Working alongside human colleagues to automate repetitive tasks, ‘cobots’ are quickly invading the workplace. Stephen Holmes speaks to Universal Robots, maker of robotic arms that are getting to grips with jobs that vary from maritime welding to making coffee
Today, just 2% of applications that could be transformed by robotic collaboration are already automated — but the rise of the collaborative robot, or ‘cobot’, looks set to transform that picture. Cobots are engineered so that they can work alongside humans without the need for safety barriers and be equipped with different peripherals to perform different tasks. They typically take the form of a robotic arm and demand for them is growing at businesses intrigued by their proven ability to increase productivity.
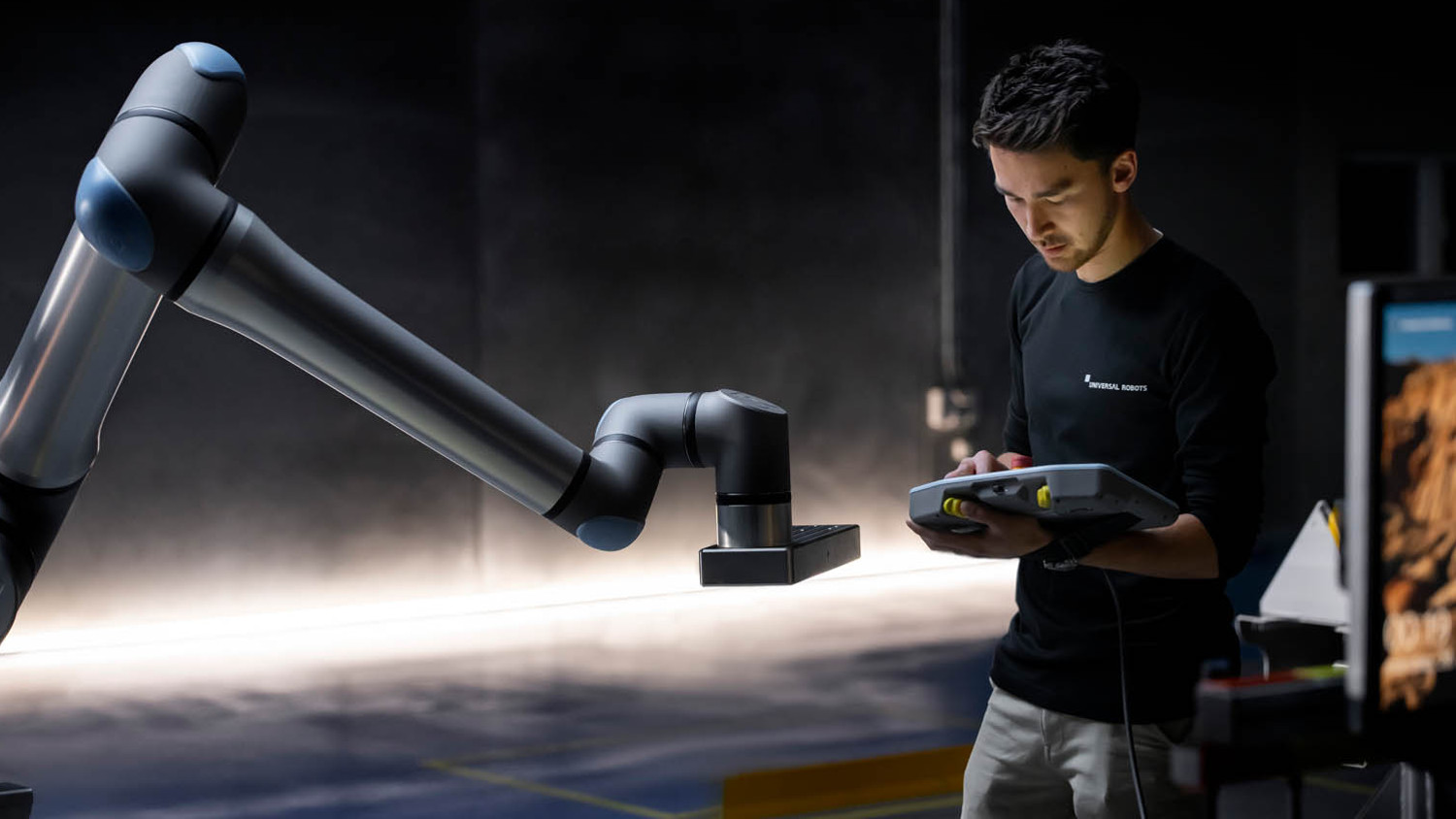
Today, cobots are performing tasks that range from welding work on ships to serving coffee from kiosks. Barriers of cost, availability and ease of programming are falling, persuading more companies to invest.
