Selle Italia has launched two new flagship bicycle saddles that showcase the historic brand’s adoption of new technology, taking the company to the front of the pack. Claudia Schergna spoke with the team at Selle Italia and its manufacturing partner Prototek about how new technology got it across the finish line in style
Cyclists are connected to their bikes by only three points of contact: the handlebars, the pedals and the saddle, making it essential that each is developed to fit the ergonomic needs of the cyclist.
The foams and gels used in a saddle start to break down after about a year of normal use, due to the effects of sweat, friction, water and sunlight. Yet these are not the only things that take a toll on your posterior. The design and manufacturing of the saddle itself plays a major role.
Saddle maker Selle Italia began life outside in a village on the outskirts of Milan back in 1897, producing seats for everyday bicycles used as general transportation. In the late 1970s, cars became common and cycling became more about sport than anything else.
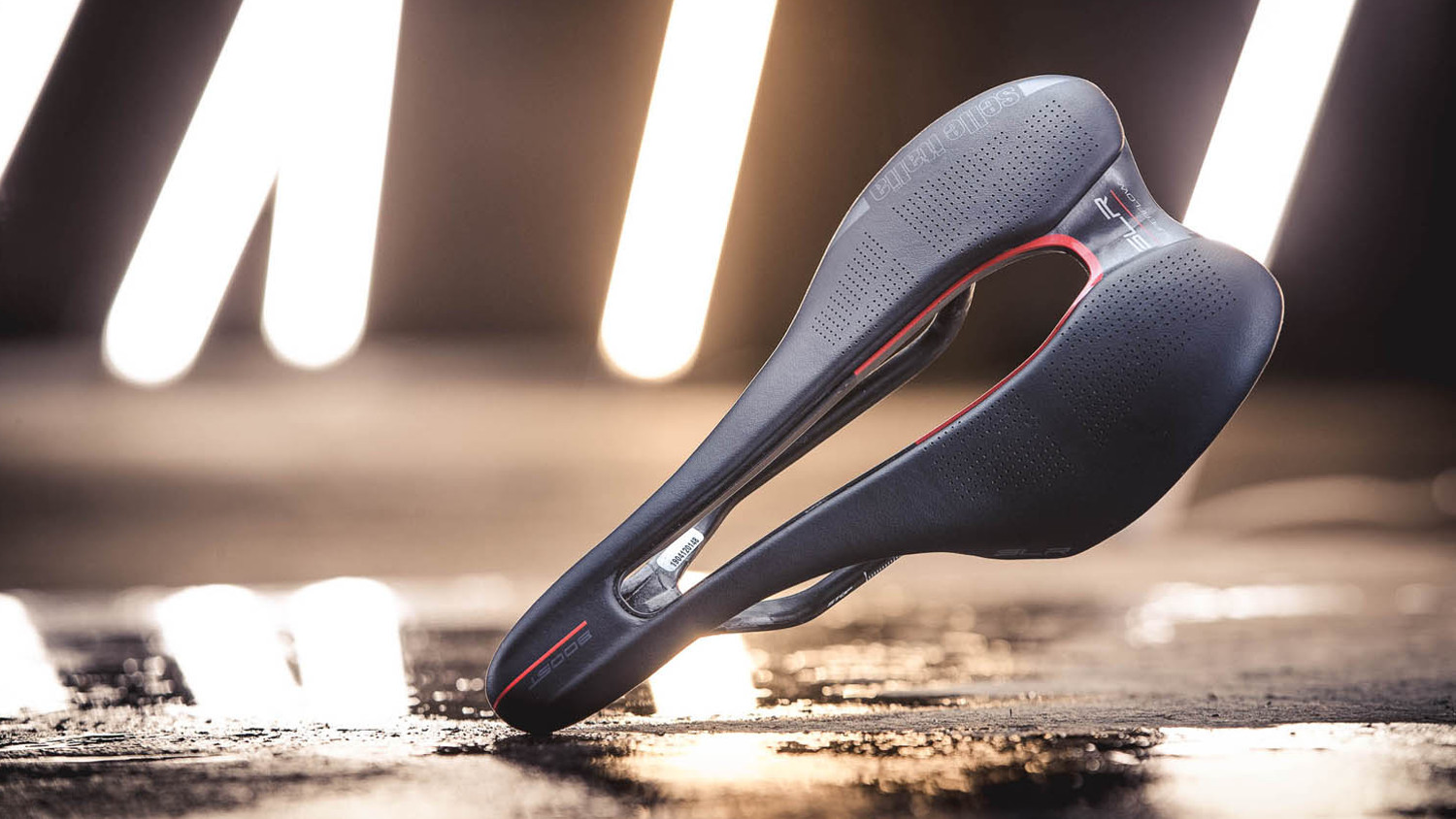
With traditional manufacturing methods, saddles can only be produced with a consistent density of material throughout the whole piece. The only way to work around this is to break the saddle into separate parts, which are then sewn together, but this creates other problems, such as seams and void areas that hinder comfort and introduce production complexity.
