
Our first test print – Makie Boots – fine details combined with solid little parts that have some interesting features here and there – thumbtack for scale
If you’ve not been following this, we’re spending time with the Form 1+ from Formlabs.
The initial post is here, but to bring you up to speed, we spent the first day unpacking, setting up the machine and printing some first test parts.
The results are in and they came out pretty well.
As you can see from the photos above, the detail is good, but before we get onto that, let’s talk about how we got to that point.
When I last did an update, the parts were just sent to build. That took a couple of hours. The machine whirred away in the corner of the workshop and was barely audible above conference calls and Public Enemy playing on the stereo (if you’re curious, the Most of My Heroes Still Don’t Appear On No Stamp album).
The machine’s display gives you a read out to tell you when it’s ready. Set up a timer on your phone and you’re ready to watch it complete – something that, even after 20 years of working with this technology, never gets old.
There’s nothing quite like seeing a dataset that was, until this point, a digital representation. Due to the way the Formlabs machine works, you’ll find the part hanging from the build platform, suspended from those ever-so-clever support structures. So what next, you ask?
Tip #3: If you decide to pull the trigger on a Formlabs machine, get a few things in place as you do and before you start building. The key one is Isopropyl Alcohol. It’s pretty easy to buy online, but if you forget, you’ll find yourself running around the local chemists/pharmacies, buying their stocks of surgical spirit (it’s the same thing)… And trust me, buying near enough pure alcohol in half litre bottles at 9.30 on a monday morning looks more than a touch iffy.
Removing the parts from the machine
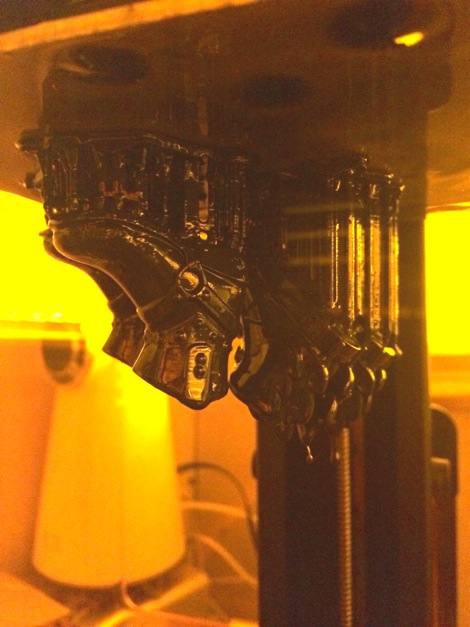
Our first test parts – suspended from the build platform
It’s pretty straightforward. Angle the cover back (don’t leave this open, that resin in the build tray doesn’t do well when exposed to UV light in uncontrolled conditions), crank forward the handle at the top of the build platform and slide it off (and close the cover again). Then move to the Finishing Station that’s supplied with the machine.
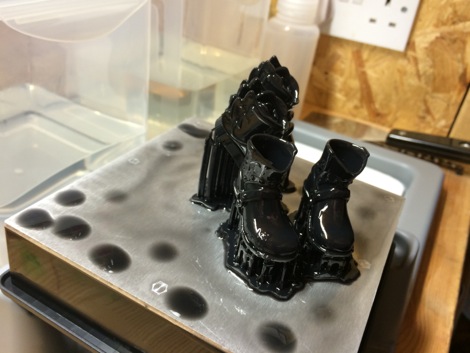
Build platform removed from the machine, placed into the Finishing Station, ready for some prep work
Essentially, this a station for placing your build platform on and removing the parts without it skidding all over your worktop. The system is supplied with a scraper, a bag full of disposable gloves and some flush snippers to help with removing the supports nice and cleanly.
