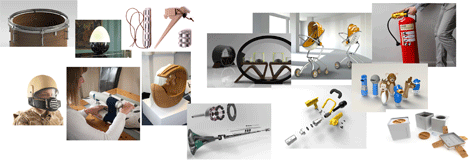
New Designers gives us the chance to assess the latest crop of graduate design talent all under one roof, and this year didn’t disappoint.
Click through to see part two of our highlights, with our top five picks getting their own individual blog post later in the week.
Inigo Martin-Quirk – Sussex
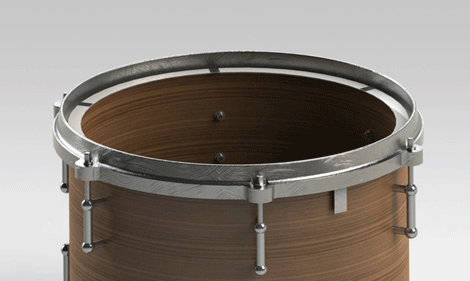
Unlike guitars and other such instruments of ‘raawk’, drums have to be tuned by ear – time consuming and sometimes inaccurate – so drum fanatic Inigo produced an electronic solution.
Each drum has a pressure sensing ring fitted between the drum shell and the drum head, a handheld device is then plugged in to a tab on the ring and displays the pressures read by the different sensors. The user then adjusts the tension via the lugs as usual. When all the numbers around the ring of the drum on the display are matched the drum is in tune.
Sketches to visualise the product were quickly followed by research into pressure sensing materials and products. When the technology was chosen the Apache Drum Tuner could be modelled in PTC Creo and rendered. The handset model was used to create a SLA printed handset, with all mocked-up parts attached to one of the drums that Inigo himself designs.
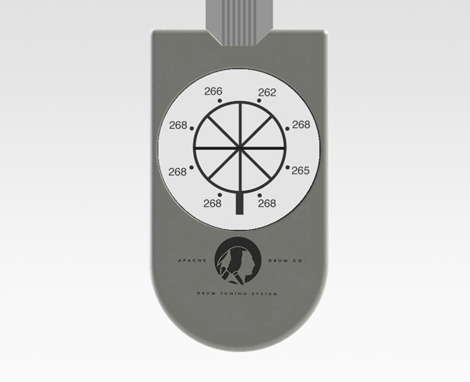
Isabel Heubl – Falmouth
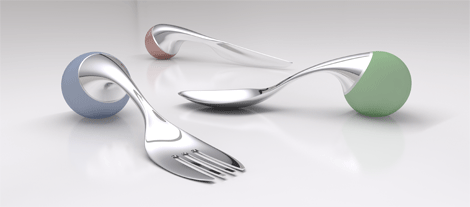
Isabel’s two projects both caught the eye, Rocky, an egg-shaped, colour-changing light was initially designed as a fun and interactive children’s lamp. When nudged it wobbles around, and the colour of the lamp changes in an attractive manner – so much so that it’s being redeveloped for grown-ups.
Ergonomic cutlery was much more purposeful; targeting the user group of people suffering from dexterity issues, in particular arthritis, and giving them attractive, but manageable utensils.
After much research through user groups, both projects were designed using Rhino, with the cutlery being taken a step further and 3D printed with a metal chrome in the final piece to give a realistic visualisation.
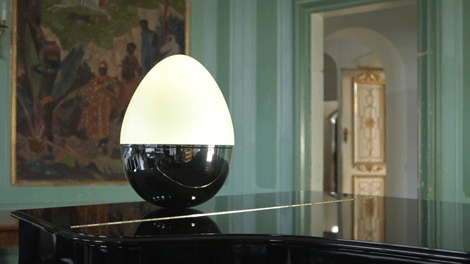
James Carswell – Brunel
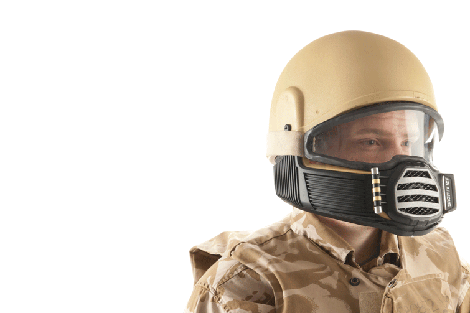
One in five military veterans from Afghanistan and Iraq has been shown to suffer some form of Traumatic Brain Injury (TBI) from repeated exposure to Improvised Explosive Device (IED) blasts. James’ Air Armour system is designed to provide protection against from this by deflecting blast waves away from the user’s face so the blast pressure does not traumatise the brain.
