Hard on the heels of Rhino 7, DEVELOP3D caught up with Rhino CEO Bob McNeel and business development head Scott Davidson, in order to dig a little deeper into the features of this latest release
Rhino occupies a special place in the designer’s CAD arsenal: a generic modelling tool, not skewed towards any single scale or industry.
It’s used in footwear development and jewellery design just as much as it’s used in automotive surfaces and architecture. The only rule here is that the geometry that this system defines is able to be manufactured.
While new features provide core functionality, such as mould design, it’s not a full or dedicated feature set. In other words, other developers or customers are welcome to develop on top.
With Rhino 7 now available, DEVELOP3D spoke to two of the company’s guiding figures about what the latest release has in store, and what is yet to come.
DEVELOP3D (D3D): There are a lot of features crammed into this new release. What were you thinking about when you decided on this feature list?
Bob McNeel (BM): It was a timing thing. Part of it was that we needed to get the SubD stuff up to par. A lot of that was core work that had to be done by very small group of people, just because of the type of work it is.
It allowed other people to work on all the other stuff, which just needed to be hooked up. It wasn’t inventing stuff from scratch, like the SubD project was, which was really going on for about three years.
This is core geometry. What that means is that you touch every import/ export function, display pipeline, the picking engine, plus, then you’ve got to do all the core geometry work. And, the SubD stuff is a classic problem.
The classic SubD implementation is basically just a mesh or refined mesh at various levels. For the Rhino community, where everything’s got to be at manufacturable precision, we had to develop the core technology to have the limit surface be a spline surface, not a mesh.
D3D: So, how much better is this than T-splines?
BM: It’s better and it’s different in a couple ways. There’s no patents involved, so that means that we can publish this, we can let people play with it, we can expose it in software development kits and we can put it in open source projects that we support.
In terms of data structures and stuff, our SubD is actually compatible with Pixar’s OpenSubdiv. So, if you use the same control net from our SubD, and hand off to another open SubD project, they’ll get the same limit surface with their calculations.
Now, the other system’s output may be a mesh, but for downstream applications like rendering, STL printing and, of course, animation and all of that stuff in the movie industry, they are identical, so there isn’t a loss going that way. But on the same hand, it can go the other way as a spline surface, so you can export it as a STEP file or whatever, and it’ll come in as ordinary B-rep.
D3D: But can you turn it back into a SubD on demand?
BM: You can in certain cases. It depends on what somebody does with it later. If you take a trimmed B-rep, something with round holes, a typical mechanical part, there’s not an obvious way to always go back.
Scott Davidson (SD): Every SubD has a NURBS equivalent, but not every NURBS model has a SubD equivalent, because they’re two different geometry types. But going back the other way, you know, that’s where QuadRemesh comes in. We can QuadRemesh and go back to SubD.
Now it’s a different SubD, but it’s close to the NURBS.
While you can take a mesh and QuadRemesh it and go to SubD, and therefore go to NURBS, there is a limit to how damaged the mesh can be. We don’t have all the tools to do mesh repair in all cases.
D3D: For Rhino, is injection-moulded parts and toolmaking an important market?
BM: The essential geometry calculation to figure out where those mould lines go, so that parts will come out – it’s a heavy-duty math problem. And to hand that off to some other product, especially when the shape is freeform, is not something that anybody but a bunch of math geeks can figure out.
We’ve actually had the math in there to do that for a while and finally one of our guys pointed out that they keep having to help people figure out how to use this stuff. We’ve just wrapped it up within a user-friendly interface.
We’ve got customers in shoe companies and toy companies building these little plastic parts, and they have hundreds of people just working on the mould.
The shoe folks tell me that, for every designer they have in Germany or Portland, Oregon, they’ve got somewhere between 60 and 600 people developing the moulds!
