Bombing along the country lanes in a Morgan three-wheeler with the air whipping round your face, the rumbling of the engine and the beautiful views of the Malvern Hills in the distance is an experience I won’t forget for a long time.
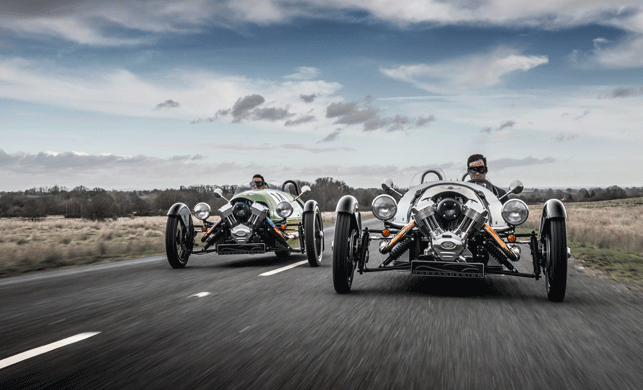
The Morgan three-wheeler was relaunched in 2011 after having stopped production of the original in 1952. Jonathan Wells is behind the wheel of the right car
It may be a nod to the past but with its American v-twin engines, five-speed gearbox and on-board computer system, this is a wholly modern incarnation. The drive certainly left me with a grin from ear to ear that remained for the rest of the day.
Fun is exactly the emotion the Morgan Motor Company is aiming for with its cars. As Charles Morgan, company shareholder and former director, says: “We want every Morgan we build to bring a smile to your face. If we’ve achieved that, then we’ve achieved one of the key elements of our philosophy.”

During the 1920s and 1930s the Morgan three-wheelers enjoyed success on the road and on the race track
It was in fact Charles Morgan’s grandfather Henry F.S. Morgan who in 1909 founded the Morgan Motor Company, which is still a family-owned business today.
He designed a three-wheel vehicle with the simple intention of it being able to transport him up and down the hill to his house. This single-seat machine with its lightweight chassis and body was powered by a motorcycle engine and steered with a tiller.
Having patented his design, in 1914 he moved out of his garage to a factory just round the corner in Pickersleigh Road, where production has remained for the past 100 years.
These Runabouts, as they became known, were very popular as economical cars and were the only output from the factory until 1936 when the Morgan Motor Company diversified into four wheels. The Morgan 4/4 (four wheels, four cylinders), is still produced today and has been bestowed with the title of the world’s longest running series production car.
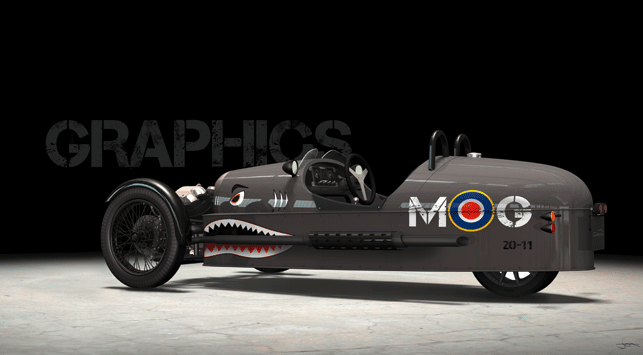
A rendering of the new Morgan three-wheeler
A number of other cars have joined the 4/4 to form the company’s Classic Car range. It also produces a further two ranges: the Aero, which was launched in 2000 when Morgan entered the supercar world, and the three-wheeler, which was re-launched in 2011, the production of the original having stopped in 1952.
Back in time
The factory, which consists of a number of large sheds each dedicated to a different part of the production process, is described by one of the shop floor workers, who has been there for 53 years, as stepping into a time capsule. The reason being that all Morgan cars are built by hand in aluminium, wood and leather using very traditional techniques and tools.
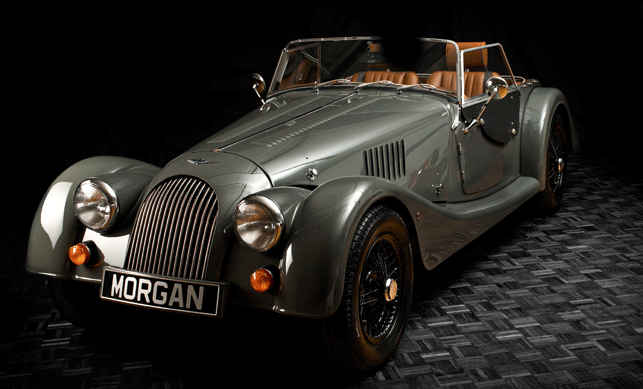
Launched in 1936 the Morgan 4-4 has been in production ever since
However, it’s a different story in the design office and it’s here where Morgan’s reputation for ‘craftsmanship meets technology’ is evident.