The multi-layered composite shell deflects the blast waves and acts as a shock absorbing mechanism, combined with a flexible rubber skin to help protect against blunt trauma forces, while respiratory protection, provided by an existing compact blower unit, provides cool air and helps lower heat fatigue.
A Solidworks CAD model, was developed further by (impressively) using Ansys for CFD and FEA analysis. KeyShot was used to render the images, while physical parts were built using 3D printing.
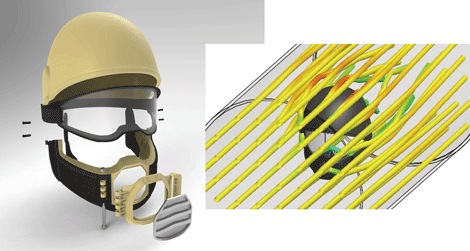
James Wood – Bournemouth
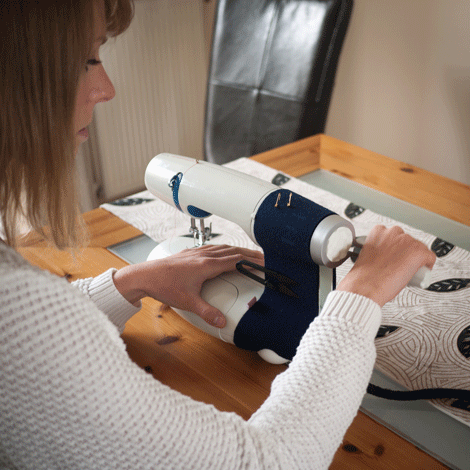
Sewing machines were all the rage at this year’s exhibition, with some impressive models on show, although for the ultimate in packing in every feature possible, while keeping the product simple to use, James’ Sue Machine wins.
With detachable sections, magnetic strips for scissors, felt for pins, a bluetooth pedal, all packed into a compact unit that can be stood on one end for storage, it has it all.
Sketchbook Pro was used to evaluate final concepts before moving the design into SolidWorks, and Keyshot for the renders. The physical prototype was brilliant, even though only manually powered at this stage, with 3D printed parts of all materials being used.
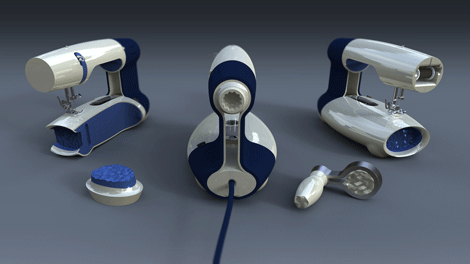
Jonathan Sellars – Northumbria
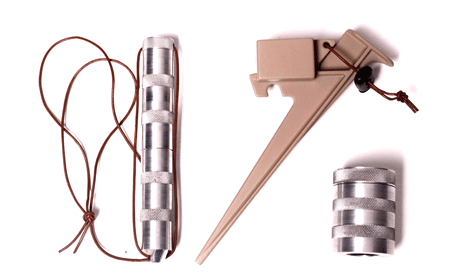
As fans of the great outdoors, stumbling across Jonathan’s work amongst the wooden furnishings of his counterparts made us long for a campfire somewhere away from London.
The results are manly in appearance – all turned aluminium and wax cord: The tent peg is not only a stronger anchor for the guy lines, but comes equipped with a solar-powered light to warn of the trip danger. The Bee Dry is a waterproofing wax dispenser/holder to save you from a soaking, while the Steel Survivor fire steel can be used to start a fire in adverse conditions (unlike a match or cigarette lighter).
Designed through sketches into Autodesk AutoCAD and then SolidWorks, 3D printing had a prominent role in realising how the tent peg’s strength and structural qualities would work. Elsewhere, the tricky part was the craftsmanship required to turn the aluminium casings.