At Universal Robots, a leader in collaborative robotic automation, vice-president of strategy and innovation Anders Billeso Beck is confident that we will all soon be accustomed to seeing cobots at work in our daily lives.
“We see more and more cobots where tasks are done repetitively, and where we’re still struggling to find labour to perform them,” he says, speaking from the brand’s headquarters in Odense, Denmark.
Universal Robots is one of the most recognisable brands associated with robot arms, with its products standing out from the crowd with their blue and silver colour schemes, in marked contrast to the block primary colours more typically seen on the heavyweight robotic arms that populate many manufacturing assembly lines.
Beck compares the evolution of the cobot to that of the mobile phone. “People were competing on battery life, and then suddenly, some other people brought along a phone that had really poor battery life and the worst antenna in the world, but it had a touchscreen and could run apps. It really displaced the value proposition!”
Cobots are similar, he explains, in that they may not designed to be as fast, strong, stiff or accurate as industrial robots, but they change the basic value proposition, because what users prize more highly is ease of use.
“We’re getting to the point where people don’t want to tinker with technology. They want to find a way to get their automation problems solved. And, of course, we offer technology for that – we’ve invested a lot into that, and we have now grown a huge ecosystem around our cobots.”
Over 350 partners have built technologies for the Universal Robot cobot – from gripping tools and vision technologies to simple cable guidance and bumpers. Some 160 OEM partners, meanwhile have built fully integrated systems of which a Universal Robots cobot forms an integral part.
“It’s safe to be around, it’s easy to programme, and it’s fast to deploy. These are the core things, and that demand has actually not changed a lot,” Beck says.
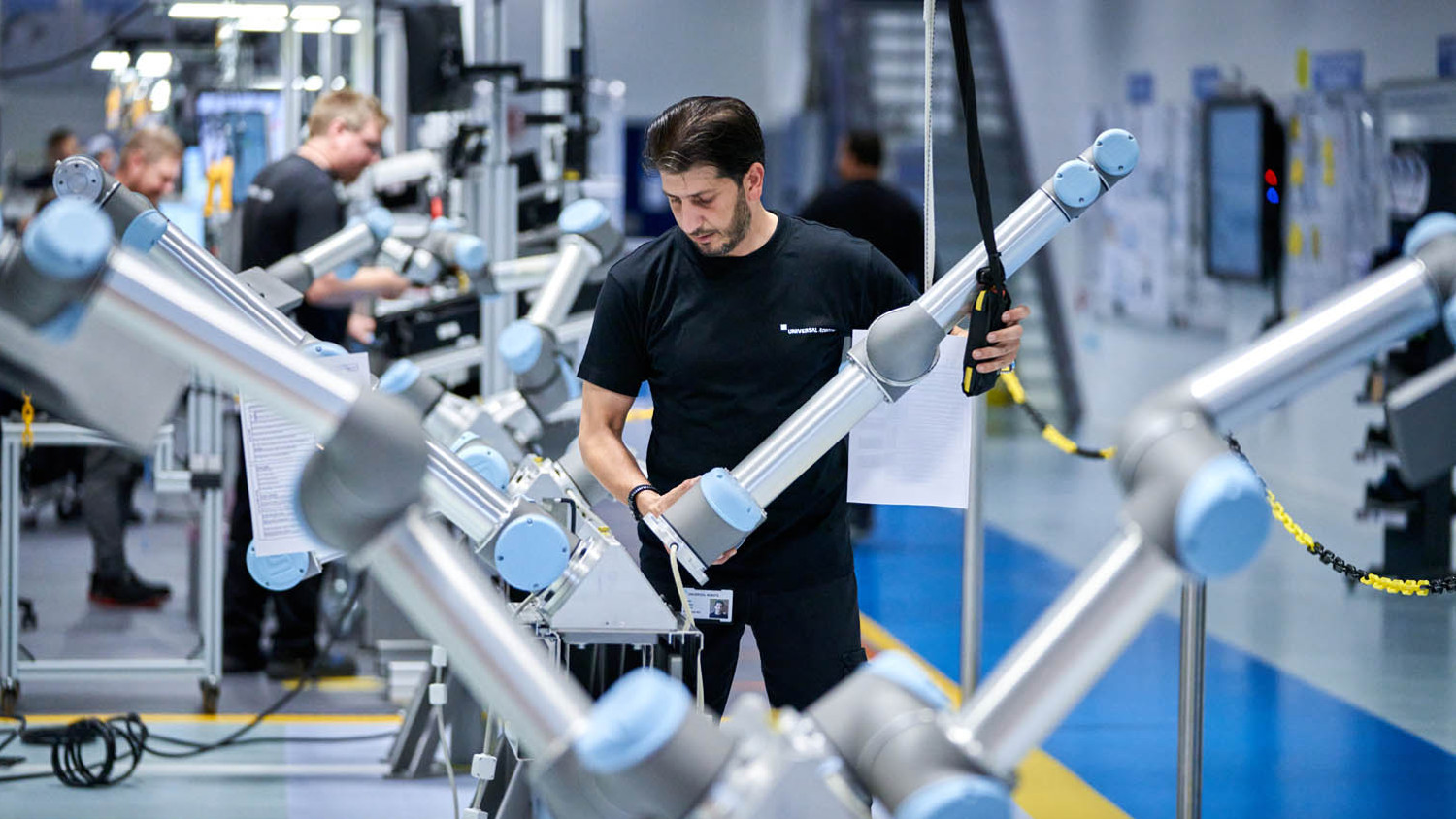
Power and precision
