In America, Thanksgiving is a time to take stock of one’s good fortune, usually pertaining to health, home and family. John Allen, maintenance superintendent for Owensboro Municipal Utilities in Kentucky, had additional thanks to give over the holiday: a centrifugal pump vital to the capacity of his electrical plant was back in service, much faster than originally anticipated.
A couple of weeks before Thanksgiving, the pump, used to generate hydraulic pressure to start a steam turbine in the Owensboro power plant, had a major malfunction. Half of the shroud was destroyed and the tops of the impeller blades were sheared.
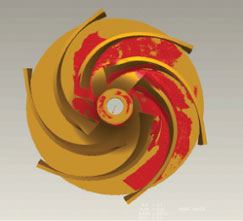
ADC used Pro/Engineer to pattern the master vane, making exact copies around the impeller’s axis (Courtesy of ADC) built from Geomagic Studio’s polygon model
Without the pump, the generation unit couldn’t operate, reducing the power plant’s capacity by a third. Owensboro supplies electricity to 26,000 customers and water to 24,000. There was no backup for the pump, since under normal conditions it will perform for 40 or 50 years without needing replacement. Nor were there CAD models or documentation to help rebuild it.
Under pressure to replace the pump quickly, Allen turned to long-time Wisconsin, USA-based contractor Rotating Equipment Repair (RER). RER has nearly 25 years of experience and a 38,000-square-foot facility housing the latest in pump repair and manufacturing equipment. The company also has nearby partners with unique credentials: Advanced Design Concepts (ADC), a company that specialises in the use of digital shape sampling and processing (DSSP) to digitally reconstruct parts for companies such as Harley-Davidson, Briggs & Stratton, and Simons-Voss; and Signicast, which operates one of the largest, most innovative foundries of its kind in North America.
Traversing physical and digital worlds
The pump project began on the evening of November 8, when RER received the severely damaged pump from the Owensboro plant. The next day, RER disassembled the pump and began preparing it for reconstruction.
Based on the original dimensions of the pump, the damaged remains of the impeller, and its experience in pump design, RER created a 2D CAD model of the impeller in AutoCAD and obtained cross dimensions from it. Over the weekend, a pattern maker at RER built up an impeller vane in clay to match the specifications of the original.
ADC received the clay impeller and the AutoCAD dimensional drawings on Monday morning, November 13. The company was a natural fit for this project. ADC is less than seven miles from RER, but more importantly, the company has used DSSP technology to recreate everything from classic Harley-Davidson fuel tanks to cylinder head ports for Nextel Cup race cars.
DSSP enables companies to navigate easily between physical and digital worlds. This capability helps companies speed development of products based on legacy designs, conduct accurate engineering analysis with digital models that replicate manufactured parts, inspect faster and more precisely, and continuously improve products over their lifespan.
Accelerating the Design
ADC’s task was to create a 3D digital model of the impeller vane as the basis of a 3D CAD model for use in the manufacture of the replacement. Since the impeller vanes were identical, ADC only needed to capture the shape of one vane, then recreate it for the CAD model. By noon, the impeller had been scanned and its geometry captured in the form of a point cloud using a Cimcore scanning head with a Romer arm.
We didn’t have a spare part, so it was important to replace the pump as quickly as possible
John Allen, Owensboro Municipal Utilities in Kentucky
The point cloud was read into Geomagic Studio DSSP software which was used to automatically align the scan data, then “wrap” the point cloud with a polygon model. The Wrap module of Geomagic Studio eliminates time-consuming and labour-intensive surface reconstruction work by mathematically wrapping a polygonal surface around point cloud data. The patented process is automatic, but gives users control to fine-tune the model if necessary. Wrap creates watertight polygonal models without approximation. The polygon model was saved as an STL file that could be used as a guide for the CAD model.
“Geomagic Studio enabled us to align the scan data easily and to quickly create an STL model that accurately depicted the part in a form that Pro/Engineer CAD/CAM software could handle,” says Chris Mulhall, the ADC design engineer who managed the project. “This allowed me to model the part and simultaneously compare the model to the scan data in a time-efficient manner.”
The Geomagic model served as the basis for building a parametric model of the impeller in Pro/Engineer. Mulhall overlayed the scan data onto the Pro/E model of the master vane as it was being created to ensure accuracy. Exact copies of the master vane were then made and patterned around the impeller’s axis. Geometry from the shroud on the bottom of the impeller was used to recreate a model of the top shroud.
The initial plan was to produce a two-part model, which would then be machined, assembled and welded. But, some quick adjustments by RER led to a much more time-efficient solution.
Casting the quick way
RER had originally planned to do a sand casting mould of the impeller. This requires intricate wooden moulding boxes that are hand-made and filled with casting sand or a mixture of sand and clay. The process is labour intensive and the resulting metal castings are rough, characterised by a sand-like texture on the mould. Sand-cast moulds usually require a fair amount of hand work – including hammering, grinding and sanding – to make them suitable for manufacturing. They also take a lot of time, a luxury RER didn’t have.
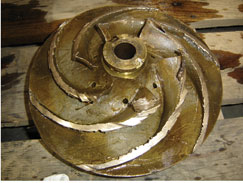
A close-up of the damage sustained by the impeller (Courtesy of RER)
“It can take four to six weeks to get foundry time for a sand casting, then another two to three weeks for the foundry to complete the mould,” says Eric Kirschling, the RER mechanical engineer who headed up the impeller project. “The standard turnaround time is eight-to-twelve weeks, which we couldn’t afford.”
To shorten the turnaround time and increase accuracy of the mould, Kirschling looked into investment casting. In this process, a wax mould is coated in ceramic and placed in a furnace, where the ceramic hardens, and the wax melts away, leaving a finished ceramic mould. RER found a way to further accelerate the process by working with Signicast in nearby Hartford, Wisconsin.
Signicast creates the casting using a rapid prototyping system that produces the mould directly from the CAD model. A hard coating is applied to the rapid prototyped mould and liquid metal is poured into it to form the cast part.
“The end product is better quality than a sand casting,” says Kirschling; “it’s smoother and has tighter tolerances.”
But Mulhall had finished the two-part CAD model of the impeller when Kirschling contacted him with the change in plans, which now required a one-piece model.
“It took Chris about an hour to switch gears and create the one-piece model in Geomagic Studio,” says Kirschling.
The entire digital reconstruction – from scanning to geometry processing to 3D CAD model – took just a day and a half. On November 14, RER had the solid model from ADC, ready for Signicast’s process, sometimes called quick casting.
A reason to give thanks
Signicast did the rapid prototyping and created three investment castings in a week. RER heat-treated the castings that night, then machined and balanced them the next day, November 22. The pump was fully assembled and shipped by the end of the following day, which happened to be Thanksgiving.
The combination of DSSP, CAD and quick casting saved anywhere from six to ten weeks of time by Kirschling’s estimations.
At Owensboro, John Allen and his team had also been making best use of their time. Although the pump replacement was only part of his problem, it was a major part, as an entire energy-generating unit was out of service until it could be replaced. While work was being done on the pump, Allen and his team were busy cleaning the tank in which the pump was submerged and repairing damage in lube oil piping caused by the parts of the pump that blew into pieces.
“We didn’t have a spare part, so it was important to replace the pump as quickly as possible,” says Allen. “RER met our needs to get the pump back and working as soon as possible, and now we have a couple of replacements if ever needed.”
Geomagic to the rescue in fixing a damaged electrical plant