{encode=”jonathansellars88@gmail.com” title=”jonathansellars88@gmail.com”}
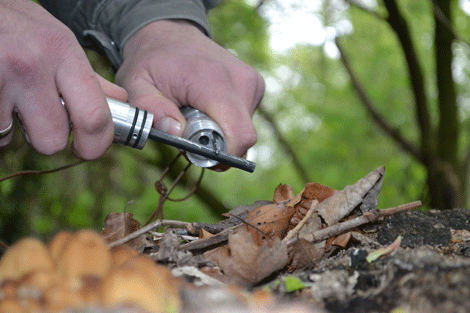
Jose Olliveira – Teeside
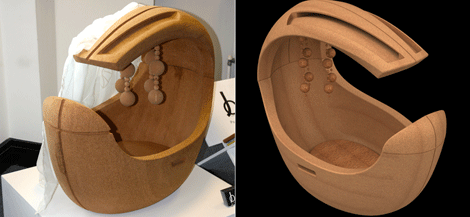
Made entirely from cork, which in turn is harvested by a sustainable method, Jose’s cot has some great material qualities suited for a little-one’s bed, as well as being radically different in design.
Light weight so it can be moved easily around the home, impermeable to liquids or gas (babies have lots of both), and an excellent thermal and acoustic insulator, the material is also resistant to abrasions. Plus it’s one hundred per cent natural, recyclable and reusable (most baby equipment is bought brand new and used only for a short period).
Sketched and then modelled in SolidWorks, the design was proofed in CAD first before being milled and hand finished.
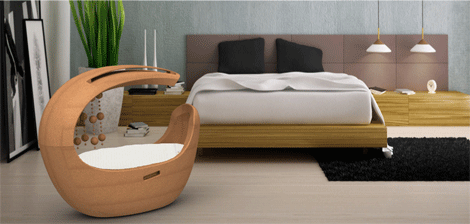
Kirath Ahdan – Loughborough
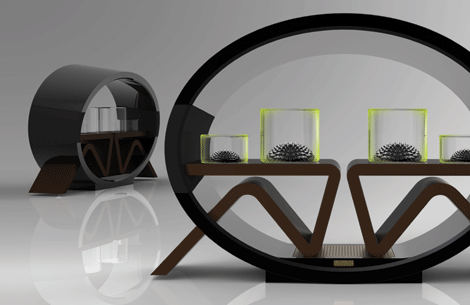
Providing the show’s soundtrack was Kirath’s incredible – and entirely desirable – Mirage sound system. Combining lighting, sound and magnetically influenced Ferrofluid to create ‘active visuals’, Mirage creates a visual accompaniment to enhance the loud speaker experience.
Through the use of Ferrofluid, spiked sculptures arise from each glass chamber, giving it the ‘wow factor’ that the intended high-end customer would be after. Ferrofluid is in fact used in speaker design already as a lubricant for speaker drivers, with Kirath’s approach being an innovative visual use. Further impressive points include the iPhone control UI, a physical volume control that is touch controlled on the system cabinet, and its all-round ‘open side’ acoustic properties.
Designed using Sketchbook Pro and SolidWorks, the project was hand built by Kirath himself, with some marketing visualisation done in Keyshot.
{encode=”kirathahdan@hotmail.com” title=”kirathahdan@hotmail.com”}
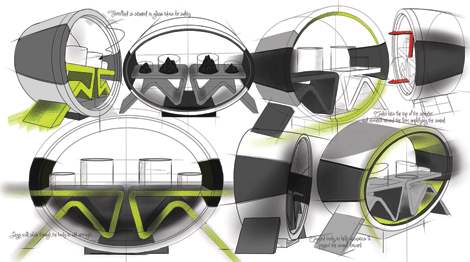
Nell Bennett – Loughborough
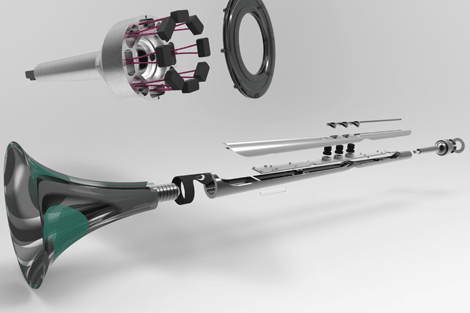
With most established Western musical instruments having an electrical equivalent Nell got frustrated that there wasn’t one of her favoured trumpet, so she designed one with the hope of pushing its use into new genres.
An electronic system picks up the musician’s unique playing style through sets of pressure sensors located in the mouthpiece, a mini microphone and capacitive touch sensors. To maintain visual appeal for the audiences and emotional attachment for musicians she crafted the ‘bell’ of the trumpet from blown glass, which could effectively be any material that the musician chooses.
Once understanding the electrical components required, Nell sketched out concepts that would effectively hold the electronic components and retain some aesthetic forms identifiable as a trumpet. SolidWorks was used to model the design, developing a realistic design proposal focused on assembly features and internal component fixtures, with KeyShot renders used to test the various visual elements.