For the first time in its 18-year history, Universal Robots has taken its full product design process in-house, undertaking a full ground-up design on the mechanics, mechatronics infrastructure and all electromechanical parts of its latest models, the UR20 and UR30.
The big challenge is blending the power and precision of the servo motors mounted in each joint of the arm. Beck says that, for the UR20, its biggest produces over 700 newton metres of torque.
“That’s more than a performance model Tesla does on all four wheels, and it does that in a drive that’s the size of a small handball, so there’s an immense amount of torque being generated in a very small, weight-optimised unit,” he explains.
At the same time, he continues, cobots also need to deliver accuracy measured in micro radians. “You have this servo drive, and you attach it to a 1.7-metre-long stick. And then you still need to hit a spot that is within 50 micrometres. So, it has to be ultra-accurate and so powerful at the same time.”
The design process at Universal Robots begins with a 3D model in Dassault Systèmes’ Solidworks. Beck explains that the company is a big user of the Solidworks package, but on top of that, it has added several additional capabilities to help accelerate its design process.
Much of this revolves around simulation and the heavy use of finite element analysis (FEA) modelling. “One of the key challenges is that we are really pushing every component to just before the breaking point,” Beck emphasises, saying that the engineering team is challenging every material in the robot to optimise it for weight, performance and accuracy.
“Using simulation has increasingly, over the last five years, become a natural development for us,” he says. For much of this work, Ansys Mechanical has been utilised, with Ansys helping support Universal Robots in setting up the simulation environment and collaborating on the various challenges of trying to simulate so many different use cases.
“It’s actually a really difficult product to do these simulations on, because people will do everything with them,” says Beck.