For road cycling, greater support is needed in the central part of the saddle, while the front and side elements require more perceived cushioning. While this would be impossible to achieve using traditional manufacturing methods, 3D printing makes it possible to produce as a single form.
Many 3D-printed bike saddles are already on the market, designed for both elite athletes and passionate amateurs willing to pay for the latest accessories.
We allowed ourselves the luxury of trying to raise the bar and apply these new technologies according to our needs, trying to make the technology adapt to the product, and not the other way around
Late to this technological upheaval, the Selle Italia team decided to turn this disadvantage into a strength. “We weren’t in a rush to be pioneers, as we weren’t the first. Carbon technology had already been tested on other products and industries. So, we allowed ourselves the luxury of trying to raise the bar and apply it according to our needs. Trying to make the technology adapt to the product, not the other way around,” explains Selle Italia marketing manager Enrico Grando.
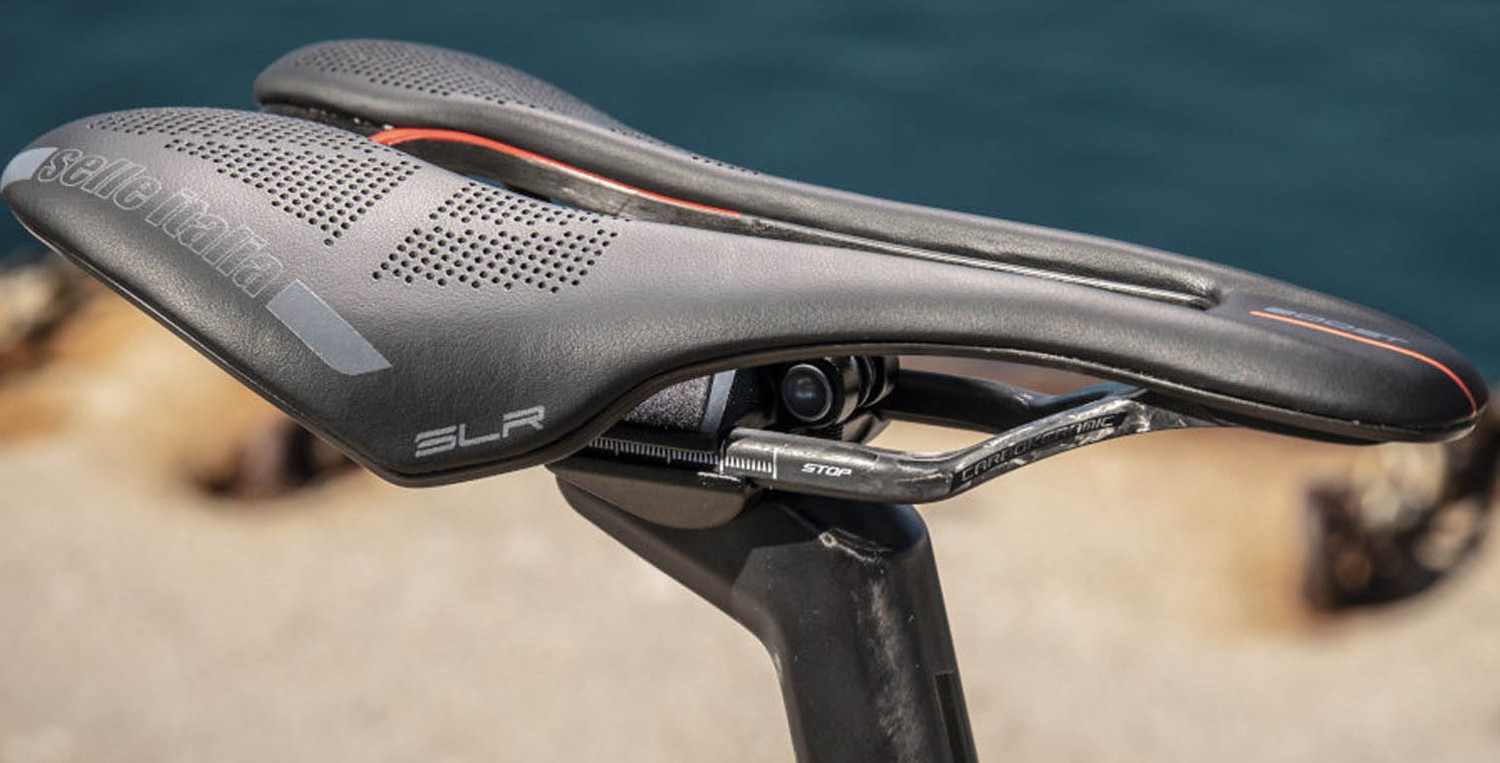
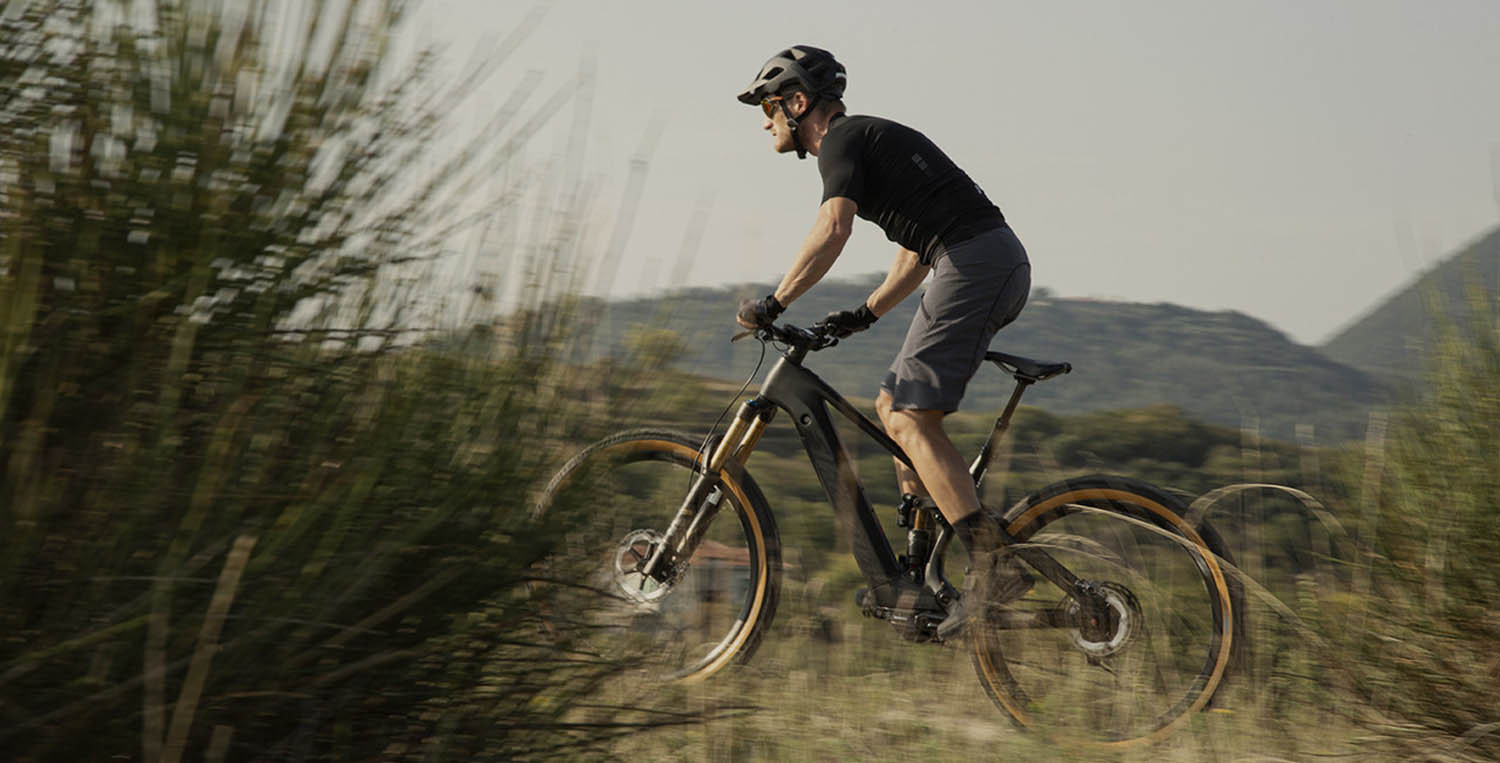
Long-lasting performance
Saddles produced with 3D printing do not only last longer, but if printed with some kinds of resin, they also improve their performance the more they get used. Grando says that a saddle produced using an elastomer resin achieves better results when pedalling because it adapts to the cyclist’s needs, “as if it were a live material, that adjusts to the cyclist’s body and pedalling style.”