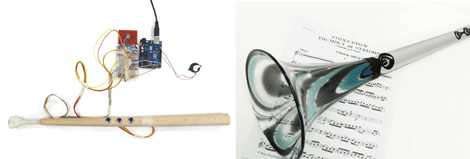
Nicola Danks – Coventry
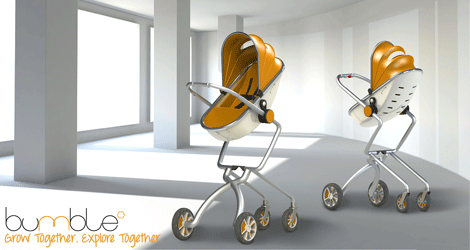
Inspired by bees looking after their young in the hive, the Bumble pushchair is a modular first time parent kit, consisting of a baby carrier, bassinet and pushchair with a higher frame than products in the market.
Nicola’s design merges the different components into one another to reduce storage and cost issues, while focussing on aiding child development through maintaining its eye contact with the parent through a raised seating position, and moveable handlebar.
After initial sketched concepts were rendered in Photoshop, the model was rebuilt and fully rendered in SolidWorks. The scale model consisted of a 3D printed SLA frame, with additional 3-axis-milled parts, giving an incredibly detailed visualisation.
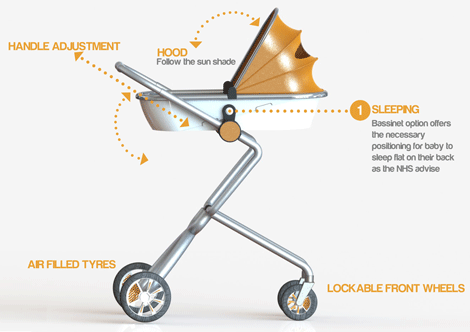
Phil Reilly – De Montfort
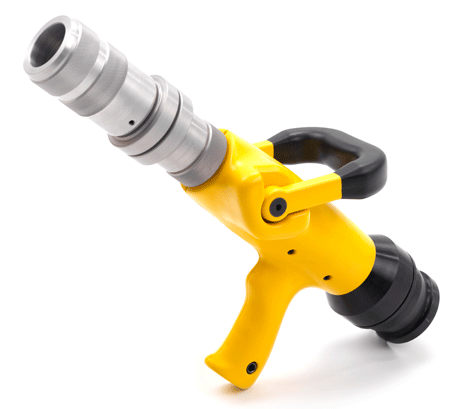
Tackling the issues of our fire services, Phil designed and manufactured a compressed air and foam system, with improved ergonomics and developing a
system that allows the ball valve inside the branch to open in a controlled manner (rather than the current, adrenaline-fuelled issue of an initial, ineffective jet burst).
Having consulted experts from Leicestershire Fire and Rescue Service he did a nice job of redesigning the mechanics, using a rotary damper with a sprag clutch, allowing increased resistance on the valve to operate in one direction only.
Solidworks was used to model the 3D CAD file with Keyshot providing the renders, but the body of the work proved to be in the production of test rigs of which several were built to prove the design.
{encode=”philreillydmu@googlemail.com” title=”philreillydmu@googlemail.com”}
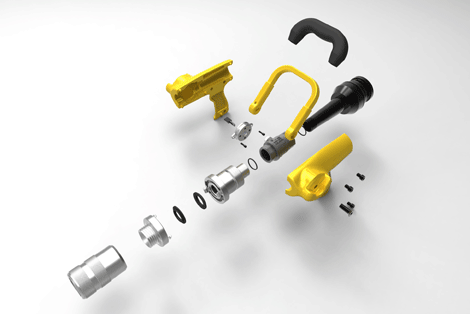
Robert George – Aston
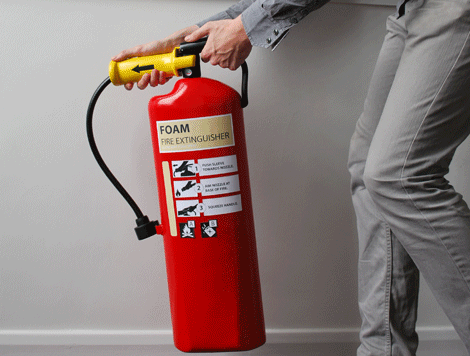
Continuing the theme of challenging existing and accepted designs in fire fighting, Robert George identified the speed of deployment and intuitiveness of the standard domestic fire extinguisher as possible areas for development.
