans of yesteryear.
“We also use Solidworks, mainly in our US factory, when we are designating drawings for specific tools and tool-paths. DraftSight has also been a great resource for us on the fly and eDrawings Pro has a mobile app which can view CAD files on your smartphone.”
One feature on the Starfire 1 Jet 90 of which Chapman is particularly proud is its rotary switch control. Electric guitars often have three- or five-way switches, but the rotary switch is something that’s typically only found on more esoteric models.
For Chapman, the combination of three pickups and a six-way switch means that his team can give a musician as many good tones as possible, but without overwhelming them.
“Looking at the three pickups, we knew we wanted to give players a stripped-back choice for rock, but we also wanted to give the option of those jazz tones you’re used to in a Guild guitar,” he says.
“There are a lot of switches that are standard in guitars, but they are quite limited for the Jet 90’s set-up. The final choice was a six-position rotary switch which gives the consumer six different tonal choices. One of the really cool things is if you zoom in on the Jet 90, you’ll see vintage pins that you would see on a 1960s Guild electric guitar to mark each position.”
Advertisement
Into production
While Cordoba has built a guitar factory in California, the facilities for US-based production of electric models are still a few years away. So, once a concept has been developed into a final product, the Guild team works with manufacturing partners in either Korea or Indonesia to get it ready for production.
The process begins with the manufacturing partner producing a series of samples, which are then examined in fine detail by Chapman and his team.
“One of the beauties of being in California is that we can go to a lot of the major guitar retailers and get their feedback on that sample,” he says.
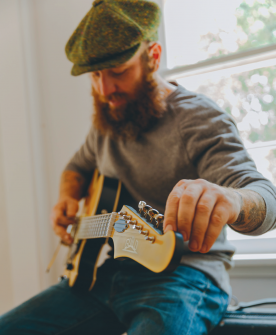
Several sampling rounds might be carried out, not only to finetune the design, but also to ensure that the product can be put into production in a consistent manner.
At the same time, a lot of prototyping and testing is carried out in-house in the US, says Chapman. This includes making pickguards out of plastics and putting them on guitars.
“The same is true of our hardware, such as bridges – anything that will directly interfere with how the instrument plays or sounds, we definitely prototype all of that in our US office,” he adds.
The sampling process can sometimes throw up dramatic design changes – as happened with the Starfire 1 Jet 90. “We wanted to make sure that it had some bite and attitude and could handle higher gain to get that rock distortion sound from a turned-up amplifier,” he says.
“One of the issues with a hollow-body guitar like the Jet 90, is that you’re more prone to feedback, so we added a block into the centre of the guitar. That’s not something that’s new in guitar construction, but it’s new to this body style.”
When the first round of guitar samples arrived, the team loved the product, he says, “but we also noticed that, because it was a clearly hollow body with f-holes and such, the additional block meant it was a lot heavier than your brain expects.”
So on the next round of samples, material was cut from that centre block, preserving the ability to play at high gain, but reducing the weight of the instrument. As Chapman recalls: “It was one of those interesting moments where the guitar itself was ready to go, but we went into a redesign loop and another round of sampling.”
Coda
Chapman’s enthusiasm and pride when it comes to the Starfire 1 Jet 90 come across loud and clear – but what does he have planned for the future? The answer is to keep combining vintage strengths with fresh new thinking.
“Many of our customers have been with us for years. Also, because there haven’t been a lot of new models, and even fewer for less than $1,000 over the past 10 or 20 years, we realised that a lot of our customers are on the older side.
“So, one of the things we are looking at now is how do we get those new players, who walk into a store, pick up a guitar and start playing, to pick one of ours?”
That makes first impressions very important. “We want customers to pick our product, not because it’s a Guild Guitar, but because it’s a good-looking guitar.
“We can’t rely on our legacy and word of mouth; we also have to make instruments that speak for themselves to a new generation, while simultaneously not insulting those who have stuck with our brand for so long.”