Askja Audio overcomes limitations of traditional manufacturing for its ‘haute couture’ Origin sound system. Stephen Holmes hears how Stratasys additive manufacturing brought this visual and auditory creation to life
An established figure in the French audio-visual industry, Didier Kwak has worked with some of the biggest movie producers – most recognisably in his visual effects work on the film The Fifth Element.
Having felt that the quality of acoustic technologies available to him did not meet the standards he could achieve in his visual work, he decided to embark on a mission to design and create an ultra-high-end sound system.
“For me, the level of audio quality has drastically decreased since the 1970s with the use of cheaper materials by audio system manufacturers and the rise of digital music streaming services largely to blame,” he explains.
“For years, manufacturers have developed increasingly powerful devices whilst using substandard materials and, as a consequence, the output does not meet quality expectations.”
This inspired Kwak to build his own personal audio systems, culminating with the founding of Askja Audio in 2014, and most recently the launch of Origin – a system that looks to blend perfect sound with ‘haute couture’ design.
With the support of Swiss Fibertec, a company with expertise in designing carbon fibre and composite moulds, Kwak designed the audio system to achieve the ultimate sound aerodynamics.
The complex design of the Askja Audio system includes an amplifier with multiple organic curves, which immediately stood out as a challenge for the project design engineers as to how it could be manufactured.
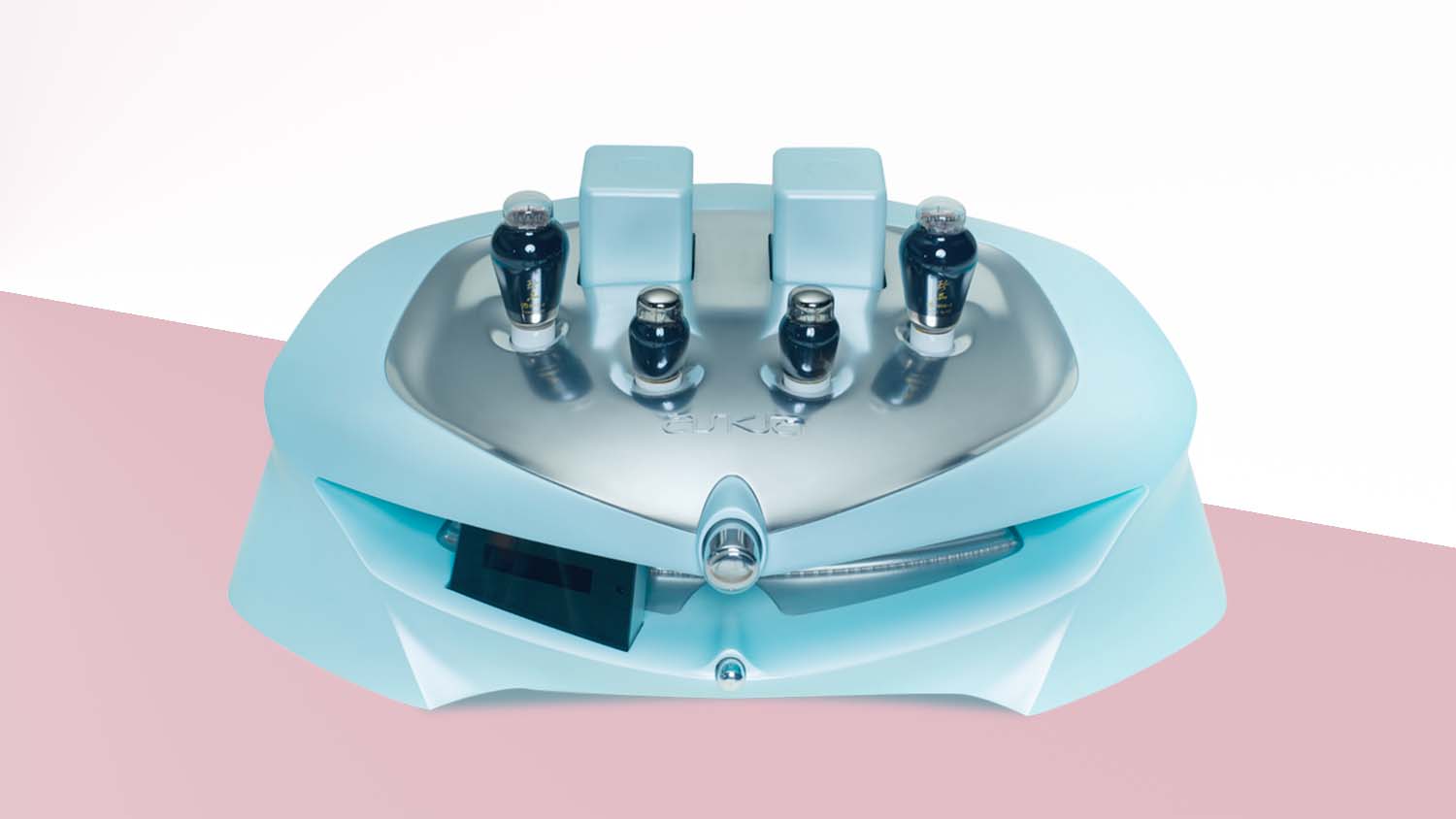
Production in several parts would result in an assembly with obvious joints, negatively impacting both the look and the vibratory continuity vital to achieving a perfect sound.
“We initially considered moulding the only viable solution to produce the hybrid amplifier, but at 800 x 650 x 270mm, the part was too complex to be removed from the mould,” explains Kwak.
“After some research, we realised that Stratasys FDM additive manufacturing offered us the ability to produce any complicated shape with no geometric limitation. This capability proved to be the cornerstone to realising the design and production of our hybrid amplifier, filters and power supply unit.”
Given the size of the Stratasys F900 3D printer’s build area, Askja was able to 3D print the large parts without constraint, even adding modifications to the design to allow for more complex part assemblies that consolidated a number of parts.
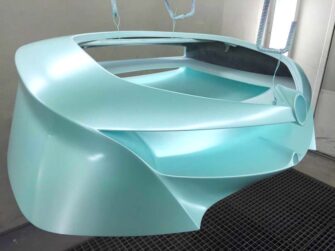
Offering strong rigidity, ULTEM 9085 material was used to reduce any unwanted resonances and vibrations in the amplifier. ASA, which behaves like ABS, was used to balance between stiffness and handling at the system’s core.
The massively reduced lead times also made it possible for Askja to be more experimental at the design phase – testing concepts and making any necessary iterations to optimise the final designs.
Additionally, it allowed for bespoke elements, such as ridges on top of the power supply unit for the addition of ‘skins’ made from materials such as leather – without affecting the efficiency of the sound system.
“The unique quality of our audio system ranks Askja within the luxury goods category, but the use of additive manufacturing to permit clients to customise their own design is a tremendous asset,” says Kwak.
Askja is already facing requests from clients to add diamonds all around the surface of the hybrid amplifier, which Kwak calmly states is easily customisable through 3D printing, making this extraordinary audio system even more unique.