The designers and engineers use a combination of 3D design tools including Dassault Systèmes’ CATIA and the Autodesk Design Suite, which encompasses Alias, Showcase and 3D Studio Max (3DS Max). All these tools run on HP Z Workstations with NVIDIA graphics cards.
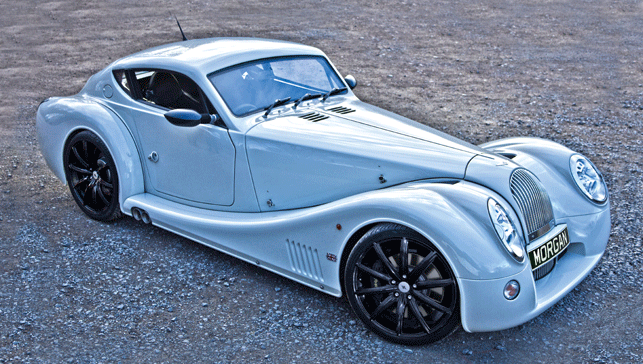
In the supercar range is the Morgan Aero Coupe
However, Autodesk was only introduced into the company seven years ago when Morgan’s current head of design, Jonathan Wells, started.
“My foot in the door was being able to introduce digital design and modern rendering capability and skills into the upfront design process,” he explains.
“It was essentially about bridging the gap between the sketch work and the engineering side of things.”
Before and after
Prior to Alias, concept and prototype cars would involve the craftsmen bending wood and panel beating metal from the designer’s sketches. This was the case with the Morgan AeroMax, which took a long time to build with very little scope for reworking the form with speed.
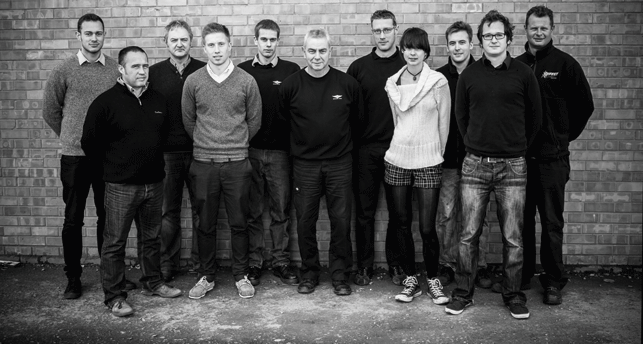
Morgan’s design and development department consists of just 11 people
However, when the prototype was eventually launched at the Geneva Motor Show 2008 it was very well received. In a matter of weeks all 100 of these £110,000 limited edition cars were sold. Although the deposits helped to fund the tooling, a problem soon became evident.
“Due to the nature of how it was built, the lines seemed to drop off a little too quickly and some of the curves and highlights weren’t as sharp as they could be. There was also quite a lot of visual weight underneath the rear of the car and these areas needed timely readjustment before launch, in turn delaying production,” comments Wells.
This experience proved that Morgan needed to link the initial sketch work to the final production of the car to ensure greater first attempt accuracy. It would also in turn result in the cars going into production quicker.
The new three-wheeler
One case study that proves how digital technology has helped speed up the process is that of the new three wheeler, which took just 18 months from initial sketch to production. This vehicle was designed from the ground up and all on screen.
Production of the original three-wheeler ceased over 60 years ago and for predominantly nostalgic reasons the company decided to launch a modern interpretation for its centenary.
The process kicked off with brainstorming ideas and creating mood boards with inspiration coming from classic aviation and motorcycles.
The whole design and development department is involved in this stage. Consisting of just eleven people, they work together as a team on all aspects of the car from aesthetic and mechanical design to CAD, homologation, electronics, managing ongoing production issues as well as creating the branding and marketing materials.
This means that individual members are not working in silos but very much involved in each stage of a project from concept to production and launch. This not only helps to speed up the process but means that, with the designers and engineers working side by side, they can establish very early on what can and can’t work.