Not only can the arms and joints be moved in all directions, but there are also different speeds and loads to consider. And then there are use cases that involve vibration stresses from impact wrenches and sanders, or heat from welding. “There are all sorts of things that the robots get exposed to in their natural habitats, and we need to account for all of those when we’re designing the product. Barely a day goes by where we don’t get a contact from a customer, where they have a brilliant but superchallenging idea about doing something!”
Universal Robots will run a simulation to pre-validate a challenging scenario, like magnetically mounting an arm onto the side of a ship to weld repairs at high temperatures, or handling power tools on building sites that produce juddering vibrations.
In the last five years, the company has built a huge physical testing capability, which allows for functional testing all the way through the development process. For the design team, the goal is to get to a physical product as quickly as possible so that it can start running real-world tests. This speed helps build validation that can be fed back into the simulation analysis.
A farm of nearly 50 robots currently exists to test all the cobot software updates, running through test cycles to make sure that nothing fundamental around the motion or sensors has altered.
Beck adds that, every few weeks, the company has robots run through 16 real-world use cases built by its partners, forming part of a large battery of tests that make sure nothing has changed that would harm a customer application in the outside world and maintaining the harmony between Universal Robots’ in-house hardware and software development teams.
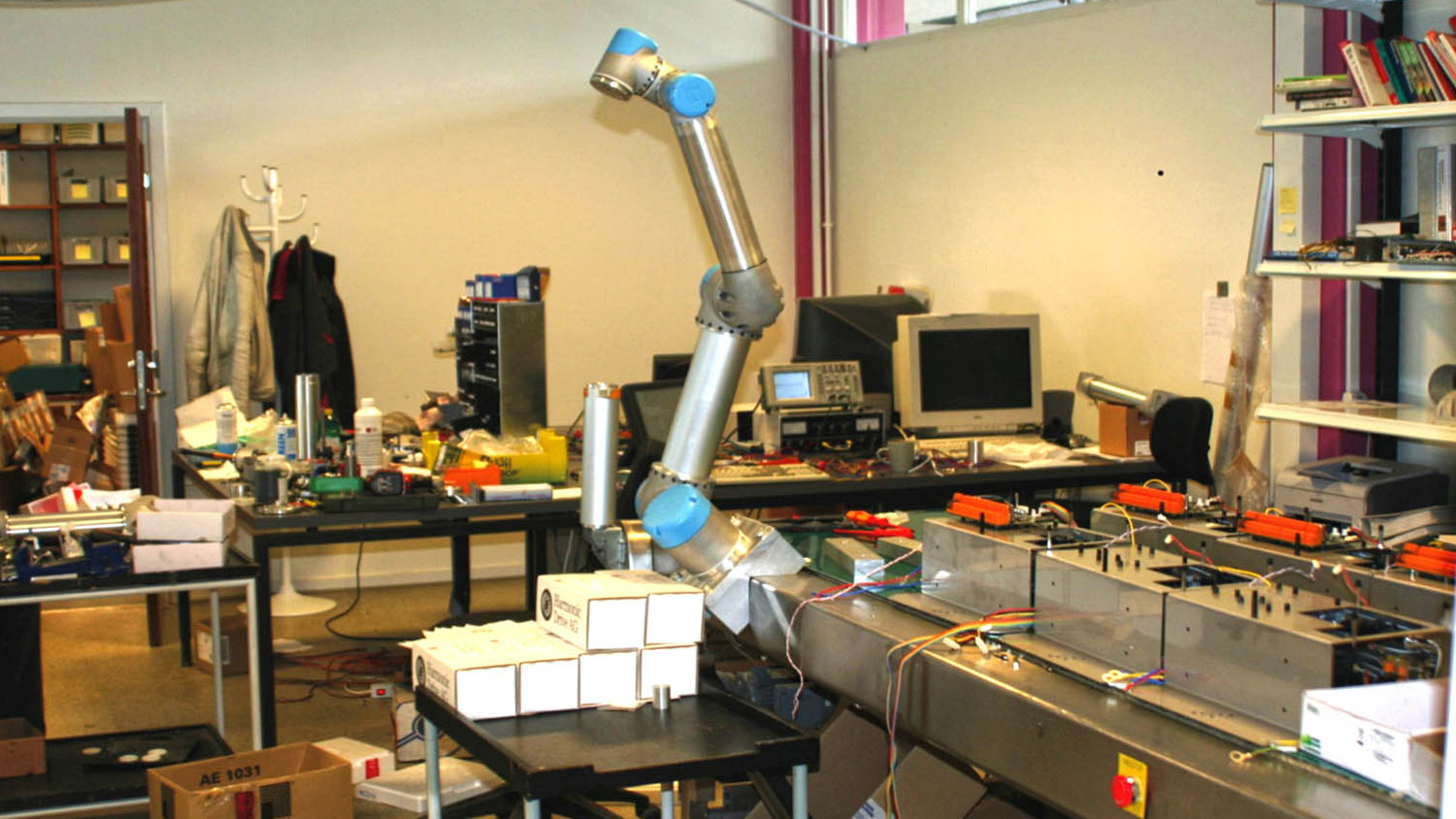
Power-to-weight ratios
The key to achieving the perfect design, says Beck, comes down to the power-to-weight ratio that a robotic arm can offer. The less of a moving mass you have, the safer and more productive the robot will be.
