Just a cotton-pickin’ minute
John Deere with its green and yellow livery is one of the most recognisable brands amongst farmers and its leaping deer motif patrols fields across the world.
A specialist machine is needed for the process of cotton harvesting, in which the company has been at the forefront for the last 60 years. To enable the most efficient way of harvesting from the giant cotton fields John Deere’s design team has produced the 7760 Cotton Picker, a machine that can harvest non-stop, providing on-the-go packaging of seed cotton as it moves.
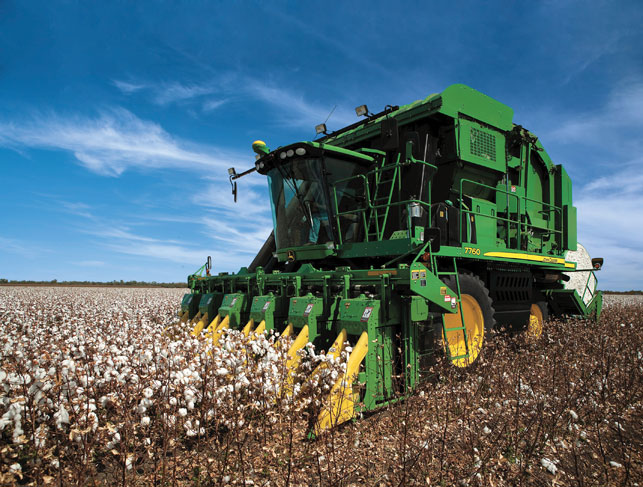
John Deere’s 7760 Cotton Picker can harvest non-stop, providing on-the-go packaging of seed cotton wrapped in a special plastic
The picked cotton is automatically wrapped in a special plastic, forming a secure, round bale, which then drops onto a rear handler shelf that can lower the bale to the ground at the end of the row. Throughout this process the driver need not stop and can continue to harvest more cotton.
Having spent time testing multiple concepts to find what shape of bale and mechanism would be best suited to the harvesting process, David Winter, the global manager of John Deere’s cotton engineering sector, relied heavily on 3D design tools to develop the final design.
“All components of the machine are created in a virtual environment using the 3D modelling software Pro/Engineer,” says David. “These models feed downstream tools to analyse the design and make improvements before actual parts are made.
“For example, the model geometry is imported into a finite element analysis tool to help determine if the part, or parts in question, will meet the rigorous demands of the final product. Manufacturing also uses the 3D models to perform virtual builds, helping them define assembly methods and the production line configuration well before a build begins.”
One of the biggest challenges faced by John Deere was designing the cotton picker for two specific groups of users that would transform the way the cotton harvesting workflow operates. The design not only had to meet the requirements of the cotton farmer, but also the those of the downstream user of the new ‘packaged’ cotton, the cotton ginners, who process the raw cotton by removing the seeds from the useful fibres. Through careful consultation with both sets of users the final result is a product that saves time and lowers waste for all involved in the industry.
Blades of glory
Agricultural mowers are tough pieces of kit, far more so than the Flymos used for preening the garden, but even they can have difficulties when the land gets steep.
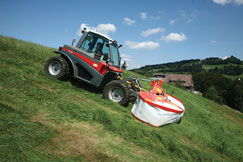
The GMD Compact mower is optimised to work in hills and mountains while being light enough to be operated by small or low powered tractors
A new range of front disc mowers from Kuhn have been designed to tackle this problem. The result is the GMD Compact which is optimised to work in hills and mountains while being light enough to be operated by small or low powered tractors.
The mowing unit adapts to ground contours through its central pivot point. The ground pressure adjustment is made directly from the tractor for those equipped with an integrated front lift suspension or using powerful springs.
The design of the cutting discs means there is no area where two discs rotate simultaneously frontwards, allowing forage to be moved more efficiently to the rear.
One of the main concerns with the design was to keep the weight low without sacrificing the reliability of the machine and this was considered throughout the design process. Keeping the weight below 600kg the team aimed to give the machine the lowest possible overhang to allow it to mow grass on steep slopes.
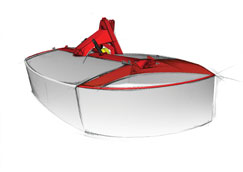
Concept sketches wanted to give the GMD a ‘sporty’ effect
“For the computer assisted conception we use Pro/Engineer software and its different attached modules, which enabled us to make structure resistance calculations, kinematics simulations as well as realistic pictures of the machine,” says design engineer Gilles Fischbach.
Away from the practicalities of such equipment, Kuhn aimed to give the piece of equipment an innovative style of its own, contrasting with the majority of the Kuhn range of machinery. “The scope was to obtain a somehow ‘sporty’ look, with dynamic and harmonious lines,” says Gilles.
The end product is both small and manoeuvrable, but tough and designed with purpose for the ever-expanding reach of modern farmland.
I’ve got a brand new combine harvester…
The infamous song of West Country bumpkins and their preferred choice of agricultural machinery failed to mention exactly what these machines are capable of doing – it must have been the cider.
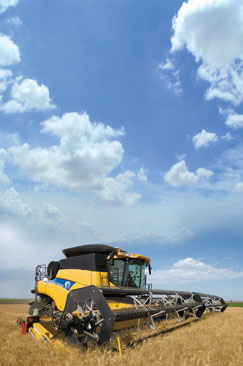
New Holland’s CR9090, a beast of a combine harvester, holds the world record for harvesting: 551.6 tons of wheat in eight hours. That equates to, er, quite a few loaves of bread
The CR9000 Series is the giant of New Holland’s combine harvester family, with particular attention devoted to capacity, operator comfort, grain and straw quality, and residue management.
The technically advanced rotary model was launched last year with a series of unique features, much to the delight of farmers across the globe. An electronic stone detection and ejection system stops any unwanted stones entering the straw elevator; a Twin Rotor threshing and separation system ensures high capacity and gentle handling of grain and straw; a camera system measures the concentration of chaff and the amount of broken grain in the grain sample and the CR9000 also has one of the largest and quietest operator’s cabs available.
Designed primarily in Pro/E, the giant machine underwent substantial model testing before anything was built. Pro/Mechanica was used for force simulations and FEA and CFD for respectively assessing strength and air flow in the cleaning systems. The design team also uses in-house software to calculate drive lines and variators needed to ensure the machine can handle all worldwide crop variations.
New Holland run its designs through its very own virtual reality room DMU (Digital Mock Up) linked with Pro/E to verify any build interferences. This became key when packaging the sub modules into one assembly, ensuring access and serviceability is available for all the required components.
Soon after being set loose on the world’s crops the flagship model, the CR9090, set a world record for harvesting: 551.6 tons of wheat in eight hours. This astonishing feat was achieved in the UK in September 2008, and it is still unbeaten.
www.newholland.com
Harvesting gets high-tech with new agricultural machinery