A partnership between Heraeus Amloy and Trumpf looks to open door to 3D printing of amorphous metals, boosting the process and cost efficiency end-use parts for industry.
Amorphous metals are formed by cooling molten metal extremely quickly – but what a 3D printer can do that other methods can’t is build them into larger, more complex parts, creating isotropic material parts regardless of the direction in which the 3D printer builds them.
A number of areas stand to benefit from 3D printing amorphous metals, including parts that are subject to significant stresses and lightweight designs – sectors such as aerospace and mechanical engineering.
The move from Heraeus Amloy and Trumpf was to create a standard production method on the shop floor by improving process and cost efficiencies, which already means that Trumpf 3D TruPrint systems owners can now process zirconium-based alloys from Heraeus Amloy.
The two partners are also hoping to make copper- and titanium-based alloys available for 3D printing in the future, while it is currently possible to order 3D printed amorphous parts directly from Heraeus Amloy.
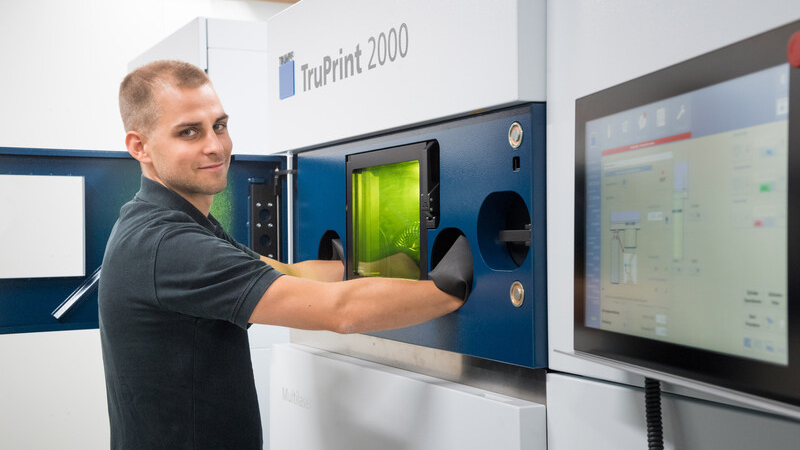
The latest-generation TruPrint 2000 machine is a particularly good for printing amorphous metals as its design allows for excess powder to be prepared in an inert gas environment for the subsequent building process.
This protects the powder from any adverse influences – a key benefit for amorphous metals as they react so quickly with oxygen.
“3D printing of amorphous components in industry is still in its infancy. This new collaboration will help us speed up printing processes and improve surface quality, ultimately cutting costs for customers,” said Heraeus Maloy’s Jürgen Wachter.
“This will make the technology more suitable for a wider range of applications, some of which will be completely new.”
For their part, amorphous metals are very light by nature, so the combination of 3D printing and amorphous metals can reduce weight in all sorts of applications.
3D printing makes the production of amorphous parts faster and simpler in a wide range of contexts.
The technology enables users to build parts in one piece instead of making components one by one and then assembling them into a finished part.