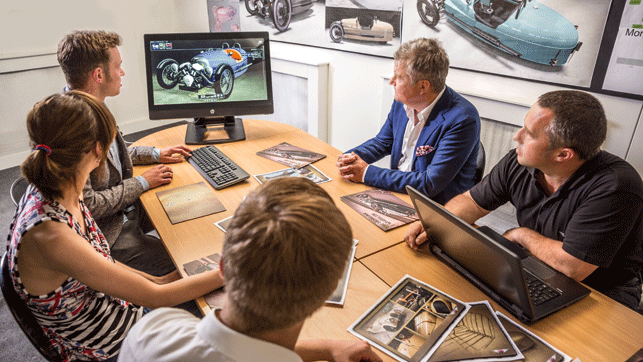
“We can get a real idea of what this car is going to look like before we’ve even spent a penny on a physical tool” – Jon Wells, head of design
“This is something that is very important right from the start especially with the three-wheeler where, much like a motorcycle, the mechanical parts of the car are as important to the overall look as the bodywork is.
“So straight away we are specifying the engine, the wheels and suspension and working alongside the engineers whilst also considering things like ergonomics and how people will get into and out of the car,” says Wells.
From the pen and paper sketches, a basic package is then created in Alias that includes the form and proportion of the tubular steel chassis. From here the surfaces are created working out what the reflections are and how light casts over the surface of the car.
This data is shared with the engineers who bring it into CATIA to manipulate and engineer the surface data. Once complete, the file is then brought back into Alias.
From virtual to physical
With everyone happy with the form on screen, a full-scale styrofoam model was machined directly from the Alias data. The reason for a physical model was to take it to the craftsmen responsible for surfacing in the paint shop and use their expertise to ensure that the continuity of the surfaces was perfect.
“What we actually found was that the surfaces we created were too good – essentially the car had such tangency, such continuity in the curves that it didn’t appear to end at the tail – it looked like it continued and there wasn’t a back to the car as such.
“So in the paint shop we surfaced this car by hand pinching it at the end and making it look a little more defined. Using a 3D scanner, we scanned the model and opened that data straight back into Alias and quickly adjusted those curves,” explains Wells.
Using Alias’ inherent evaluation tools, the aerodynamic performance of the virtual model was then tested by simulating wind and airflow as well as lift and drag.
Three wheeler interior
When it came to designing the interior of the car, the aviation inspiration is evident in the aircraft-style cockpit with switch gear and dials that appear to be bolted on. Interestingly, the start button in the centre of the dash, which fires up the two litre engine, is a bomb release button from a Euro Fighter.
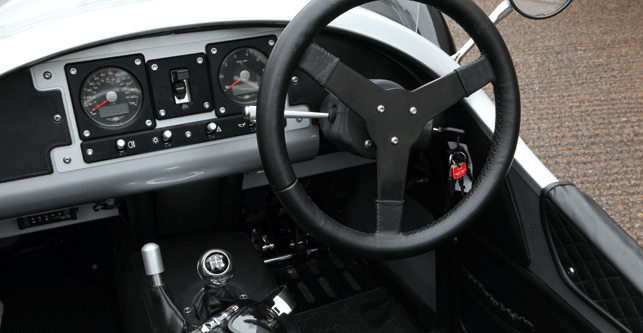
The three-wheeler’s aviation-style cockpit with the Euro Fighter bomb release start button in the centre of the dash
“The same switch company that makes switches for the military also make switches for automotive and they came in with literally two boxes – a black one for automotive and a green and yellow ‘danger’ one for the military switches and we said that it has got to be that one,” smiles Wells.
With the Alias model now complete it is introduced into Showcase, Autodesk’s presentation software within 3DS Max, to present it to the company directors. A Z1 HP workstation with its NVIDIA Quadro graphics card is placed on a table with everyone gathered around it. The 3D model can be spun around showing the three-wheeler from all angles and also the different paint and leather colour combinations that are possible. This helps immerse everyone in the project, giving them a good understanding of the proposed design.
“We can get a real idea of what this car is going to look like before we’ve even spent a penny on a physical tool, which is very nice for our directors because they are able to sign off with great confidence before we actually go into production,” says Wells.