The power-to-weight ratio of the UR20 cobot, for example, is astonishing given its size. Weighing in at just 64Kg, it can carry a 20Kg weight within a 1.75 metre reach, using a similar amount of power as a household washing machine and taking up only a 245mm footprint.
Attaining these results forced the team to consider everything that could potentially go wrong. They needed to think not only about combining components in the neatest package, but also how the massive forces generated might deform the intricate parts.
The use of aluminium for Universal Robot’s cobots has its pros and cons, says Beck. It is proven to be the best material in terms of price, weight and performance, but still poses issues for the designers.
“It’s a super-challenging material to use, because it doesn’t have this infinite fatigue life, so you need to be super-careful with that,” he says.
“It’s really poor at dampening vibrations, and vibrations are the enemy of any robot. That’s why all traditional robots are cast iron. They’re perfect for dampening vibrations,” he says.
“So, in that way, we were leveraging Ansys very much to get the best out of these materials, so we don’t run into hidden traps we haven’t thought about.”
According to Beck, the ‘nucleus’ of each cobot is the highprecision servo motor in each joint, for which the reuse of components across the family proves a fundamental building block of the design and validation process.
“Our cobots have a very modular design. We build them very modularly in a way where internally we are reusing the joints, so that some joints that are maybe in the wrists of the bigger robots like the UR10 are also the base joint for a small 3kg robot.” With key components in place, for the UR20 and UR30, the team looked to optimise the designs, removing any ‘kinks’ found in previous models.
That involved taking apart how things were done previously and putting it back together, says Beck, “in a way that’s significantly better than the way we’ve done it before. Because with every design, of course, there are known weaknesses.”
Handling this process entirely in-house meant that any issues around manufacturing or assembly that had caused headaches over the years could be engineered out of the newer models. Additionally, the team looked to make its own production processes as automated as possible, from managing multiple suppliers to making parts that can snap together but still meet high-tolerance requirements.