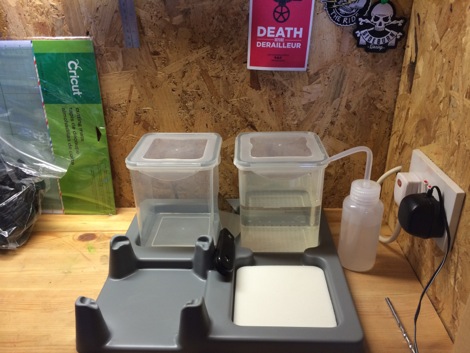
Interestingly, the support structures are built, in the PreForm software, with smaller areas that let you get some purchase with the scraper (other vendors need to get this into their software ASAP). You then push/lever the parts off. It’s then best practice to clean up the build platform (just with a paper towel) and put it back into the machine, ready to go again.
Part clean up
You then move to the two rinse rubs and wash baskets (with the IPA in) that are used to remove the remaining resin from the parts.
One has a nicely designed basket that helps with removing the parts, particularly useful if you are, as we are, running the darker resins as the IPA quickly becomes a touch murky. Or the parts are very small.
Tip#4: The machine is supplied with gloves. Use them. The combination of the resin and the IPA is slippery.
There are various thoughts on how best to rinse the parts, but I found it easier to remove the part intact (leave the supports in place for now), put it in the right hand rinse tub. Give that a gentle shake for a couple of minutes with the lid closed and leave it to settle and work into the smaller areas for 10 minutes.
Tip#5: Open the window. Trust me. Working with two tubs full of, what is essentially, raw alcohol, while pleasant and not all that dangerous (apart from the fire risk), can make you a bit woozy.
You can then use the supplied squeeze bottle to remove any remaining resin from nooks and crannies. Then place the part into the second Rinse Tub and let it soak for a little. Remove the parts and place them on the foam pad and let them drain.
Curing and support removal
While the parts are solid straight off the machine the resin doesn’t appear to be 100 per cent cured at this point.
They’re still a bit sticky and the surface finish is very easy to damage. Common practice is to leave these in a sunny spot and let the sun work its magic to harden them off.
If you’re just tinkering with this machine, that’s all good.
If you’re working in a professional environment, the chances are that you’ll be needing those parts as soon as possible – if not before.
This is where we’d recommend buying in a UV Steriliser unit. They cost around 30-40 quid on eBay or Amazon (search “UV tool Cabinet”, otherwise you’ll end up with pond filters). And yes, these are the exact same things that are used in beauty salons to sterilise tools.
They’re a closed box, they typically have two UV strip bulbs in them (top and bottom – to get both sides of your part), a rack and the model we got hold of, has a timer – perfect.
You even get that satisfying ‘DING’ when you parts are ready.
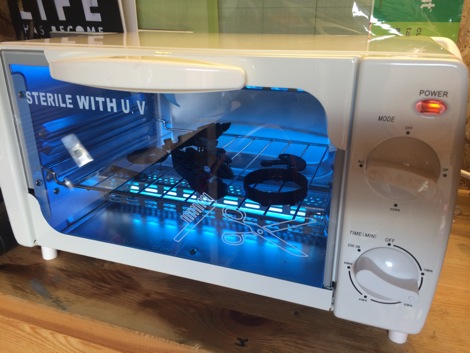
I have to give credit where it’s due. I ran into Shapeway’s 3D printing guru, Duann Scott, at the museum of Modern Art in New York. They were running a FormLabs machine in the gallery to print scans of visitors and did exactly the same.
Whether you follow this route, use a home-brewed UV bulb and some cardboard to make your own or let the big orange thing in the sky do its thing, my advice is to let the parts cure before you remove the supports. The resin will be nice and hardened and using the supplied snips to trim off the supports is super easy, leaving a nice clean cut.
The end result
Over the last few days, we’ve had the machine running pretty much constantly. We’ve been experimenting with different build resolutions, different types of geometry.
Bearing in mind the compact build envelope of this machine (it’s 125 × 125 × 165 mm), you can get a lot done in a short space of time.
It’ll give you excellent results, but with a few caveats. So let’s run those down and look at things to consider when you’re first running the machine.
The first is that you need to trust the set-up software. If you’re used to working with other desktop 3D printers, you’ll be tempted to ignore the automatic orientation tools to get a quicker build time or to get the best surface finish you want.
While there are a few tricks you can use to get the part aligned the way you want, go with what the machine gives you (we’ll explore these later in the week).
