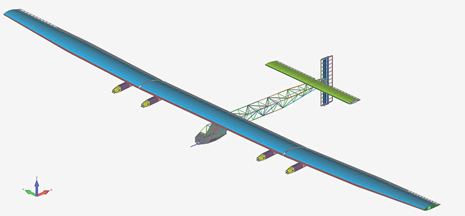
Femap with NX Nastran is being used to optimise and verify the structure of first plane to circumnavigate the earth using solar power alone
Last week we published a blog post on the Solar Impulse 2 project and its attempt to fly around the world powered only by solar energy.
Following lift off in Abu Dhabi on 9 March, the plane has been to Muscat, Oman, then Ahmedebad, India, and is currently being prepared for its third flight to Varanasi, also in India. The team’s progress can be followed via the project’s logbook.
A plan hatched by the Swiss team and co-pilots, Bertrand Piccard and André Borschberg, the aim is to fly around the world with the craft’s only power coming from the sun.
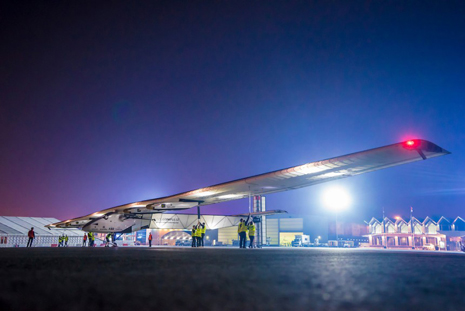
Ground testing in Abu Dhabi before take-off
The total flight time will be around 25 days (500 hours) covering 35,000 km, making 12 stops over five months.
To create this feat of engineering, Solar Impulse 2’s design team have used a range of technologies. As well as using Dassault Systèmes’ 3DEXPERIENCE platform, including its CATIA and ENOVIA applications, they have also made use of the the finite element analysis (FEA) solution – Femap with NX Nastran – from Siemens PLM Software.
One remarkable aspect of the Solar Impulse 2 is the fact that, even with its massive wingspan (71.9 metres) and all of the batteries required (633kg), the plane weighs just slightly more than an average automobile (2300kg).
Obviously, minimising weight was one of the most critical design challenges. “The plane needs a lot of batteries, and batteries are heavy,” explains Geri Piller, head of structural analysis at Solar Impulse. “Yet the plane gets only a small amount of energy from the solar cells, so it has to be really light.”
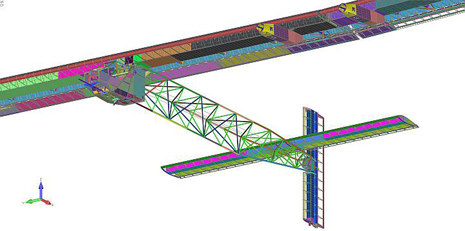
Femap accepts the Solar Impulse design team’s geometry, created with CATIA software, in STEP or IGES format. The geometry becomes the basis for finite element (FE) models
The plane’s cockpit is a good example of how the Femap with NX Nastran FEA solution helped minimise weight.
The single-seat cockpit is tiny (3.8 cubic metres), but it’s actually three times larger than the cockpit of the Solar Impulse 1, which proved as a test bed for all the complex technologies onboard. Although the new cockpit is larger, it weighs less than twice as much as the original (60 kg for the new cockpit versus 42 kg for the original).
The new plane’s wing structure is another place where Femap contributed to a significant weight reduction. The wing consists of a Kevlar honeycomb core covered with an advanced carbon fibre material. Because the new plane flies faster than the first one, its wings had to withstand greater loads.
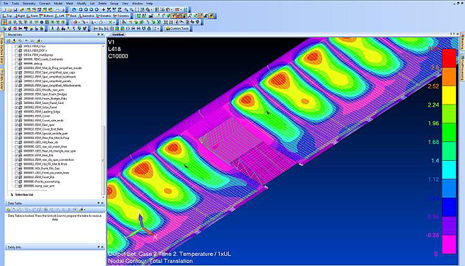
Ability to optimise carbon fibre ply thickness and number of plies helped hold down weight of wing structure
Analysts used Femap to optimise the amount of the carbon fibre plies so that they could meet the needed loading conditions with the least amount of added weight. They were able to go from using a material weighing 100 grams per square metre to one weighing 25 grams per square meter, a significant weight reduction.
Similarly, the motor gondola of the second plane has to carry a heavier load, but the weight increase was kept to a minimum, in part by changing from a framework structure with fairing to a sandwich structure and, in part, by using FEA to optimise components such as facings and spar caps.
By using Femap on this project, Piller and his colleagues were able to quickly determine how best to minimise the plane’s weight while still meeting the rigours of an around-the-world adventure. “Using Femap, it was really fast to see what we had to work on and where we could optimise,” Piller says.
To follow Solar Impulse’s round the world flight, progress will be updated on its website and twitter feed. Videos can of the team’s progress can also be viewed on its youtube channel (like the latest one below).