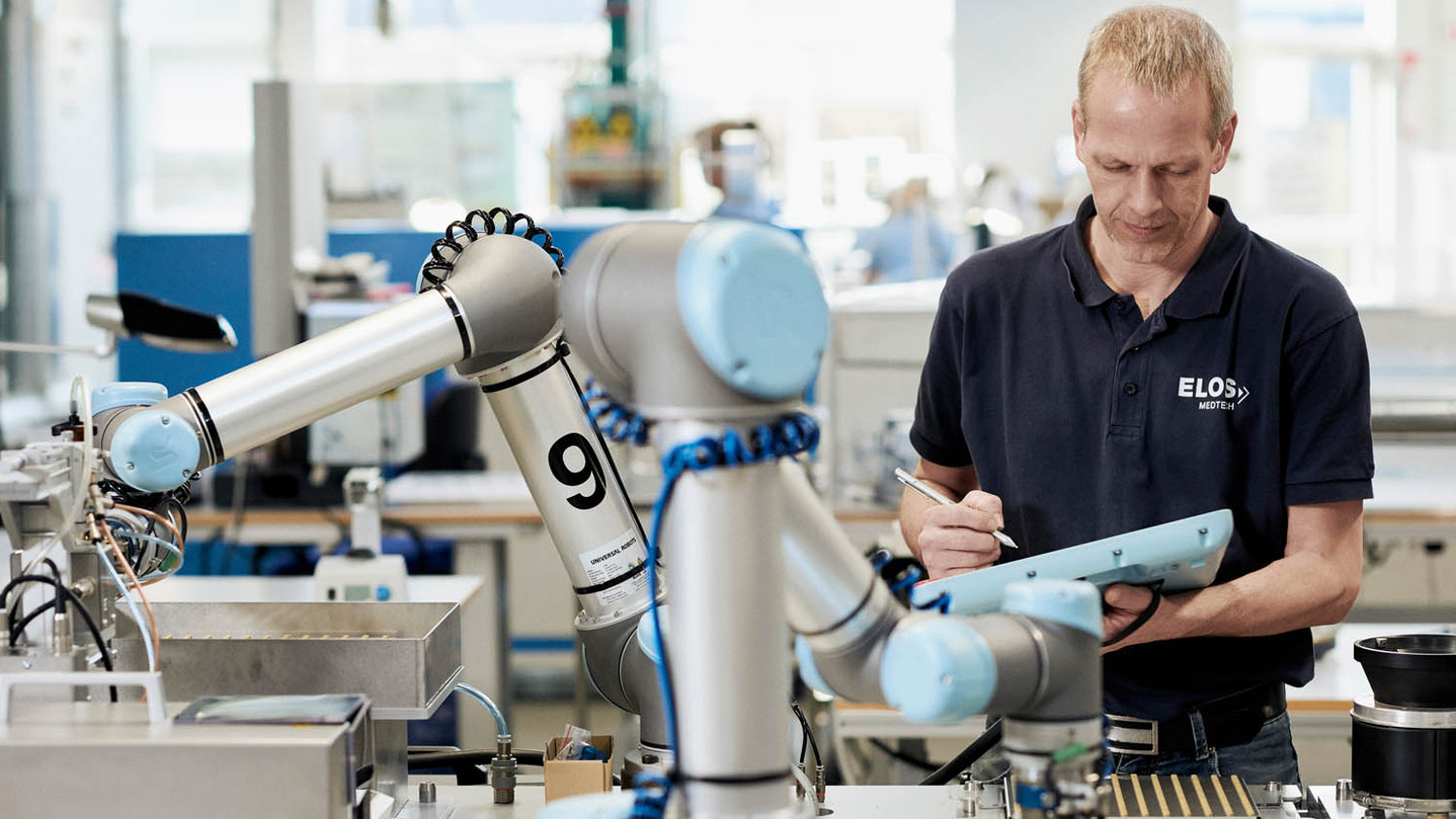
Joint effort
By improving the abilities of the new designs, adding strength to joints and increasing ease of assembly, the team encountered another key challenge: maintaining its brand’s visual identity.
Universal Robot’s iconic blue lid caps on each joint of the cobot are also an indication of how the joint is assembled from two sides. The housing on previous models formed the exoskeleton of the joint, where all the components are put together inside. “That’s why it has the blue cap, because we are accessing it from both sides,” explains Beck.
“In the new design, we designed something that’s just an independent servo motor, which allows us to put the housing on at the end, and basically sliding in, bolting it on, screwing into the housing. And then we can have this closed design instead.”
The closed design added a lot more stiffness to the arm but took away the iconic logo that stood out wherever it was placed in factories, laboratories and kitchens. The new generation instead features monogrammed joint bumpers in the trademark light blue, which maintain the branding, as well as conforming to the team’s ‘Nordic functional’ design language.
