In design, the right material choice can make all the difference. In the case of Vuzix’s Shield smart glasses, expert advice from Materialise gave this piece of kit the rigidity to operate in tough working conditions while still remaining stylish
At first glance, Vuzix’s Shield glasses are a pair of safety work glasses with a stylish titanium frame. Wear them, however, and their onboard 8-core CPU puts some unexpected capabilities within view.
Cut to the present day, and barely a fashion week passes without another 3D printed running shoe, clog or slip-on being launched. The reasons for that – beyond aesthetics – are clear.
These smart glasses connect their wearer to a world of IT sensors, instructions and live remote guidance, via miniature uLED stereo displays. Codes can be scanned with an advanced reader and video can be streamed from the field, with all functions enabled through voice or touch.
For Vuzix, it was important for all of its technology to be incorporated in a traditional eyewear form factor. In turn, this eyewear had to meet the requirements laid out by the ‘three Fs’ – fashion, function, and fit.
In other words, it was crucial that these smart glasses looked as good as they worked, so that they would appeal to a broad audience, while also taking into account the science around how the human eye works, and also how consumers wear their glasses.
But in designing the Shield, the biggest challenge came down to stability. With the twin displays sitting in a fixed component within each temple, keeping the frame rigid was key, explains Shane Porzio, vice president of engineering at Vuzix.
“If anything’s out of alignment, especially on binocular systems, you literally can’t use the images. So, from user to user, taking them on and off , beating them up, these things all have to stay aligned within a pixel for rotation and vertical and horizontal positioning. That means we can’t aff ord any twisting, rocking or ratcheting across the front frame.”
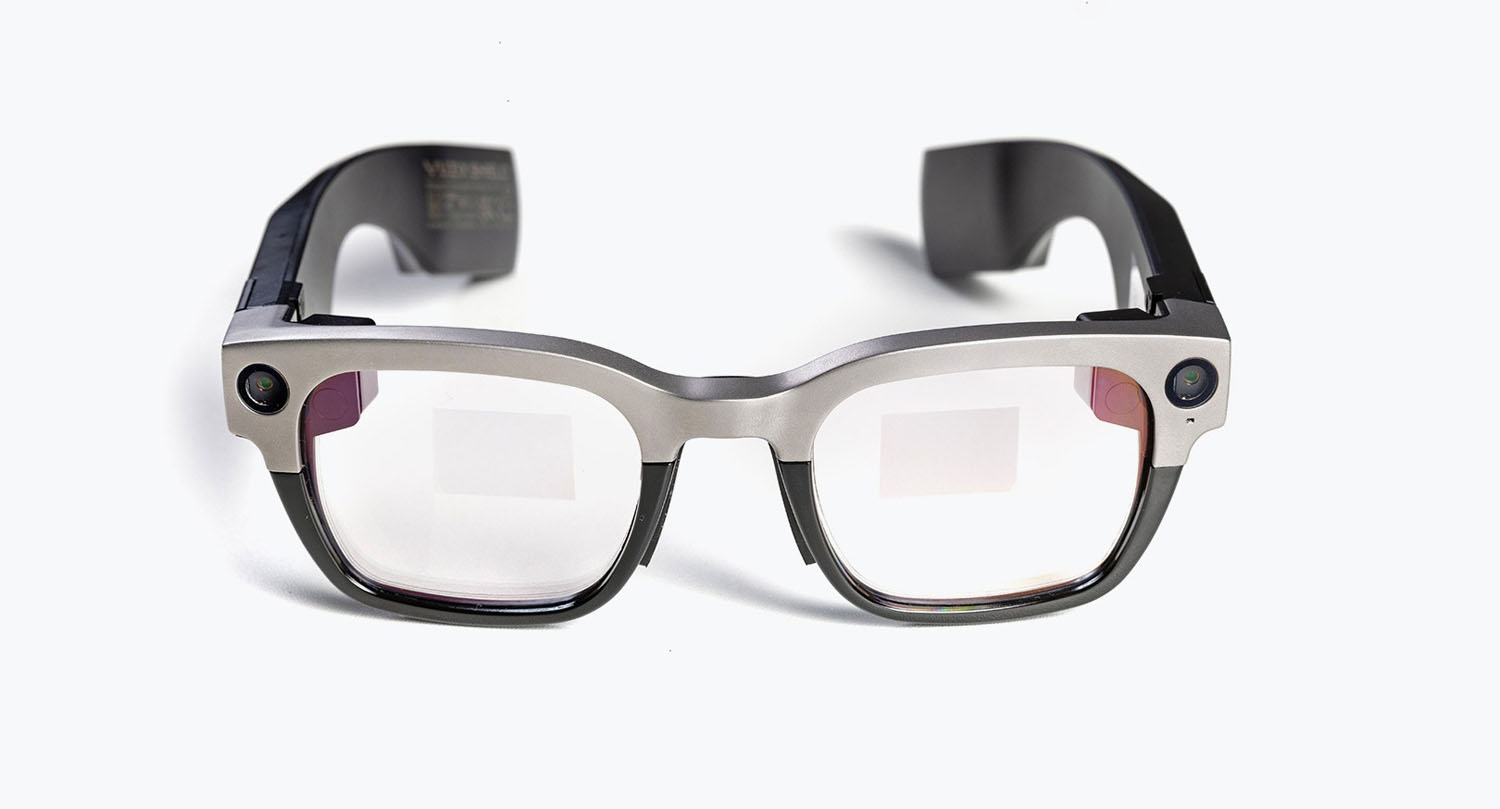
Stiff challenge
Prototypes built using injection moulding with both carbonand glass-filled polymers failed to provide the necessary stiffness, according to Porzio. “No matter what the industrial design was, we couldn’t get the support rigid enough. If you were just wearing the glasses on their own, they were fine. But if you connected a cable to the battery in your pocket, for example, it could put just enough torque on the glasses to cause a slight misalignment from right to left.”
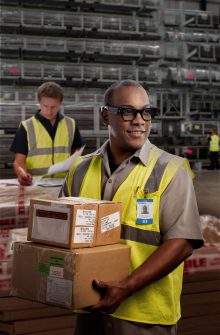
Having identified the rigidity of the top of the frame as the key issue, the design team partnered with 3D printing experts Materialise to evaluate other materials, eventually turning to 3D-printed titanium.
The Shield’s temples contain the CPU and batteries, meaning that they’re already a little thicker than average. But by ensuring the newly designed 3D-printed front connects easily to the remaining components, other materials could be used in that area. As a bonus, a hybrid frame design further reduces the weight, increasing comfort and wearability.
“In a situation like this, if you think about how we’re trying to get this just right, there’s a lot of iteration that has to happen,” says Porzio, adding that 3D printing with the aid of Materialise helped the team’s iterative design process, allowing for lightning-fast prototyping.
“If you were doing that with injection-moulded parts, it would be incredibly expensive and time-consuming, because of tooling changes and the like.
” For production, Materialise and Vuzix combined their expertise to identify the tight tolerances required. Together with post-processing capabilities, the titanium parts were fi nished to an accuracy within 0.1mm. The high-quality surface, meanwhile, gives Vuzix Shield an extra touch of luxury, ensuring that the frames don’t just function as intended but also look great, too.
This article first appeared in DEVELOP3D Magazine
DEVELOP3D is a publication dedicated to product design + development, from concept to manufacture and the technologies behind it all.
To receive the physical publication or digital issue free, as well as exclusive news and offers, subscribe to DEVELOP3D Magazine here