Depending on the riding style and the physical features of the user, saddles best perform with different densities and stiffnesses, which 3D printing allows.
The design process at Selle Italia starts with its sister company, specialist bike fitting service ID Match, gathering information, feedback and requirements from a range of elite cyclists.
“Longer, shorter, wider, narrower, central hole, no central hole, frame type, material type. There are countless options for a cyclist, and making a decision is not easy,” explains Grando.
“So cyclists often ask, ‘How do I choose the right saddle for me?’ To answer this question, ID Match was created, initially with more experimental tools and now much more advanced.” ID Match has more than two hundred branches worldwide, conducting thousands of bike fitting sessions every month. As this entire system is cloud-based, it provides an exceptional database for the Selle Italia design team.
“After having collected the data, our design office receives a brief and starts designing a saddle, usually starting with a hand sketch. From there, an in-house prototyping process begins,” says Grando.
The nature of the organic forms sees the design team use Rhino 3D to create an initial CAD model, from which early prototypes can be built and assessed. Then a mechanical model is produced in Solidworks, allowing the team to assess assembly modelling mould flow simulations. For some simulation phases, Selle Italia’s designers use the embedded software within Solidworks, but for more advanced validation simulations, they rely on specialist external studios that use Ansys.
The team relies heavily on outsourcing, although has acquired a Photocentric machine inhouse, while outsourced HP Multi Jet Fusion 3D-printed parts are used for hard shells and parts that will later be injection moulded.
A fully Italian job
Once the design team produces its final prototype, the process moves outside of Selle Italia’s facilities to experts in Carbon’s DLS 3D printing process at Prototek.
Originally founded as a 3D printer reseller and service house, Prototek’s location in the goldsmiths’ capital of Italy, Valenza, meant it has a long history in serving the country’s jewellery industry.
Printing directly in wax allowed jewellery artisans to skip a step in their process. Instead of drawing a model in CAD, printing it in stereolithography and using it as a master to make a silicone mould, they can just draw the model in CAD and print directly in wax for metal casting.
“Valenza, which is extremely artisanal and linked to the traditional way of making models, was actually one of the first areas to adopt this technology,” says Andrea Barchi, head of the 3D printing department at Prototek.
“At first, it was met with extreme scepticism by master goldsmiths, who saw it as a loss of creativity on their work,” he goes on, explaining how its history of helping skilled craftsmen adopt a new process did not begin with saddlemakers.
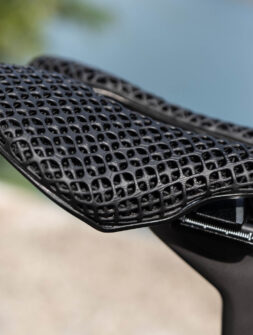
With time, the company expanded to serve different industries and different additive manufacturing technologies. Moving beyond casting moulds and prototyping, and adding SLS and HP Multi Jet Fusion technologies, it began working with the automotive, sport and industrial machinery sectors.
“Obviously, in 2006, when we started, 3D printing was used 99% for prototypes, because the materials did not have the strength and durability required for a product used in part production,” says Barchi.
Then, an encounter with Carbon’s technology shook things up, accelerating Prototek’s move into 3D printing end-use parts.
“The first time I saw Adidas soles [printed using Carbon’s technology], I thought, ‘These guys are crazy! It’s not possible for the elastomer to support a person’s weight repeatedly when all the other thermoplastic elastomers I’ve seen break immediately and are only suitable for a few uses in prototypes’.”
Taking a chance on the technology and acquiring a Carbon M2 3D printer, the bureau immediately began to target the sports industry, and in particular, the flourishing cycling industry in northern Italy.
“We received much more response than we expected!” says Barchi. Selle Italia was one of Prototek’s first customers for the M2 and, as the ideas started to flow, it became apparent that the M2 was too small for some applications, including saddles. So Prototek quickly installed two larger Carbon L1 machines.
Above all, we have managed to maintain the essence of our products
Prototek produced two models for the company: the SLR Boost 3D for the Selle Italia brand, and Shortfit 2.0 3D for its sister brand, Selle San Marco.
“We are very satisfied with the results,” says Grando. “Above all, we have managed to maintain the essence of our products. Like all brands, we have iconic products. For example, Selle Italia’s SLR is our flagship saddle. Many cyclists are more familiar with the SLR model than the Selle Italia brand itself,” he says.
“Over the years, we have adapted it to the needs of modern cycling, but without altering its distinctive features, such as the shell, the saddle base, which are much loved by cyclists.”