“It’s minimalistic, we think it’s nice and pretty, but it’s also functional. It still feels like it’s a product designed to get work done, not to sit in a showroom,” smiles Beck. “We’re very, very proud actually about the UR20 design, because we think it captures the company’s DNA, where we came from, but also it looks like a clear evolution.”
With the company dead set on filling those remaining 98% of cobot-friendly processes, expect to see far more flashes of the silver and light blue around you soon, automating all manner of tasks.
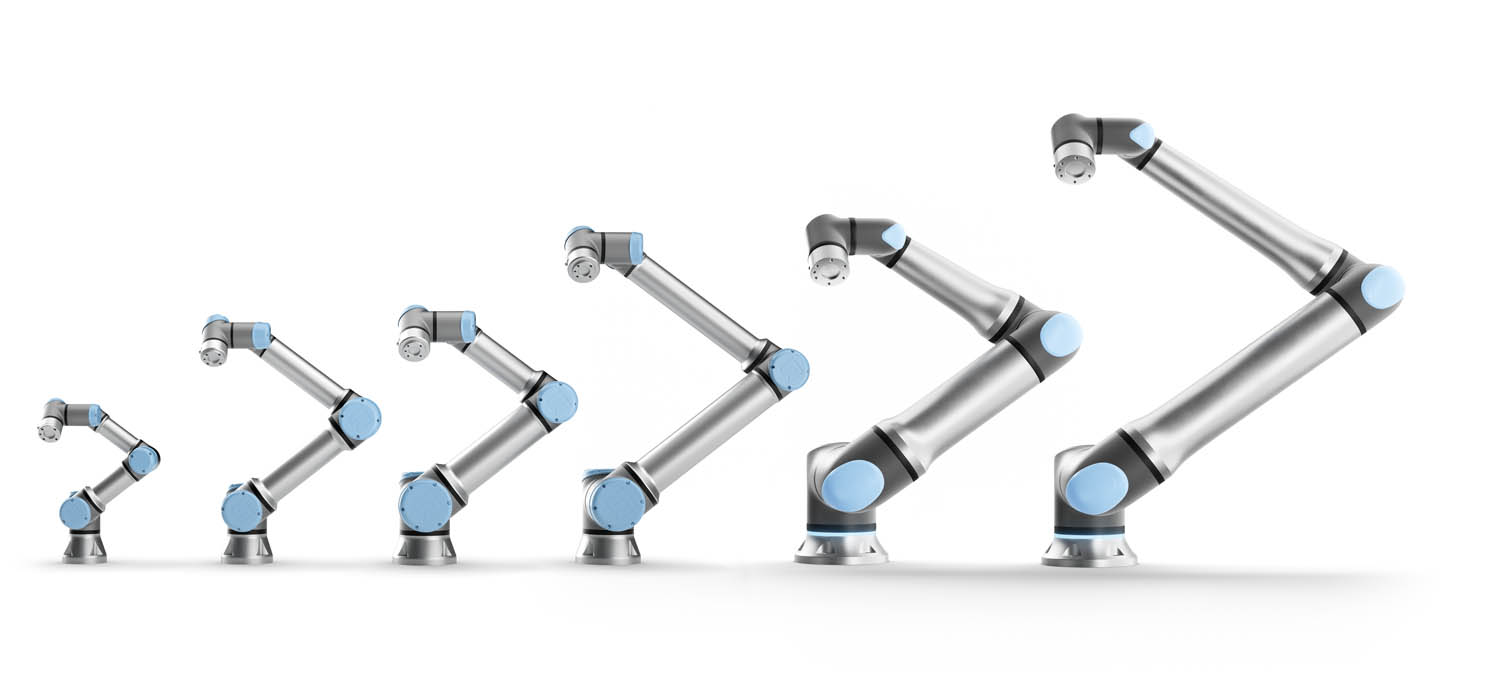
This article first appeared in DEVELOP3D Magazine
DEVELOP3D is a publication dedicated to product design + development, from concept to manufacture and the technologies behind it all.
To receive the physical publication or digital issue free, as well as exclusive news and offers, subscribe to DEVELOP3D Magazine here