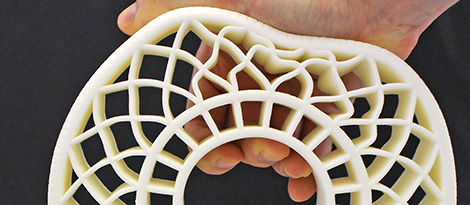
A deal between chemicals giant BASF and Belgian 3D Printing pioneers Materialise will see wide scale testing and further optimisation of BASF’s materials on the machines and within the infrastructure of Materialise.
BASF is expanding its cooperation with Materialise with an investment of $25M, as they work together within the framework of an ‘open business model’ to improve materials and software for various 3D printing technologies and bring them more rapidly to the market.
The need for a greater range of materials to aid market expansion VS The cost of developing materials en masse for a small industry has always been a Catch-22 for the 3D printing industry, so this partnership should prove an interesting development, considering that the deal outlines a focus on ‘applications in the consumer goods sector and in the automotive and aviation industries’.
“To increase the adoption of 3D printing as a complementary manufacturing technology for final products, our industrial customers increasingly demand more control, more choice and ultimately lower cost,” says Materialise CEO Fried Vancraen.
“We are confident that this collaboration with a leading manufacturer of materials will help to accelerate the adoption of 3D printing in existing vertical markets and create significant business opportunities in new markets.”
Volker Hammes, managing director of BASF 3D Printing Solutions GmbH, added: “Our two companies’ business areas complement each other very well and our cooperation will put us in an even better position to find and develop new business opportunities.”
How will this help grow the additive manufacturing industry? Materialise CEO Fried Vancraen gave us this extended answer:
3D-printing is a revolutionary technology, capable of transforming entire industries and challenging our traditional manufacturing processes.
Development of new materials, better and faster machines and increased automation provide new impulses to the 3D-printing industry and lead to continued innovation.
This has helped to position 3D-printing not just as a prototyping technology but as a relevant alternative and complementary manufacturing technology for final products.
As a result, we are seeing increased adoption of 3D-printing among industrial manufacturing companies. Leading manufacturers in the automotive, aerospace and consumer goods industry turn to 3D-printing as they recognise the design optimisations it creates in existing vertical applications and the potential to create new and significant business opportunities in new markets.
However, today’s 3D-printing industry doesn’t yet offer the interoperability that industrial manufacturers are looking for.
If they want to be serious about adopting 3D-printing as a complementary manufacturing technology for final products, they simply cannot afford to be locked into proprietary solutions that limit their flexibility and choice.
If we, as an industry, want to increase the adoption of 3D printing, we need to work together to provide more control, more choice in materials and systems and ultimately lower cost.
If we, as an industry, want to increase the adoption of 3D printing, we need to work together to provide more control, more choice in materials and systems and ultimately lower cost.
That’s why today, I am proud to announce a strategic alliance with BASF, the largest chemical producer in the world, which intends to drive growth in the 3D-printing industry by promoting a more open market model.
Materialise and BASF share a vision for growth in the 3D-printing industry that builds on the creation of meaningful applications in an open and vibrant ecosystem.
That’s why Materialise will continue to identify applications that can benefit from 3D-printing and our close collaboration with BASF will help to develop these applications, especially when new materials or material adaptations are required.
BASF will use our 3D-printing facilities, one of the largest in the world, to launch or certify new materials in multiple verticals such as aerospace, automotive and wearables.
A good example is the transformation we are driving in the eyewear industry. The design optimisations and functional improvements enabled by 3D-printing in combination with the possibility of mass customisation hold the potential of revolutionizing this entire industry, similar to what we did in the hearing aids industry. But for many people, eyewear is an extension of their personality.
So if we want to be truly successful in capturing the eyewear market, we need to think beyond optimising production processes and functional optimisations. By identifying and developing new materials we can also create the bespoke look and feel that people are demanding from their eyewear.
The combination of our software and the expertise of BASF in chemicals will accelerate the development of new applications and create new business opportunities.
To support Materialise in identifying and developing these applications, BASF has agreed to invest $25 million in our company through a private placement of new shares.
In addition, we are also extending the possibility to participate in our capital increase by announcing a public offering of up to $50 million in new shares.
The support and expertise from a leading company such as BASF is a testament, not only to the capabilities of Materialise but to the relevance and the growth potential of the entire 3D-printing industry.
Today’s announcement signals another giant leap forward in unlocking the full potential of 3D printing as a complementary manufacturing technology and taking a bigger share of the 12 trillion dollar global manufacturing market.
Want to read more on how an eyewear project from a lens-making giant and Materialise looks to have finally seized on 3D printing’s potential – Click here to read the article
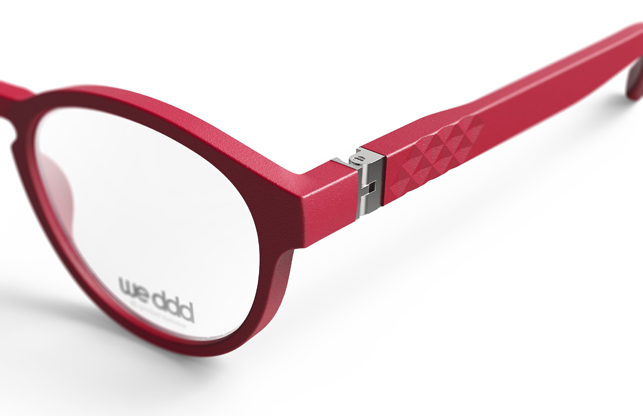