Almost all vendors are introducing topology optimisation tools in their latest releases. Driven by and heavily linked to the metal additive world, Al Dean wonders whether these tools are being marketed in the right way
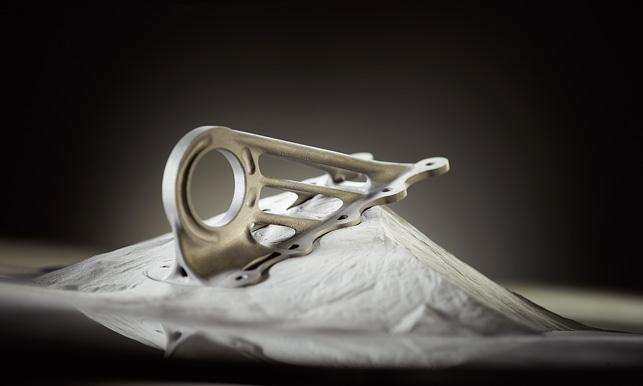
This titanium bracket is 30 percent lighter than its conventionally manufactured predecessor. With a little redesign, it could have been machined and offer similar weight savings at a lower cost Image Credit: Airbus
If I think back over the last year or so, one key trend has emerged from the 3D design and CAD industry: the whole market has gone bat-shit crazy for topology optimisation. From my vague recollections, in recent releases from SolidWorks, Solid Edge, NX, Creo and Inventor, we’ve seen topology optimisation tools in some form or another. In fact, the only CAD vendor I can think of that hasn’t yet introduced such tools is Onshape (though partners do offer connections to such tools).
What’s interesting is how the vendors are pitching the use of topology optimisation. I’ve seen all the Powerpoint slides on the subject, multiple times, and all but a handful focus on the link between topology optimisation and additive manufacturing.
The most common refrain is, “Topology optimisation has been around for a while, but we’ve never been able to manuacture the parts before.” It’s usually accompanied with a photo plucked from a Google Image Search for ‘3D printer’.
It’s at that point you know that they’ve not thought their shit through. A slide meant to illustrate the use of complex mathematics and physics calculations to grow parts using lasers and powdered metals is left flacid by an image of a desktop plastics 3D printer.
The power of topology optimisation is something that has been around for decades now. Those of us who have been around long enough have seen it come and go, rise and fall. What’s changed is that there’s now an immediately tangible way to pitch it – and it’s one that appears to come from the future.
I can’t count the number of times that I’ve heard the phrase “complexity comes for free”. Horseshit. Additive isn’t a complexity free process. It introduces a set of design rules that is not only process-specific, but is also specific in terms of material, process and design intent.
It’s at that point you know that they’ve not thought their shit through. A slide meant to illustrate the use of complex mathematics and physics calculations to grow parts using lasers and powdered metals is left flacid by an image of a desktop plastics 3D printer
While the additive industry loves to talk about stepping away from the Design for Manufacture constraints of processes like machining and injection moulding, the reality is that it introduces a whole new set of rules that are undefined, unexplored and unformalised. These rules are going to be very expensive and time-consuming to establish.
So when a CAD vendor introduces its latest topology optimisation-related update and tell us, “Complexity is free”, it suggests it may just be jumping on a bandwagon, ticking a box to say, “Yeah, we do topology optimisation too”, rather than thinking through the implications of its words.
A much smarter approach might be to pitch these tools and configure them so that users can use the same approach, to remove material from a design space to reach an optimum, to manufacture components traditionally. After all, we all design and engineer a wide range components and very few of them are additively manufactured.
They’re machined, they’re moulded, they’re cast, they’re stamped. Topology optimisation, with the correct controls, has the ability to reduce their mass and retain their strength and stiffness where needed. Surely that’s good thing for everyone, which benefits a much wider range of products?
Of course it is. It’s just as valid, if not more so, to use optimisation techniques to find new forms and functional shapes for less exotic parts, those structural members that could have reduced mass and use less energy to move or to support. Those parts under the hood that are never seen. It’s a less futuristic vision, maybe, but it’s a hell of a lot more impactful on a product’s performance.
Are they being marketed to customers in the right way?
Default