A unique ‘pull sleeve’ acts as the conventional safety pin and an indicator of the type of extinguishing agent inside the product; giving its operator something robust to cling onto when tackling a blaze and locking into the hose nozzle to indicate that it’s been used. Material choices and a redesign of the shape meant it was lighter and could be dragged along the floor if necessary, while a flatter profile and use of readily available velcro means it takes up much less space. Despite all these changes, it manages to meet all the stringent British Standards required.
Once modelled in 3D using SolidWorks, early designs of the extinguisher sleeve and valve were produced on a Z-Corp 3D printer, helping judge the size and feel of the attachment and to create the final concept.
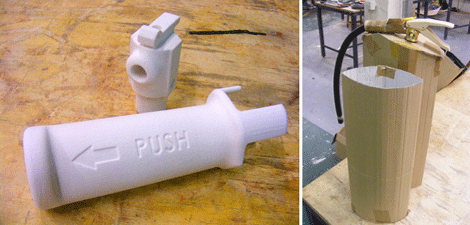
Ross Reeves – Hertfordshire
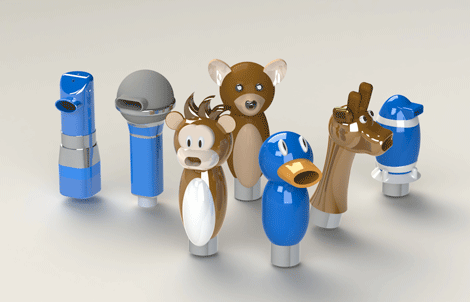
With 35 million asthma inhalers used each year in the UK, the need to replace them totals 450 tons of annual waste – plus they’re ugly – so Ross’ idea was to incorporate an incentive into the newly proposed recycling service.
Making the casings more attractive for children would help them use it more regularly, and by creating a range of different animal casings, they would be encouraged to recycle their old penguin if they knew they’d get a different design the next time around (like a Happy Meal incentive). The characters even conform to the compulsory blue and brown colourings.
Designed in SolidWorks, a prototype was built using the university’s FDM machine for testing, before a more polished prototype was produced by Shapeways and enamel painted.
{encode=”ross.reeves10@googlemail.com” title=”ross.reeves10@googlemail.com”}
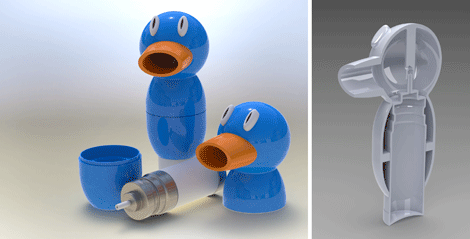
Thomas Smith – Huddersfield
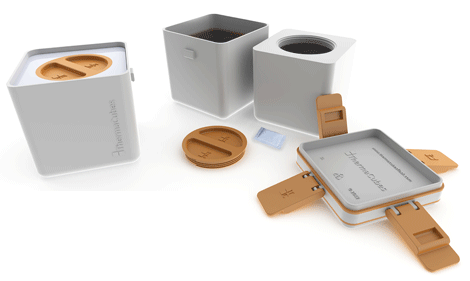
Although quite simple in its design, what was impressive about Tom’s design for device to promote healthy eating in the workplace was that everything had been considered for mass production, injection moulding and all-round manufacture.
Some nice design features make it ideal for Britain’s construction workers – robust clasps, dual compartments for tea AND coffee (luxury), a square build that can be opened whilst wearing gloves and that stops it from rolling around in the footwell of your white van.
A placement at a firm that does a lot of injection moulding has paid off, as Tom purposefully built his 3D SolidWorks model with manufacture in mind, from the location of split-lines, runners and risers, to draft angles and ejector points.
{encode=”tomsmith00@live.co.uk” title=”tomsmith00@live.co.uk”}
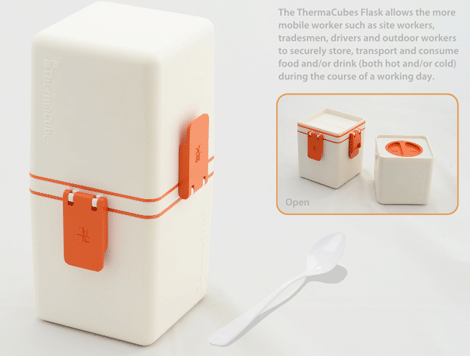