Vlaze – Hard-wearing enamel has found a new home in a range of designer garden furniture that adds even more colour to the summer months. Stephen Holmes speaks to the team at AJ Wells & Sons about the company’s bright new direction
With its extensive knowledge of the vitreous enamel process, AJ Wells & Sons has been designing and manufacturing beautifully finished products for over 50 years. It has made signage that guides millions of passengers each year on the Paris Metro and the London Underground, including the newly opened Elizabeth Line. It also works on large architectural cladding and interiors projects for designers such as Thomas Heatherwick and Tom Dixon.
The company continues to explore new directions for its enamel finishes and extensive metalworking skills to introduce new products. Vitreous enamel is an incredibly durable, weatherproof and unique finish, and with that in mind, the team looked into developing a range of outdoor home products.
Following market research, the team focused on developing mobile kitchen units, perfect for entertaining guests, preparing meals and lending gardens an amazing pop of colour.
After initial discussions, the development team began to sketch out concepts for its Vlaze Adapt range. “It’s a quick way to explore alternative build methods and refine the overall concepts,” says Vlaze creative director Cedric Wells.
“Once the basic ideas are formed, then block models are developed in Solidworks and renders using Keyshot. These ideas are then presented to the directors of the company to discuss the alternative ways the products can be progressed to the prototype stage.”
One Adapt design uses a reverse angle on the outer panels, nicknamed the ‘shark nose’ by Wells, to make the appearance lighter and more interesting, combining with the pop of bright-coloured enamel, giving it more character and a more unique form.
Further detail modelling was then carried out and parts developed. Designing products that would need to operate on uneven ground proved to be a challenge. The solution was a range that can be fitted with a choice of feet or castors to aid movement around different surfaces and gradients of an outdoor space.
With the 3D design finalised, the process moved back into 2D using Bystronic Bysoft CAD/CAM software to draw and nest the panels for cutting on AJ Wells & Sons’ laser system and folded on its programmable press brakes for prototyping.
Wells says that the first physical prototypes generally highlight opportunities to improve the design both in production and also introduce improvements for the end user. Through the process, the dimensions of the structure and strength of the finished product was refined, while also allowing the different processes such as welding and folding to be finetuned for volume manufacturing.
While the interior structure is made from a corrosionresistant grade of stainless steel that can weather the elements and is easy to keep clean, the exterior panels are coated with the vitreous enamel finish for which AJ Wells & Sons is famous.
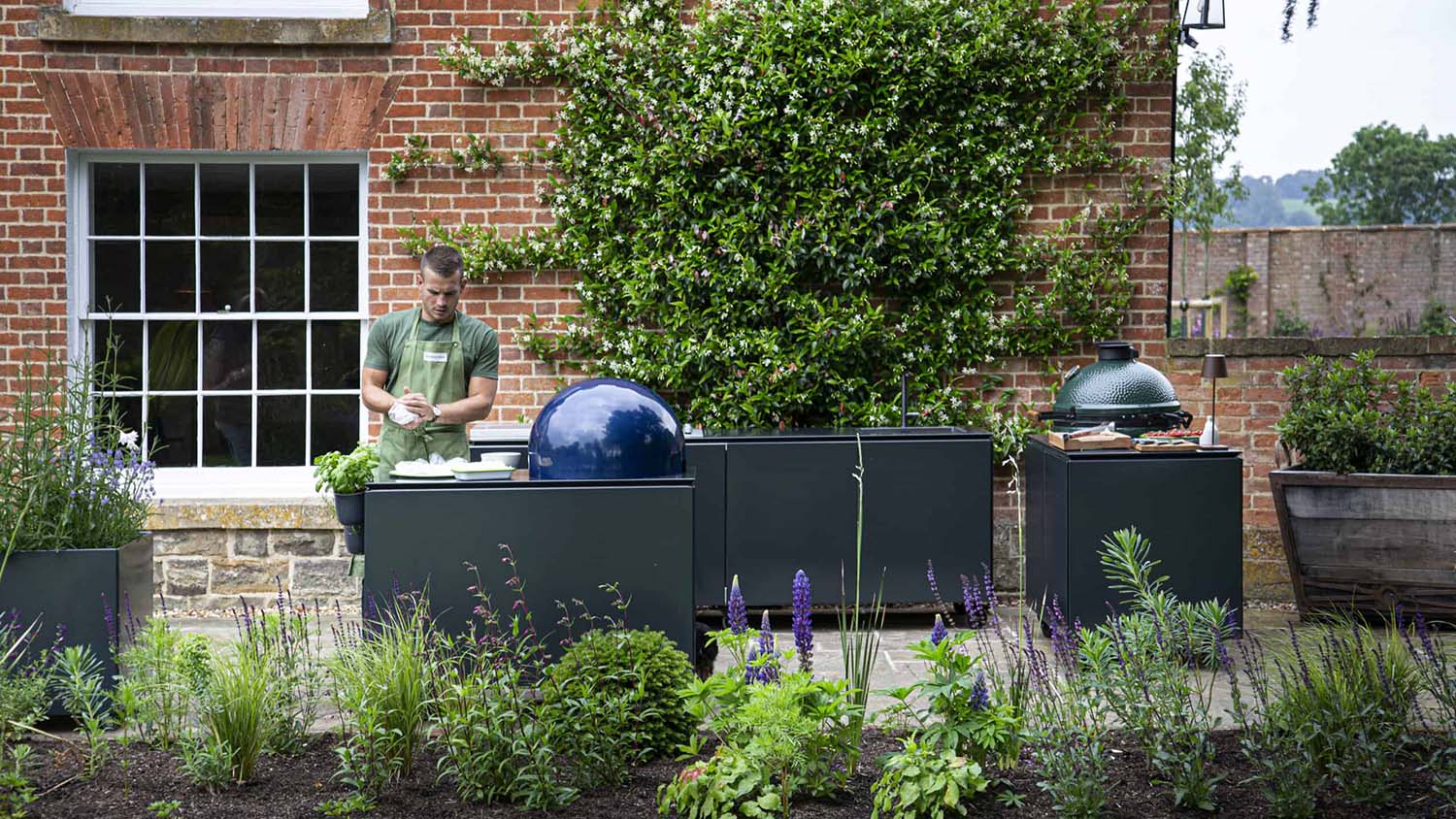
The enamel coating provides a hard-wearing surface that can stand up to the elements and won’t fade in bright sunlight. Being heatproof and hygienic, it’s perfect for cooking and preparing food.
The nature of applying the enamel means the surfaces can be decorated with a textured or printed finish, and each piece can be customised to a different user’s taste or to complement their existing outdoor furniture.
The first Vlaze prototype was built in late 2019. Since then, demand for home improvement has rapidly increased following the pandemic and the Vlaze range has expanded to take advantage of that shift.
A range of different sizes is now available, while the fitting of various grills, sinks and fridges has resulted in the introduction of multiple options and offshoots. With the outdoor range now stretching to planters and fire pits, the company has its feet well and truly under the table.