At this stage the physical prototype was far from ready however, Morgan Motors wanted to promote the vehicle ahead of its official launch at the Geneva Motor Show 2011. So, the high definition renderings created in Showcase were used for the promotional as well as point of sale (POS) materials.
With the Geneva Motor Show looming, it was all hands on deck especially as the factory were also producing the show stand, which had been designed and simulated on screen too. “We did a 48-hour stint before the motor show with fish and chips and Red Bull and we assembled the two cars for the motor show ourselves,” says Wells.
Fast turnaround
So, from initial sketch to a physical production vehicle in just 18 months was a great achievement, especially taking into account how well it was received by the automotive press and visitors, some of whom were putting down deposits there and then.
“When you consider that most companies will spend five or six years developing a new car, you see that the three-wheeler is testament not only to how well our team works together but also to how HP and Autodesk technology gives us the ability to visualise, test, evaluate and produce a vehicle quickly,” says Wells.
The three-wheeler proved so popular that it had a 12-month waiting list and production in the factory was increased by an extra hundred cars the following year to reach the demand. Morgan recently announced that the 1000th three-wheeler has rolled off the production line.
At this year’s Geneva Motor Show, the new 2014 version of the three-wheeler was launched with a raft of new improvements. To accompany it on the stand Morgan also showcased a new POS solution – a car configurator that includes all the information from the VRED file, Autodesk 3D visualisation software. Mike Russell, Autodesk technical account manager – Automotive & Transportation NE, was on hand running the configurator on four big screens from a HP laptop.
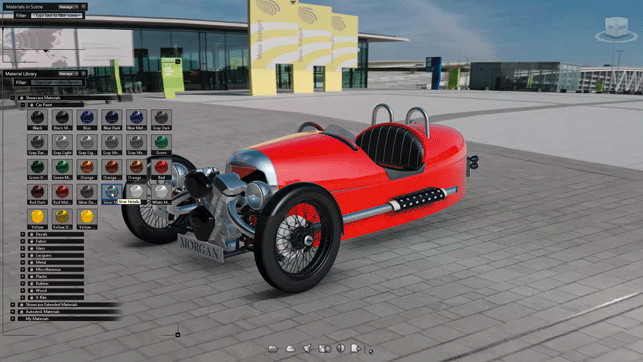
The Autodesk car configurator enables users to select paint and leather options from a wide palette
Visitors were able to tailor a three-wheeler through a wide range of paint and leather combinations. They could also select the environment that the car is in whether it’s a white studio or out on the road to reveal the real-life reflections. And they could even view it at night time to see what the car looks like in the dark with its lights on.
“I joke with Jon Wells but they did have the most advanced car configurator in the whole of the Geneva Motor Show,” says Russell. “So although Morgan has been around for so many years and has a very traditional way of building its cars, it’s about how they merge this great classic feel with modern technology and utilise it to give the customers the experiences they want.”
The hope is to roll out this configurator as part of Morgan’s dealer network and possibly on the websites too. This means that customers can tailor their car on screen and then, if they wish, visit the factory to watch it being built and meet the craftsmen who’ve brought it to life.
So, with a 100 years behind it, Morgan is looking ahead to the next 100. And no doubt it will be producing cars that are fun – not just to design but to drive.
morgan-motor.co.uk
autodesk.com
hp.com | nvidia.com
The Morgan Motor Company has an on-site museum for visitors. Its factory is also open during the week for guided tours (£12.50 per person) and a Morgan can even be taken out on loan.
Workstations
The Morgan Motor Company standardises on HP Z Workstations running the Autodesk Product Design Suite.
At the start of the design process, a 2D sketch soon becomes a digital model manipulated in Alias by designers using HP Z420 Workstations. With a NVIDIA Quadro K4000 graphics card, they are able to design and render in real time, without impacting workflow.
Later on in the process, the Alias data is used to produce a clay or styrofoam scale model of the car. Once the surfaces have been worked on by hand, this physical model is scanned back into Alias using a 3D scanner that is driven by a HP ZBook Mobile Workstation.
“Scanning is very technical and the amount of data which is pushed through is tremendous so you need the hardware to support that and that’s where the ZBook Mobile Workstations really come into their own,” says Graham Chapman, Morgan Motor Company’s director of engineering.
In design review meetings, and to gain approval from the board of directors, an accurate 3D representation of the proposed design is shown using Autodesk Showcase on HP Z1 Workstations.
