Software, automation and the cloud are all set to play huge roles in the future of manufacturing. Stephen Holmes speaks with Oqton CEO Ben Schrauwen about how the company is bringing together different production software tools within the 3D Systems portfolio, in order to help designers get the best out of existing manufacturing set-ups
The acquisition of Oqton by 3D Systems last year caused a stir, as many feared the former’s impressive brand-agnostic, cloud-based Manufacturing Operating System (MOS) might disappear into the closed shop of 3D System’s technology stack.
The acquisition transpired to be part of a wider change in positioning for the 3D printing giant. The days of 3D Systems protecting its nascent IP for prototyping technology have made way for end-part production technology, ready to be used in diverse shop floor environments.
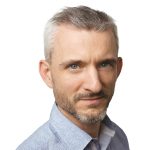
“It’s much more often used in heterogeneous environments. You need to make the shift to being open, and interestingly, the 3D Systems leadership team is now really pushing for that openness – openness for materials, openness for software, openness for machine platforms,” says Ben Schrauwen, CEO of Oqton, which proudly continues to operate under its own banner and remains open to most 3D printing systems.
That brand now includes all of 3D Systems’ software products from prior acquisitions: from Geomagic’s reverse engineering and digital sculpting platform, added back in February 2013, through to Amphyon, bought as recently as May 2021, for SLS build simulation. In short, the portfolio holds a striking range of technologies.
Schrauwen excitedly points out that these fractured tools are now being brought together as a more coherent package, one that is leading the new era of 3D Systems’ openness and expansion.
“In the past, for example, 3DSprint was only for 3D Systems polymer machines; 3DXpert was only for 3D Systems metal machines. We’re taking those products and really allowing them to be used on any type of equipment – particularly with 3DXpert, the one we’re focusing on first,” he says, explaining that support is now added for systems from Trumpf, SLM Solutions, Renishaw and more.
To maintain this neutrality, Schrauwen says a data firewall between Oqton and the rest of 3D Systems has been erected, giving external OEMs reassurance when cooperating with its team of over 300 experienced staff on developing manufacturing software.
Bridging the gap
Having previously worked at Autodesk, Schrauwen is aware of the trend to package CAD software with other tools, such as CAM and CAE. But he feels that this doesn’t really solve a fundamental issue with manufacturing: that production realities are often very different from what engineers have in their minds. “And so one of the reasons I left Autodesk is really to work on this vision, where in my mind, engineering tools need to be much more closely connected to the production reality,” he says.
The Oqton CEO explains that the first step needed is to capture the production state, “which is really three different systems combined.”
These include: an MOS that captures what the operators are doing and their training levels; the IoT platform and what the machines are doing; and quality management.
“These three things together really represent the current state of the production environment,” he says.
Oqton’s slick additive manufacturing automation solution has expanded to production technologies like CNC machining and welding robots, says Schrauwen. “Those are two different manufacturing technologies, where we also demonstrated that AI can lead to 100% automated preparation of these technologies, all from the core Oqton MOS.”
Changing bits is easy, changing atoms is really hard. So changing your production environment is really difficult whereas, as long as you can automate everything, it’s much easier to change a design
This knowledge can be used at the earliest stages of the development process, allowing teams to design parts that their existing production environments can support. “That’s the underlying agenda. That’s what I’m working towards and that’s why I call it a Manufacturing Operating System. Everything needs to be centred around this production capability,” states Schrauwen.
“Changing bits is easy, changing atoms is really hard. So, changing your production environment is really difficult, whereas as long as you can automate everything, it’s much easier to change a design than it is to change your production environment,” he adds.
“If you want to bring things to market more quickly, you need to design for what you’re able to do today and not for a hypothetical factory that you might have to build.”
Oqton // Leaving legacy behind
To enable this to work, Oqton has taken the existing 3D Systems desktop software and added it to its cloud, creating a connected platform.
“The expert user can still use the desktop tools, but they are part of an automated workflow that we orchestrate through the web platform,” says Schrauwen, adding that the refresh has allowed for any poor legacy algorithms to be left behind. “We’re really bringing them to the cloud and turning them into services that allow us to automate these processes much more significantly.”
The days of OEMs shunning the cloud are now over, he says. As evidence, he points to the CIOs of automotive giants like Volkswagen and BMW, who have flipped their policies 180 degrees in as little as five years. “Cloud is now the thing they want to deploy first, because they understand that is the only thing long term that is scalable and maintainable, and that will allow them to innovate and move faster. And that’s what we’re really seeing with Oqton. Everything – the whole spectrum – is moving to the cloud.”
Of course, each industry has its own strict regulatory framework for compliance, and it takes a lot for software like Oqton to be able to operate within these mandates. But as Schrauwen says, it also solves many IT management issues for companies that would otherwise have had to do it all in-house.
Speaking with Schrauwen, it’s clear that if automation is key to the future, then Oqton might hold the key that opens the factory door to next-stage digital manufacturing.