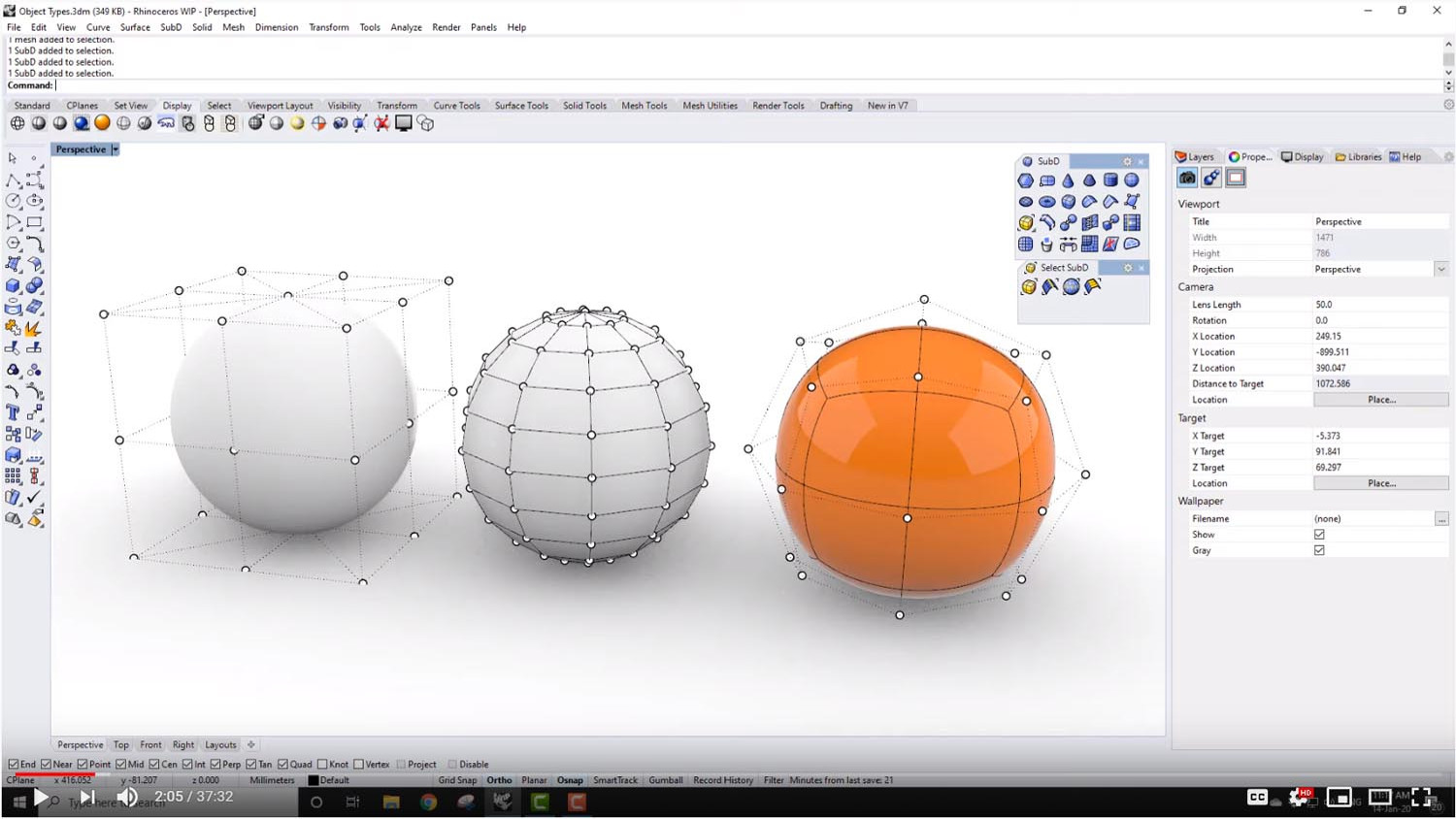
D3D: How about rendering tools?
BM: The first thing with Rhino 7 was to replace the rendering tools that we had in Rhino and replace the core rendering technology with Cycles – which is what’s in Blender – and that just opens up a whole bunch of capability.
One of our guys is on the core team for Cycles in the Blender project, so he’s going back and forth between what he’s implementing for us, plus making sure its compatible with a bunch of stuff, particularly on the materials side, which is looking pretty good.
SD: This is good to talk about, because it’s a pretty sophisticated advancement and not just as to what we have in Rhino. We have Cycles, and Cycles is modern and supports a bunch of modern technologies like denoisers, right? Everybody has come out with denoisers lately – Nvidia, AMD and Intel all have their own denoisers, and we support all three. It takes renderings from 20 minutes down to two minutes – kind of crazy numbers.
Then you’ve got the materials. One of the things that people have asked for decades is, ‘Can I have compatible materials across multiple rendering tools?’ PBR [physically based rendering] done by Disney and Pixar and whoever else, is a step in that direction. We support PBR materials.
Now, PBR is really great, because you can do a lot of sophisticated maps and we can take the bitmaps and textures from another product and use those in ours. But, there’s some kind of unspoken advantages here; for example, Adobe Substance Designer outputs PBR materials.
So now you can use Substance and read Substance materials into Rhino and use them in your renders. You can also use Substance as a kind of a 3D painter. But if you want to talk about augmented and virtual reality, if you look at Unity, or Unreal, or Nvidia’s Omniverse, they use PBR materials too!
Now, we’re pushing out to those, and have ongoing work to be compatible with Enscape, TwinMotion (which is free for Rhino users) and all of those type of tools.
Rhino 7 is very much a play into all of this, but it’s also a lot of the foundation work that’s going to play into AR/VR worlds. We want to play well with all these tools. We want to be able to store their information and to be able to write their information out.
D3D: So what is the AMD ProRender play for you then?
SD: ProRender is there. It’s AMD’s play into using their GPUs and we can support all that stuff. It’s one of our strategies and what you’ll see throughout Rhino 7 is that we are really trying to be compatible with the SubD engines, PBR materials, the way we can get in and out of other products.We are trying to be a better player on the world stage of CAD information.