Modern vehicle wheels need to be designed for efficiency, both on the road and during manufacture. Maxion Wheels explains how it is creating a workflow with Castor to find out which existing parts it can 3D print in order to achieve peak performance
Producing over 50 million wheels each year, Maxion is a key supplier for a wide range of vehicles, from passenger to commercial to military. Wheels, it transpires, occupy almost 30% of a car’s profile, and are one of the most important configuration decisions that buyers make when purchasing a new car.
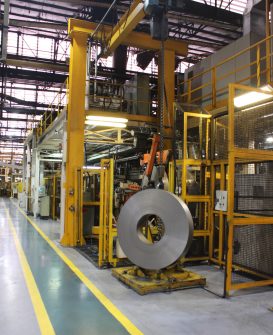
They’re also a key consideration in the design of electric vehicles. Thin-spoked designs, originally optimised for cooling the brakes, are counterproductive on an electric vehicle, creating unwanted drag. Modern wheel designs instead favour large, smooth surfaces for clean air flow and aerodynamic efficiency.
Efficiency is also seen in Maxion’s manufacturing workflow. With all of the machine, material and labour costs associated with prototyping, tooling, mould design and set-up, getting a return on investment depends on achieving high-volume production.
Based across 23 manufacturing plants globally, Maxion’s business relies heavily on the use of tooling and moulds, despite it being an early pioneer of additive manufacturing. Initially, the company used 3D printing for product concepts and spare machine parts. But as additive manufacturing technologies advanced, so has the company’s interest and involvement. And yet a major hurdle to broader adoption remains: knowing when to apply the alternative manufacturing process.
Deciding 3D or not
With numerous 3D printing opportunities in its pipeline, Maxion needed a proven and fast analytical method to evaluate them for their merits in terms of applicability in the company’s demanding industrial working conditions.
The search was handed to Maxion Advanced Technologies (MAT), the company’s global innovation hub based in Berlin. A team there undertook an 8-month research project to find a digital solution.
“Discovering the most promising components for additive manufacturing is resource-intensive,” says Dr Saul Reichman, head of Maxion Advanced Technologies, and global director of innovation and corporate venturing at Maxion Wheels. “Analysing the numerous assemblies, tools, fixtures and jigs used in our manufacturing processes – globally – is a ‘needle in a haystack’ challenge. We identified Castor as the right partner to support us on this journey.”
Castor is an automated 3D printing software capable of analysing thousands of parts at once and providing technical analysis for a full component design, helping to identify cost reduction opportunities and suggesting geometry changes to the part’s design.
It estimates the cost and lead-time for each part and can even connect the manufacturer to a service bureau that can print and supply the part according to requirements.
In proof of concept testing conducted by Maxion, the software analysis focused on tooling components, testing adapters, spare parts and complex products. In total, the CAD files of 25 parts were analysed, resulting in a report determining the part’s 3D printability with an estimation of the cost and lead-time for 3D production, and a breakeven point calculation versus traditional manufacturing.
Maxion – Strength and durability
From the initial part selection, three parts were chosen for 3D printing. Based on Castor’s material analysis recommendation and assurance that the part’s strength and durability would not be compromised during its lifecycle, maraging steel was selected as the material.
Tooling components were found to be the best candidate by Maxion for metal 3D printing technologies. For a certain tooling application investigated, metal 3D printing could provide equivalent mechanical performances to CNC machining, achieving the same values of cycle time performance.
The different metal microstructures of additive parts, compared to machining, do require post-processing, making them more suitable for certain applications on the shop floor than others, with Maxion keen to explore the full potential.
“In only eight months, we engaged Castor with both Maxion Structural Components and Maxion Wheels, shortlisted potential opportunities, selected the most suitable ones, conducted the analysis, and secured a third-party printer in Brazil,” explains Reichman. “Our fast pace is more proof of the innovation culture embedded within Maxion and its employees.”
With expanded use, it’s hoped that this speed and economy in manufacturing will roll on to benefit customers.