The reason is that if you, as I did, think you can get what you want more quickly by aligning a flat surface with the build platform or having mating or interface surfaces at the bottom on the part, don’t.
What you’ll end up with is a failed print and an hour of cleaning out the resin tank. The reason for this is down to the machine’s build method and physics.
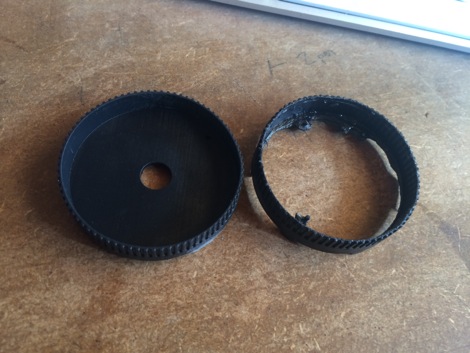
This week’s only failed print. And that was down to Al being a smart arse and ignoring the software
The machine uses capillary action to get each layer to the fine resolutions it uses (0.1mm is the largest layer size – medium is 0.5mm – with 0.025mm as an option but save that for ultra fine parts). Part of that process induces suction between the build platform, the resin tank and the part.
If you have too much surface area being built at one time, the chances are you’ll end up with a part that sticks to the resin tank, not the build platform and rips off.
Another point to note is that while the machine has a decent build volume, because of this requirement to ease the part in and out of the build process (see image below), if you’re building up to the maximum dimensions, you need to bear in mind that you’ll need to angle that part (unless you’re really lucky with the geometry) so the maximum build volume is reduced.
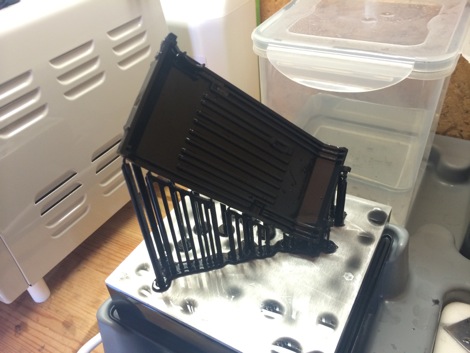
This rear cover from a Lomography camera is a pretty nice test part. Complexish features and very linear to test for warp in the parts – the results are pretty nice.
The part above should, theoretically, fit easily, but because of the requirement to tilt the part and not have it rip the supports, it takes a bit of juggling to fit, then build, correctly.
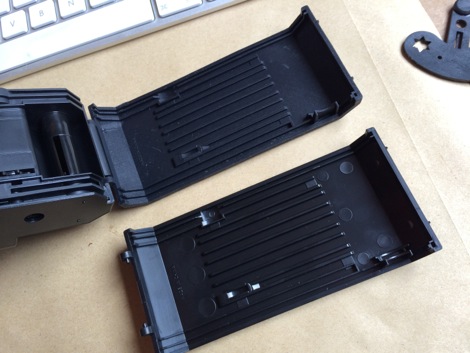
When assembled into the actual product, it’s clear that the Form 1+ builds a very nice prototype indeed (hint: the actual part is below the 3D print)
I also got to build a prototype of a design from one of GrabCAD’s challenges last year.
That was a rather gratifying moment to see something from idea to reality. Something I’m sure we’re all more than familiar with.

So what next?
I’ve got a few meetings and a few pressing deadlines, so I’ll take a few days to gather some more thoughts – on the list for experimentation are:
- Tall parts: How does it handle those?
- Small, ultra fine details: How do they survive the build and post processing?
- Big solid parts: Any issues?
- Support editing: Can it effectively support your parts while reducing any post processing or support artefacts?
- Super complex geometry and how best to tackle it.
- Finishing methods: Best approaches and things to avoid.
- Best practices and ideas to make the most of the Form 1+
- Resolution. What’s best?
- Isopropyl Alcohol: Can you put it in your tea without ill effects?*
Of course, anything else you’d like to know, any questions or, indeed, tips or tricks, drop us a line in the comments or reach out to us on the usual social media (twitter is best for Al – @alistardean or @develop3D).
*Kidding, honest