It’s also important for the design team to portray their ideas accurately to the craftsmen and women on the shop floor who will actually be building the cars. “We’ve got a series of ZBook Mobile Workstations that we take out, and they can spin around the Showcase models or the engineering models in Alias, and we can demonstrate exactly how the car has been assembled virtually.
“They can focus in on certain areas, and we can detail and measure and explore in real time with them. I think for them, having that level of technology accessible has made a big impact on their understanding of the products we’re developing too,” says Jonathan Wells, head of design.
Hand built in the UK
The Morgan Motor Company hand builds its motor cars. Although some components, like the superformed body panels, may be made using sophisticated technologies, the cars are assembled by hand.
Some other UK companies using traditional methods of manufacture include:
Pashley Bicycles
Moulton Bicycles
Purdey guns and rifles
The Great British Banjo Company
The Hiut Denim Company
Simpsons Shaving Brushes
Factory and manufacture
The Morgan Motor Company factory is based in Pickersleigh Road in Great Malvern, where it has been for the past 100 years. Over 170 craftsmen and women work in this factory producing in excess of 1,200 cars a year. Morgan has also instigated an apprenticeship scheme whereby young people can learn the skills from those who have been at Morgan for many years, some more than 50.
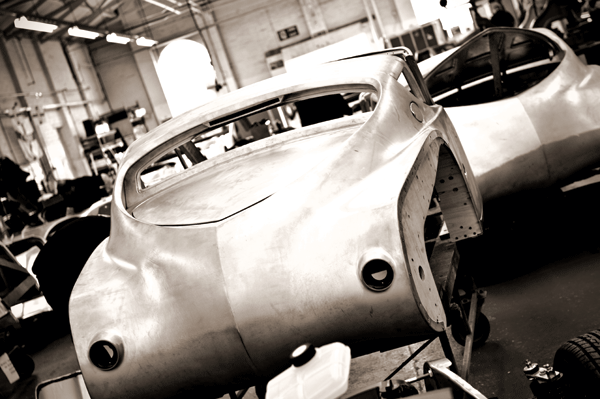
All Morgan cars are coach built by hand using a combination of wood, aluminium and leather. Essentially, an ash wooden body frame lies as a buffer between the chassis and aluminium body.
The factory consists of a series of large sheds with a Morgan car starting its life at the top in the chassis shop. Each chassis is assembled by hand whether it is the aluminium bonded and riveted Aero platform, which consists of state-of-the-art superformed body panels, the Classic galvanised steel ladder chassis or the tubular frame of the three wheeler.
Next is the assembly shop where the body tubs get amalgamated onto the chassis.
Then it’s the tin shop where the aluminium body parts are put onto the frame. There is very little machinery in here just hammers, dollies and rollers, one of which dates back to the 1920s. Amazingly, there are no tape measures either as all work is done by eye and experience.
Then it’s into the woodshop. Firstly, the wood pieces are cut out from templates (94 pieces in a two seater and 120 in a four seater) and then a vacuum bagging process is used to clamp the wood together. There is no steam bending here, it’s all done via wooden jigs using pressure.
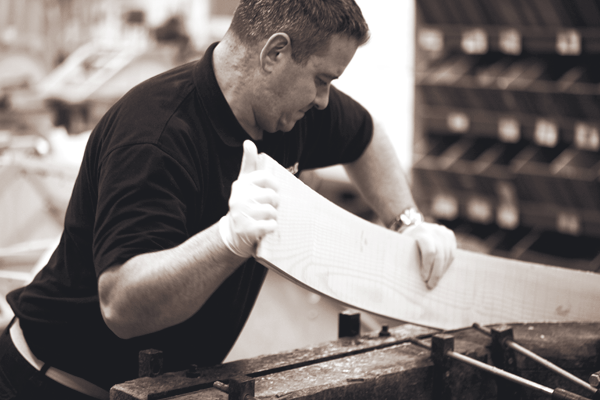
The paint shop is followed by the trim shop, where the car is tailored to what the customer wants in terms of colour and leather options.
With the three-wheeler having been so popular, it now has its own separate shed dedicated to its production.
Today 75 per cent of Morgan cars are exported with Europe being the biggest market. However, with dealerships opened in Taipei and Beijing in the past year, those markets are expected to grow too.
The Morgan Motor Company – 100 years of engineering excellence
Default