The design was adapted for 3D printing by Selle Italia’s in-house design team with the help of Prototek, so that it offered a new cushioning experience while maintaining the classic form. The challenge was that the saddle is formed close to the shape of the rider, with many curves in different directions, including the lateral sections. “I think these shapes drove Andrea and the Prototek team crazy,” Grando laughs.
The finished product, he explains, offers improved aesthetics, strength and performance. Moreover, this method allows Selle Italia to design its own lattice structures. Carbon offered one of its own lattice patterns, but Grando explains that the team wanted to develop their own, not only to improve aesthetics and differentiate the models, but also to boost the functional properties of the saddle.
“The aesthetics are obviously important: this saddle costs €450 and is mounted on bicycles that may cost €10,000,” explains Grando. “It could have worked with Carbon’s [lattice] as well, but the purpose of applying this technology is to provide much greater comfort by allowing for differentiated cushioning zones.”
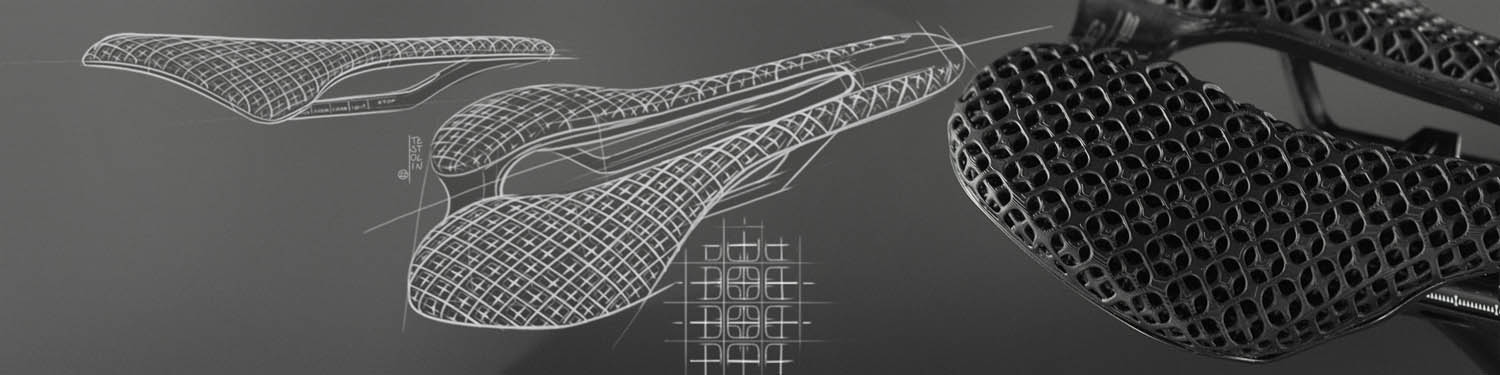
Looking ahead
The new line of 3D-printed saddles has been extremely well received by Selle Italia customers, despite the fact that many of them are traditionalists at heart.
“It’s still a new technology in the industry, which requires some adaptation time for cyclists to understand the advantages,” says Grando.
Despite the success of this project, however, he doesn’t see 3D printing replacing traditional manufacturing on the whole production line at Selle Italia just yet, primarily because 3D printing with this technology is simply not economically viable yet when you’re dealing with large production volumes.
“Currently, Prototek is able to print approximately three saddles per hour with a Carbon L1. Production volumes are limited, because the timeframes are considerably longer compared to traditional saddle production. Currently, 3D printing is still slower than traditional production,” he explains.
This is not a problem for Selle Italia when it comes to more expensive saddles, he says. “Production volumes are lower, but the quality is higher, which gives us the highend product we wanted to achieve.”
What is undoubtedly true is the success of the collaboration between Prototek and Selle Italia, even at a time when, post-pandemic, the cycling market has plateaued.
“We experienced two years of very high sales volumes during the pandemic, and now everything has come to a halt. Obviously, it’s a period of recession, of high inflation. But even in this less-than-optimal period, our 3D printed series is selling very well.”
According to Grando, the key to the project’s success was the union of different experiences and know-how shared between Selle Italia and Prototek, enhancing the former’s 125-year tradition with a technology-led saddle that sets the standard for others to try and catch for years to come.
This article first appeared in DEVELOP3D Magazine
DEVELOP3D is a publication dedicated to product design + development, from concept to manufacture and the technologies behind it all.
To receive the physical publication or digital issue free, as well as exclusive news and offers, subscribe to DEVELOP3D Magazine here